- お役立ち記事
- Latest solution for thick plate parts welding equipment design
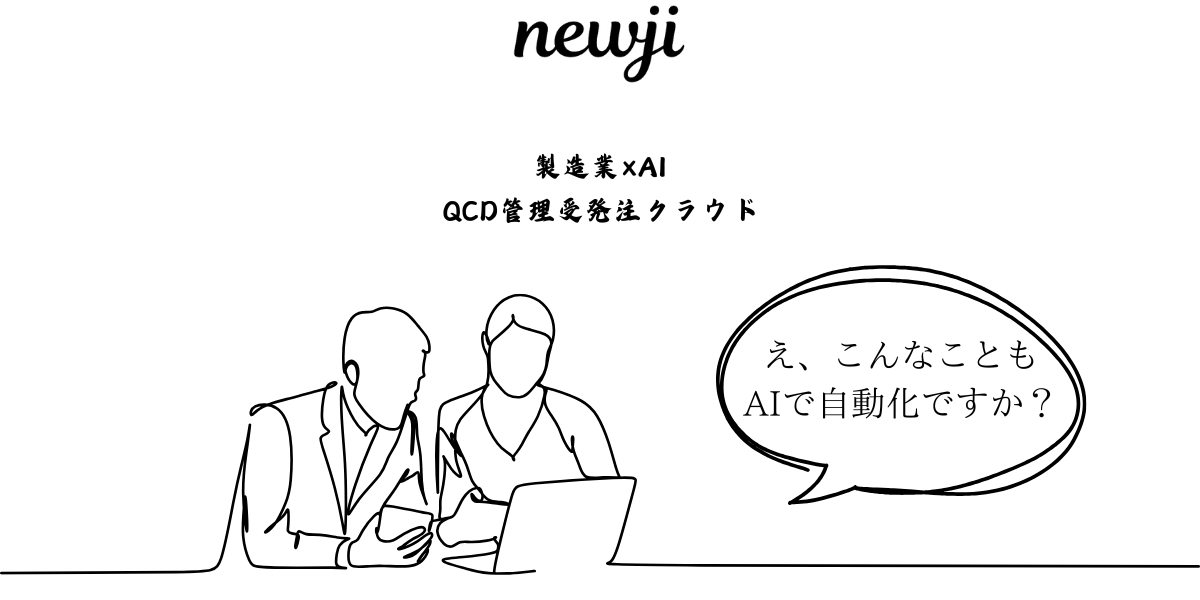
Latest solution for thick plate parts welding equipment design
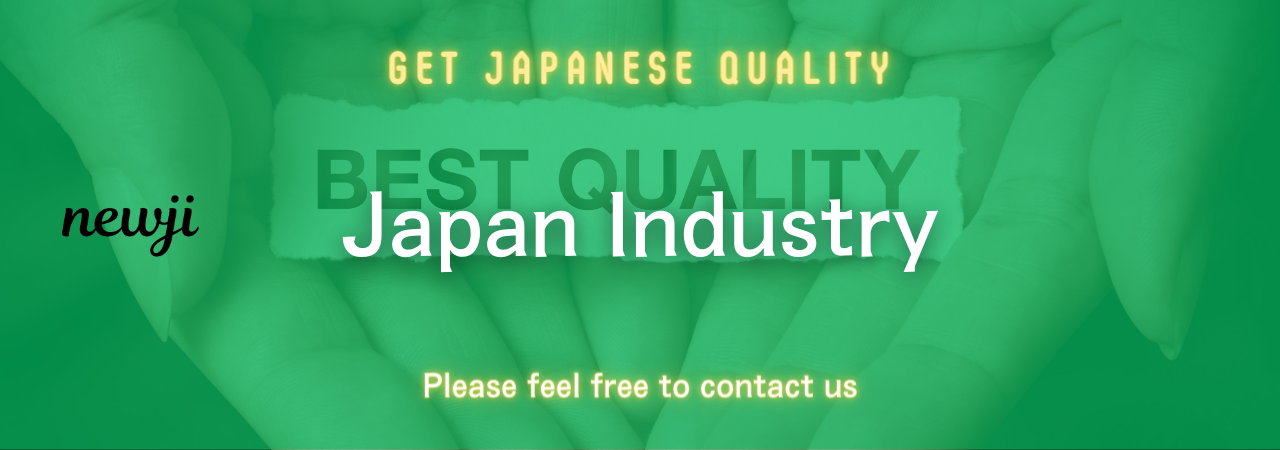
目次
Introduction to Thick Plate Welding
Welding is a critical industrial process used to join materials, usually metals or thermoplastics, creating strong bonds.
When it comes to thick plate welding, the complexity and challenges increase significantly compared to thin plates.
Thick plate welding is essential in industries such as shipbuilding, construction, and heavy machinery.
Designing equipment for this process requires careful consideration of several factors to achieve quality welds and ensure safety.
In this article, we will explore the latest solutions for thick plate parts welding equipment design.
We will discuss the techniques, tools, and innovations that have emerged to tackle the challenges associated with welding thick plates.
Challenges in Welding Thick Plates
Welding thick plates presents unique challenges that are not as prevalent in thin plate welding.
Firstly, the heat input required for thick plates is much greater, which can lead to issues such as warping or distortion if not handled correctly.
Moreover, the cooling time is extended, increasing the chances of weld defects like cracks or incomplete fusion.
Another challenge is the need for multi-pass welding, which involves applying multiple layers of weld to achieve full penetration.
This adds time to the welding process and requires precision to ensure consistent quality across layers.
Furthermore, accessibility to the weld joint can be problematic due to the size and position of thick plates, necessitating specialized welding equipment that can reach these areas effectively.
Innovations in Thick Plate Welding Equipment
Innovation has played a significant role in advancing the design of welding equipment for thick plates.
One of the most notable developments is the automation of welding processes.
Robotic welding systems can be programmed to perform complex welds with high precision and consistency.
These systems help reduce human error and increase efficiency, particularly in large-scale production environments.
Additionally, advanced welding torches have been designed to handle the greater demands of thick plate welding.
These torches often incorporate features like enhanced cooling systems to manage the increased heat and high duty cycles.
Welding torches have also evolved with adjustable settings to optimize the welding parameters for various thicknesses and materials.
The Role of Welding Machines in Thick Plate Solutions
Welding machines have had to adapt to accommodate the specific needs of thick plate welding.
High-capacity power sources are essential for providing the necessary heat and current levels for deep penetration welds.
Modern welding machines are equipped with features such as digital controls and programmable settings that allow for precise adjustment of welding parameters.
Furthermore, pulse welding technology has become a staple in thick plate welding equipment.
Pulsed welding provides better control over the heat input, reducing the risk of overheating and minimizing distortion.
It also enhances arc stability, resulting in improved weld quality and appearance.
Importance of Welding Consumables
In addition to machinery, the selection of welding consumables is crucial in thick plate welding.
Consumables such as welding wires, electrodes, and fluxes must be chosen based on the specific material and thickness being welded.
High-quality consumables contribute to better arc performance and can help reduce defects like porosity and inclusions.
For thick plate applications, flux-cored wires are often preferred due to their efficiency in depositing metal and ability to handle higher amperages.
Similarly, low-hydrogen electrodes are recommended to prevent cracking in thick steel welds.
These consumables help ensure the integrity and durability of the final weld, which is vital in structural applications.
Best Practices for Designing Thick Plate Welding Equipment
Designing equipment for welding thick plates involves several best practices to ensure optimal performance.
Customized Jigs and Fixturing
Customized jigs and fixtures are essential to correctly position and stabilize thick plates during welding.
They prevent movement and distortion, maintaining the quality and alignment of the weld joint.
Preheating and Post-Weld Heat Treatment
Preheating thick plates before welding can help reduce thermal shock and prevent cracking.
Similarly, post-weld heat treatment normalizes the welded joints, reducing residual stress and ensuring maximum strength.
Regular Equipment Maintenance
Thick plate welding equipment must be regularly maintained to ensure reliability and accuracy.
This includes checking cables, connectors, and all moving parts for wear and tear.
Conclusion
The latest solutions in thick plate parts welding equipment design focus on overcoming the inherent challenges of the process.
Through advancements in automation, machine capabilities, consumables, and best practices, the industry is better equipped to handle the demands of thick plate welding.
Implementing these solutions can lead to greater efficiencies, reduced production times, and enhanced quality in welded structures.
By staying up-to-date with these innovations, manufacturers can ensure they are delivering safe and durable products, meeting the high standards required in fields where thick plate welding is critical.
資料ダウンロード
QCD調達購買管理クラウド「newji」は、調達購買部門で必要なQCD管理全てを備えた、現場特化型兼クラウド型の今世紀最高の購買管理システムとなります。
ユーザー登録
調達購買業務の効率化だけでなく、システムを導入することで、コスト削減や製品・資材のステータス可視化のほか、属人化していた購買情報の共有化による内部不正防止や統制にも役立ちます。
NEWJI DX
製造業に特化したデジタルトランスフォーメーション(DX)の実現を目指す請負開発型のコンサルティングサービスです。AI、iPaaS、および先端の技術を駆使して、製造プロセスの効率化、業務効率化、チームワーク強化、コスト削減、品質向上を実現します。このサービスは、製造業の課題を深く理解し、それに対する最適なデジタルソリューションを提供することで、企業が持続的な成長とイノベーションを達成できるようサポートします。
オンライン講座
製造業、主に購買・調達部門にお勤めの方々に向けた情報を配信しております。
新任の方やベテランの方、管理職を対象とした幅広いコンテンツをご用意しております。
お問い合わせ
コストダウンが利益に直結する術だと理解していても、なかなか前に進めることができない状況。そんな時は、newjiのコストダウン自動化機能で大きく利益貢献しよう!
(Β版非公開)