- お役立ち記事
- Latest Technology in Compression Molding and Efficiency Gains Through Implementation
月間76,176名の
製造業ご担当者様が閲覧しています*
*2025年3月31日現在のGoogle Analyticsのデータより
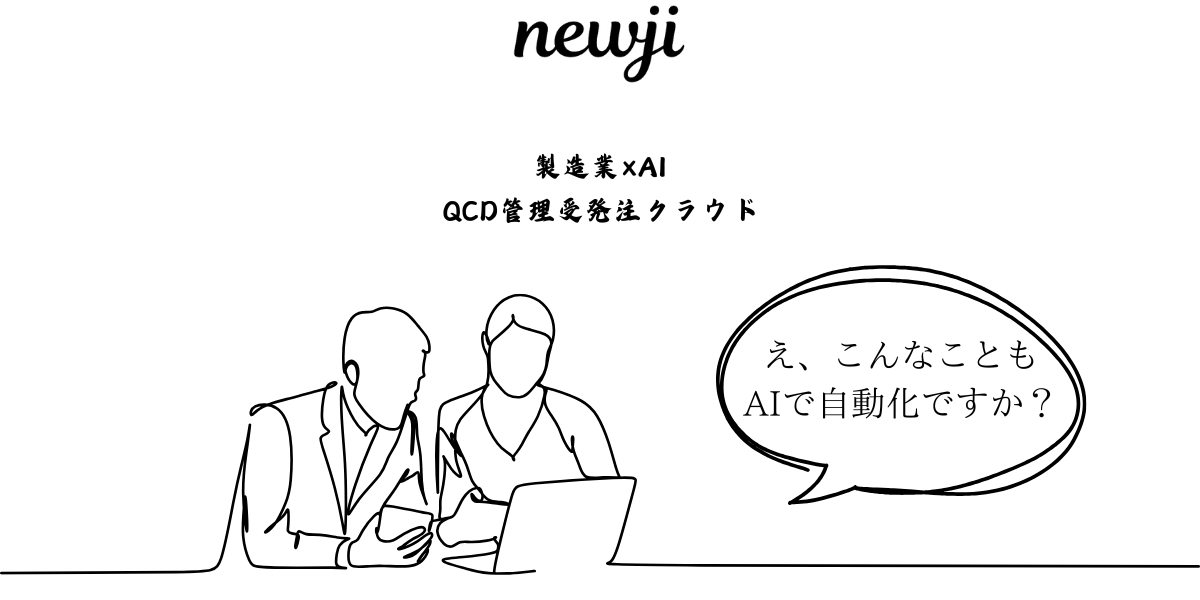
Latest Technology in Compression Molding and Efficiency Gains Through Implementation
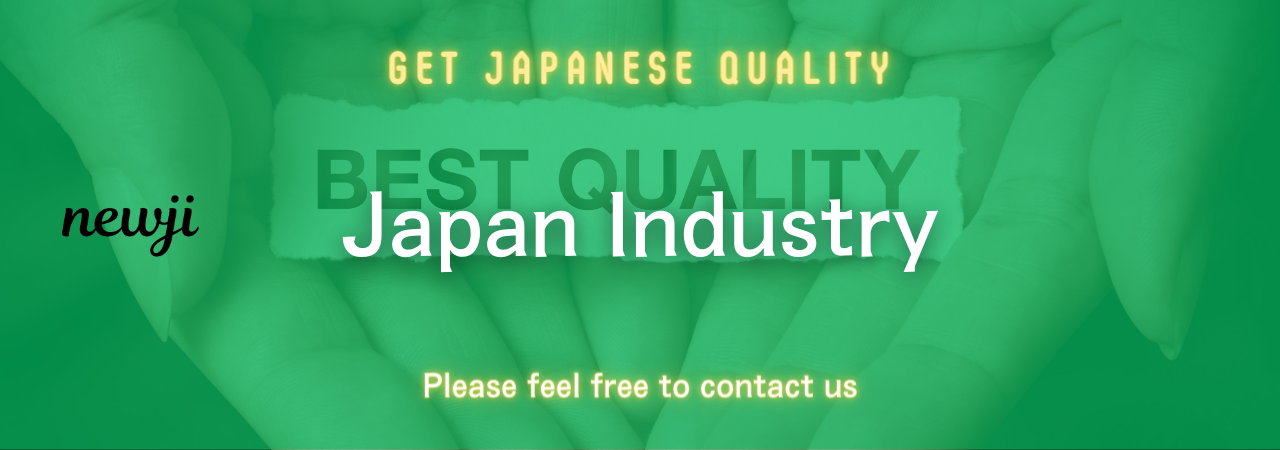
目次
Understanding Compression Molding
Compression molding is a manufacturing process that involves shaping a material inside a heated mold using pressure.
The technique is widely employed in the production of various polymer matrix composites.
This method is highly regarded in the industry for its ability to produce parts with high strength and good surface finish.
The process starts by placing the molding material, often preheated, into the open, heated mold cavity.
Then, the mold is closed and pressure is applied to force the material to fill the mold’s shape.
Once the material cools and solidifies, the mold is opened, and the finished part is removed.
Compression molding is especially beneficial for producing large, relatively flat parts with complex geometries.
It’s a cost-effective method that minimizes waste material while producing durable and reliable components.
This process is ideal for automotive parts, appliances, and heavy-duty equipment.
Advancements in Compression Molding Technology
Recent advancements in compression molding technology have focused on increasing efficiency and expanding the range of materials that can be used.
One notable development is the introduction of high-performance polymers and blends that offer enhanced properties.
These new materials provide greater strength and durability, allowing manufacturers to produce lighter but more robust components.
Additionally, developments in mold design and manufacturing have led to improved heat transfer and cycle times.
These innovations help reduce energy consumption and increase production speed.
Modern molds often feature enhanced cooling systems that can rapidly dissipate heat, preventing warping or defects in the final product.
Automation is another significant advancement in compression molding technology.
Automated systems and robotics can now handle material placement and part removal, which reduces labor costs and increases consistency.
These systems ensure precise and repeatable processes, which is crucial for high-volume production runs.
Efficiency Gains Through Implementation
Implementing the latest compression molding technologies can lead to substantial efficiency gains for manufacturers.
Firstly, the use of high-performance materials means less material is needed to achieve desired strength, reducing material costs.
Additionally, faster cycle times contribute to increased production rates, allowing manufacturers to meet demand more effectively.
Another area of efficiency improvement is the reduction of waste.
Traditional manufacturing methods often result in significant material wastage, but compression molding minimizes this by precisely using the required material amount.
This not only reduces costs but also contributes to more sustainable manufacturing practices.
The integration of automation in the compression molding process reduces the dependency on manual labor.
This results in fewer human errors and more precise control over the manufacturing environment.
Automation also enables manufacturers to run operations 24/7, significantly increasing output and optimizing resource utilization.
Case Study: Automotive Industry
The automotive industry is one of the leading sectors benefitting from advancements in compression molding.
Automotive manufacturers utilize the process to produce a variety of components, from under-hood parts to interior trim pieces.
The lightweight yet strong components contribute to overall vehicle efficiency and performance.
By implementing automated compression molding systems, car manufacturers have been able to decrease production costs while improving part quality.
These systems ensure that each part meets rigorous industry standards for safety and durability.
The ability to mass-produce lightweight components also aids in reducing fuel consumption and emissions, aligning with global sustainability goals.
Challenges and Considerations
While compression molding offers numerous benefits, it is not without challenges.
The initial setup and development of molds can be costly and time-consuming, particularly for custom or highly intricate designs.
Companies must consider these upfront costs when deciding to invest in the technology.
Material selection is another critical factor.
While new materials offer enhanced properties, they may also require specific handling and processing conditions.
Ensuring compatibility with existing equipment and processes is essential to fully reap the benefits of these advancements.
Lastly, implementing automated systems requires significant investment in machinery and training.
Manufacturers must ensure that their workforce is adequately trained to handle new technologies and systems.
Maintenance and regular updates of automated systems are also necessary to sustain long-term efficiency benefits.
Future Trends in Compression Molding
The future of compression molding promises even more exciting developments.
One trend is the continued exploration and use of bio-based materials to further promote sustainable manufacturing practices.
These materials can reduce reliance on fossil fuels and decrease the environmental impact of production.
Nanocomposites are also gaining attention for their potential to significantly improve material properties.
Incorporating nanoparticles into polymers can enhance strength, thermal stability, and chemical resistance of molded parts.
This innovation opens up new possibilities for the application of compression molding across different industries.
Another future trend is the integration of smart technology into molds and machines.
This can involve sensors that monitor real-time conditions within the mold, providing data to optimize the molding process continuously.
Such smart technologies can help in predictive maintenance, reducing downtime and enhancing the overall efficiency of manufacturing processes.
As compression molding continues to evolve, manufacturers will likely see more streamlined operations, improved product quality, and increased competitiveness in the market.
Embracing these technological advancements is key to securing a strong position in an ever-advancing industrial landscape.
資料ダウンロード
QCD管理受発注クラウド「newji」は、受発注部門で必要なQCD管理全てを備えた、現場特化型兼クラウド型の今世紀最高の受発注管理システムとなります。
ユーザー登録
受発注業務の効率化だけでなく、システムを導入することで、コスト削減や製品・資材のステータス可視化のほか、属人化していた受発注情報の共有化による内部不正防止や統制にも役立ちます。
NEWJI DX
製造業に特化したデジタルトランスフォーメーション(DX)の実現を目指す請負開発型のコンサルティングサービスです。AI、iPaaS、および先端の技術を駆使して、製造プロセスの効率化、業務効率化、チームワーク強化、コスト削減、品質向上を実現します。このサービスは、製造業の課題を深く理解し、それに対する最適なデジタルソリューションを提供することで、企業が持続的な成長とイノベーションを達成できるようサポートします。
製造業ニュース解説
製造業、主に購買・調達部門にお勤めの方々に向けた情報を配信しております。
新任の方やベテランの方、管理職を対象とした幅広いコンテンツをご用意しております。
お問い合わせ
コストダウンが利益に直結する術だと理解していても、なかなか前に進めることができない状況。そんな時は、newjiのコストダウン自動化機能で大きく利益貢献しよう!
(β版非公開)