- お役立ち記事
- Latest Technologies for Optimizing Clamping Force and Case Studies of Implementation
Latest Technologies for Optimizing Clamping Force and Case Studies of Implementation
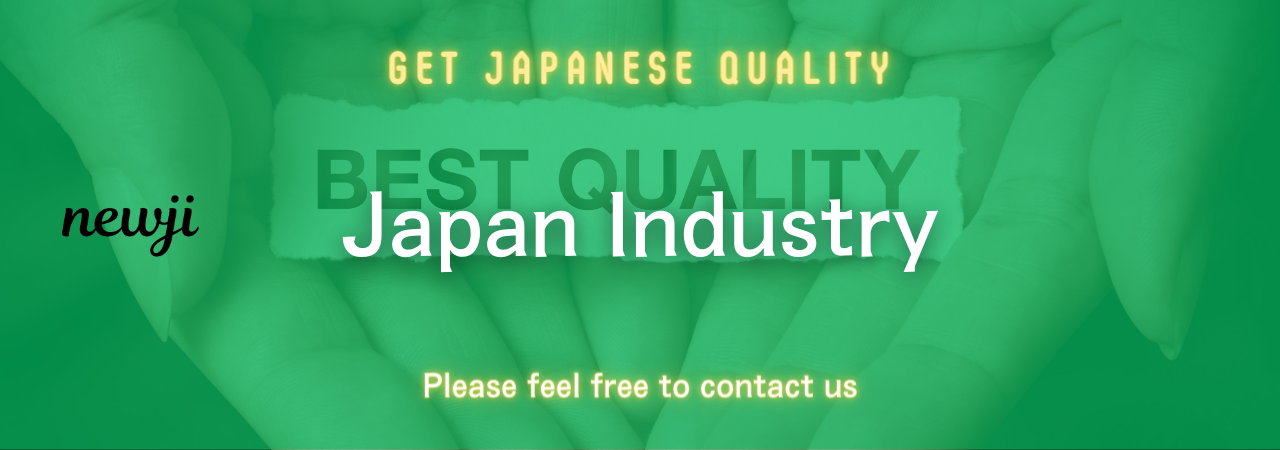
目次
Introduction to Clamping Force Optimization
In the realm of manufacturing, the importance of clamping force cannot be overstated.
It’s a critical factor that ensures tools and workpieces remain secure during the machining or molding process.
Proper clamping optimizes the efficiency and safety of operations, reducing the risk of tool wear and product defects.
With advancements in technology, optimizing clamping force is more precise and effective, paving the way for innovation and increased productivity.
Understanding Clamping Force
Clamping force is the pressure applied by a clamp to hold an object securely in place.
The force must be sufficient to prevent slippage and movement, but not so excessive that it damages the object being held.
Industries such as automotive, aerospace, and electronics often rely on precise clamping force to ensure product integrity.
The Role of Clamping Force in Manufacturing
In manufacturing, clamping force plays a crucial role in maintaining the positional stability of parts.
This stability is essential to ensure that parts are machined or molded with the highest precision.
Incorrect clamping force can lead to various issues, including misalignment, deformation, and defective end products.
Latest Technologies for Optimizing Clamping Force
With continuous technological advancements, new methods and tools have emerged to optimize clamping force effectively.
These technologies are designed to enhance accuracy, reduce downtime, and improve overall operational efficiency.
Smart Clamping Systems
Smart clamping systems integrate sensors and actuators to automatically adjust the applied force based on real-time data feedback.
These systems use advanced algorithms to calculate the optimum clamping pressure for a specific application.
This reduces the risk of human error and ensures consistent application across production cycles.
They also enable predictive maintenance by alerting operators to potential issues before they cause downtime.
Hydraulic Clamping Solutions
Modern hydraulic clamping systems offer robust and precise force control.
They provide a uniform clamping force distribution, reducing the potential for part deformation.
These systems are relatively easy to automate and are often integrated with CNC machines for streamlined operations.
Electromagnetic Clamping
Electromagnetic clamping is gaining popularity in industries where quick changeover times are essential.
This method utilizes powerful magnetic fields to secure parts.
It’s particularly effective for ferrous materials and offers significant advantages in terms of speed and ease of use.
By eliminating the need for mechanical adjustments, electromagnetic clamping reduces setup times and increases production throughput.
Advanced Materials for Clamping Tools
The use of advanced materials, such as lightweight composites and high-strength alloys, has improved the performance of clamping tools.
These materials offer enhanced durability and resistance to wear, extending the life of clamps.
Their lightweight nature can also lower machine load and reduce energy consumption.
Case Studies of Implementation
The integration of these advanced technologies into manufacturing processes has had significant impacts, as demonstrated by various case studies.
Automotive Industry: Enhancing Production Efficiency
In the automotive industry, a major manufacturer implemented smart clamping systems in their assembly lines.
The deployment resulted in a 20% increase in production efficiency and a 15% decrease in downtime.
The automatic adjustments and predictive maintenance capabilities allowed the manufacturer to maintain high quality without compromising speed.
Aerospace Sector: Ensuring Precision and Safety
An aerospace components manufacturer adopted hydraulic clamping solutions to handle delicate components.
The uniform force application and precision control reduced the occurrence of part rejection due to deformation, saving costs and maintaining stringent safety standards.
This implementation led to greater customer satisfaction and helped the company secure additional contracts.
Electronics Manufacturing: Speed and Versatility
A leading electronics assembly company faced challenges with frequent tool changes and limited production flexibility.
By incorporating electromagnetic clamping, they achieved faster changeovers and improved versatility in handling different product configurations.
The time saved on tool changes translated into increased production capacity and responsiveness to market demands.
Benefits of Optimized Clamping Force
Optimizing clamping force brings several benefits to manufacturing operations.
Increased Efficiency and Productivity
With optimized clamping force, processes become more efficient, reducing cycle times and boosting overall productivity.
This efficiency results in lower operational costs and higher output rates.
Enhanced Product Quality
Proper clamping force minimizes product defects and inconsistencies.
By ensuring secure and stable positioning, it enhances the quality of finished products and reduces waste.
Reduced Equipment Wear and Maintenance
Optimizing clamping force can decrease tool and machine wear, leading to fewer repairs and replacements.
This not only extends equipment lifespan but also reduces maintenance costs and downtime.
Improved Worker Safety
Automation and precision in clamping force settings reduce the risk of accidents related to incorrect handling or part slippage.
Safer working conditions lead to lower injury rates and boost workforce morale.
Conclusion
The technological advancements in optimizing clamping force are transforming manufacturing processes.
They offer significant benefits, including improved efficiency, product quality, and operational safety.
As industries continue to evolve, the deployment of smart systems, hydraulic and electromagnetic solutions, and advanced materials will play a crucial role in shaping the future of manufacturing.
資料ダウンロード
QCD調達購買管理クラウド「newji」は、調達購買部門で必要なQCD管理全てを備えた、現場特化型兼クラウド型の今世紀最高の購買管理システムとなります。
ユーザー登録
調達購買業務の効率化だけでなく、システムを導入することで、コスト削減や製品・資材のステータス可視化のほか、属人化していた購買情報の共有化による内部不正防止や統制にも役立ちます。
NEWJI DX
製造業に特化したデジタルトランスフォーメーション(DX)の実現を目指す請負開発型のコンサルティングサービスです。AI、iPaaS、および先端の技術を駆使して、製造プロセスの効率化、業務効率化、チームワーク強化、コスト削減、品質向上を実現します。このサービスは、製造業の課題を深く理解し、それに対する最適なデジタルソリューションを提供することで、企業が持続的な成長とイノベーションを達成できるようサポートします。
オンライン講座
製造業、主に購買・調達部門にお勤めの方々に向けた情報を配信しております。
新任の方やベテランの方、管理職を対象とした幅広いコンテンツをご用意しております。
お問い合わせ
コストダウンが利益に直結する術だと理解していても、なかなか前に進めることができない状況。そんな時は、newjiのコストダウン自動化機能で大きく利益貢献しよう!
(Β版非公開)