- お役立ち記事
- Know-how to significantly reduce calibration costs and measuring instrument management costs and specific ways to do so
月間77,185名の
製造業ご担当者様が閲覧しています*
*2025年2月28日現在のGoogle Analyticsのデータより
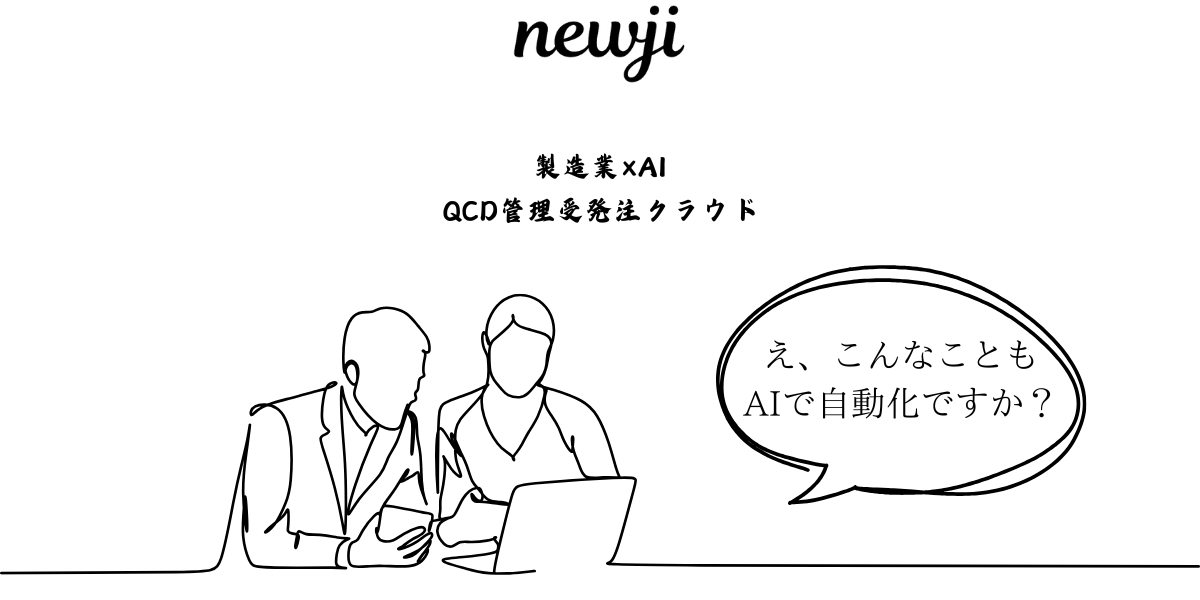
Know-how to significantly reduce calibration costs and measuring instrument management costs and specific ways to do so
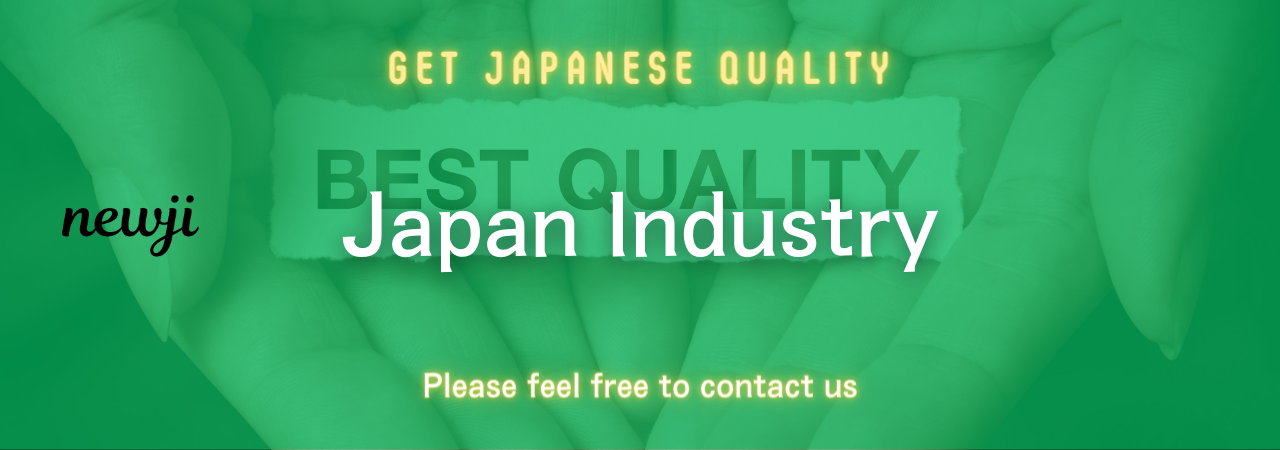
目次
Understanding Calibration Costs and Measuring Instrument Management
Every organization using precise measuring instruments faces the challenge of maintaining accuracy and efficiency.
This includes understanding the expenses involved in calibration and management.
Calibration is essential to ensure that measuring instruments provide correct data, which can impact product quality, safety, and compliance with regulations.
The costs associated with calibration often include service fees, downtime during calibration, and potential production delays.
Measuring instrument management, on the other hand, involves maintaining an inventory of instruments, tracking their calibration schedules, and ensuring they are functioning optimally.
Both calibration and management of measuring instruments are crucial for businesses to run smoothly and effectively.
Therefore, finding ways to reduce these costs can significantly enhance a company’s profitability and operational efficiency.
Assessing the Importance of Regular Calibration
Calibration ensures that the measurement tools are performing according to set standards.
This process addresses any possible drifts or inaccuracies that occur over time.
Industries like manufacturing, pharmaceuticals, and aerospace rely heavily on precise measurements, where even a small error can lead to significant issues.
Improper calibration or outdated equipment can lead to faulty products, which not only incur additional costs but can also damage a company’s reputation.
Regular calibration ensures compliance with industry standards and helps maintain customer trust.
While the importance of calibration is indisputable, it is also a cost that businesses continuously strive to optimize.
By maximizing the efficiency of the calibration process, companies can reduce unnecessary expenses while maintaining high standards of accuracy.
Strategies to Minimize Calibration Costs
To effectively reduce calibration costs, companies can implement several strategies.
1. Optimize Calibration Intervals
Regularly reviewing and adjusting calibration intervals based on instrument performance and usage can save costs.
Instruments that are stable and not used frequently may not require calibration as often as those that are critical and heavily used.
By analyzing historical calibration data, companies can determine the appropriate frequency for each instrument, avoiding unnecessary calibrations.
2. Use Predictive Maintenance
Employing a predictive maintenance program can help in foreseeing potential instrument failures or issues.
Using data analytics and monitoring tools, organizations can predict when an instrument might deviate from its set parameters.
This proactive approach allows for timely calibrations before issues arise, consequently saving costs associated with reactive maintenance and reducing downtime.
3. Implement In-House Calibration
Setting up an in-house calibration lab can be a significant cost-saving measure for companies with a large number of instruments.
While the initial setup cost may be high, it allows greater flexibility in scheduling and reduces transport and third-party service costs.
Staff training and investment in good quality calibration standards are crucial to ensure the in-house lab meets the required standards.
4. Embrace Automation
Utilizing automated calibration solutions can greatly reduce the time and manpower needed for the calibration process.
Automation minimizes human error and ensures consistency and accuracy in testing procedures.
Investing in automated calibration equipment can be costly initially, but it often pays off through the savings made in labor and the reduced likelihood of costly errors.
Effective Management of Measuring Instruments
Beyond calibration, efficient management of measuring instruments is crucial for controlling costs and ensuring seamless operations.
1. Maintain an Up-to-Date Inventory
Having a current and accurate inventory of all measuring instruments is essential.
Using asset management software can help track the location, status, and history of each instrument, simplifying scheduling for calibrations and maintenance.
This minimizes the risk of missing equipment and ensures all devices are compliant with calibration schedules.
2. Prioritize Critical Instruments
Not all instruments are critical to operations.
Prioritizing the calibration and maintenance of instruments that have the most significant impact on production or quality can ensure resources are allocated effectively.
Critical instruments should be given higher priority to minimize their downtime and maintain operational integrity.
3. Train Staff Adequately
Proper training of staff responsible for handling measuring instruments can lead to better management and reduced mishaps.
Employees who are well-versed in handling and maintaining these instruments can help extend their lifespan and ensure they are used correctly, thus minimizing wear and tear and preventing costly repairs or replacements.
Leveraging Technology for Cost Efficiency
The role of technology in managing calibration and measuring instrument costs cannot be overstated.
Embracing advanced technologies such as IoT devices and cloud-based management systems provides real-time data and insights.
These technologies assist in maintaining a centralized database for monitoring instrument conditions, recording calibration history, and scheduling future calibrations.
By leveraging such systems, organizations can make informed decisions that enhance the efficiency of their operations and reduce expenditures on repairs, replacements, and unplanned downtime.
Employing a comprehensive and structured approach to calibration and instrument management can offer substantial cost savings while maintaining the integrity and accuracy of processes.
Through strategic planning and leveraging technology, businesses can sustain superior quality outputs in a cost-effective manner.
資料ダウンロード
QCD管理受発注クラウド「newji」は、受発注部門で必要なQCD管理全てを備えた、現場特化型兼クラウド型の今世紀最高の受発注管理システムとなります。
ユーザー登録
受発注業務の効率化だけでなく、システムを導入することで、コスト削減や製品・資材のステータス可視化のほか、属人化していた受発注情報の共有化による内部不正防止や統制にも役立ちます。
NEWJI DX
製造業に特化したデジタルトランスフォーメーション(DX)の実現を目指す請負開発型のコンサルティングサービスです。AI、iPaaS、および先端の技術を駆使して、製造プロセスの効率化、業務効率化、チームワーク強化、コスト削減、品質向上を実現します。このサービスは、製造業の課題を深く理解し、それに対する最適なデジタルソリューションを提供することで、企業が持続的な成長とイノベーションを達成できるようサポートします。
製造業ニュース解説
製造業、主に購買・調達部門にお勤めの方々に向けた情報を配信しております。
新任の方やベテランの方、管理職を対象とした幅広いコンテンツをご用意しております。
お問い合わせ
コストダウンが利益に直結する術だと理解していても、なかなか前に進めることができない状況。そんな時は、newjiのコストダウン自動化機能で大きく利益貢献しよう!
(β版非公開)