- お役立ち記事
- Latest Technologies for Machining High-Hardness Materials in Production Machinery
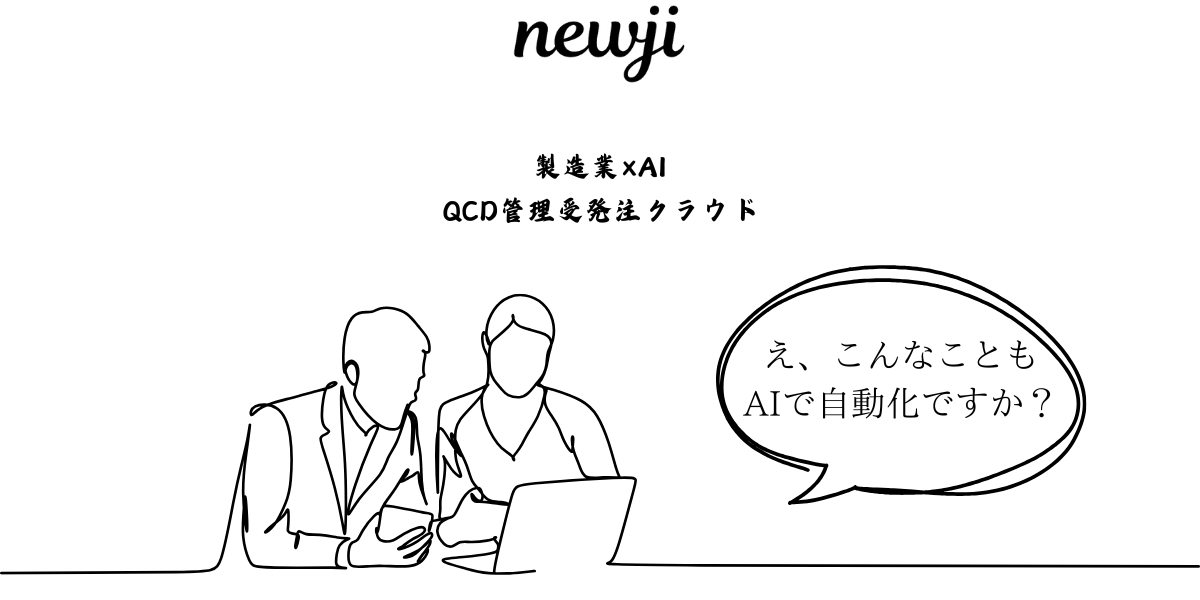
Latest Technologies for Machining High-Hardness Materials in Production Machinery
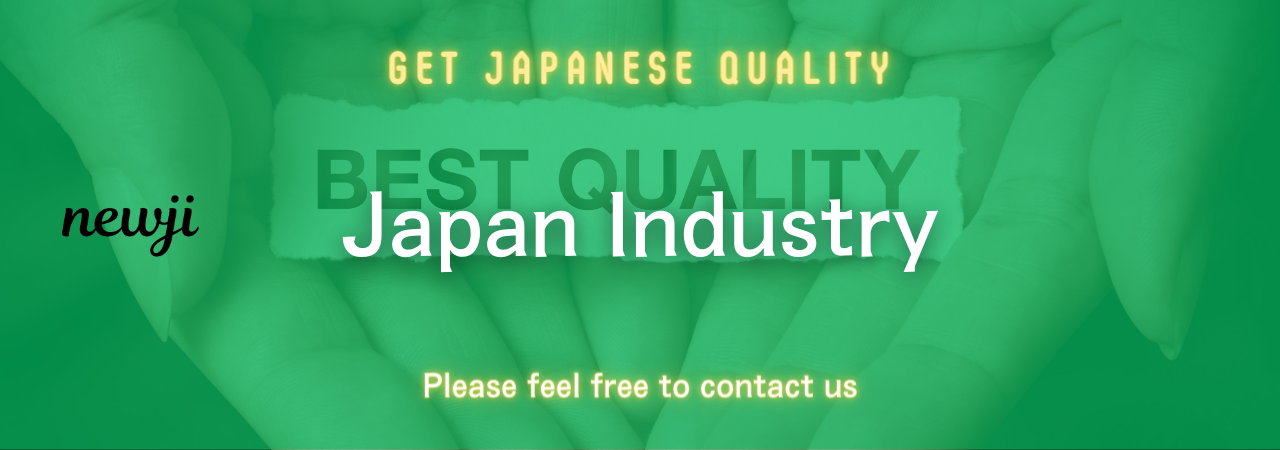
目次
Introduction to Machining High-Hardness Materials
In the world of production machinery, high-hardness materials pose unique challenges.
These materials, often used in industries like aerospace, automotive, and defense, require advanced techniques for machining.
Traditional methods may fall short, which is why the latest technologies have been developed to tackle these challenges head-on.
Understanding High-Hardness Materials
High-hardness materials include alloys, ceramics, and tool steels.
These materials are valued for their durability and strength.
However, their resistance to wear and deformation makes them difficult to cut or shape using standard machining techniques.
As a result, specialized tooling and processes are essential.
Challenges of Machining High-Hardness Materials
Machining these materials generates high levels of heat and stress.
Traditional tools can wear out quickly, leading to production downtime and increased costs.
Precision is critical, and even minor inaccuracies can result in significant issues in the final product.
The need for optimized processes is paramount in maintaining efficiency and quality.
Advancements in Cutting Tool Technology
Recent advancements in cutting tools have revolutionized the machining of high-hardness materials.
Innovations in tool materials and coatings play a significant role in enhancing tool life and cutting performance.
Carbide and Ceramics
Carbide tools, renowned for their strength, have been further developed to improve toughness and resistance to chipping.
Ceramic tools, meanwhile, are valued for their heat resistance and ability to maintain hardness at high temperatures.
These tools are particularly effective in high-speed applications.
Coatings and Surface Treatments
Various coatings, such as titanium aluminum nitride (TiAlN) and diamond-like carbon (DLC), are applied to cutting tools to reduce friction and increase wear resistance.
These coatings help maintain the sharpness of the tools, ensuring precision in machining hard materials.
Advanced Machining Techniques
New machining techniques have emerged to maximize efficiency and precision when working with high-hardness materials.
These advanced processes accommodate the limitations of traditional methods, offering innovative solutions.
High-Speed Machining (HSM)
High-speed machining uses increased spindle speeds and feed rates to improve material removal rates.
This method reduces the amount of heat generated by distributing it over a larger area, decreasing tool wear and enhancing surface finish quality.
Electrical Discharge Machining (EDM)
EDM is used for materials that are difficult to machine with traditional methods.
This process involves removing material by applying a series of electrical discharges.
EDM offers precision in creating intricate shapes and is suitable for hard and brittle materials.
Laser-Assisted Machining (LAM)
Laser-assisted machining uses a laser beam to preheat the material before cutting.
The preheating reduces the material’s hardness, allowing for easier milling or turning.
LAM is particularly effective for materials like ceramics and superalloys.
Benefits of Using Latest Technologies
Employing the latest technologies in machining high-hardness materials provides several benefits.
These advancements not only address the challenges but also empower manufacturers to achieve greater results.
Improved Tool Life and Cost Efficiency
Enhanced tool materials and coatings lead to longer tool life, reducing the frequency of tool changes and downtime.
This not only cuts costs but also maximizes productivity.
Precision and Quality
Advanced techniques ensure high precision, critical in applications where accuracy is paramount.
The quality of the final product improves, minimizing defects and enhancing customer satisfaction.
Environmental Impact
Technological advancements often emphasize sustainability.
Less energy consumption and waste generation are noticeable benefits, aligning with industry efforts to minimize environmental impact.
Conclusion
The challenges associated with machining high-hardness materials are significant, yet not insurmountable.
Through advancements in cutting tool technology and adaptation of cutting-edge machining techniques, industries can overcome these challenges efficiently.
As technologies continue to evolve, the potential for even greater breakthroughs remains promising.
Investments in these technologies signify a commitment to precision, efficiency, and sustainability in the production of machinery components.
資料ダウンロード
QCD調達購買管理クラウド「newji」は、調達購買部門で必要なQCD管理全てを備えた、現場特化型兼クラウド型の今世紀最高の購買管理システムとなります。
ユーザー登録
調達購買業務の効率化だけでなく、システムを導入することで、コスト削減や製品・資材のステータス可視化のほか、属人化していた購買情報の共有化による内部不正防止や統制にも役立ちます。
NEWJI DX
製造業に特化したデジタルトランスフォーメーション(DX)の実現を目指す請負開発型のコンサルティングサービスです。AI、iPaaS、および先端の技術を駆使して、製造プロセスの効率化、業務効率化、チームワーク強化、コスト削減、品質向上を実現します。このサービスは、製造業の課題を深く理解し、それに対する最適なデジタルソリューションを提供することで、企業が持続的な成長とイノベーションを達成できるようサポートします。
オンライン講座
製造業、主に購買・調達部門にお勤めの方々に向けた情報を配信しております。
新任の方やベテランの方、管理職を対象とした幅広いコンテンツをご用意しております。
お問い合わせ
コストダウンが利益に直結する術だと理解していても、なかなか前に進めることができない状況。そんな時は、newjiのコストダウン自動化機能で大きく利益貢献しよう!
(Β版非公開)