- お役立ち記事
- Latest Technologies in Hold Pressure Processes and Case Studies of Their Application
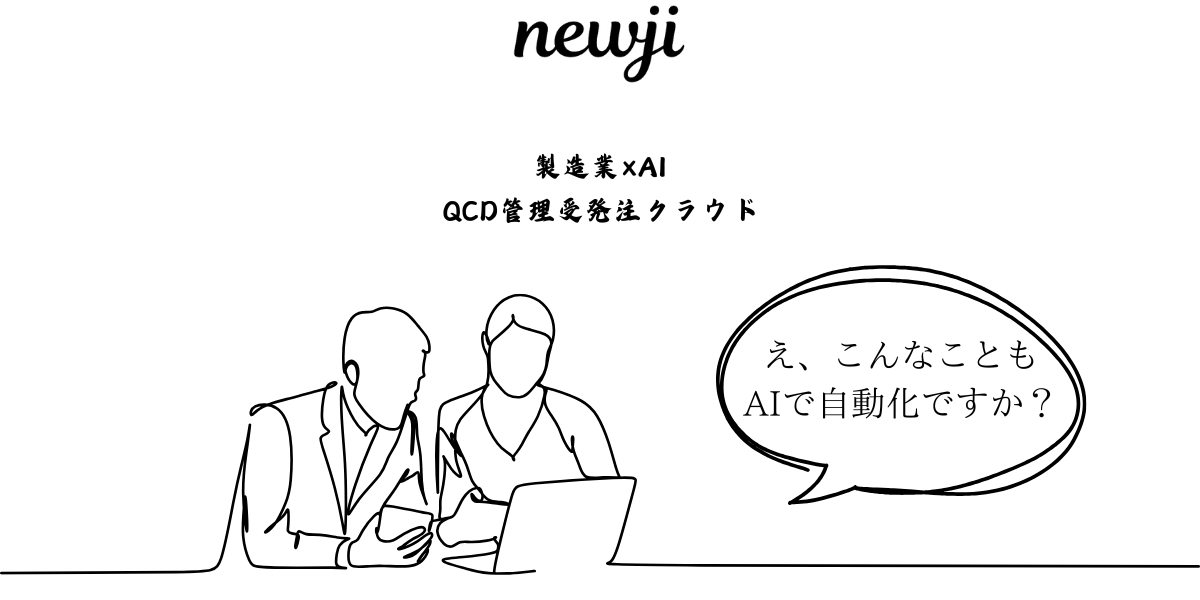
Latest Technologies in Hold Pressure Processes and Case Studies of Their Application
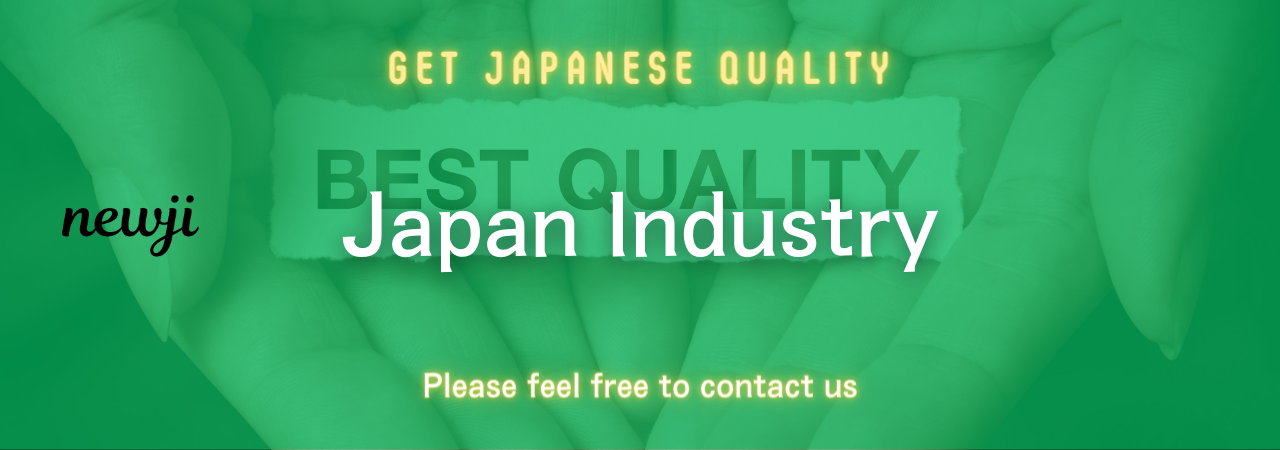
目次
Understanding Hold Pressure in Manufacturing
Hold pressure is a critical concept in various manufacturing processes, particularly those involving molding and shaping materials like plastics or metals.
In these processes, hold pressure is applied to ensure the material conforms to the desired shape and dimensions during and after the molding stage.
The pressure is maintained for a specific duration to ensure product integrity and minimize defects.
Advancements in technology have significantly enhanced the methods and tools used to control and optimize hold pressure.
These innovations not only improve the quality of the finished products but also increase the efficiency and sustainability of manufacturing operations.
Latest Technologies in Hold Pressure Processes
Several new technologies have emerged in recent years to improve hold pressure processes.
These advancements focus on automation, real-time data monitoring, and predictive analytics to enhance precision and efficiency.
Automated Control Systems
Automated control systems are revolutionizing how hold pressure is applied and monitored.
These systems use sensors and advanced algorithms to adjust pressure levels in real-time, ensuring optimal conditions are maintained throughout the manufacturing process.
This automation reduces human error and increases the consistency of the products.
Incorporating machine learning algorithms allows systems to learn from data patterns.
This learning enables more precise control over hold pressure, as the system can adjust variables based on historical data and predicted trends.
Real-Time Data Monitoring
Real-time data monitoring tools provide manufacturers with immediate insights into the hold pressure processes.
Sensors installed in machines collect data continuously and transmit it to centralized systems for analysis.
This detailed monitoring helps in identifying any deviations from the set parameters promptly.
Operators can then take corrective actions to bring the process back on track, thus preventing defects and material wastage.
These systems often use advanced analytics software to present data in an easily understandable format, enabling quick decision-making.
Predictive Maintenance
Predictive maintenance is another technology making significant strides in improving hold pressure processes.
Traditional maintenance often involves scheduled checks, whether needed or not, which can lead to unnecessary downtime or unexpected failures.
Predictive maintenance systems, on the other hand, use data analytics to predict when a machine is likely to fail.
By integrating predictive maintenance systems, manufacturers can ensure that machinery involved in hold pressure processes operates at peak efficiency.
This approach not only extends the lifespan of equipment but also ensures consistent quality in production by minimizing unplanned disruptions.
Case Studies of Technology Application
To illustrate the effectiveness of these technologies, let’s explore some real-world case studies.
These examples demonstrate how companies have leveraged the latest technologies to enhance their hold pressure processes.
Automotive Industry: Reducing Production Defects
In the automotive industry, the precision of injection molding is crucial for producing high-quality parts.
One major automotive manufacturer implemented an automated control system to manage hold pressure in their molding processes.
By using real-time data analytics, the company was able to reduce production defects by 30% within the first six months.
The system provided insights into how different materials responded to pressure, allowing engineers to refine the process further.
This case highlights the potential for significant quality improvements and cost savings when leveraging technology in hold pressure applications.
Consumer Electronics: Enhancing Efficiency
A leading consumer electronics company faced challenges with maintaining consistent product quality in their plastic casings.
They introduced real-time data monitoring systems to oversee hold pressure during the manufacturing process.
The sensors allowed for constant tracking and adjustment of pressure levels, ensuring uniformity across batches.
As a result, the company saw a 20% increase in manufacturing efficiency and a noticeable improvement in product quality.
The real-time feedback loop enabled by the data monitoring system was instrumental in achieving these outcomes.
Medical Device Manufacturing: Ensuring Precision and Reliability
In the medical device industry, precision is of utmost importance.
A medical device manufacturer incorporated predictive maintenance technology to enhance their production line’s reliability.
With the ability to foresee machinery issues before they occurred, the company minimized downtime and maintained high standards in their hold pressure processes.
This integration not only enhanced product reliability but also improved overall patient safety by ensuring consistent device quality.
Such applications underscore the critical role new technologies play in advancing industries where precision and reliability are non-negotiable.
Future Directions and Innovations
The future of hold pressure technology seems promising, with continuous innovations anticipated.
Developments such as artificial intelligence (AI) and the Internet of Things (IoT) will likely play significant roles.
These technologies can further automate and streamline processes, increasing accuracy and efficiency.
AI can enhance decision-making capabilities, allowing systems to predict and optimize pressure levels automatically without human intervention.
IoT, on the other hand, can interconnect machines, facilitating even more seamless data exchange and monitoring capabilities on a global scale.
The integration of these futuristic technologies can propel hold pressure processes into a new era of manufacturing excellence, paving the way for even higher standards of quality and efficiency in production.
Incorporating these technologies into hold pressure processes offers immense potential to revolutionize various industries.
By staying informed and adaptable, manufacturers can ensure they remain at the forefront of technological advancements, driving innovation and improvement in their operations.
資料ダウンロード
QCD調達購買管理クラウド「newji」は、調達購買部門で必要なQCD管理全てを備えた、現場特化型兼クラウド型の今世紀最高の購買管理システムとなります。
ユーザー登録
調達購買業務の効率化だけでなく、システムを導入することで、コスト削減や製品・資材のステータス可視化のほか、属人化していた購買情報の共有化による内部不正防止や統制にも役立ちます。
NEWJI DX
製造業に特化したデジタルトランスフォーメーション(DX)の実現を目指す請負開発型のコンサルティングサービスです。AI、iPaaS、および先端の技術を駆使して、製造プロセスの効率化、業務効率化、チームワーク強化、コスト削減、品質向上を実現します。このサービスは、製造業の課題を深く理解し、それに対する最適なデジタルソリューションを提供することで、企業が持続的な成長とイノベーションを達成できるようサポートします。
オンライン講座
製造業、主に購買・調達部門にお勤めの方々に向けた情報を配信しております。
新任の方やベテランの方、管理職を対象とした幅広いコンテンツをご用意しております。
お問い合わせ
コストダウンが利益に直結する術だと理解していても、なかなか前に進めることができない状況。そんな時は、newjiのコストダウン自動化機能で大きく利益貢献しよう!
(Β版非公開)