- お役立ち記事
- Latest Technologies for Lightweight and Strength Enhancement in Manufacturing with CFRP
Latest Technologies for Lightweight and Strength Enhancement in Manufacturing with CFRP
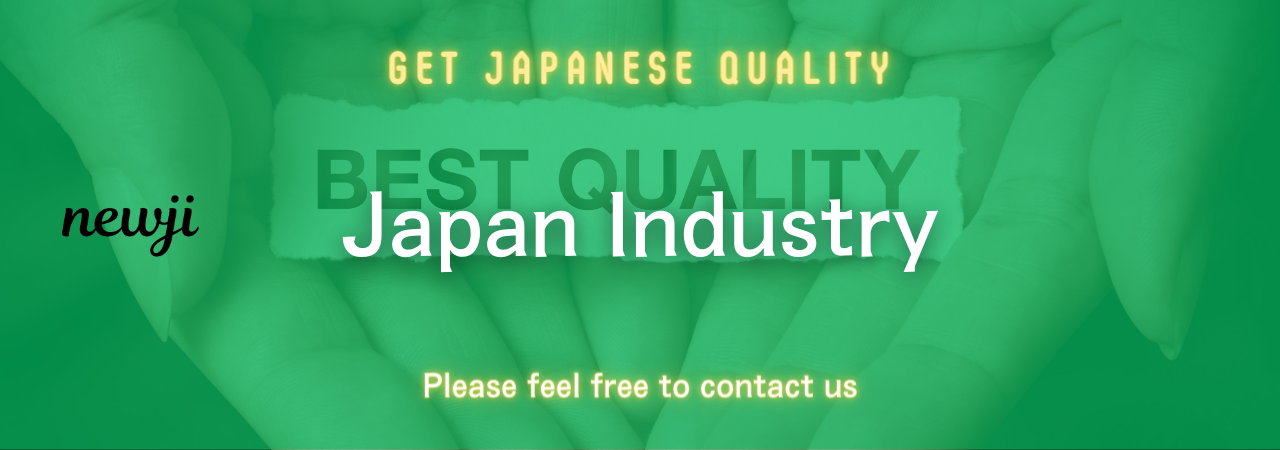
Carbon Fiber Reinforced Polymer (CFRP) is a material that combines carbon fibers with a polymer matrix, resulting in a composite that is both lightweight and extremely strong.
It has revolutionized various industries such as aerospace, automotive, and sports equipment, to name a few.
The push for ever-lighter and stronger materials has led to several exciting advancements in CFRP manufacturing technologies.
Let’s explore these cutting-edge innovations.
目次
Autoclave Processing
Autoclave processing has been a staple in the production of high-performance CFRP components for years.
This technology involves placing the material inside a specialized oven where heat and pressure are applied.
The controlled environment allows for the optimization of curing, enhancing the strength and consistency of the composite.
Recent advancements have made autoclave processing even more efficient by improving temperature uniformity and reducing cycle times.
Temperature Control
One of the key improvements in autoclave technology is the ability to maintain precise temperature control throughout the curing process.
New sensors and control systems have been developed to ensure that the entire material is subjected to uniform heating.
This minimizes residual stresses and enhances the mechanical properties of the final product.
Reduced Cycle Times
Traditionally, autoclave processing could be time-consuming, sometimes taking several hours for a single cycle.
Innovative heating elements and more efficient power usage have significantly reduced these cycle times.
This not only speeds up production but also lowers manufacturing costs, making high-quality CFRP more accessible.
Out-of-Autoclave (OOA) Techniques
While autoclave processing is highly effective, it is also expensive and requires large-scale infrastructure.
Out-of-Autoclave (OOA) techniques have emerged as cost-effective alternatives that still yield high-quality CFRP components.
Resin Transfer Molding (RTM)
Resin Transfer Molding (RTM) is an OOA method that involves injecting resin into a closed mold containing a pre-shaped fiber reinforcement.
The pressure from the injection ensures that the resin thoroughly impregnates the fibers, resulting in a strong and lightweight component.
RTM has the advantage of being scalable and versatile, making it suitable for both small and large production runs.
Vacuum-Assisted Resin Infusion (VARI)
Vacuum-Assisted Resin Infusion (VARI) is another OOA technique where the resin is drawn into the fiber preform under vacuum pressure.
This method is particularly useful for creating large, complex shapes without the need for high-pressure equipment.
Improvements in vacuum pump technology and resin formulations have made VARI more reliable and easier to control.
Automated Fiber Placement (AFP)
Automated Fiber Placement (AFP) is a cutting-edge manufacturing process that uses robotic systems to lay down carbon fibers in precise patterns.
This technology allows for greater design flexibility and can produce parts with intricate shapes and variations in thickness.
Increased Speed and Accuracy
Recent advancements in robotic systems have significantly increased the speed and accuracy of fiber placement.
High-performance actuators and improved software algorithms allow for more complex geometries to be manufactured quickly and with minimal waste.
Material Optimization
AFP also enables the use of different types of carbon fibers and matrix materials within a single component.
This “tailored” approach allows engineers to optimize the material properties for specific applications, enhancing both performance and durability.
3D Printing of CFRP
3D printing, or additive manufacturing, has opened new possibilities for creating CFRP components.
This technology allows for the fabrication of complex, multi-material structures that were previously impossible to achieve through traditional methods.
Direct Energy Deposition (DED)
Direct Energy Deposition (DED) is a form of 3D printing where focused energy sources, such as lasers or electron beams, are used to melt and deposit material.
Incorporating carbon fibers into the deposited material can produce highly robust and intricate structures.
DED is particularly useful for creating custom parts on-demand, reducing lead times and inventory costs.
Stereolithography (SLA) with Composite Resins
Stereolithography (SLA) is another 3D printing method that can be adapted for CFRP manufacturing by using composite resins.
These resins contain carbon fibers suspended in a photocurable liquid matrix.
When exposed to UV light, the resin hardens, forming a strong and lightweight component.
Recent advancements have improved the resolution and mechanical properties of SLA-printed parts, making them viable for high-performance applications.
Nanotechnology in CFRP
Nanotechnology is another area that has shown great promise in enhancing the properties of CFRP materials.
Incorporating nanoparticles into the polymer matrix can significantly improve the mechanical, thermal, and electrical properties of the composite.
Carbon Nanotubes (CNTs)
Carbon Nanotubes (CNTs) are cylindrical nanostructures that offer exceptional strength and electrical conductivity.
When incorporated into the polymer matrix, CNTs can enhance the composite’s mechanical performance and durability.
Advancements in CNT dispersion techniques have made it easier to integrate these nanoparticles uniformly, resulting in materials with superior properties.
Graphene
Graphene, a single layer of carbon atoms arranged in a hexagonal lattice, is another nanomaterial showing great potential.
It offers remarkable strength, flexibility, and thermal conductivity.
By incorporating graphene into CFRP, researchers have achieved significant improvements in strength and weight reduction.
Innovative production methods have made graphene more accessible, allowing for its broader application in CFRP manufacturing.
Sustainable Manufacturing of CFRP
Sustainability is becoming increasingly important in material science and manufacturing.
Several new techniques aim to make CFRP production more eco-friendly.
Recycling Methods
Traditional CFRP components are difficult to recycle due to the strong bonding between fibers and the matrix.
New methods, such as pyrolysis and solvolysis, are being developed to break down these bonds and reclaim the fibers for reuse.
These recycling processes not only reduce waste but also lower the environmental impact of CFRP production.
Bio-Based Resins
Another exciting development is the use of bio-based resins derived from renewable sources like plants and algae.
These resins offer similar performance characteristics to traditional petroleum-based resins but with a reduced carbon footprint.
Advancements in resin chemistry have made bio-based options more viable for high-performance applications, aligning CFRP manufacturing with sustainability goals.
The ongoing innovations in CFRP manufacturing technologies are propelling industries toward new heights of performance and efficiency.
From improved processing techniques to the incorporation of nanomaterials and sustainable practices, the future of CFRP is bright and full of possibilities.
These advancements not only make products lighter and stronger but also contribute to a more sustainable and efficient manufacturing landscape.
資料ダウンロード
QCD調達購買管理クラウド「newji」は、調達購買部門で必要なQCD管理全てを備えた、現場特化型兼クラウド型の今世紀最高の購買管理システムとなります。
ユーザー登録
調達購買業務の効率化だけでなく、システムを導入することで、コスト削減や製品・資材のステータス可視化のほか、属人化していた購買情報の共有化による内部不正防止や統制にも役立ちます。
NEWJI DX
製造業に特化したデジタルトランスフォーメーション(DX)の実現を目指す請負開発型のコンサルティングサービスです。AI、iPaaS、および先端の技術を駆使して、製造プロセスの効率化、業務効率化、チームワーク強化、コスト削減、品質向上を実現します。このサービスは、製造業の課題を深く理解し、それに対する最適なデジタルソリューションを提供することで、企業が持続的な成長とイノベーションを達成できるようサポートします。
オンライン講座
製造業、主に購買・調達部門にお勤めの方々に向けた情報を配信しております。
新任の方やベテランの方、管理職を対象とした幅広いコンテンツをご用意しております。
お問い合わせ
コストダウンが利益に直結する術だと理解していても、なかなか前に進めることができない状況。そんな時は、newjiのコストダウン自動化機能で大きく利益貢献しよう!
(Β版非公開)