- お役立ち記事
- Latest Technologies and Case Studies for Shortening Molding Cycle Times
Latest Technologies and Case Studies for Shortening Molding Cycle Times
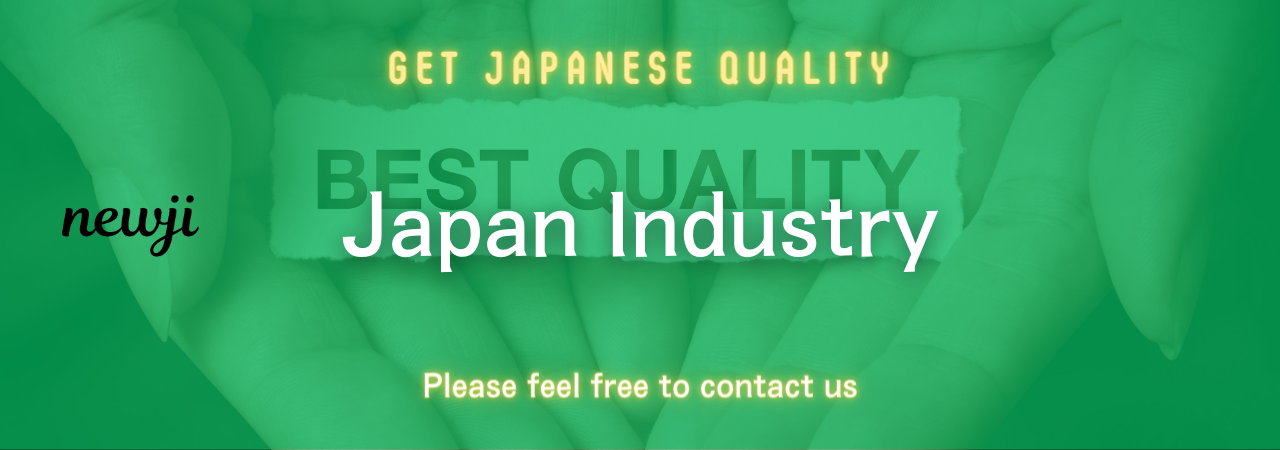
目次
Understanding Molding Cycle Times
Molding cycle time refers to the total time it takes to produce a single molded part, from the beginning of the molding process to the ejection of the finished product.
This encompasses various stages, including clamping, injection, cooling, and demolding.
The efficiency of the molding cycle impacts the overall productivity and cost-effectiveness of manufacturing processes.
Thus, finding ways to shorten these cycle times is essential for manufacturers aiming to increase output and reduce costs.
Innovative Technologies for Reducing Cycle Times
The continuous evolution of technology has brought forward numerous advancements that help in reducing molding cycle times.
High-Speed Machine Operations
The development of high-speed injection molding machines has revolutionized the manufacturing industry.
These machines operate at faster speeds and higher precision than traditional models, which significantly reduces the cycle time.
They also maintain consistent quality in the final product.
By leveraging enhanced control systems, manufacturers achieve faster throughput without compromising on part quality.
Optimized Cooling Systems
Cooling time often represents a significant portion of the overall cycle time.
Introducing innovative cooling technologies can drastically reduce this phase.
Conformal cooling, for example, is a technique that uses specially designed cooling channels to conform closely to the part geometry.
This allows for more efficient heat removal and shorter cooling times compared to conventional cooling systems.
Advancements in materials and design software have made conformal cooling more accessible and effective.
Advanced Material Usage
The selection of materials plays a vital role in determining the cycle time.
Using materials with suitable thermal properties can help shorten cooling periods.
For instance, high-thermal conductivity materials dissipate heat faster, reducing the time required for cooling.
Additionally, the development of engineered polymers and composites provides options that cure quickly without sacrificing mechanical properties.
Innovative Mold Designs
Modern mold designs incorporate various techniques that contribute to faster cycle times.
For example, the use of hot runner systems can reduce the cycle time by eliminating the need for solidified runners.
These systems keep the plastic in a molten state inside the runner, which not only reduces wastage but also allows for quicker injection cycles.
The integration of smart sensors and real-time monitoring in molds also optimizes the process by detecting issues instantly, thereby minimizing downtime.
Case Studies Demonstrating Success
Case Study 1: Automotive Industry
A leading automotive parts manufacturer implemented advanced high-speed injection molding machines coupled with conformal cooling technology.
By switching from traditional machines, they achieved a 30% reduction in production time for complex parts.
This change not only increased their output but also enhanced the quality of the components, reducing the need for post-production adjustments.
Case Study 2: Consumer Electronics
A major player in the consumer electronics market integrated hot runner systems in their injection molds.
Previously, they faced challenges with balancing cycle time and quality.
With the hot runner system, they reduced the cycle time by 20% and minimized material wastage.
This advancement allowed them to meet increasing market demands more efficiently.
Case Study 3: Medical Device Manufacturing
A company specializing in medical devices adopted new polymer materials with high thermal conductivity for molding components.
The materials allowed for quicker cooling and demolding, shortening the cycle time without compromising the sterility and precision required in medical products.
The efficiency gained enabled the company to produce a higher volume of parts, aligning with the stringent healthcare industry demands.
Future Prospects in Reducing Cycle Times
The future of molding technologies continues to hold promise for further reducing cycle times.
Artificial intelligence (AI) and machine learning offer possibilities for self-optimizing systems that can predict and adjust parameters in real-time to enhance efficiency.
As 3D printing and additive manufacturing technologies progress, they may integrate with traditional molding processes to further decrease cycle times through rapid prototyping and mold development.
In addition, the increased emphasis on sustainability is driving companies to explore eco-friendly materials and energy-efficient machinery.
These innovations will not only reduce cycle times but also align with global sustainability goals.
Manufacturers must stay abreast of these developments to remain competitive in their respective industries.
Conclusion
Reducing molding cycle times is a multifaceted challenge that requires a blend of cutting-edge technology, innovative design, and strategic material selection.
With the proven successes in various industries, companies can leverage these advancements to improve efficiency and meet increasing market demands.
As technology continues to evolve, the potential for further reduction in cycle times remains an exciting prospect for the manufacturing sector.
資料ダウンロード
QCD調達購買管理クラウド「newji」は、調達購買部門で必要なQCD管理全てを備えた、現場特化型兼クラウド型の今世紀最高の購買管理システムとなります。
ユーザー登録
調達購買業務の効率化だけでなく、システムを導入することで、コスト削減や製品・資材のステータス可視化のほか、属人化していた購買情報の共有化による内部不正防止や統制にも役立ちます。
NEWJI DX
製造業に特化したデジタルトランスフォーメーション(DX)の実現を目指す請負開発型のコンサルティングサービスです。AI、iPaaS、および先端の技術を駆使して、製造プロセスの効率化、業務効率化、チームワーク強化、コスト削減、品質向上を実現します。このサービスは、製造業の課題を深く理解し、それに対する最適なデジタルソリューションを提供することで、企業が持続的な成長とイノベーションを達成できるようサポートします。
オンライン講座
製造業、主に購買・調達部門にお勤めの方々に向けた情報を配信しております。
新任の方やベテランの方、管理職を対象とした幅広いコンテンツをご用意しております。
お問い合わせ
コストダウンが利益に直結する術だと理解していても、なかなか前に進めることができない状況。そんな時は、newjiのコストダウン自動化機能で大きく利益貢献しよう!
(Β版非公開)