- お役立ち記事
- Latest information on safety testing and international regulations for printing inks for food packaging
月間76,176名の
製造業ご担当者様が閲覧しています*
*2025年3月31日現在のGoogle Analyticsのデータより
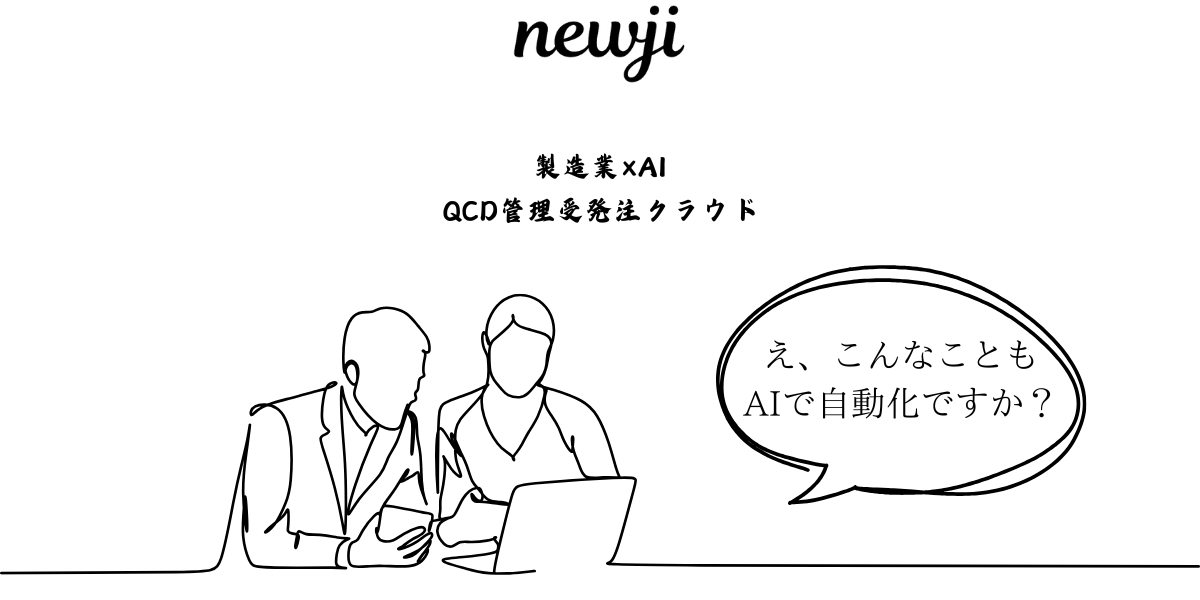
Latest information on safety testing and international regulations for printing inks for food packaging
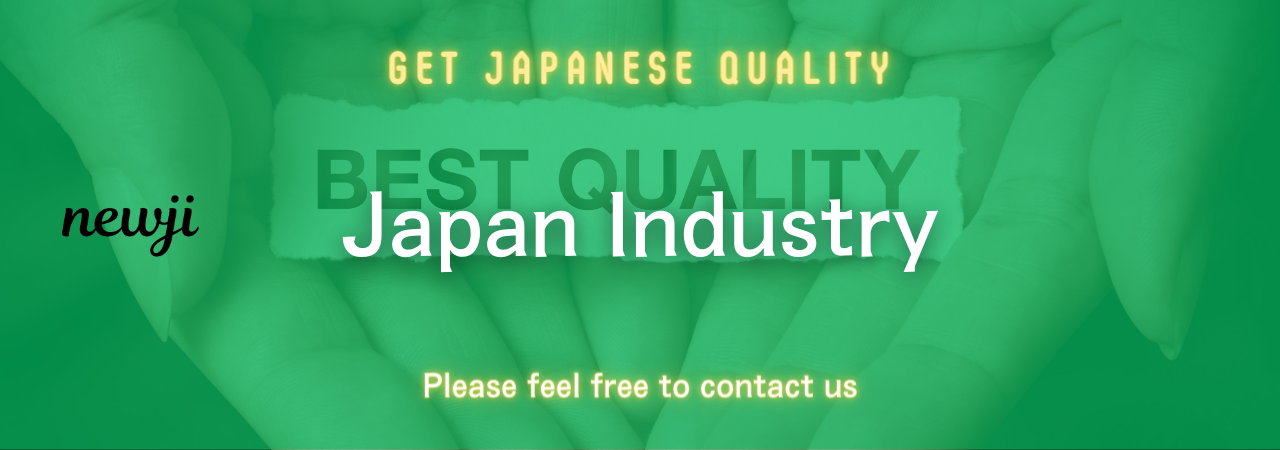
目次
Introduction to Food Packaging Safety
Food packaging plays a crucial role in preserving the quality and safety of food products.
It acts as a barrier against contamination and prolongs shelf life.
However, it’s not just the packaging material that is important, but also the inks used for printing on these packages.
Printing inks are an essential part of food packaging, providing necessary information such as branding, nutritional details, and instructions.
Ensuring these inks are safe for use with food products involves a meticulous process of safety testing and complying with international regulations.
The Importance of Printing Ink Safety
Inks used on food packaging need to be safe because they can come into contact with food items, either directly or indirectly.
Harmful substances from inks can migrate into food, posing health risks to consumers.
Thus, it’s imperative that these inks do not contain hazardous chemicals and are tested for safety.
Migratory Chemicals in Printing Inks
One of the major concerns with printing inks is the migration of chemicals into food.
This can occur when inks transfer from the packaging to the food they contain.
The risk arises when migration leads to a change in the chemical composition of the food, potentially making it unsafe for consumption.
Therefore, rigorous testing is necessary to assess the potential for migration and ensure any substances involved are within safe limits.
Testing for Ink Safety
To guarantee the safety of printing inks, they must go through extensive testing processes.
These tests are designed to ensure that chemicals do not migrate into food in harmful quantities.
Types of Tests Conducted
Several tests are conducted to check the safety of printing inks.
These include chemical analysis to monitor the presence and levels of specific substances.
Some common substances tested for include heavy metals, solvents, and photo-initiators used in UV inks.
Migration tests simulate different conditions (such as temperature and pH levels) to predict how inks behave when in contact with food over time.
Simulants in Testing
Migration tests use food simulants, which mimic the chemical properties of different food types.
Simulants are used to recreate scenarios under which inks might migrate into food products.
These include oils for fatty foods or ethanol for alcoholic beverages.
This process helps in understanding how inks will perform under various real-world conditions.
International Regulations Governing Printing Inks
Various international bodies have established regulations to ensure the safety of printing inks, providing a framework for manufacturers to follow.
The Role of the European Union
The European Union has been at the forefront of setting standards for food contact materials, including printing inks.
Regulation (EC) No 1935/2004 serves as the central legislation, ensuring materials do not endanger human health or alter the composition of food.
Specific regulations, such as Regulation (EU) No 10/2011, address plastic materials and articles intended to come into contact with food, which often includes food packaging.
For inks, the Swiss Ordinance plays a significant role by listing permitted substances for ink formulations.
US Food and Drug Administration (FDA) Guidelines
In the United States, the FDA lays out guidelines for materials that are safe for food contact.
Each component of packaging, inks included, must comply with the Federal Food, Drug, and Cosmetic Act.
The FDA evaluates the compositions of inks, ensuring they adhere to safe usage guidelines.
Compliance with Global Harmonization Systems
Efforts are underway globally to harmonize regulations concerning printing inks.
This helps in setting a uniform safety standard, making compliance easier for international manufacturers.
The Global Food Safety Initiative (GFSI) supports this, promoting consistent standards across countries.
Challenges and Advancements in Ink Technology
While regulations and testing are crucial, manufacturers are also focusing on improving ink formulation to minimize risks.
Developments in Barrier Properties
One advancement is in improving the barrier properties of packaging, which in turn affects ink safety.
Better barriers mean reduced migration of substances from inks into food.
Innovation in Ink Composition
Additionally, there is ongoing research into developing safer ink compositions.
The use of bio-based inks and those cured with LED-UV rather than traditional UV is an example.
This approach reduces the number of hazardous chemicals, thus decreasing potential health risks.
Conclusion
Printing ink safety is paramount in maintaining the overall safety of food packaging.
Complying with international regulations and undergoing extensive safety testing are non-negotiable steps in this process.
As the food packaging industry evolves, it’s vital to stay informed about the latest technologies and regulatory updates.
This ensures not just compliance but also the well-being of consumers relying on safe and quality food packaging.
資料ダウンロード
QCD管理受発注クラウド「newji」は、受発注部門で必要なQCD管理全てを備えた、現場特化型兼クラウド型の今世紀最高の受発注管理システムとなります。
ユーザー登録
受発注業務の効率化だけでなく、システムを導入することで、コスト削減や製品・資材のステータス可視化のほか、属人化していた受発注情報の共有化による内部不正防止や統制にも役立ちます。
NEWJI DX
製造業に特化したデジタルトランスフォーメーション(DX)の実現を目指す請負開発型のコンサルティングサービスです。AI、iPaaS、および先端の技術を駆使して、製造プロセスの効率化、業務効率化、チームワーク強化、コスト削減、品質向上を実現します。このサービスは、製造業の課題を深く理解し、それに対する最適なデジタルソリューションを提供することで、企業が持続的な成長とイノベーションを達成できるようサポートします。
製造業ニュース解説
製造業、主に購買・調達部門にお勤めの方々に向けた情報を配信しております。
新任の方やベテランの方、管理職を対象とした幅広いコンテンツをご用意しております。
お問い合わせ
コストダウンが利益に直結する術だと理解していても、なかなか前に進めることができない状況。そんな時は、newjiのコストダウン自動化機能で大きく利益貢献しよう!
(β版非公開)