- お役立ち記事
- Latest casting technology to prevent defects and defects in die casting, and technology to improve quality and extend the life of molds
月間77,185名の
製造業ご担当者様が閲覧しています*
*2025年2月28日現在のGoogle Analyticsのデータより
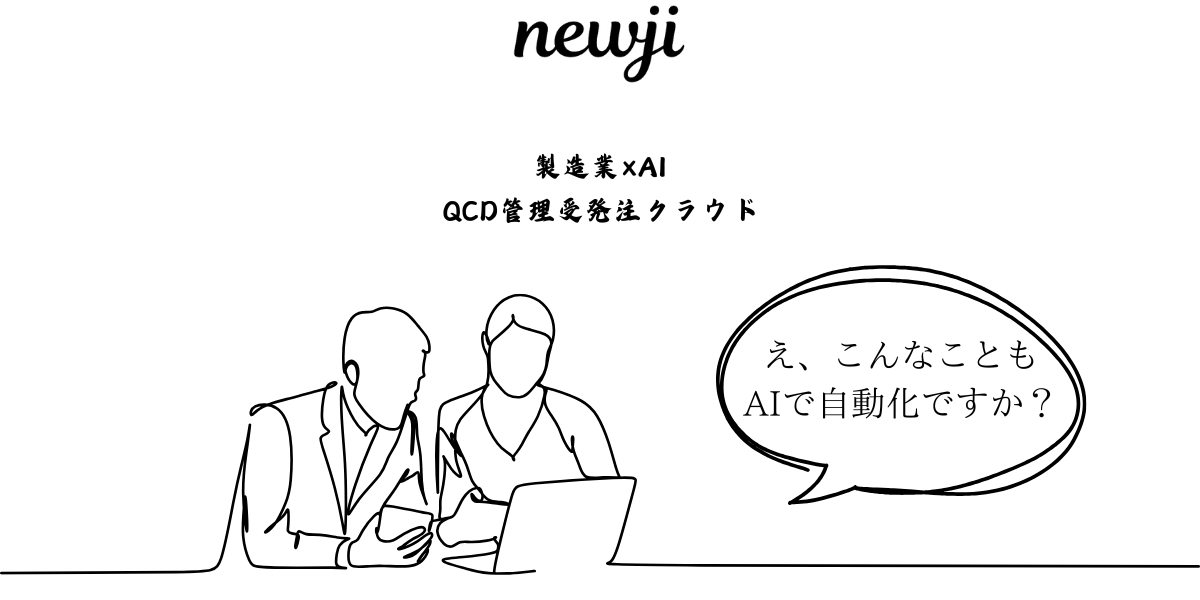
Latest casting technology to prevent defects and defects in die casting, and technology to improve quality and extend the life of molds
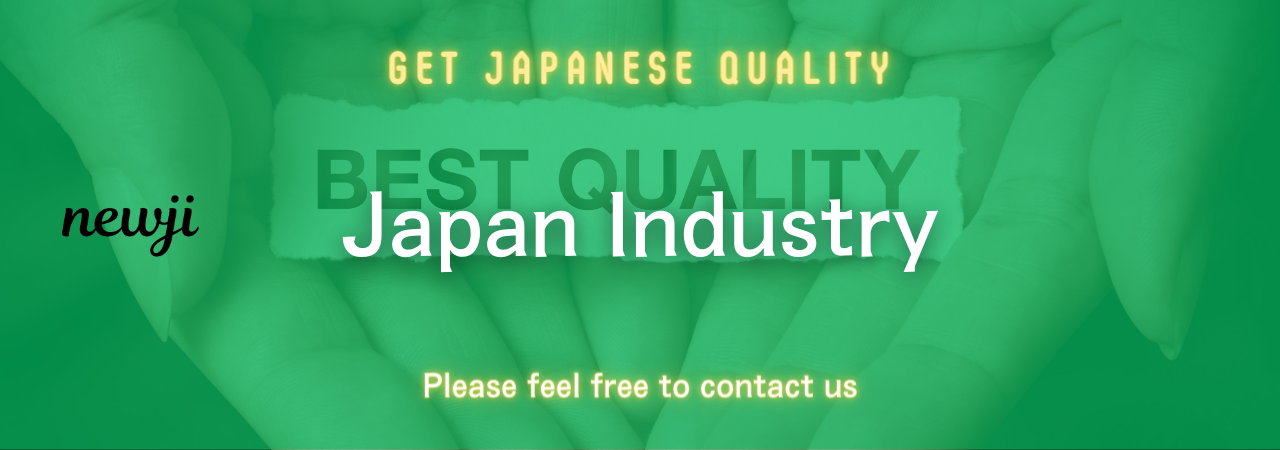
目次
Introduction to Die Casting and Its Importance
Die casting is a popular manufacturing process that involves forcing molten metal into a steel mold or die under high pressure.
This method is widely used in industries like automotive, aerospace, and consumer electronics due to its ability to produce complex shapes with high dimensional accuracy and excellent surface quality.
However, like any manufacturing process, die casting is susceptible to defects that can compromise the quality and lifespan of the final product.
Understanding Die Casting Defects
Defects in die casting can arise from various factors such as improper temperature control, inadequate venting, and poor die design.
Common defects include porosity, cold shuts, shrinkage, and warping.
Porosity occurs when gas is trapped within the mold, leading to air bubbles and voids in the final product.
Cold shuts happen when two streams of molten metal do not fuse properly, resulting in weak joints.
Shrinkage, the result of improper cooling, causes sections of the metal to contract unevenly, while warping leads to distorted and misshapen parts.
Latest Casting Technologies to Prevent Defects
To minimize these defects, manufacturers are increasingly adopting advanced casting technologies.
These innovations focus on improving precision, enhancing control over the casting process, and extending the life of molds.
Vacuum Die Casting
One of the most notable advancements in casting technology is vacuum die casting.
By creating a vacuum within the mold, this technique significantly reduces the presence of air and gas inclusions, thereby minimizing porosity.
The result is die-cast parts with higher integrity and improved mechanical properties.
Vacuum die casting is particularly beneficial for applications where high strength and lightweight components are crucial, such as in the automotive and aerospace industries.
Low-Pressure Die Casting
Another effective method is low-pressure die casting, which operates by filling the die with molten metal under low pressure.
This method allows for better control of the filling process, reducing turbulence and the risk of air entrapment.
As a result, the final parts exhibit fewer defects and enhanced consistency in quality.
Furthermore, low-pressure casting is beneficial for producing larger components with complex geometries.
Hot Chamber vs. Cold Chamber Die Casting
Both hot chamber and cold chamber die casting techniques continue to evolve, with technological improvements aimed at reducing defects.
In hot chamber die casting, where the metal chamber is submerged in the molten metal, advanced materials and coatings are used to prevent corrosion and improve the durability of die components.
Cold chamber die casting, suited for metals with high melting points, benefits from improved thermal management systems and automation, ensuring precise control over the casting process.
Quality Improvement Techniques
Quality improvement in die casting not only involves minimizing defects but also enhancing the overall properties of cast parts.
Various techniques have been developed to achieve these objectives, ensuring the final products meet stringent industry standards.
Metal Filtration
Metal filtration during the melting process is a critical step in ensuring high-quality die-cast parts.
Filters remove impurities and non-metallic inclusions that could compromise the structural integrity and aesthetic finish of the cast parts.
By using modern filtration systems, manufacturers can significantly improve the homogeneity and quality of the final product.
Optimized Die Design
Die design plays a crucial role in the quality of die-cast products.
Computer-aided design (CAD) software and simulation tools allow engineers to optimize die design by predicting potential defects and addressing them during the development phase.
Simulations can model the flow of molten metal within the die, helping designers to identify areas prone to defects and modify designs accordingly.
This proactive approach reduces the need for costly and time-consuming adjustments after the tool is manufactured.
Extending the Life of Molds
Mold maintenance is essential for ensuring long-term quality and cost-efficiency in die casting operations.
With advances in technology, several strategies have emerged to extend the life of molds.
Surface Coatings and Treatments
Surface coatings and treatments are applied to molds to enhance their resistance to thermal shock, corrosion, and wear.
Techniques such as thermal spray coatings and physical vapor deposition (PVD) create a robust barrier between molten metal and the mold surface.
These treatments not only protect the mold but also improve the surface finish of the cast parts.
Regular Maintenance and Repair
A systematic maintenance schedule is crucial for maximizing mold lifespan.
Regular inspections help detect early signs of wear or damage, allowing for timely repairs before the issues become severe.
By implementing a predictive maintenance approach, manufacturers can minimize unexpected downtime and extend the overall productivity of their casting operations.
Advanced Monitoring Systems
The integration of advanced monitoring systems in die casting facilities enables real-time tracking of mold conditions.
Sensors can measure key parameters such as temperature, pressure, and cycle times, providing valuable data to predict mold lifespan and optimize processing conditions.
This data-driven approach aligns with Industry 4.0 initiatives, paving the way for smarter and more efficient manufacturing processes.
Conclusion: Embracing Innovation in Die Casting
The latest advancements in casting technology offer significant potential for reducing defects, improving product quality, and extending mold life in die casting.
By embracing techniques such as vacuum and low-pressure casting, optimizing die design, and utilizing advanced maintenance practices, manufacturers can achieve unprecedented levels of efficiency and reliability.
As the industry continues to evolve, staying at the forefront of technology will be key to ensuring competitive advantage and meeting the ever-growing demands for high-quality die-cast products.
資料ダウンロード
QCD管理受発注クラウド「newji」は、受発注部門で必要なQCD管理全てを備えた、現場特化型兼クラウド型の今世紀最高の受発注管理システムとなります。
ユーザー登録
受発注業務の効率化だけでなく、システムを導入することで、コスト削減や製品・資材のステータス可視化のほか、属人化していた受発注情報の共有化による内部不正防止や統制にも役立ちます。
NEWJI DX
製造業に特化したデジタルトランスフォーメーション(DX)の実現を目指す請負開発型のコンサルティングサービスです。AI、iPaaS、および先端の技術を駆使して、製造プロセスの効率化、業務効率化、チームワーク強化、コスト削減、品質向上を実現します。このサービスは、製造業の課題を深く理解し、それに対する最適なデジタルソリューションを提供することで、企業が持続的な成長とイノベーションを達成できるようサポートします。
製造業ニュース解説
製造業、主に購買・調達部門にお勤めの方々に向けた情報を配信しております。
新任の方やベテランの方、管理職を対象とした幅広いコンテンツをご用意しております。
お問い合わせ
コストダウンが利益に直結する術だと理解していても、なかなか前に進めることができない状況。そんな時は、newjiのコストダウン自動化機能で大きく利益貢献しよう!
(β版非公開)