- お役立ち記事
- Latest trends in factory safety management and methods for risk reduction
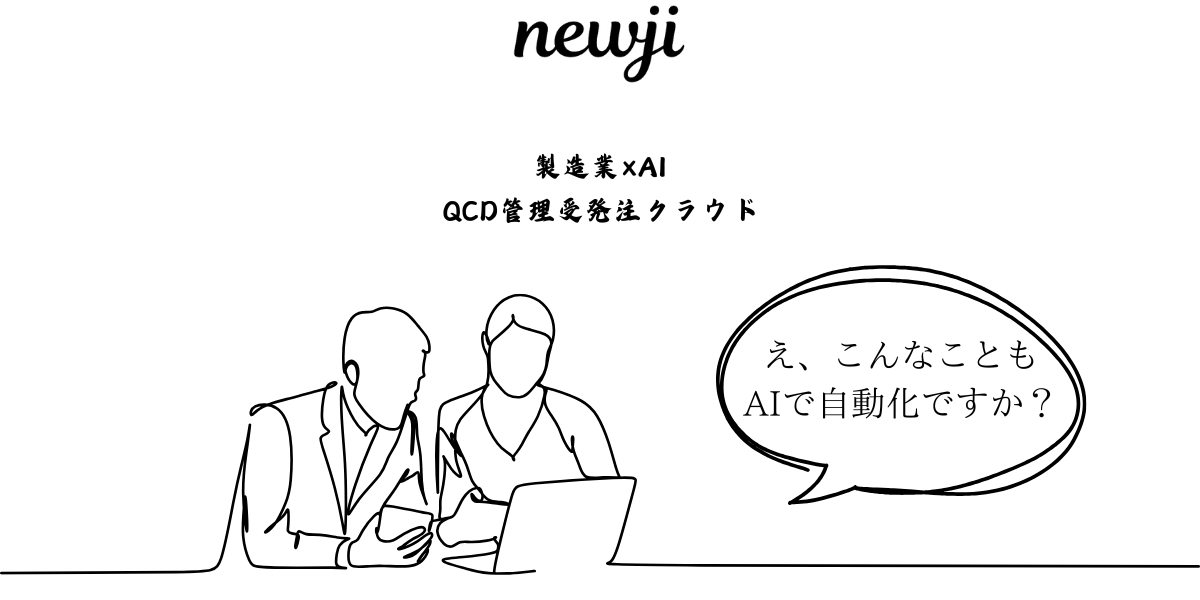
Latest trends in factory safety management and methods for risk reduction
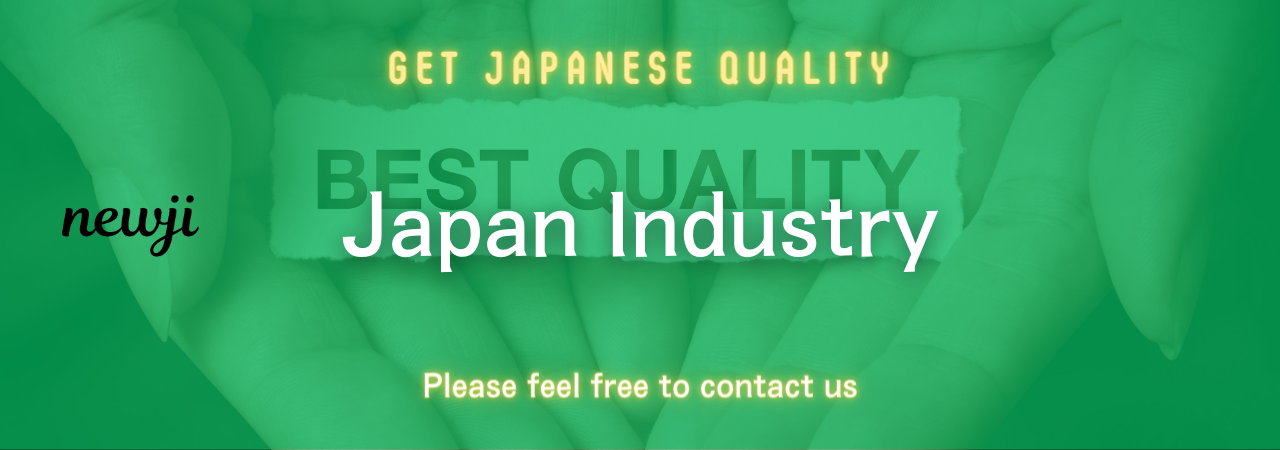
目次
Understanding Factory Safety Management
Factory safety management is a critical aspect of any industrial operation.
It ensures the protection of employees, machinery, and the environment from potential hazards that can arise from industrial processes.
In the ever-evolving landscape of industrial production, factory safety management has seen substantial advancements and changes.
Understanding these trends is crucial for businesses to maintain safety standards and minimize risks effectively.
The Importance of Safety Management
Safety management in factories is not just about compliance with legal regulations.
Its primary purpose is to safeguard human lives, protect assets, and enhance overall productivity.
Accidents and unsafe practices can result in downtime, legal penalties, and reputational damage.
Therefore, integrating safety management practices into daily operations is not an option but a necessity.
Latest Trends in Factory Safety Management
With the advancement of technology and changing industry standards, factory safety management is becoming more sophisticated.
Here are some of the latest trends that are shaping the future of industrial safety.
1. Technological Integration
Technological innovations are playing a crucial role in enhancing factory safety.
The integration of smart technologies, such as the Internet of Things (IoT), artificial intelligence (AI), and machine learning, are transforming how safety protocols are implemented.
These technologies help in real-time monitoring of equipment, predict potential hazards, and automate safety alerts.
For instance, IoT devices can track the operational status of machinery, predict maintenance needs, and alert operators to potential issues before they become critical.
2. Data-Driven Safety Decisions
Data analytics is another trend revolutionizing factory safety management.
Factories are now leveraging big data to make informed decisions about safety protocols.
By analyzing historical data and real-time information, managers can identify patterns and predict potential hazards.
This proactive approach allows factories to implement measures to prevent incidents before they occur, rather than simply reacting to them.
3. Safety Culture and Training
Establishing a strong safety culture is an emerging trend that places emphasis on the attitudes and behaviors of employees towards safety.
Training programs have become more interactive and engaging, utilizing virtual reality (VR) and augmented reality (AR) to simulate real-world scenarios.
This hands-on approach enhances the learning experience and prepares workers for potential emergency situations in a controlled environment.
4. Regulatory Compliance and Standards
Regulatory bodies across the globe are constantly updating safety standards to match the dynamic nature of industries.
Keeping abreast of these changes ensures factories remain compliant, avoiding legal repercussions and maintaining their operational license.
Adhering to updated regulations not only enhances factory safety but also demonstrates a company’s commitment to creating a safe working environment for its employees.
Methods for Risk Reduction
Reducing risk in a factory setting involves implementing a combination of strategies that focus on prevention, preparedness, and response.
Here are some effective methods for mitigating risks in the industrial environment.
1. Risk Assessment and Management
Conducting regular risk assessments is fundamental for identifying potential hazards in the workplace.
These assessments should involve evaluating processes, machinery, and the operational environment.
Once risks are identified, a management plan should be developed to either eliminate or minimize these risks.
This may involve implementing engineering controls, administrative controls, or personal protective equipment (PPE).
2. Continuous Training and Education
Training and education are vital components of a robust safety management system.
Continuous learning opportunities ensure that employees are aware of the latest safety practices and are equipped to handle potential hazards.
Regular workshops, seminars, and training sessions should be conducted to keep the workforce informed and prepared.
3. Emergency Preparedness Plans
Being prepared for emergencies can significantly reduce the impact of unexpected incidents.
Factories should have comprehensive emergency preparedness plans that include emergency response teams, evacuation procedures, and communication strategies.
Regular drills should be conducted to ensure that all employees are familiar with these plans and can act swiftly in case of an emergency.
4. Maintenance and Inspection
Regular maintenance and inspection of machinery and equipment are crucial for ensuring their safe operation.
A routine maintenance schedule should be established, and compliance with this schedule must be monitored.
Effective inspection protocols can detect potential mechanical failures and prevent accidents.
5. Enhanced Communication Systems
Communication is essential in maintaining safety within factories.
Implementing effective communication systems, including public address systems and instant messaging platforms, ensures that information is quickly disseminated to all employees.
Clear and precise communication can help prevent misunderstandings and ensure that all workers are aware of ongoing safety measures.
Conclusion
Factory safety management is a dynamic field that continuously adapts to new challenges and technological advancements.
By understanding and implementing the latest trends and methods for risk reduction, factories can create safer working environments for their employees.
Whether through technological integration, enhancing safety culture, or maintaining compliance with regulatory standards, the goal is always the same: to prevent accidents and protect the workforce.
By staying informed and proactive, businesses can minimize risks and ensure the safety and well-being of all their employees.
資料ダウンロード
QCD調達購買管理クラウド「newji」は、調達購買部門で必要なQCD管理全てを備えた、現場特化型兼クラウド型の今世紀最高の購買管理システムとなります。
ユーザー登録
調達購買業務の効率化だけでなく、システムを導入することで、コスト削減や製品・資材のステータス可視化のほか、属人化していた購買情報の共有化による内部不正防止や統制にも役立ちます。
NEWJI DX
製造業に特化したデジタルトランスフォーメーション(DX)の実現を目指す請負開発型のコンサルティングサービスです。AI、iPaaS、および先端の技術を駆使して、製造プロセスの効率化、業務効率化、チームワーク強化、コスト削減、品質向上を実現します。このサービスは、製造業の課題を深く理解し、それに対する最適なデジタルソリューションを提供することで、企業が持続的な成長とイノベーションを達成できるようサポートします。
オンライン講座
製造業、主に購買・調達部門にお勤めの方々に向けた情報を配信しております。
新任の方やベテランの方、管理職を対象とした幅広いコンテンツをご用意しております。
お問い合わせ
コストダウンが利益に直結する術だと理解していても、なかなか前に進めることができない状況。そんな時は、newjiのコストダウン自動化機能で大きく利益貢献しよう!
(Β版非公開)