- お役立ち記事
- Latest Trends in Effective Factory Layout Implementation
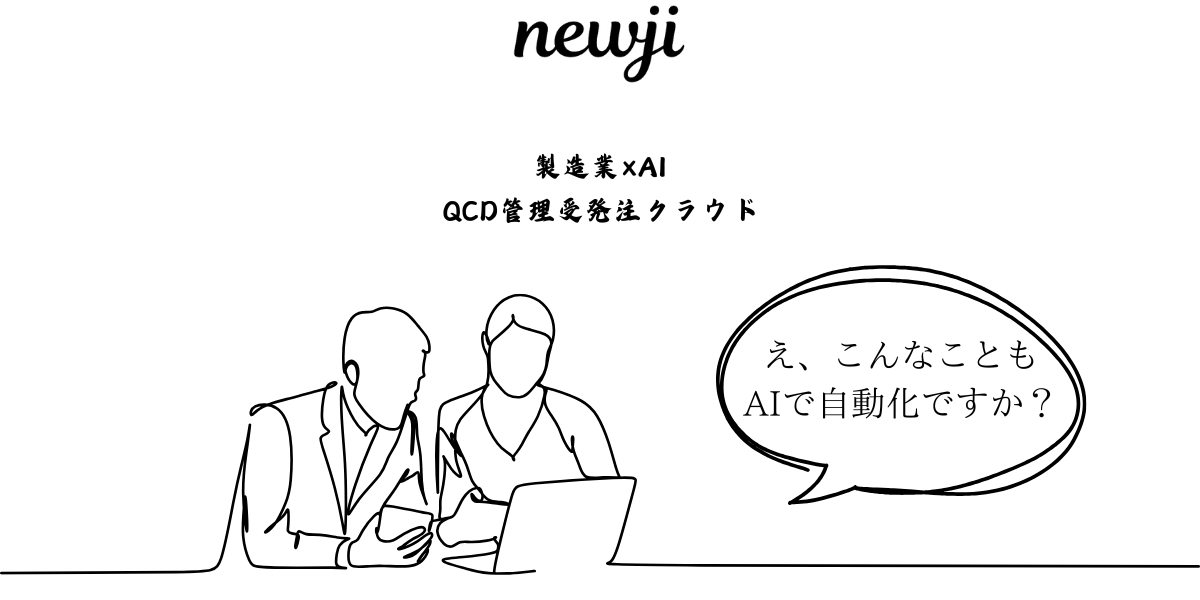
Latest Trends in Effective Factory Layout Implementation
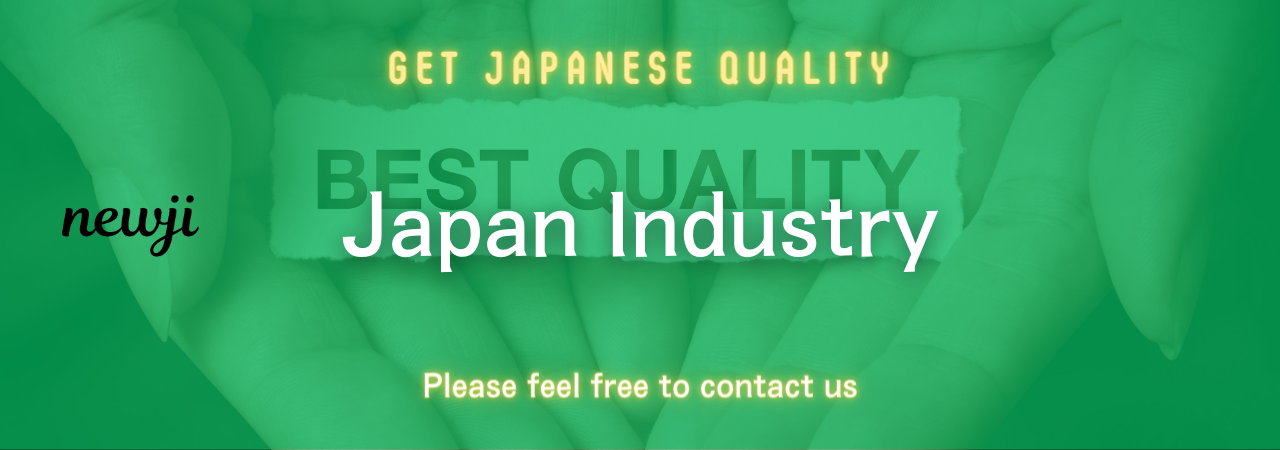
In today’s fast-paced industrial world, optimizing factory layouts is more crucial than ever. The latest trends in effective factory layout implementation can greatly improve efficiency, reduce costs, and enhance overall productivity. Businesses are constantly seeking innovative ways to streamline their operations, which makes understanding these trends essential.
目次
Embracing Lean Manufacturing Principles
Lean manufacturing is not a new concept, but its application to factory layouts continues to evolve. The core principle of lean manufacturing is to minimize waste while maximizing value. This involves carefully analyzing every step of the production process to ensure resources are used as efficiently as possible.
One of the latest trends in lean manufacturing is the implementation of flexible workstations. These are designed to be easily movable and reconfigurable, allowing factories to adapt quickly to changes in production demands. With flexible workstations, downtime is minimized during retooling or shifting production lines, thereby maintaining high levels of productivity.
Integration of IoT and Smart Technologies
The Internet of Things (IoT) and smart technologies are revolutionizing factory layouts. By integrating IoT devices, factories can collect real-time data on operations, equipment health, and worker productivity. This data can then be used to optimize layouts and workflows, ensuring that the factory runs as smoothly as possible.
For instance, IoT-enabled sensors can monitor the performance of machinery and alert management about potential issues before they cause significant downtime. Similarly, smart technologies like automated guided vehicles (AGVs) can be used to transport materials efficiently within the factory, reducing the need for manual labor and cutting down transit times.
Ergonomic and Employee-Centric Designs
Manufacturers are increasingly recognizing the importance of creating factory layouts that prioritize the health and well-being of their employees. Ergonomic designs aim to reduce physical strain and the risk of injury by considering human factors in the arrangement of workstations and equipment.
Height-adjustable workstations, for instance, can accommodate workers of different statures, reducing the risk of musculoskeletal disorders. Furthermore, well-planned layouts that minimize unnecessary movement can help reduce fatigue and increase overall worker satisfaction, which can positively impact productivity.
Sustainability in Layout Design
As environmental concerns become more pressing, sustainable practices are gaining prominence in factory layout design. Efficient use of space is one key aspect of sustainable factory design. By reducing the footprint of production processes, factories can minimize their environmental impact.
Energy-efficient lighting and climate control systems are also critical components of sustainable factory layouts. Using natural lighting and ventilation where possible can reduce energy consumption and create a more pleasant working environment. Additionally, strategically placing machinery to optimize energy flow can contribute to overall energy savings.
Utilizing Renewable Energy Sources
Another trend in sustainable factory design is the incorporation of renewable energy sources. Solar panels, wind turbines, and geothermal systems are increasingly being used to power factories. This not only reduces reliance on non-renewable energy but also cuts operational costs in the long run.
Recycling and Waste Management
Factories are also focusing more on recycling and effective waste management. By designing layouts that facilitate easy waste segregation and recycling, factories can significantly reduce their environmental footprint. This involves placing recycling stations in strategic locations and ensuring that processes are in place to handle waste efficiently.
Advanced Simulation and Modeling Tools
The use of advanced simulation and modeling tools is another trend shaping factory layouts today. These tools allow factory designers to create virtual models of the factory layout and simulate various scenarios. This helps in identifying potential bottlenecks, optimizing workflow, and testing different configurations before implementation.
Simulation tools can also be used to plan for future expansions. By modeling different layout scenarios, manufacturers can make informed decisions about scaling up production without disrupting current operations. This predictive capability is invaluable in maintaining continuous improvement and optimal factory performance.
Collaborative Robots (Cobots)
Collaborative robots, or cobots, are becoming increasingly popular in modern factories. Unlike traditional industrial robots, cobots are designed to work alongside human workers, enhancing productivity and safety.
Cobots can take on repetitive and physically demanding tasks, freeing up human workers for more complex and creative activities. This collaboration can lead to more efficient use of both human and robotic capabilities, optimizing the overall factory layout.
Modular Layouts
Modular layouts are another emerging trend in factory design. This approach involves creating factory layouts that can be easily reconfigured or expanded as needed. Modular layouts offer great flexibility, allowing manufacturers to respond quickly to changes in demand or production processes.
These layouts typically involve standardized sections or modules that can be rearranged without significant downtime. This adaptability is particularly useful in industries with rapidly changing markets or where customization is a key competitive advantage.
Conclusion
The latest trends in effective factory layout implementation are increasingly focused on flexibility, efficiency, and sustainability. By embracing lean principles, integrating smart technologies, prioritizing ergonomic designs, and adopting sustainable practices, manufacturers can significantly enhance their operations.
Moreover, using advanced simulation tools and incorporating collaborative robots can lead to more optimized and adaptable factory layouts. These trends not only improve productivity but also contribute to a safer and more sustainable working environment.
As factories continue to evolve, staying informed about these trends will be essential for manufacturers looking to maintain a competitive edge.
資料ダウンロード
QCD調達購買管理クラウド「newji」は、調達購買部門で必要なQCD管理全てを備えた、現場特化型兼クラウド型の今世紀最高の購買管理システムとなります。
ユーザー登録
調達購買業務の効率化だけでなく、システムを導入することで、コスト削減や製品・資材のステータス可視化のほか、属人化していた購買情報の共有化による内部不正防止や統制にも役立ちます。
NEWJI DX
製造業に特化したデジタルトランスフォーメーション(DX)の実現を目指す請負開発型のコンサルティングサービスです。AI、iPaaS、および先端の技術を駆使して、製造プロセスの効率化、業務効率化、チームワーク強化、コスト削減、品質向上を実現します。このサービスは、製造業の課題を深く理解し、それに対する最適なデジタルソリューションを提供することで、企業が持続的な成長とイノベーションを達成できるようサポートします。
オンライン講座
製造業、主に購買・調達部門にお勤めの方々に向けた情報を配信しております。
新任の方やベテランの方、管理職を対象とした幅広いコンテンツをご用意しております。
お問い合わせ
コストダウンが利益に直結する術だと理解していても、なかなか前に進めることができない状況。そんな時は、newjiのコストダウン自動化機能で大きく利益貢献しよう!
(Β版非公開)