- お役立ち記事
- Laser welding/welding and laser processing technology and its application to joining dissimilar materials
月間77,185名の
製造業ご担当者様が閲覧しています*
*2025年2月28日現在のGoogle Analyticsのデータより
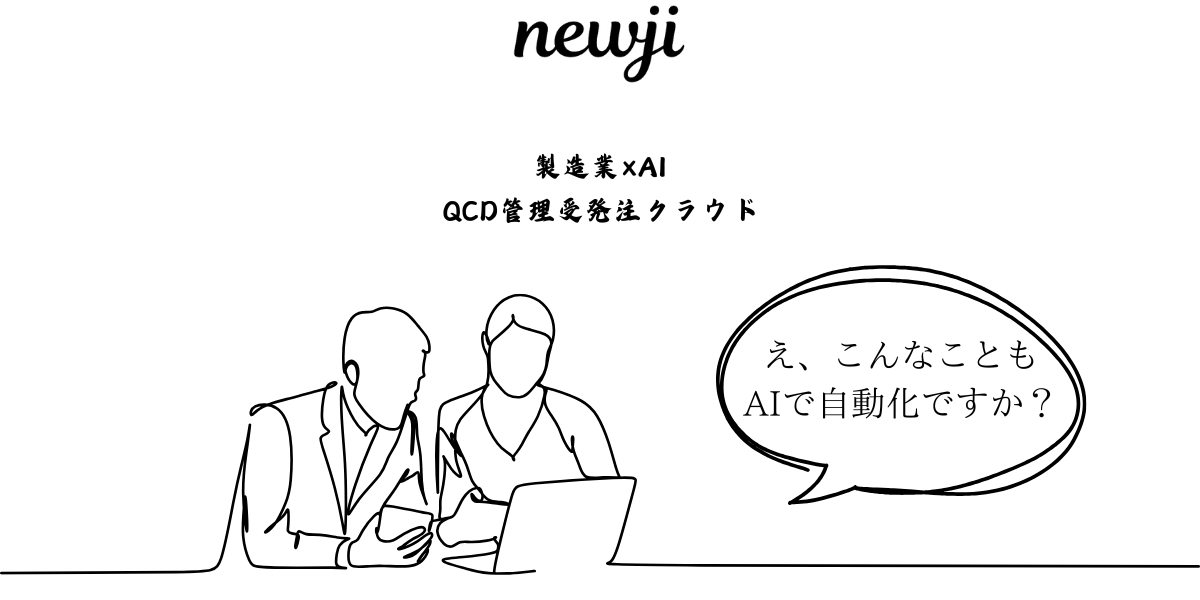
Laser welding/welding and laser processing technology and its application to joining dissimilar materials
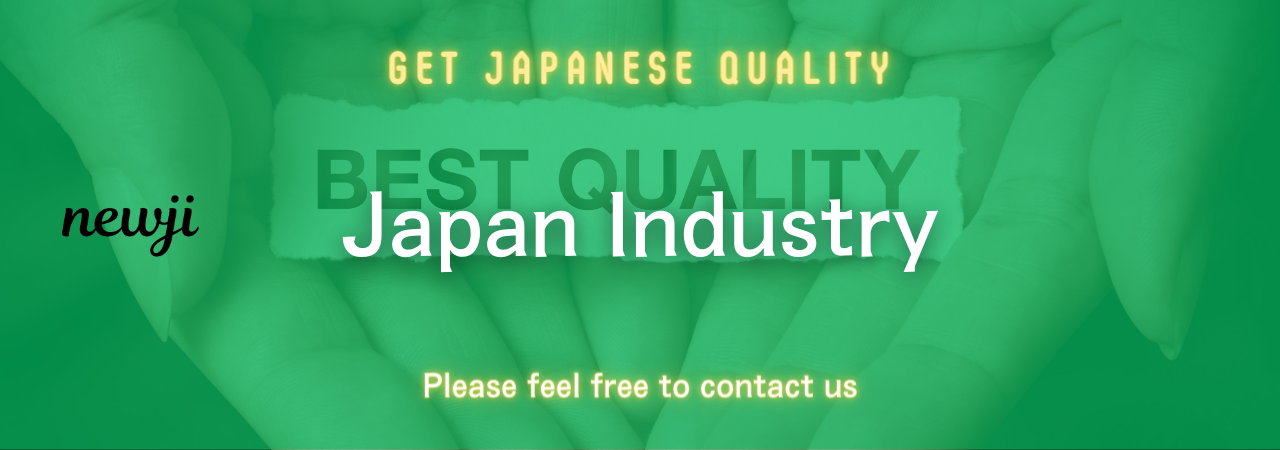
目次
Introduction to Laser Welding
Laser welding is a revolutionary technology that has transformed the manufacturing industry with its precision and efficiency.
At its core, laser welding involves using a concentrated beam of light to melt and join materials, primarily metals and thermoplastics.
This method stands out due to its ability to provide high-speed, precise welds in various applications, whether it be in the automotive, aerospace, or electronics industries.
Principles of Laser Welding
Laser welding operates by focusing a beam of laser light onto the surfaces to be joined.
The beam delivers energy that heats the material to its melting point, creating a molten pool.
As the materials cool, they solidify and form a strong weld seam.
This process is particularly beneficial for situations requiring intricate detail and minimal thermal distortion.
Types of Laser Welds
There are several types of laser welds, with conduction, conduction/penetration, and keyhole welding being the most prominent.
– **Conduction Welding**: Utilizes a lower power density laser, resulting in shallow welds limited to the surface of the material.
– **Conduction/Penetration Welding**: A hybrid approach that merges the benefits of conduction with deeper penetration.
– **Keyhole Welding**: Employs high power density to create deep welds with minimal surface width, ideal for thick materials.
Laser Welding Equipment
Laser welding setups can vary depending on the application but generally consist of a laser source, delivery system, and a focusing optic.
Several types of lasers are prevalent in welding applications:
Types of Lasers Used
– **Fiber Lasers**: Known for their efficiency and compact size, fiber lasers are ideal for high-precision welding tasks.
– **Nd:YAG Lasers**: These solid-state lasers are effective for deep penetration welding and are highly versatile.
– **CO2 Lasers**: Commonly used in industrial applications for their ability to cut and weld thick materials.
Components of a Laser Welding System
– **Laser Source**: Provides the concentrated beam of light.
– **Beam Delivery**: Composed of optical fibers or mirrors that direct the laser to the welding area.
– **Focusing Optic**: Concentrates the laser on the specific spot, allowing accurate heat application.
Advantages of Laser Welding
The popularity of laser welding is due to its numerous benefits, which include:
Precision and Quality
Laser welding provides unparalleled precision, allowing intricate details to be accomplished with minimal distortion.
This results in a high-quality weld that often requires little to no post-processing.
Moreover, the narrow heat-affected zone (HAZ) minimizes defects and residual stress in the welded material.
Speed and Efficiency
The speed of laser welding is another advantage, with faster welding processes compared to traditional methods.
This rapid execution leads to increased productivity and reduced lead times.
Additionally, laser welding can be automated, further enhancing its efficiency and consistency.
Versatility
Laser welding is highly versatile, capable of joining a wide range of materials, including different thicknesses.
It supports welding in hard-to-reach areas and complex geometries, making it ideal for a variety of industrial applications.
Applications of Laser Welding
Laser welding has a broad spectrum of applications because of its efficiency and versatility.
Automotive Industry
In the automotive sector, laser welding is used to assemble car bodies and other components.
It’s particularly useful for providing strong, lightweight joints that are crucial for constructing fuel-efficient vehicles.
Aerospace Industry
In aerospace, precision is paramount, and laser welding delivers just that.
It’s used in the fabrication of aircraft components, providing strong and reliable joints for critical parts.
Electronics Industry
The electronics sector benefits from laser welding for its ability to join delicate components without causing damage.
Joining Dissimilar Materials
One of the notable applications of laser welding is its capability to join dissimilar materials.
Traditional welding methods often face challenges when attempting to weld different materials due to variations in melting points and thermal expansion coefficients.
Overcoming Challenges
Laser welding addresses these challenges through its precision and control of the heat input.
The precise energy application allows materials with different properties to be joined effectively.
Innovations in Material Joining
Advancements in laser welding technology have led to innovative solutions in joining dissimilar materials.
For instance, laser welding is increasingly used in hybrid joining processes, where it is combined with adhesive bonding or mechanical fasteners to enhance joint strength and durability.
Future Prospects
As industries continue to demand higher efficiency and precision, the role of laser welding is expected to expand even further.
Future advancements may focus on improving the accessibility of laser welding technology for a broader range of applications, including in small to medium-sized enterprises.
Research and Development
Ongoing research is likely to yield improvements in laser sources, beam delivery systems, and focusing optics, which will enhance the capabilities of laser welding even more.
Sustainability and Cost-Effectiveness
Moreover, as sustainability becomes a major focus, laser welding’s potential to reduce material waste and energy consumption positions it as an eco-friendly manufacturing solution.
Conclusion
Laser welding represents a significant leap forward in manufacturing technology, offering precision, efficiency, and versatility.
Its ability to join dissimilar materials opens up new possibilities in design and assembly, making it indispensable across various industries.
As technology evolves, the applications and benefits of laser welding are set to grow, making it a crucial component of modern manufacturing processes.
資料ダウンロード
QCD管理受発注クラウド「newji」は、受発注部門で必要なQCD管理全てを備えた、現場特化型兼クラウド型の今世紀最高の受発注管理システムとなります。
ユーザー登録
受発注業務の効率化だけでなく、システムを導入することで、コスト削減や製品・資材のステータス可視化のほか、属人化していた受発注情報の共有化による内部不正防止や統制にも役立ちます。
NEWJI DX
製造業に特化したデジタルトランスフォーメーション(DX)の実現を目指す請負開発型のコンサルティングサービスです。AI、iPaaS、および先端の技術を駆使して、製造プロセスの効率化、業務効率化、チームワーク強化、コスト削減、品質向上を実現します。このサービスは、製造業の課題を深く理解し、それに対する最適なデジタルソリューションを提供することで、企業が持続的な成長とイノベーションを達成できるようサポートします。
製造業ニュース解説
製造業、主に購買・調達部門にお勤めの方々に向けた情報を配信しております。
新任の方やベテランの方、管理職を対象とした幅広いコンテンツをご用意しております。
お問い合わせ
コストダウンが利益に直結する術だと理解していても、なかなか前に進めることができない状況。そんな時は、newjiのコストダウン自動化機能で大きく利益貢献しよう!
(β版非公開)