- お役立ち記事
- Latest Techniques and Strategies for Growth in Precision Cutting
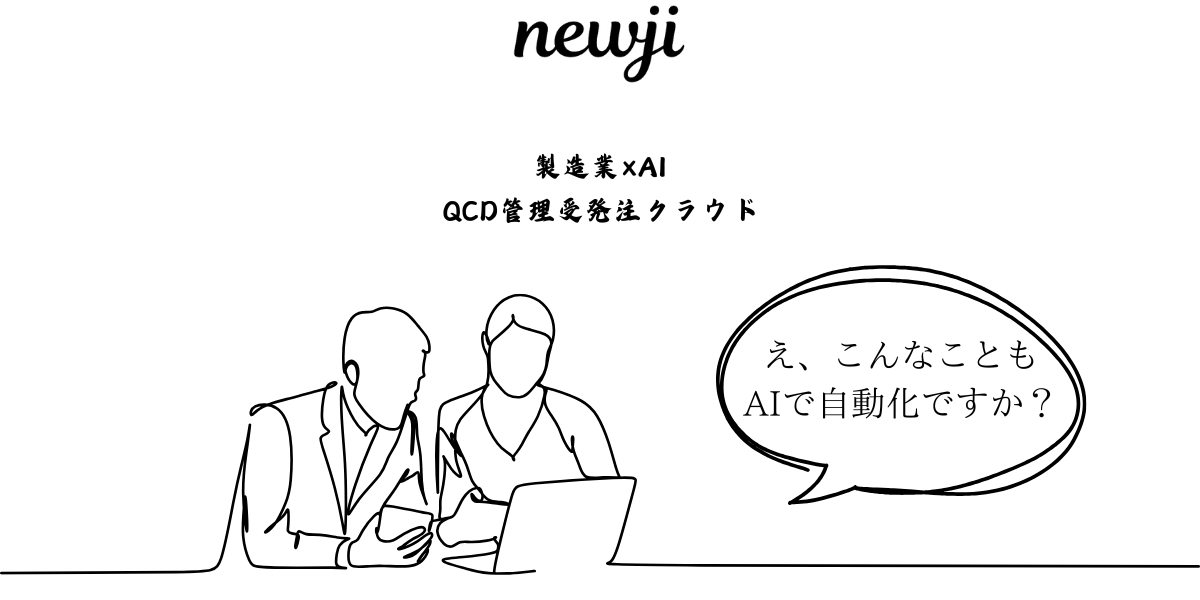
Latest Techniques and Strategies for Growth in Precision Cutting
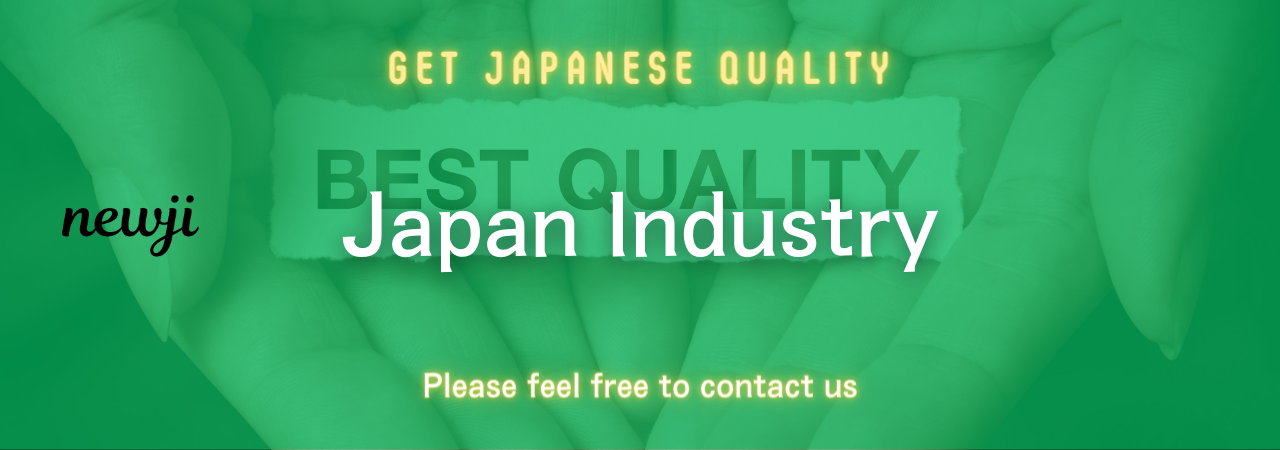
目次
Understanding Precision Cutting
Precision cutting is an advanced manufacturing process that involves the detailed and accurate cutting of materials to specified dimensions and shapes.
Industries like aerospace, automotive, medical, and electronics heavily rely on precision cutting for producing parts that meet strict quality standards.
By employing the latest techniques and strategies, manufacturers can achieve superior results, enhancing both productivity and product quality.
Latest Techniques in Precision Cutting
Laser Cutting
Laser cutting is one of the most popular precision cutting methods.
It uses a high-powered laser beam to cut materials with extreme accuracy.
Today’s laser cutting machines offer improved cutting speeds, higher power, and enhanced precision.
With the integration of computer numerical control (CNC) systems, these machines deliver consistent and repeatable results, allowing for complex geometries and intricate designs.
Laser cutting is suitable for metals, plastics, glass, and even some composites.
Water Jet Cutting
Water jet cutting employs a high-pressure stream of water, often mixed with abrasive materials, to cut through various substrates.
This technique is highly versatile and can handle materials that are difficult to cut using other methods, such as ceramics, stone, and thick metals.
The primary advantage of water jet cutting is that it produces no heat-affected zones, minimizing thermal distortion and material degradation.
It’s also environmentally friendly, using water as the cutting medium.
Electrical Discharge Machining (EDM)
EDM is a highly specialized precision cutting technology used primarily for hard metals and conductive materials.
It works by creating electrical sparks between an electrode and the workpiece, eroding material precisely where the spark hits.
EDM is ideal for complex shapes, detailed contours, and high-tolerance applications.
It’s commonly used in the production of molds, dies, and intricate parts for the aerospace and medical industries.
Strategies for Growth in Precision Cutting
Investing in Advanced Machinery
To stay competitive, manufacturers must invest in the latest cutting technologies.
Modern machinery offers improved performance, higher efficiency, and better precision.
Investing in advanced equipment not only enhances production capabilities but also reduces downtime and maintenance costs.
It’s crucial to evaluate the specific needs and requirements of the business before investing in new technology.
Embracing Automation
Automation is transforming the manufacturing landscape, and precision cutting is no exception.
By integrating automated systems, manufacturers can streamline operations, reduce labor costs, and increase output.
Robotic arms, CNC machines, and automated cutting systems can work around the clock, ensuring consistent quality and productivity.
Moreover, automation reduces the risk of human error, resulting in fewer defects and higher overall quality.
Training and Skill Development
As precision cutting technologies evolve, so must the skills of the workforce.
Regular training and skill development programs are essential to keep employees updated with the latest techniques and best practices.
Skilled operators can maximize the capabilities of advanced machinery, ensuring optimal performance and quality outcomes.
Investing in employee development also fosters a culture of continuous improvement and innovation.
Quality Control and Maintenance
Maintaining high standards of quality control is vital in precision cutting.
Implementing rigorous inspection and testing processes ensures that each part meets the required specifications.
Modern technologies like laser scanning and coordinate measuring machines (CMM) can be used to verify accuracy and precision.
Additionally, regular maintenance of machinery is crucial to prevent breakdowns and ensure consistent performance.
Routine inspections, timely repairs, and part replacements can significantly extend the life of cutting equipment.
Collaborative Partnerships
Building strong partnerships with suppliers, clients, and other stakeholders can drive growth and innovation.
Collaborative efforts can lead to the development of new techniques, materials, and applications in precision cutting.
Manufacturers can benefit from shared knowledge, resources, and expertise, resulting in improved processes and products.
Engaging with industry associations and participating in trade shows and conferences can also provide valuable networking and learning opportunities.
The Role of Technology in Precision Cutting
Software Integration
Software plays a critical role in enhancing precision cutting processes.
Advanced CAD/CAM software allows for detailed design, simulation, and optimization of cutting paths.
This ensures that each cut is executed with the highest accuracy and efficiency.
Furthermore, software integration with machines enables real-time monitoring and control, allowing for quick adjustments and error corrections.
IoT and Industry 4.0
The Internet of Things (IoT) and Industry 4.0 are revolutionizing manufacturing, including precision cutting.
Connected devices and sensors collect data on machine performance, material usage, and environmental conditions.
This data is analyzed to identify patterns and insights that can improve operations.
Predictive maintenance, for example, uses data to foresee potential machine failures and schedule maintenance proactively.
Such technologies lead to greater efficiency, reduced downtime, and improved overall productivity.
Conclusion
In the ever-evolving field of precision cutting, staying ahead requires the adoption of the latest techniques and strategies.
By investing in advanced machinery, embracing automation, and prioritizing skill development and quality control, manufacturers can achieve significant growth.
Collaborative partnerships and leveraging technology such as software integration and IoT further bolster competitive advantage.
Ultimately, precision cutting is not just about making the perfect cut; it’s about continuous improvement, innovation, and staying agile in a dynamic industry.
By embracing these methods, companies can ensure they remain at the forefront of precision manufacturing.
資料ダウンロード
QCD調達購買管理クラウド「newji」は、調達購買部門で必要なQCD管理全てを備えた、現場特化型兼クラウド型の今世紀最高の購買管理システムとなります。
ユーザー登録
調達購買業務の効率化だけでなく、システムを導入することで、コスト削減や製品・資材のステータス可視化のほか、属人化していた購買情報の共有化による内部不正防止や統制にも役立ちます。
NEWJI DX
製造業に特化したデジタルトランスフォーメーション(DX)の実現を目指す請負開発型のコンサルティングサービスです。AI、iPaaS、および先端の技術を駆使して、製造プロセスの効率化、業務効率化、チームワーク強化、コスト削減、品質向上を実現します。このサービスは、製造業の課題を深く理解し、それに対する最適なデジタルソリューションを提供することで、企業が持続的な成長とイノベーションを達成できるようサポートします。
オンライン講座
製造業、主に購買・調達部門にお勤めの方々に向けた情報を配信しております。
新任の方やベテランの方、管理職を対象とした幅広いコンテンツをご用意しております。
お問い合わせ
コストダウンが利益に直結する術だと理解していても、なかなか前に進めることができない状況。そんな時は、newjiのコストダウン自動化機能で大きく利益貢献しよう!
(Β版非公開)