- お役立ち記事
- Latest technology and application examples for non-destructive inspection of internal defects in resin parts
月間76,176名の
製造業ご担当者様が閲覧しています*
*2025年3月31日現在のGoogle Analyticsのデータより
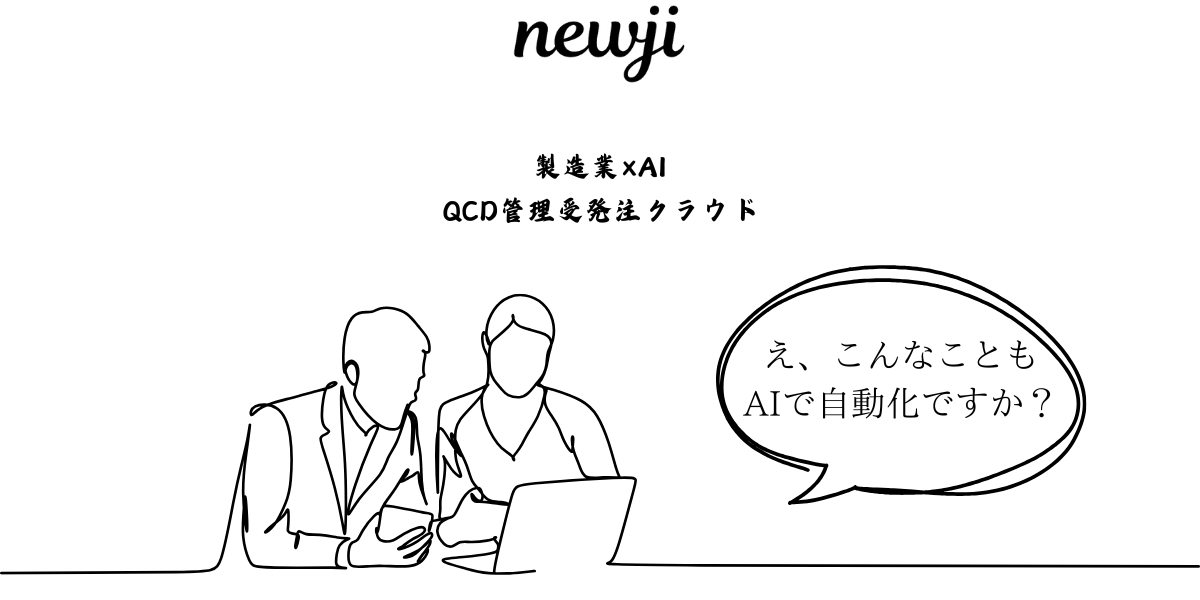
Latest technology and application examples for non-destructive inspection of internal defects in resin parts
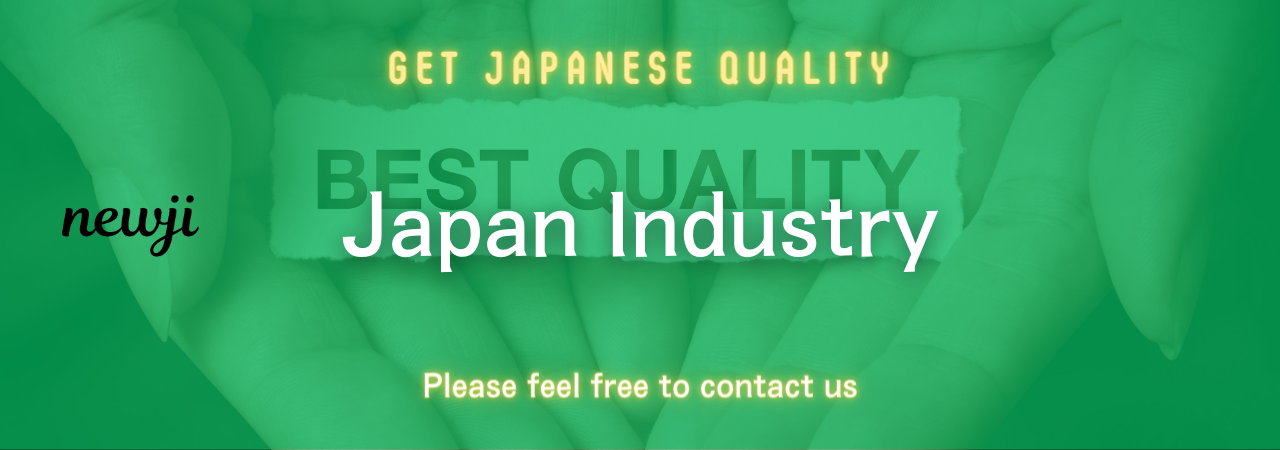
目次
Introduction to Non-Destructive Inspection
Non-destructive inspection (NDI) is a critical process in the manufacturing industry, especially for resin parts.
It allows engineers and quality control teams to evaluate the integrity of a product without causing any damage.
This is particularly important for resin parts, which are widely used in various applications from automotive to consumer electronics.
The ability to inspect these parts thoroughly without altering their usability is invaluable.
With the latest technological advancements, NDI methods have become more reliable, efficient, and user-friendly.
Why Inspect Resin Parts?
Resin parts are used extensively due to their lightweight and versatile nature.
However, these components can sometimes have internal defects such as voids, cracks, or inclusions.
If left undetected, these defects may lead to product failure, affecting safety and performance.
Therefore, conducting NDI on resin parts ensures they meet quality standards and function as intended.
This process helps manufacturers avoid costly recalls and maintains customer trust in the product.
Technological Advancements in NDI
Several new technologies have emerged in recent years to enhance the inspection of resin parts.
Some of the most notable advancements include digital radiography, ultrasonic testing, infrared thermography, and computed tomography.
Digital Radiography
Digital radiography has become a popular method due to its high-resolution imaging capabilities.
It uses X-rays to produce digital images of the material being inspected.
This method is advantageous because it provides quick results and is highly accurate, allowing detailed analysis of the internal structure of resin parts.
Compared to traditional radiography, digital options reduce exposure time and can be easily integrated into automated inspection systems.
Ultrasonic Testing
Ultrasonic testing involves the use of high-frequency sound waves to detect internal defects in materials.
This technique is particularly effective for inspecting resin parts of varying thickness.
One significant advantage is its ability to provide real-time feedback, making it suitable for in-line production inspections.
Recent advancements have improved the precision of ultrasonic testing, making it more reliable in detecting even the smallest anomalies within a resin part.
Infrared Thermography
Infrared thermography is another cutting-edge technology used for inspecting resin parts.
This non-contact method utilizes thermal imaging to detect variations in temperature on the surface of a component.
Such variations often indicate underlying defects.
Advancements in infrared sensor technology have increased the sensitivity and resolution of thermal images, providing more accurate inspections.
This method is particularly beneficial for complex shapes and surfaces where other NDI techniques might struggle.
Computed Tomography (CT)
Computed tomography combines X-ray imaging with advanced computational techniques to generate 3D models of a part’s internal structure.
This technology offers unparalleled insight into the composition and integrity of resin parts.
It allows engineers to detect even the most inconspicuous defects with a high degree of accuracy.
Although traditionally seen as a costly option, recent technological improvements have made CT more accessible and cost-effective for routine inspections.
Application Examples
The application of these advanced NDI technologies spans various industries:
Automotive Industry
In the automotive sector, resin parts are widely used in components like dashboards, bumpers, and interior panels.
Ensuring these parts are free of defects is crucial for vehicle safety and durability.
NDI methods are commonly applied to inspect these components during production, helping manufacturers maintain high quality.
Aerospace Sector
The aerospace industry utilizes resin parts in aircraft interiors and structural components.
NDI plays a vital role in the sector, as any failure could have catastrophic consequences.
Techniques like ultrasonic testing and computed tomography ensure that these parts meet stringent safety and performance standards before they’re deemed ready for use.
Consumer Electronics
Many consumer electronic products feature resin components in their casings and circuit boards.
Inspecting these components non-destructively helps manufacturers ensure they are free of defects, thus avoiding malfunctions.
Infrared thermography and digital radiography are particularly popular in this domain due to their ability to quickly process high volumes of parts.
Conclusion
The latest technology in non-destructive inspection provides manufacturers with effective tools to evaluate the quality of resin parts.
With digital radiography, ultrasonic testing, infrared thermography, and computed tomography, industries can ensure that their products meet the highest standards without the risk of damage.
As these technologies continue to develop, the scope and precision of NDI in quality control will only enhance further.
Consequently, industries that rely heavily on resin parts are better equipped to provide safe, high-quality products for their customers.
資料ダウンロード
QCD管理受発注クラウド「newji」は、受発注部門で必要なQCD管理全てを備えた、現場特化型兼クラウド型の今世紀最高の受発注管理システムとなります。
ユーザー登録
受発注業務の効率化だけでなく、システムを導入することで、コスト削減や製品・資材のステータス可視化のほか、属人化していた受発注情報の共有化による内部不正防止や統制にも役立ちます。
NEWJI DX
製造業に特化したデジタルトランスフォーメーション(DX)の実現を目指す請負開発型のコンサルティングサービスです。AI、iPaaS、および先端の技術を駆使して、製造プロセスの効率化、業務効率化、チームワーク強化、コスト削減、品質向上を実現します。このサービスは、製造業の課題を深く理解し、それに対する最適なデジタルソリューションを提供することで、企業が持続的な成長とイノベーションを達成できるようサポートします。
製造業ニュース解説
製造業、主に購買・調達部門にお勤めの方々に向けた情報を配信しております。
新任の方やベテランの方、管理職を対象とした幅広いコンテンツをご用意しております。
お問い合わせ
コストダウンが利益に直結する術だと理解していても、なかなか前に進めることができない状況。そんな時は、newjiのコストダウン自動化機能で大きく利益貢献しよう!
(β版非公開)