- お役立ち記事
- Layout design and automation equipment design know-how for production line automation
Layout design and automation equipment design know-how for production line automation
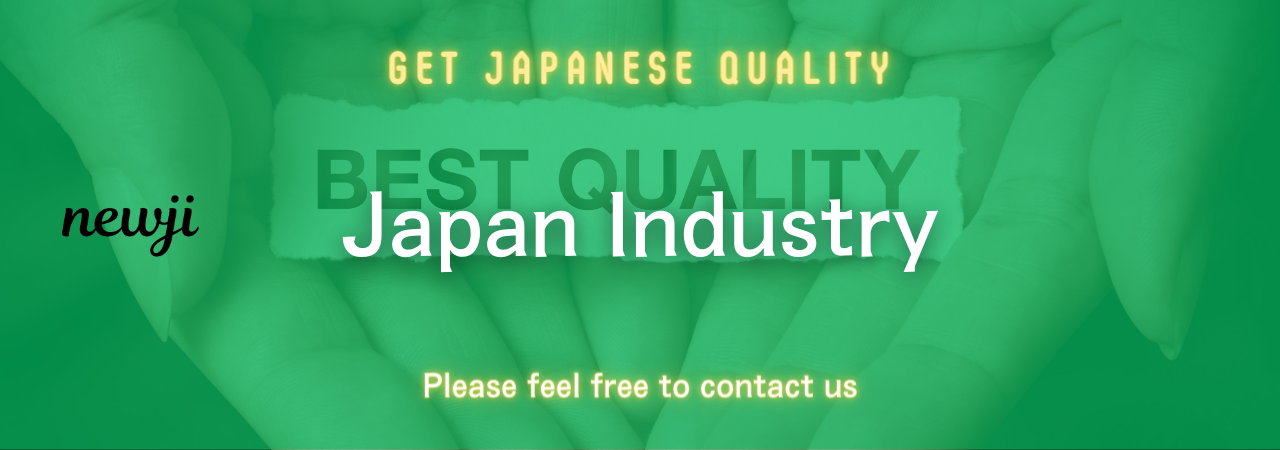
目次
Understanding Production Line Automation
Production line automation is a critical aspect of modern manufacturing that enhances efficiency, reduces costs, and improves quality.
By integrating advanced technologies and equipment into production lines, manufacturers streamline operations and maintain competitive advantages in their industries.
Understanding the basics of layout design and automation equipment is essential for optimizing these processes.
The Importance of Layout Design
Layout design is the blueprint for setting up a production line, determining how resources like machines, materials, and human labor are arranged.
A well-designed layout maximizes space utilization, minimizes material handling, and eliminates bottlenecks, ensuring smooth workflow and increased productivity.
There are several key factors to consider when planning the layout design of a production line:
1. **Process Flow**: Understanding the sequence of processes is essential.
An efficient layout should facilitate a logical flow of materials and products.
2. **Space Utilization**: Making effective use of available space is vital.
This includes arranging equipment to optimize space without compromising safety or accessibility.
3. **Flexibility**: Production demands can change, so it’s important to design a layout that can be easily adapted to meet these changes.
4. **Safety and Accessibility**: Ensuring that safety regulations are met, and that employees have easy access to all areas of the production line, is crucial.
Automation Equipment and Its Role
Automation equipment encompasses a broad range of machinery and technology designed to automate repetitive tasks in a production line.
The integration of automation equipment offers several benefits:
– **Increased Efficiency**: Automation reduces the time taken to complete repetitive tasks, allowing for higher production rates.
– **Consistency and Quality**: Machines can perform tasks with greater precision and consistency than human workers, leading to improved product quality.
– **Cost Reduction**: By reducing labor costs and minimizing waste, automation can significantly cut down on production expenses.
Types of Automation Equipment
Understanding the different types of automation equipment is crucial for selecting the right solutions for a production line.
Some popular types include:
1. **Robotics**: Used for tasks such as assembly, welding, and painting, robots enhance precision and can operate continuously without fatigue.
2. **Conveyors**: These systems move materials between different stages of production, reducing the need for manual labor and speeding up the production process.
3. **Automated Guided Vehicles (AGVs)**: These are used to transport materials and products within a factory, offering flexibility and efficiency.
4. **Computer Numerical Control (CNC) Machines**: CNC machines are used for precision manufacturing tasks like cutting and shaping materials.
They are highly accurate and reduce human error.
Implementing Automation in a Production Line
Successful implementation of automation in a production line requires careful planning and execution.
Here are the essential steps involved:
1. **Assessment and Planning**: Identify the areas of your production line that can benefit from automation.
Analyze the current workflow and pinpoint processes that can be automated for better efficiency.
2. **Selecting the Right Technology**: Based on the assessment, choose the appropriate automation equipment and technology that aligns with your production needs.
Consider flexibility, scalability, and compatibility with existing systems.
3. **Design and Development**: Design the layout to accommodate the new automation equipment and ensure it integrates seamlessly with current operations.
This might involve redesigning the workflow or upgrading existing infrastructure.
4. **Testing and Implementation**: Conduct thorough testing of automated systems to ensure they operate as expected.
Implement the systems in phases to minimize disruption to ongoing production.
5. **Training and Maintenance**: Train the workforce to operate and maintain the new automated systems.
Regular maintenance checks and upgrades are essential to keep equipment working efficiently.
Challenges in Production Line Automation
While automation offers numerous benefits, it also presents some challenges that manufacturers need to address:
1. **Initial Investment**: The cost of acquiring and installing automation equipment can be high.
However, the long-term savings and increased productivity often justify the investment.
2. **Complexity and Integration**: Integrating automation equipment with existing production systems and processes can be complex.
This challenge requires careful planning and expertise to ensure compatibility and smooth operation.
3. **Workforce Adaptation**: Automation impacts employment, requiring companies to manage changes in the workforce.
This might involve retraining employees or reallocating them to more value-added tasks.
The Future of Production Line Automation
The future of production line automation is promising, with continuous advancements in technology driving further innovation.
Emerging trends include:
– **Industry 4.0**: This concept integrates smart technology, data, and the Internet of Things (IoT) to create more interconnected and intelligent production systems.
– **Artificial Intelligence (AI)**: AI algorithms can optimize production schedules, predict maintenance needs, and improve quality control.
– **Sustainability**: Automation facilitates energy-efficient processes and reduces waste, contributing to more sustainable manufacturing.
In conclusion, mastering layout design and automation equipment design know-how is vital for the success of automated production lines.
By leveraging the power of automation, manufacturers can enhance productivity, reduce costs, and stay ahead in a competitive landscape.
As technology continues to evolve, embracing these advancements will be key to driving future success in manufacturing.
資料ダウンロード
QCD調達購買管理クラウド「newji」は、調達購買部門で必要なQCD管理全てを備えた、現場特化型兼クラウド型の今世紀最高の購買管理システムとなります。
ユーザー登録
調達購買業務の効率化だけでなく、システムを導入することで、コスト削減や製品・資材のステータス可視化のほか、属人化していた購買情報の共有化による内部不正防止や統制にも役立ちます。
NEWJI DX
製造業に特化したデジタルトランスフォーメーション(DX)の実現を目指す請負開発型のコンサルティングサービスです。AI、iPaaS、および先端の技術を駆使して、製造プロセスの効率化、業務効率化、チームワーク強化、コスト削減、品質向上を実現します。このサービスは、製造業の課題を深く理解し、それに対する最適なデジタルソリューションを提供することで、企業が持続的な成長とイノベーションを達成できるようサポートします。
オンライン講座
製造業、主に購買・調達部門にお勤めの方々に向けた情報を配信しております。
新任の方やベテランの方、管理職を対象とした幅広いコンテンツをご用意しております。
お問い合わせ
コストダウンが利益に直結する術だと理解していても、なかなか前に進めることができない状況。そんな時は、newjiのコストダウン自動化機能で大きく利益貢献しよう!
(Β版非公開)