- お役立ち記事
- Latest Burr Prevention Technologies and Successful Case Studies
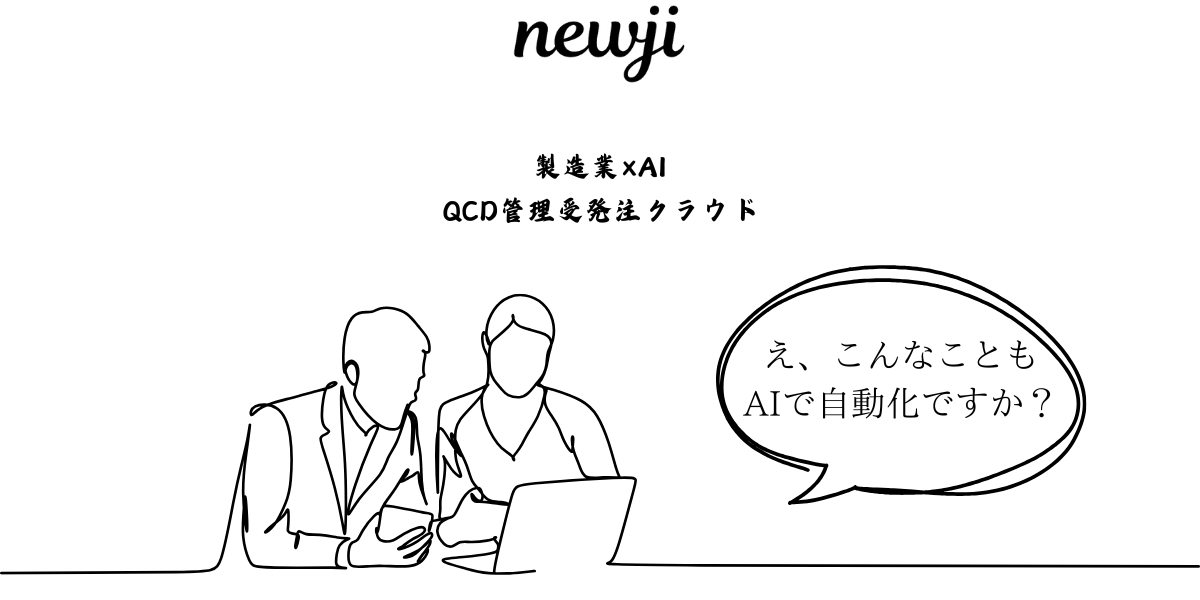
Latest Burr Prevention Technologies and Successful Case Studies
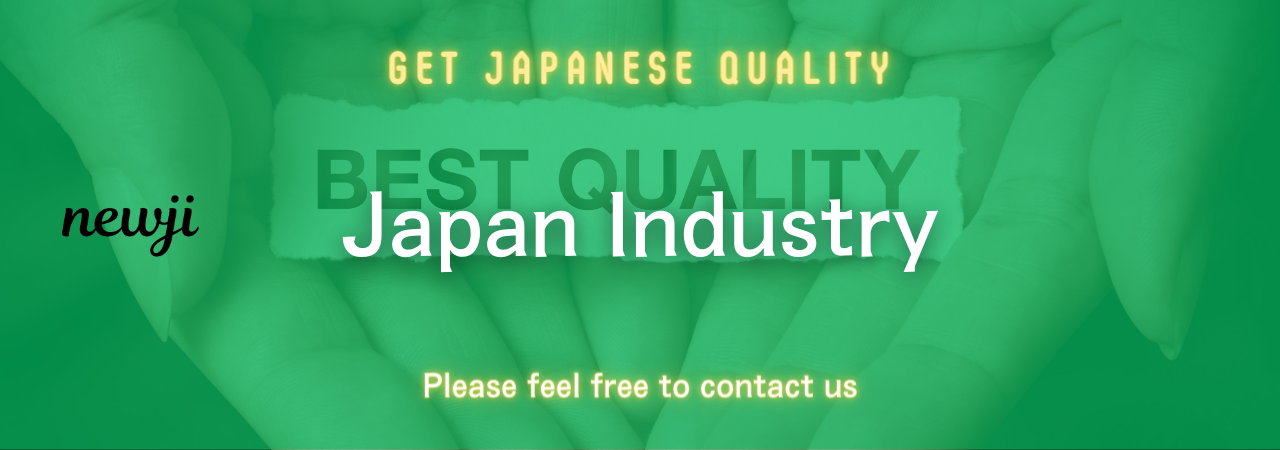
目次
Understanding Burrs and Their Impact
Burrs are small, often sharp projections or raised edges on a material after machining processes such as drilling, milling, or turning.
They can occur in metals, plastics, and other materials.
While they may seem like minor imperfections, burrs can cause significant problems in manufacturing and assembly.
They can interfere with assembly operations, cause misalignment, or even lead to mechanical failures if not properly managed.
Additionally, burrs can pose safety hazards to workers handling machined parts.
In recent years, there has been a growing focus on burr prevention technologies that aim to minimize or eliminate burrs during the machining process.
These advancements not only improve product quality but also reduce manufacturing costs and enhance safety.
The Evolution of Burr Prevention Technologies
Over the decades, various methods have been developed to address the issue of burrs in manufacturing.
Initially, manual deburring was the standard practice, requiring workers to manually file or scrape away burrs, a process that was labor-intensive and time-consuming.
As technology advanced, automated deburring systems were introduced, utilizing machines to remove burrs more efficiently and consistently than manual methods.
Today, burr prevention technologies have further evolved, incorporating advanced techniques and tools to prevent burrs from forming during the machining process.
Manufacturers are increasingly focusing on designing processes that inherently minimize burr formation, rather than only relying on post-process deburring.
Modern Techniques for Burr Prevention
Several modern techniques have been developed to prevent burr formation during machining:
1. **Tool Design and Geometry**: Optimizing the design and geometry of the cutting tools can significantly reduce the likelihood of burr formation.
By using tools with the right angles and edge sharpness, manufacturers can achieve cleaner cuts with minimal burrs.
2. **Cutting Conditions**: Adjusting the cutting speed, feed rate, and depth of cut can influence the formation of burrs.
Fine-tuning these parameters based on the material and tool being used can result in smoother machining operations.
3. **Advanced Machining Techniques**: High-speed machining and precision grinding are some of the advanced machining techniques that help in minimizing burr formation.
These methods allow for faster and more accurate cuts, reducing the opportunity for burrs to develop.
4. **Coolants and Lubricants**: Using appropriate coolants and lubricants can reduce friction and heat during machining, which in turn decreases the likelihood of burrs forming on the workpiece.
Successful Case Studies in Burr Prevention
Let’s explore some successful case studies where companies have effectively implemented burr prevention technologies to improve operations:
Case Study 1: Automotive Industry
An automotive manufacturer faced issues with burrs on metal components, leading to frequent assembly line stoppages and quality control challenges.
The company decided to implement a comprehensive burr prevention strategy, which included optimizing cutting tool designs and using high-performance lubricants.
By integrating these changes into their machining processes, the company achieved a 70% reduction in burr-related defects, resulting in increased production efficiency and reduced downtime.
Case Study 2: Aerospace Sector
A leading aerospace parts manufacturer encountered problems with burrs affecting the precision and performance of their components.
After conducting an in-depth analysis, they invested in high-speed machining equipment and employed precision grinding techniques.
This upgrade not only minimized burr formation but also enhanced the surface finish of their products, leading to improved customer satisfaction and a competitive advantage in the market.
Case Study 3: Electronics Manufacturing
In the electronics manufacturing industry, a company producing small components for consumer electronics was experiencing issues with burrs affecting the functionality of their products.
The company implemented a process optimization strategy that involved selecting optimal cutting conditions and using advanced tool geometries.
This approach led to nearly complete elimination of burrs, reducing product rejections and improving overall product quality.
Future Trends in Burr Prevention
The future of burr prevention technologies looks promising, with continuous advancements on the horizon:
1. **AI and Machine Learning**: Incorporating AI and machine learning algorithms into machining processes can allow for real-time monitoring and adjustments, minimizing burr formation proactively.
2. **Improved Tool Materials**: The development of new tool materials with enhanced wear resistance and cutting capabilities will contribute to reduced burr formation.
3. **Sustainable Practices**: As the industry shifts towards sustainability, there will be a focus on eco-friendly coolants and lubricants that not only prevent burrs but also minimize environmental impact.
4. **Digital Twins**: The use of digital twin technology can simulate and optimize machining processes before they are executed, identifying potential burr issues and allowing for solutions to be implemented in advance.
Conclusion
Burr prevention is becoming an increasingly important aspect of modern manufacturing.
As manufacturers strive for higher quality, productivity, and safety, adopting advanced burr prevention technologies becomes essential.
By understanding and implementing the latest methods, companies can enhance their production processes and deliver superior products to their customers.
The future of burr prevention holds great potential, with technological advancements paving the way for more efficient and sustainable manufacturing practices.
資料ダウンロード
QCD調達購買管理クラウド「newji」は、調達購買部門で必要なQCD管理全てを備えた、現場特化型兼クラウド型の今世紀最高の購買管理システムとなります。
ユーザー登録
調達購買業務の効率化だけでなく、システムを導入することで、コスト削減や製品・資材のステータス可視化のほか、属人化していた購買情報の共有化による内部不正防止や統制にも役立ちます。
NEWJI DX
製造業に特化したデジタルトランスフォーメーション(DX)の実現を目指す請負開発型のコンサルティングサービスです。AI、iPaaS、および先端の技術を駆使して、製造プロセスの効率化、業務効率化、チームワーク強化、コスト削減、品質向上を実現します。このサービスは、製造業の課題を深く理解し、それに対する最適なデジタルソリューションを提供することで、企業が持続的な成長とイノベーションを達成できるようサポートします。
オンライン講座
製造業、主に購買・調達部門にお勤めの方々に向けた情報を配信しております。
新任の方やベテランの方、管理職を対象とした幅広いコンテンツをご用意しております。
お問い合わせ
コストダウンが利益に直結する術だと理解していても、なかなか前に進めることができない状況。そんな時は、newjiのコストダウン自動化機能で大きく利益貢献しよう!
(Β版非公開)