- お役立ち記事
- Latest examples of production and evaluation technology for dry electrodes for lithium-ion batteries
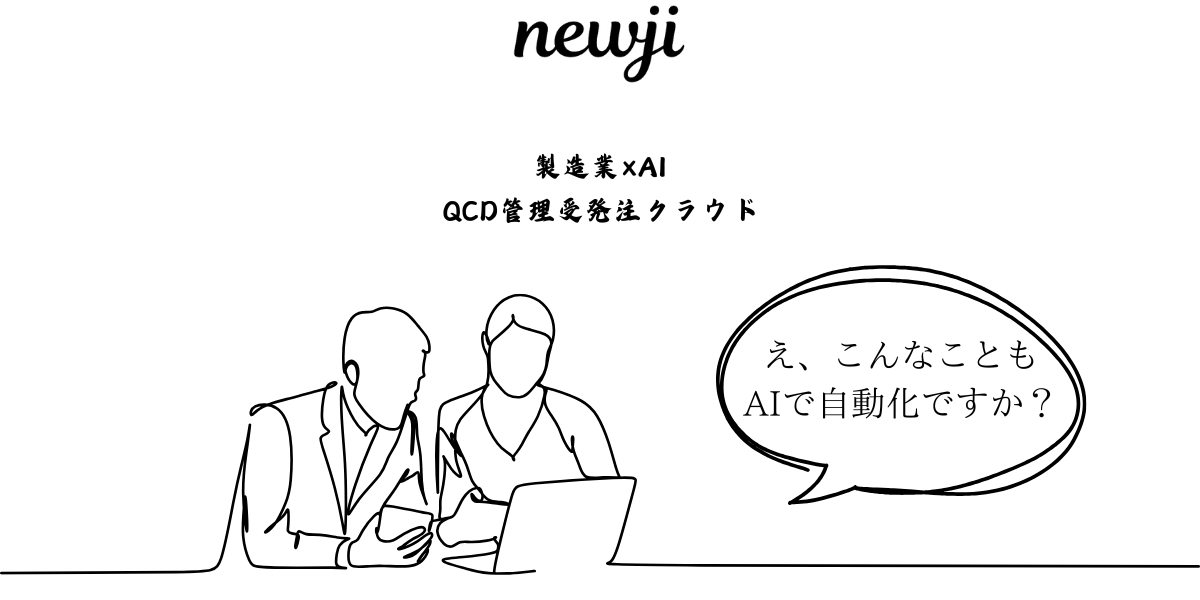
Latest examples of production and evaluation technology for dry electrodes for lithium-ion batteries
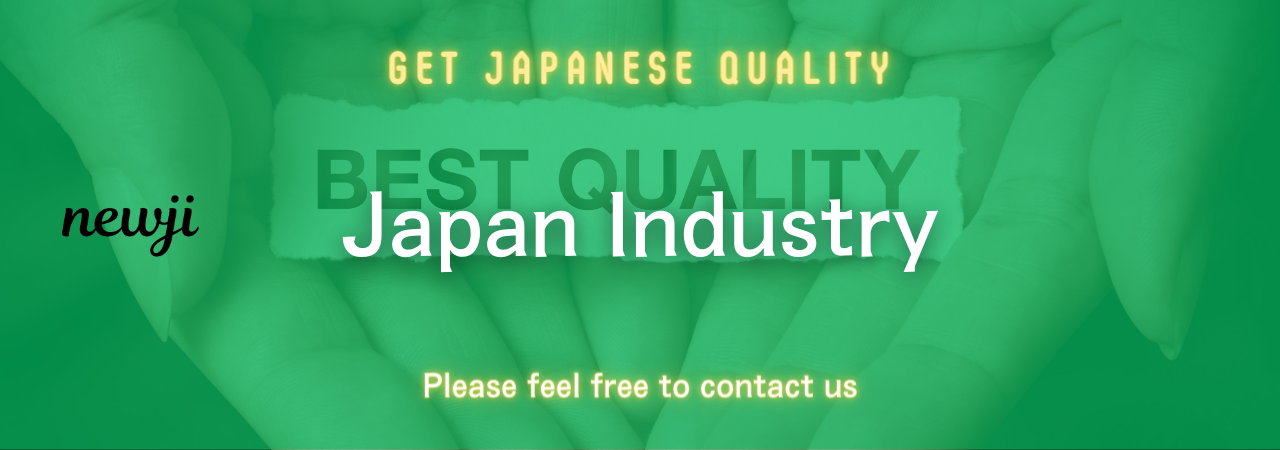
目次
Introduction to Dry Electrode Technology
Lithium-ion batteries have become a cornerstone in powering a wide range of electronic devices, electric vehicles, and renewable energy systems.
Typically, the production of these batteries involves wet electrode technology, which uses liquid solvents.
However, in recent times, dry electrode technology has gained considerable attention as a promising alternative.
The drive for innovation in this field arises from the need to enhance battery performance, increase production efficiency, and reduce environmental impacts.
Below, we dive into the latest developments and assessment techniques surrounding dry electrodes for lithium-ion batteries.
Advantages of Dry Electrode Technology
Compared to traditional wet electrodes, dry electrode technology offers several advantages.
Firstly, it removes the necessity for the use and handling of liquid solvents during the manufacturing process, significantly reducing environmental and health hazards.
Moreover, this technology can enhance energy density and increase the charge-discharge cycles of batteries.
This translates into longer battery life and better performance, which is increasingly important in today’s challenging energy demands.
Dry electrode technology also supports a more streamlined manufacturing process, potentially leading to cost reductions and increased production efficiency.
Without the need to dry solvents, the energy and time required for production are greatly minimized.
Environmental Impact
One of the biggest drivers for the development of dry electrode technologies is the environmental impact.
The elimination of toxic solvents reduces waste production and greenhouse gas emissions.
This contributes positively to the urgent need for more sustainable industrial practices.
As industries strive to minimize carbon footprints, adopting technologies that support greener manufacturing becomes crucial.
Dry electrodes promise to pave the way toward a more eco-friendly approach to battery production.
Production Techniques for Dry Electrodes
Producing high-quality dry electrodes requires sophisticated methods to ensure reliable performance and durability.
Various techniques are being explored and optimized to refine the characteristics of dry electrodes.
Compression and Sintering
One predominant approach is the use of mechanical compression methods combined with sintering.
This involves compressing the component particles to form a dense and uniform electrode structure.
Sintering further aids in improving the connectivity and adhesion between different particles, ensuring enhanced electrical conductivity.
Layer-by-Layer Assembly
Another promising method is the layer-by-layer assembly, which allows precision in crafting electrodes with specific qualities.
By stacking thin layers of active material and binders, manufacturers can tailor the electrodes for diverse applications.
This method offers flexibility in terms of controlling thickness and porosity, which are critical factors for battery efficiency.
Evaluation Techniques for Dry Electrodes
Assessing the quality and performance of dry electrodes is as crucial as their production.
Effective evaluation techniques help identify potential improvements and ensure that the electrodes meet necessary performance standards.
Electrochemical Testing
Electrochemical testing remains one of the most effective ways to evaluate dry electrodes.
These tests involve measuring various parameters such as charge capacity, discharge efficiency, and cyclability.
Advanced electrochemical impedance spectroscopy can also provide insights into the internal resistance and ionic conductivity of the electrodes, helping identify areas for enhancement.
Microscopic and Spectroscopic Analysis
Utilizing microscopic and spectroscopic tools can offer a deeper understanding of the microstructure and chemical composition of dry electrodes.
Scanning electron microscopy (SEM) helps visualize the surface morphology and particle distribution.
Meanwhile, techniques like X-ray diffraction (XRD) and Raman spectroscopy reveal structural details and detect potential impurities in the electrode material.
Recent Innovations and Future Prospects
The field of dry electrode technology is rapidly evolving, with researchers and companies pushing the boundaries to achieve better results.
From developing novel materials to refining production processes, the innovations in this area are set to revolutionize battery technology.
Nanostructured Materials
Recent research has focused significantly on the utilization of nanostructured materials.
These materials offer superior surface area, enhancing the efficiency of electrochemical reactions.
By incorporating nanoparticles into dry electrodes, it is possible to achieve greater capacity and improved thermal stability.
3D Printing Techniques
Advancements in 3D printing are also making their mark on dry electrode production.
Employing 3D printing techniques provides precision in shaping the electrode structure, allowing custom designs tailored for specific applications.
This opens the door for the production of complex architectures that were previously unachievable through conventional methods.
Outlook and Challenges
While dry electrode technology holds great promise, challenges remain in scaling up production without compromising quality.
Balancing cost, efficiency, and sustainability is crucial for widespread adoption.
Continuous research and development will likely yield solutions to these challenges, paving the way for the next generation of lithium-ion batteries.
With ongoing efforts and innovation, dry electrodes are set to play a pivotal role in addressing the energy needs of the future, promoting a greener and more efficient battery landscape.
資料ダウンロード
QCD調達購買管理クラウド「newji」は、調達購買部門で必要なQCD管理全てを備えた、現場特化型兼クラウド型の今世紀最高の購買管理システムとなります。
ユーザー登録
調達購買業務の効率化だけでなく、システムを導入することで、コスト削減や製品・資材のステータス可視化のほか、属人化していた購買情報の共有化による内部不正防止や統制にも役立ちます。
NEWJI DX
製造業に特化したデジタルトランスフォーメーション(DX)の実現を目指す請負開発型のコンサルティングサービスです。AI、iPaaS、および先端の技術を駆使して、製造プロセスの効率化、業務効率化、チームワーク強化、コスト削減、品質向上を実現します。このサービスは、製造業の課題を深く理解し、それに対する最適なデジタルソリューションを提供することで、企業が持続的な成長とイノベーションを達成できるようサポートします。
オンライン講座
製造業、主に購買・調達部門にお勤めの方々に向けた情報を配信しております。
新任の方やベテランの方、管理職を対象とした幅広いコンテンツをご用意しております。
お問い合わせ
コストダウンが利益に直結する術だと理解していても、なかなか前に進めることができない状況。そんな時は、newjiのコストダウン自動化機能で大きく利益貢献しよう!
(Β版非公開)