- お役立ち記事
- Know-how to utilize back gauge system for press brakes
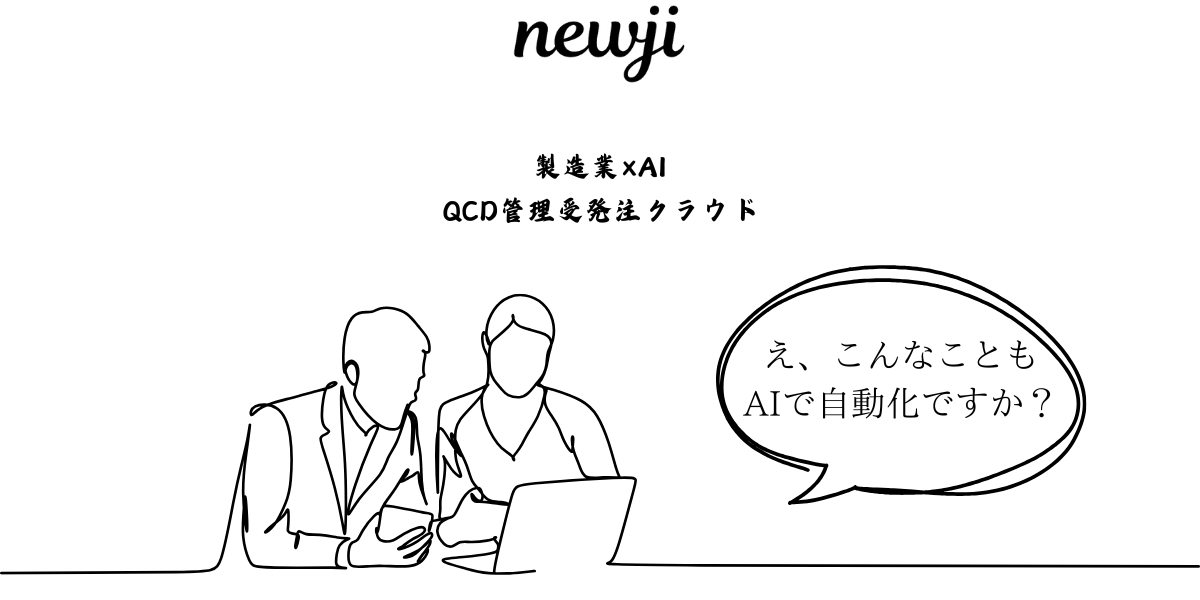
Know-how to utilize back gauge system for press brakes
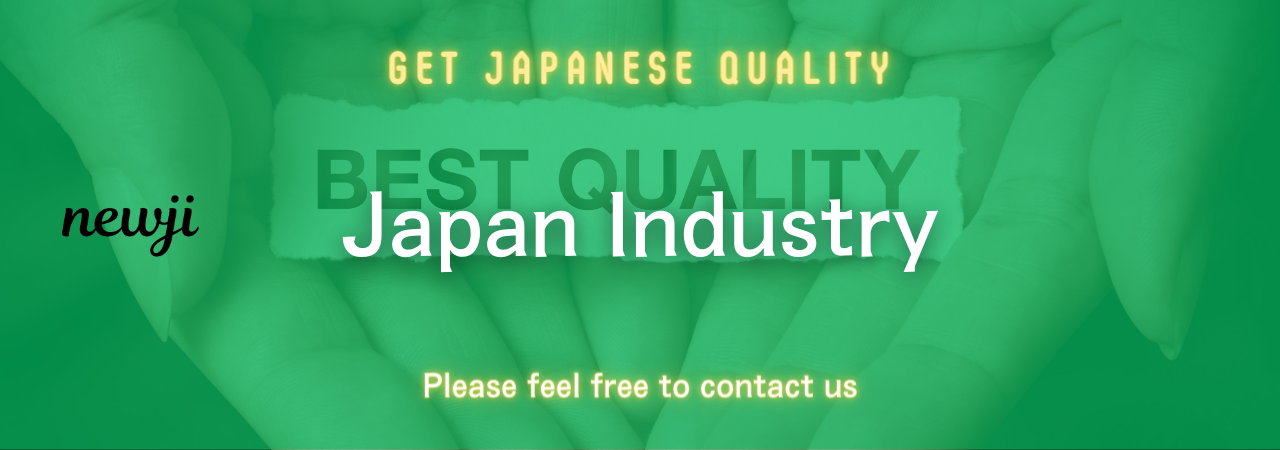
Understanding a Back Gauge System
A back gauge system on a press brake is a crucial component for achieving precision and consistency.
The back gauge is essentially a positioning tool that helps in aligning and securing metal sheets or workpieces.
This ensures accurate bending and shaping.
Without a back gauge system, getting precise bends would become a labor-intensive and time-consuming task.
Let’s delve into the ways you can utilize this system to its full potential.
目次
Setting Up the Back Gauge System
Initial Calibration
Before you start using your press brake, it’s essential to calibrate the back gauge system.
Calibration ensures that the gauge aligns perfectly with the bending line and the tooling.
Begin by referencing the manufacturer’s guidelines for calibration.
Make minor adjustments as needed until you achieve a perfect alignment.
It may require a few test bends to verify that the gauge is precisely set.
Custom Settings
Every project may have different requirements for metal bending.
Therefore, it’s beneficial to customize your back gauge settings for each specific project.
Utilize the control panel of your press brake to program specific measurements and angles.
Recording these settings can save you substantial time for future similar tasks.
Using the Back Gauge for Different Tasks
Single Bends
For a single bend, the setup is relatively straightforward.
Place your metal sheet against the back gauge and adjust the position according to the specified measurement.
Then, proceed to make the bend.
The back gauge ensures that the bend occurs at the exact location you desire.
Repeat Bending
In many industrial applications, you might need to produce multiple pieces with identical bends.
The back gauge system is ideal for this as it maintains consistent positioning throughout the production run.
Simply set the gauge to the required position, and you can repeat the process without constant readjustments.
This ensures uniformity in your output and reduces waste.
Maximizing Efficiency with the Back Gauge
Sequential Bending
For complex workpieces requiring multiple bends, you can use the back gauge to program a sequence of bends.
This feature is particularly useful for intricate designs and reducing manual intervention.
By setting the back gauge for different bends in sequence, you can automate part of the bending process.
This minimizes errors and improves overall efficiency.
Error Detection
Many modern back gauge systems come with error detection features.
These systems can alert you if there are inconsistencies or deviations from the programmed settings.
This safety feature is vital for preventing damage to the material and ensuring accuracy.
Always keep an eye on these alerts to maintain high-quality output.
Maintenance and Troubleshooting
Regular Inspection
Routine inspection of your back gauge system is essential for its longevity and consistent performance.
Check for wear and tear on the guide rails, sensors, and other moving parts.
Lubricate mechanical parts as recommended by the manufacturer to ensure smooth operation.
Replace any worn-out components promptly to avoid breakdowns.
Common Issues and Fixes
Over time, you might encounter issues like misalignment or inaccurate positioning.
These can usually be fixed by recalibrating the system.
For issues like sensor malfunctions, refer to the user manual for troubleshooting steps.
In severe cases, contact the manufacturer for professional assistance.
Safety Considerations
Proper Training
Operating a press brake with a back gauge system requires proper training.
Ensure that all operators are well-versed in using the back gauge and understand the safety protocols.
This includes wearing appropriate personal protective equipment (PPE) and adhering to standard operating procedures.
Emergency Stops
Modern press brakes are equipped with emergency stop features.
Familiarize yourself with the location and operation of these emergency stops.
In case of any malfunction or safety hazard, you can quickly halt the operation to prevent accidents.
Conclusion
A back gauge system is an invaluable tool for anyone working with a press brake.
It enhances accuracy, efficiency, and safety in metal bending tasks.
By properly setting up, maintaining, and utilizing the back gauge system, you can significantly improve your production quality.
Regular training and vigilance are key to maximizing the benefits of this essential component.
Investing time in understanding and optimizing the back gauge system will pay off in the form of better output and safer operations.
With these tips, you are now equipped to make the most out of your press brake’s back gauge system.
資料ダウンロード
QCD調達購買管理クラウド「newji」は、調達購買部門で必要なQCD管理全てを備えた、現場特化型兼クラウド型の今世紀最高の購買管理システムとなります。
ユーザー登録
調達購買業務の効率化だけでなく、システムを導入することで、コスト削減や製品・資材のステータス可視化のほか、属人化していた購買情報の共有化による内部不正防止や統制にも役立ちます。
NEWJI DX
製造業に特化したデジタルトランスフォーメーション(DX)の実現を目指す請負開発型のコンサルティングサービスです。AI、iPaaS、および先端の技術を駆使して、製造プロセスの効率化、業務効率化、チームワーク強化、コスト削減、品質向上を実現します。このサービスは、製造業の課題を深く理解し、それに対する最適なデジタルソリューションを提供することで、企業が持続的な成長とイノベーションを達成できるようサポートします。
オンライン講座
製造業、主に購買・調達部門にお勤めの方々に向けた情報を配信しております。
新任の方やベテランの方、管理職を対象とした幅広いコンテンツをご用意しております。
お問い合わせ
コストダウンが利益に直結する術だと理解していても、なかなか前に進めることができない状況。そんな時は、newjiのコストダウン自動化機能で大きく利益貢献しよう!
(Β版非公開)