- お役立ち記事
- Latest Innovations in Manufacturing for Pursuing Energy Efficiency and Implementation Examples
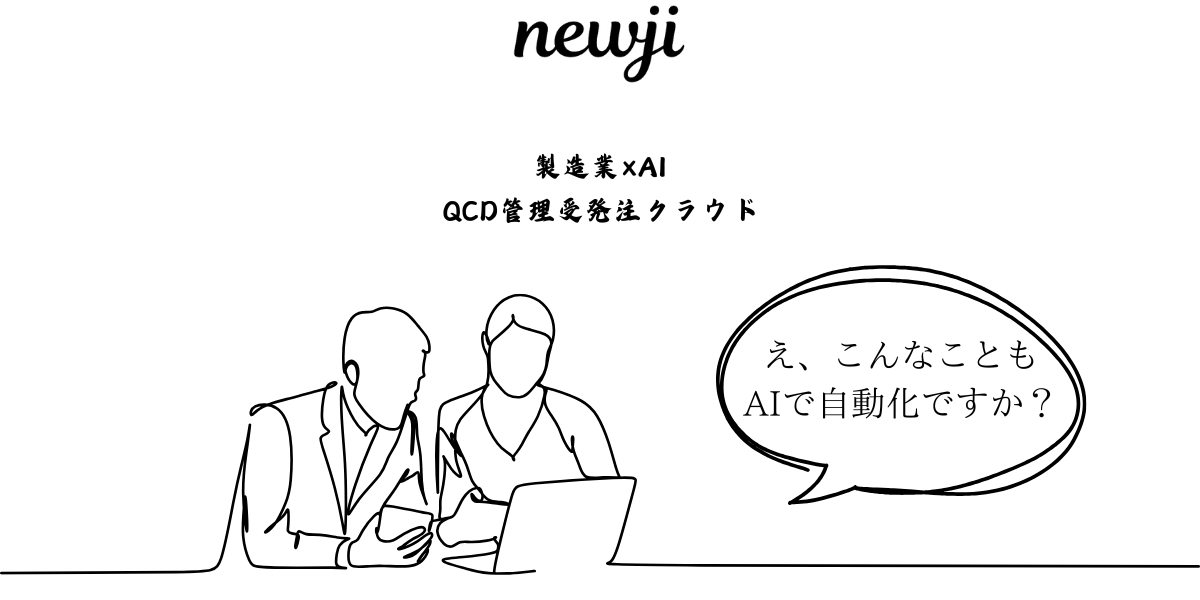
Latest Innovations in Manufacturing for Pursuing Energy Efficiency and Implementation Examples
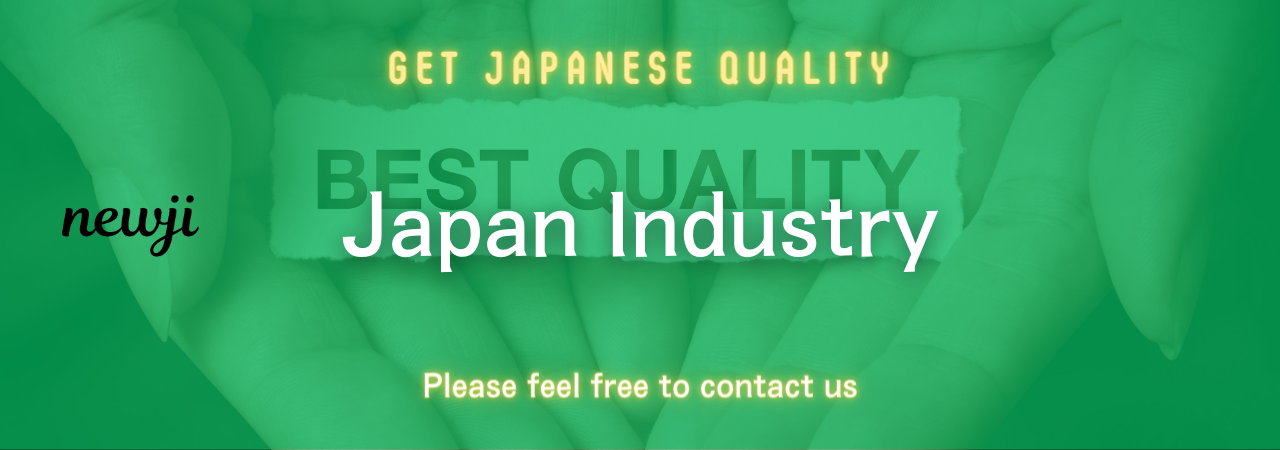
The manufacturing industry is constantly evolving, driven by the need to improve efficiency and reduce energy consumption.
Recent innovations are paving the way for a more sustainable future, ensuring not only cost reductions but also a smaller environmental footprint.
Let’s dive into some of the latest advancements and look at a few real-world examples of how these technologies are being put into practice.
目次
Advanced Sensors and IoT Integration
One of the most significant breakthroughs in manufacturing is the integration of advanced sensors and the Internet of Things (IoT).
Sensors are now more intelligent, capable of monitoring everything from temperature and humidity to machinery performance in real time.
When these sensors are connected to an IoT network, they provide valuable data that can be analyzed to optimize production processes.
Predictive Maintenance
Predictive maintenance is a game-changer for the manufacturing industry.
By utilizing data gathered from sensors, manufacturers can predict when a machine is likely to fail.
This allows for timely maintenance, preventing costly downtime and reducing the energy wasted on inefficient machinery.
Energy Management Systems
Energy management systems can also benefit from IoT integration.
These systems monitor energy consumption throughout the manufacturing process and identify areas where energy use can be minimized.
By reducing unnecessary energy consumption, manufacturers can lower their operational costs and their carbon footprint.
Automation and Robotics
Automation and robotics are no longer just futuristic concepts; they are integral parts of modern manufacturing.
These technologies contribute to energy efficiency by increasing precision and reducing the need for manual labor, which often leads to errors and wasted materials.
Smart Factories
The concept of smart factories is a testament to the power of automation and robotics.
In smart factories, interconnected machines communicate with each other and make autonomous decisions to enhance efficiency.
This results in streamlined production processes, fewer errors, and significant energy savings.
Collaborative Robots
Collaborative robots, or cobots, are designed to work alongside human workers.
These robots are equipped with sensors and AI algorithms that enable them to perform tasks with high precision.
By taking on repetitive or dangerous tasks, cobots improve worker safety and productivity, leading to overall energy savings.
Renewable Energy Integration
With the increasing focus on sustainability, many manufacturers are turning to renewable energy sources to power their operations.
Integrating renewable energy into the manufacturing process is a significant step toward reducing the industry’s reliance on fossil fuels.
Solar Power
Solar power is one of the most accessible and widely adopted renewable energy sources.
Manufacturers are installing solar panels on factory roofs and using the generated electricity to power their operations.
This not only reduces their energy bills but also contributes to a greener environment.
Wind Energy
Wind energy is another viable option for manufacturers looking to reduce their carbon footprint.
By installing wind turbines on-site or sourcing wind energy from nearby farms, manufacturers can tap into this renewable resource to meet their energy needs sustainably.
Energy-Efficient Equipment
Investing in energy-efficient equipment is a straightforward yet highly effective strategy for achieving energy efficiency in manufacturing.
Modern machinery is designed to consume less energy while delivering the same or better performance levels.
Variable Frequency Drives
Variable frequency drives (VFDs) are essential in controlling the speed of electric motors used in various industrial applications.
By adjusting the motor speed to match the required output, VFDs help reduce energy consumption and extend the lifespan of the equipment.
High-Efficiency Motors
High-efficiency motors are engineered to convert more electrical energy into mechanical energy, resulting in lower energy losses.
These motors are increasingly being adopted in manufacturing to ensure optimal performance and energy savings.
Case Studies of Energy-Efficient Manufacturing
To understand how these innovations are making a difference, let’s look at some real-world examples of energy-efficient manufacturing.
Siemens Smart Factory
Siemens has revolutionized its manufacturing process with the concept of a smart factory.
By integrating advanced sensors, IoT, and automation, Siemens has achieved significant improvements in energy efficiency.
Their Amberg plant in Germany serves as a prime example, where automated systems ensure minimal energy waste and optimal production efficiency.
Tesla Gigafactory
Tesla’s Gigafactory is a beacon of renewable energy use in manufacturing.
The facility in Nevada is powered by a combination of solar and wind energy, significantly reducing its reliance on non-renewable energy sources.
By integrating energy-efficient equipment and automated systems, the Gigafactory sets a benchmark for sustainable manufacturing practices.
General Electric’s Ecomagination
General Electric’s Ecomagination program aims to develop and deploy technologies that improve energy efficiency across various industries.
In their manufacturing facilities, GE has implemented numerous energy-saving measures, such as high-efficiency motors, advanced sensors, and renewable energy integration.
As a result, GE has achieved substantial cost savings and reduced its environmental impact.
The quest for energy efficiency in manufacturing is ongoing, and the latest innovations are making a profound difference.
Advanced sensors and IoT integration, automation and robotics, renewable energy, and energy-efficient equipment are the cornerstones of this transformation.
By adopting these technologies, manufacturers can not only improve their bottom line but also contribute to a more sustainable future.
The case studies from Siemens, Tesla, and General Electric serve as inspiration, proving that significant strides in energy efficiency are attainable with the right strategies and investments.
資料ダウンロード
QCD調達購買管理クラウド「newji」は、調達購買部門で必要なQCD管理全てを備えた、現場特化型兼クラウド型の今世紀最高の購買管理システムとなります。
ユーザー登録
調達購買業務の効率化だけでなく、システムを導入することで、コスト削減や製品・資材のステータス可視化のほか、属人化していた購買情報の共有化による内部不正防止や統制にも役立ちます。
NEWJI DX
製造業に特化したデジタルトランスフォーメーション(DX)の実現を目指す請負開発型のコンサルティングサービスです。AI、iPaaS、および先端の技術を駆使して、製造プロセスの効率化、業務効率化、チームワーク強化、コスト削減、品質向上を実現します。このサービスは、製造業の課題を深く理解し、それに対する最適なデジタルソリューションを提供することで、企業が持続的な成長とイノベーションを達成できるようサポートします。
オンライン講座
製造業、主に購買・調達部門にお勤めの方々に向けた情報を配信しております。
新任の方やベテランの方、管理職を対象とした幅広いコンテンツをご用意しております。
お問い合わせ
コストダウンが利益に直結する術だと理解していても、なかなか前に進めることができない状況。そんな時は、newjiのコストダウン自動化機能で大きく利益貢献しよう!
(Β版非公開)