- お役立ち記事
- Laser Cutting Technology and Its Applications in Metal Factories
Laser Cutting Technology and Its Applications in Metal Factories
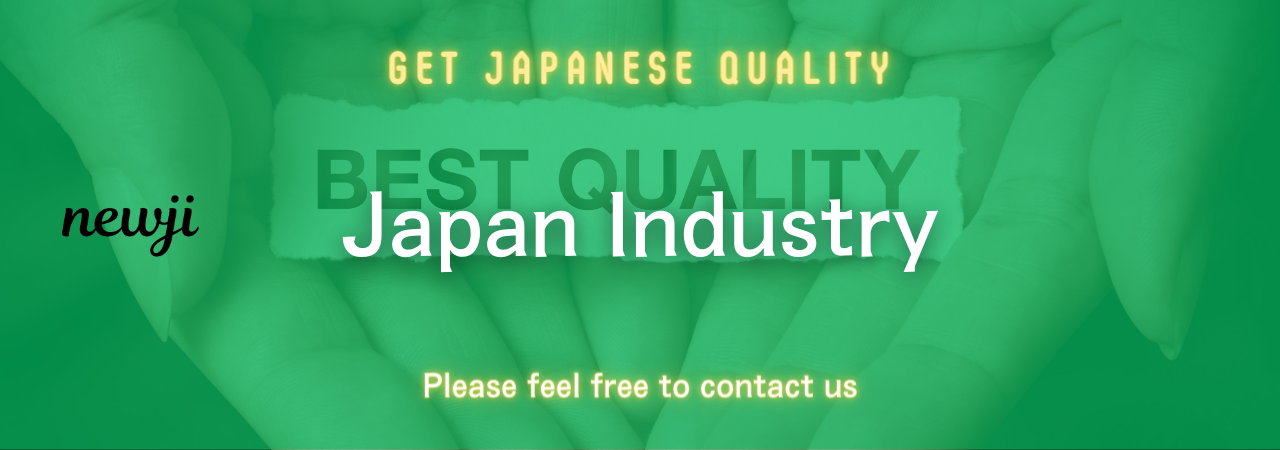
目次
Understanding Laser Cutting Technology
Laser cutting technology is a precise and efficient process used primarily in metal fabrication.
This technology utilizes a high-powered laser beam to cut, shape, or engrave materials into desired shapes and sizes.
The laser beam melts, burns, or vaporizes the material, allowing for clean edges and intricate designs.
Laser cutting is versatile, capable of handling a wide range of metals such as steel, aluminum, and copper.
This adaptability makes it a popular choice in various industries, including automotive, aerospace, and electronics.
The precision of laser cutting technology ensures that even the most complex designs are executed with a high degree of accuracy.
How Laser Cutting Works
At its core, laser cutting relies on a focused beam of light that is guided and controlled by computer programming.
The laser beam is generated by a laser resonator, which directs the beam through an optical path onto the workpiece.
Once the laser hits the material, it begins to cut through by melting or vaporizing the target area.
There are different types of lasers used in cutting processes, including CO2 lasers, fiber lasers, and YAG lasers.
CO2 lasers are typically used for cutting non-metal materials, whereas fiber lasers are more suited for metal cutting due to their ability to produce higher intensity beams.
YAG lasers, on the other hand, are often used for engraving and marking applications.
The precision of the laser cutting process is largely attributed to CNC (computer numerical control) technology.
CNC machines provide the guidance needed to control the movement of the laser, ensuring precise cuts and minimal waste.
Advantages of Laser Cutting in Metal Factories
One of the most significant advantages of using laser cutting technology in metal factories is the precision it offers.
Laser cutting allows for exact measurements and clean, burr-free edges, reducing the need for additional finishing processes.
This not only saves time but also reduces costs associated with production.
Another advantage is the speed with which laser cutting can be conducted.
Compared to traditional cutting methods, laser cutters can execute tasks much more quickly, increasing production efficiency.
Speed is particularly crucial in industries where time-to-market is a competitive advantage.
Moreover, laser cutting is a versatile technology that can handle complex geometries.
It can easily cut intricate patterns and complex designs that would be challenging to achieve through other methods.
This level of detail is essential in industries such as aerospace, where precision is paramount.
Laser cutting also minimizes material waste.
Traditional cutting methods often result in excess material, but laser cutting is precise, reducing waste and thus saving on material costs.
Applications of Laser Cutting in Metal Factories
Laser cutting technology is employed in numerous applications within metal factories.
One of the common uses is in the manufacturing of automotive parts.
The ability to produce detailed and precise metal parts makes laser cutting indispensable in this industry.
Automakers rely on this technology to produce components such as gears, panels, and brackets with high precision.
The aerospace industry also benefits significantly from laser cutting.
The precision and consistency of laser cutters are crucial for manufacturing parts that must meet stringent specifications and safety standards.
Components such as turbine blades, engine parts, and structural framework are often produced using laser cutting technology.
In the electronics industry, laser cutting is used to fabricate components for circuits and protective casings.
The technology’s ability to cut complex shapes and tiny details with precision is invaluable in producing parts for various electronic devices.
In addition to these industries, metal fabrication shops frequently use laser cutting to produce custom metal pieces for various applications.
From decorative architectural elements to custom metal signage, the possibilities are endless with laser cutting technology.
Future Trends in Laser Cutting Technology
The future of laser cutting technology holds promising developments that could revolutionize metal manufacturing further.
One trend is the increasing integration of automation in laser cutting processes.
Automation can enhance productivity by allowing machines to operate continuously with minimal human intervention.
This leads to higher efficiency and reduced labor costs.
Another trend is improving the energy efficiency of lasers.
As technology advances, laser systems are becoming more energy-efficient, reducing operational costs and environmental impact.
Energy-efficient lasers are particularly beneficial in large-scale manufacturing where energy consumption is a significant concern.
Additionally, advances in laser technology continue to improve cutting speeds and precision.
With ongoing research and development, lasers are able to cut faster, with finer tolerances and superior finish quality.
These advancements further extend the range of applications for laser cutting technology.
Conclusion
Laser cutting technology has become an indispensable tool in the metal fabrication industry.
Its precision, speed, and versatility make it ideal for various applications, from automotive to aerospace and beyond.
As the technology continues to evolve, it promises even greater efficiencies and more applications in the future.
Incorporating laser cutting into metal factories not only enhances production capabilities but also provides a competitive edge in today’s fast-paced industrial environment.
With ongoing innovations, laser cutting technology is set to remain at the forefront of manufacturing processes for years to come.
資料ダウンロード
QCD調達購買管理クラウド「newji」は、調達購買部門で必要なQCD管理全てを備えた、現場特化型兼クラウド型の今世紀最高の購買管理システムとなります。
ユーザー登録
調達購買業務の効率化だけでなく、システムを導入することで、コスト削減や製品・資材のステータス可視化のほか、属人化していた購買情報の共有化による内部不正防止や統制にも役立ちます。
NEWJI DX
製造業に特化したデジタルトランスフォーメーション(DX)の実現を目指す請負開発型のコンサルティングサービスです。AI、iPaaS、および先端の技術を駆使して、製造プロセスの効率化、業務効率化、チームワーク強化、コスト削減、品質向上を実現します。このサービスは、製造業の課題を深く理解し、それに対する最適なデジタルソリューションを提供することで、企業が持続的な成長とイノベーションを達成できるようサポートします。
オンライン講座
製造業、主に購買・調達部門にお勤めの方々に向けた情報を配信しております。
新任の方やベテランの方、管理職を対象とした幅広いコンテンツをご用意しております。
お問い合わせ
コストダウンが利益に直結する術だと理解していても、なかなか前に進めることができない状況。そんな時は、newjiのコストダウン自動化機能で大きく利益貢献しよう!
(Β版非公開)