- お役立ち記事
- Knowledge of procurement and purchasing departments to prevent quality problems of processed goods in the manufacturing industry
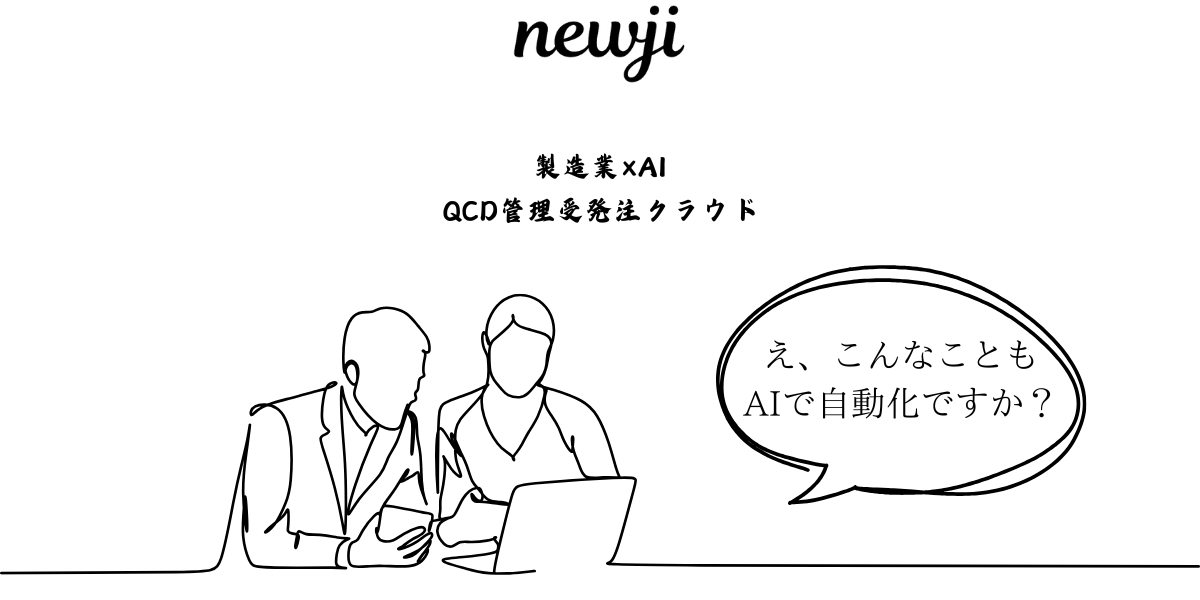
Knowledge of procurement and purchasing departments to prevent quality problems of processed goods in the manufacturing industry
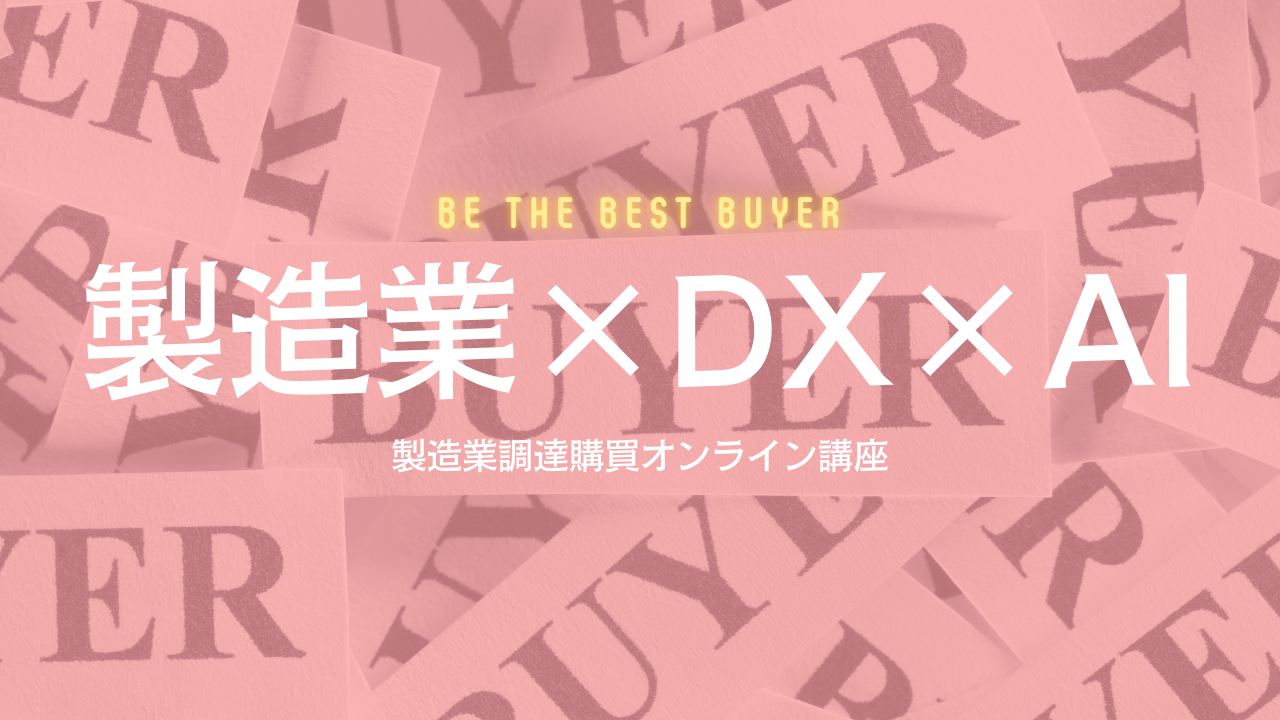
With manufacturing being such a competitive market, having high quality products is essential for businesses to be successful. Customers will not want to buy products that are faulty or break easily. This is why it is important for manufacturing companies to have procurement and purchasing departments that ensure all materials and components going into products meet strict quality standards. These departments play a key role in preventing quality issues down the line during production.
The procurement and purchasing teams are responsible for identifying suppliers of raw materials and parts needed for manufacturing. They research potential suppliers to find ones that have a proven track record of delivering consistently high quality goods. Things they might look at include how long suppliers have been in business, certifications like ISO 9001 they maintain, product defect rates, and reviews from other customers. Developing long term partnerships with suppliers who prioritize quality makes issues less likely to occur.
Once suppliers are selected, purchasing takes the lead on negotiating contracts that include commitments around quality. Key aspects to include are clear specifications for the goods being ordered, tolerance levels for acceptable variations, packaging and handling requirements, and procedures for inspections and testing. Consequences for failures to meet standards such as financial penalties or order cancellations should be outlined. Having these expectations agreed to and documented up front sets suppliers up for success in fulfilling orders properly.
Purchasing teams need to implement a robust receiving inspection process. When shipments arrive from suppliers, a percentage should be selected for thorough incoming testing and inspection. Properties examined may include chemical composition, dimensions, finish, packaging integrity, and more depending on the material. Advanced techniques like x-rays and ultrasound can detect internal flaws invisible to the naked eye. Any issues found must be reported back to the supplier for corrective action so they do not continue providing subpar goods.
Inventory management practices also impact quality. Materials and components must be stored appropriately based on their properties. For example, electronic components may need temperature controlled warehouses while chemicals require ventilated storage. First in, first out (FIFO) procedures should be followed to ensure older stock is used first before it expires. Regular cycle counts and condition checks can find expired, damaged, or mislabeled items that pose quality risks if used in production.
During the production planning process, enough time must be allocated for quality assurance checks. Lines should not be overloaded to the point where thorough checks cannot reasonably be performed. Quality control inspectors need to sample finished products at various stages – in-process, post-process, and final product. They look for defects and ensure specs are still being met as the product progresses through manufacturing. Issues found can be followed up on to determine if problems originated from incoming materials, tools, or the production process itself.
If defects become apparent, purchasing and procurement are key to resolving supplier quality problems. They facilitate communications between manufacturing quality and the supplier to clearly explain the nature of the defects. Root cause analysis with the supplier helps determine if materials need reformulating, machining processes adjusted, packaging revised, or something else changed. Corrective actions must be agreed upon and verification that the changes resolve the problem is required before orders resume. Ongoing monitoring of the supplier also occurs to prevent recurrences.
Finally, purchasing keeps records of supplier performance metrics. These include things like total defect rates, number of corrective actions needed, on-time delivery percentages, and customer satisfaction scores if obtained from other buyers. Trending this data over time can uncover suppliers whose quality is deteriorating or unexpectedly improving. It prompts discussions for continuous improvement or informs decisions about contract renewals and new business awards. The goal is leveraging procurement and purchasing expertise to proactively manage supplier relationships and head off quality issues before they threaten a company’s products and reputation.
In summary, having knowledgeable procurement and purchasing teams focused on supplier quality management is crucial for manufacturers. Their efforts in supplier selection, contract requirements, receiving inspections, inventory controls, and resolving problems keep imperfections out of incoming materials and components. This prevents defects from occurring downstream during production and reaching the customer. The result is high quality, reliable manufactured goods that customers will want to keep buying. Manufacturers who invest in developing their procurement and purchasing functions will see the benefits in increased competitiveness, productivity, and profits over the long run.
資料ダウンロード
QCD調達購買管理クラウド「newji」は、調達購買部門で必要なQCD管理全てを備えた、現場特化型兼クラウド型の今世紀最高の購買管理システムとなります。
ユーザー登録
調達購買業務の効率化だけでなく、システムを導入することで、コスト削減や製品・資材のステータス可視化のほか、属人化していた購買情報の共有化による内部不正防止や統制にも役立ちます。
NEWJI DX
製造業に特化したデジタルトランスフォーメーション(DX)の実現を目指す請負開発型のコンサルティングサービスです。AI、iPaaS、および先端の技術を駆使して、製造プロセスの効率化、業務効率化、チームワーク強化、コスト削減、品質向上を実現します。このサービスは、製造業の課題を深く理解し、それに対する最適なデジタルソリューションを提供することで、企業が持続的な成長とイノベーションを達成できるようサポートします。
オンライン講座
製造業、主に購買・調達部門にお勤めの方々に向けた情報を配信しております。
新任の方やベテランの方、管理職を対象とした幅広いコンテンツをご用意しております。
お問い合わせ
コストダウンが利益に直結する術だと理解していても、なかなか前に進めることができない状況。そんな時は、newjiのコストダウン自動化機能で大きく利益貢献しよう!
(Β版非公開)