- お役立ち記事
- Latest trends in IoT sensors used at manufacturing sites
Latest trends in IoT sensors used at manufacturing sites
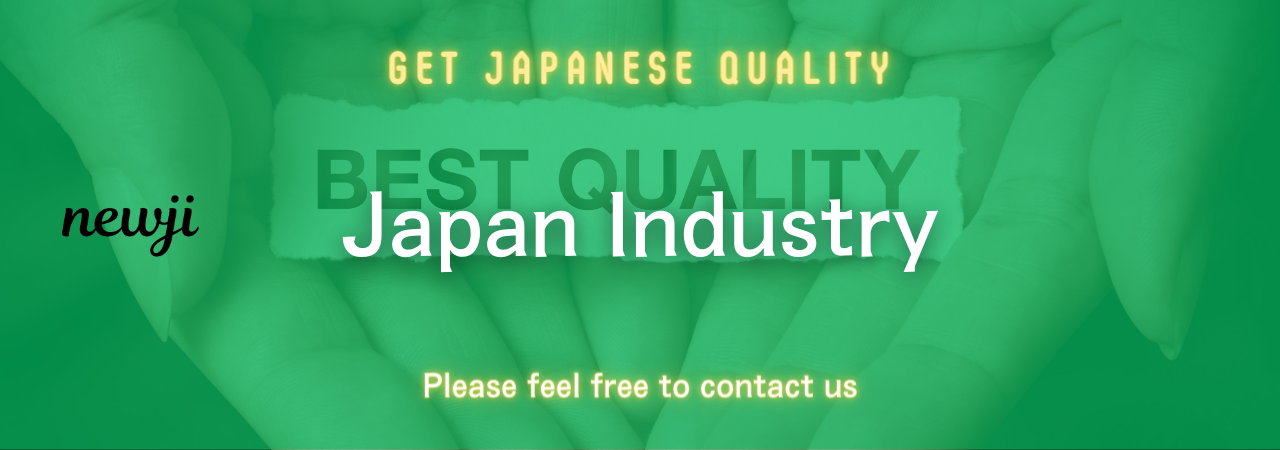
目次
Introduction to IoT Sensors
The world of technology is ever-evolving, and one of the most exciting innovations in recent years is the Internet of Things, or IoT.
This technology has revolutionized many industries, particularly manufacturing.
By using IoT sensors, manufacturers are now able to collect enormous amounts of data, leading to greater efficiency and productivity at their facilities.
Manufacturing sites have traditionally relied on human oversight and physical inspections to ensure operations run smoothly.
However, with the advent of IoT sensors, it has become possible to gather real-time data, enabling more proactive maintenance and management.
This leads to smoother operations and reduced downtime, enhancing overall productivity.
In this article, we will delve into the latest trends of IoT sensors used specifically in manufacturing and how these innovations contribute to the growth of this critical sector.
The Role of IoT Sensors in Manufacturing
IoT sensors in manufacturing have a wide range of applications that help streamline production processes, improve safety, and reduce costs.
These sensors collect real-time data that can be analyzed to optimize manufacturing activities.
Some of the primary roles these devices play include:
1. Predictive Maintenance
One of the main uses of IoT sensors is predictive maintenance.
Traditionally, manufacturers would conduct scheduled maintenance based on fixed intervals which sometimes led to unnecessary downtime or unexpected failures.
By using IoT sensors, manufacturers can monitor the health of machinery and infrastructure continuously.
These sensors provide data on vibration, temperature, and other critical parameters.
When these parameters deviate from the norm, the system sends alerts to the maintenance team, enabling them to address potential issues before they lead to equipment failure.
This approach not only reduces unplanned downtime but also extends the lifespan of machinery, thus saving costs.
2. Quality Control
Maintaining high-quality standards is paramount in manufacturing.
IoT sensors play a crucial role in quality control by monitoring various aspects of production processes such as temperature, humidity, and pressure.
By collecting data from different stages of the production line, manufacturers can ensure products meet specific standards before they reach the end consumer.
These sensors ensure that any anomalies in the production process are detected early, allowing corrective measures to be taken.
This results in a decrease in defective products and waste, thereby enhancing customer satisfaction and company reputation.
3. Inventory Management
Inventory management is a critical aspect of manufacturing, directly impacting production schedules and cost.
IoT sensors help track raw materials and products throughout the supply chain.
By offering real-time visibility into inventory levels, manufacturers can avoid overstocking or stockouts.
Automating inventory tracking not only improves efficiency but also facilitates better decision-making when it comes to procurement and distribution.
Recent Advancements in IoT Sensors for Manufacturing
Over the past few years, there have been numerous advancements in IoT sensor technology aimed at the manufacturing sector.
Here are some of the latest trends:
1. Enhanced Connectivity and Interoperability
Manufacturing facilities often comprise complex machinery from different vendors.
Ensuring these varied systems can communicate effectively is a crucial aspect of modern IoT sensor applications.
Recent advancements have improved sensor interoperability, enabling better integration with existing systems and networks.
Using standard communication protocols, these sensors can easily connect with cloud-based platforms and other IoT devices, leading to streamlined operations.
2. Artificial Intelligence and Machine Learning Integration
The integration of IoT sensors with artificial intelligence (AI) and machine learning (ML) algorithms is another notable trend.
AI and ML can analyze the vast amounts of data collected by IoT sensors at an unprecedented speed and accuracy.
This capability helps in recognizing patterns and predicting future outcomes.
For manufacturing, this means sensors can be an integral part of advanced analytical models that assist in decision-making, improving predictive maintenance, and optimizing production processes.
3. Low-Power and Energy-Efficient Sensors
IoT sensors are required to operate continuously, and their energy consumption is a considerable concern.
Manufacturers are increasingly adopting low-power and energy-efficient sensors to lower operational costs without compromising performance.
These sensors make use of energy-harvesting techniques or are equipped with long-lasting batteries, ensuring persistent and reliable operation.
The reduced power consumption also contributes to sustainability goals by minimizing the carbon footprint.
4. Edge Computing
Instead of sending all data collected to a central server for processing, modern IoT applications are embracing edge computing.
This involves processing data closer to where it’s generated, at the “edge” of the network.
Edge computing reduces latency, decreases bandwidth usage, and enhances data privacy.
It allows manufacturers to make quick decisions based on the data processed locally, which is particularly beneficial for time-sensitive applications such as real-time quality control.
Conclusion: The Future of IoT Sensors in Manufacturing
The use of IoT sensors in manufacturing is transforming the industry by improving efficiency, reducing costs, and enhancing product quality.
As technology continues to advance, we can expect these sensors to become even more intelligent and crucial in the manufacturing ecosystem.
While challenges remain, such as cybersecurity threats and the need for standardization, ongoing developments in IoT sensors, AI, and edge computing will likely prompt manufacturers to further embrace this transformative technology.
By staying ahead of these trends, manufacturers can ensure they remain competitive and capable of meeting the ever-evolving demands of the global market.
資料ダウンロード
QCD調達購買管理クラウド「newji」は、調達購買部門で必要なQCD管理全てを備えた、現場特化型兼クラウド型の今世紀最高の購買管理システムとなります。
ユーザー登録
調達購買業務の効率化だけでなく、システムを導入することで、コスト削減や製品・資材のステータス可視化のほか、属人化していた購買情報の共有化による内部不正防止や統制にも役立ちます。
NEWJI DX
製造業に特化したデジタルトランスフォーメーション(DX)の実現を目指す請負開発型のコンサルティングサービスです。AI、iPaaS、および先端の技術を駆使して、製造プロセスの効率化、業務効率化、チームワーク強化、コスト削減、品質向上を実現します。このサービスは、製造業の課題を深く理解し、それに対する最適なデジタルソリューションを提供することで、企業が持続的な成長とイノベーションを達成できるようサポートします。
オンライン講座
製造業、主に購買・調達部門にお勤めの方々に向けた情報を配信しております。
新任の方やベテランの方、管理職を対象とした幅広いコンテンツをご用意しております。
お問い合わせ
コストダウンが利益に直結する術だと理解していても、なかなか前に進めることができない状況。そんな時は、newjiのコストダウン自動化機能で大きく利益貢献しよう!
(Β版非公開)