- お役立ち記事
- Lead Time Reduction and Inventory Minimization Strategies
Lead Time Reduction and Inventory Minimization Strategies
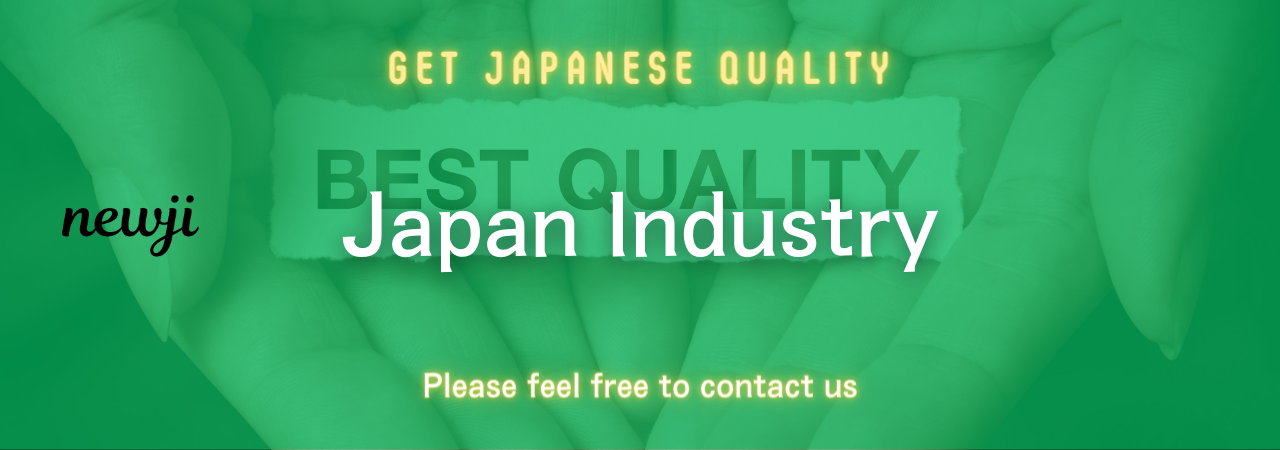
Businesses continually seek methods to streamline operations and enhance efficiency.
Two pivotal strategies that significantly impact a company’s performance are lead time reduction and inventory minimization.
Implementing these strategies effectively can lead to increased profitability and improved customer satisfaction.
目次
Understanding Lead Time Reduction
Lead time refers to the period it takes to process an order from initiation to completion.
Reducing lead time is crucial as it accelerates production, lessens waiting periods, and ultimately satisfies customer demands more swiftly.
Causes of Long Lead Times
Several factors can contribute to extended lead times:
– Inefficient production processes.
– Dependency on multiple suppliers for materials.
– Poorly managed supply chain logistics.
Understanding these causes is the first step toward implementing effective lead time reduction strategies.
Strategies to Reduce Lead Time
To tackle long lead times, businesses can adopt several tactics:
1. **Process Optimization:** Automating certain production tasks can create a smoother and faster workflow.
2. **Supplier Development:** Partnering with reliable suppliers who deliver quality materials promptly can shave off significant time.
3. **Inventory Management:** Maintaining an adequate inventory of frequently used materials ensures they are readily available when needed.
4. **Effective Communication:** Clear and consistent communication among all parties involved in the production process ensures everyone is aligned and aware of expectations.
Benefits of Lead Time Reduction
Reducing lead time offers numerous benefits:
– **Increased Customer Satisfaction:** Faster delivery times enhance the customer experience.
– **Lower Costs:** Efficient processes and less idle time can reduce operational costs.
– **Improved Cash Flow:** Quicker turnaround times mean faster payments, thereby improving the company’s cash flow.
Inventory Minimization
Managing inventory effectively is another critical aspect of business operations.
Excessive inventory ties up capital and incurs storage costs, whereas insufficient inventory can halt production and delay deliveries.
Causes of Excessive Inventory
Common reasons for overstocking include:
– Inaccurate demand forecasting.
– Inefficient purchasing processes.
– Lack of proper inventory management systems.
Identifying these causes helps businesses devise appropriate minimization strategies.
Strategies to Minimize Inventory
Several strategies can aid in minimizing inventory effectively:
1. **Accurate Demand Forecasting:** Utilizing historical data and market trends to predict future demand accurately can prevent overstocking.
2. **Just-In-Time (JIT) Inventory:** This strategy involves receiving goods only as they are needed in the production process, reducing storage costs and waste.
3. **Vendor-Managed Inventory (VMI):** Allowing suppliers to manage inventory levels can ensure that stock levels remain optimal without excessive intervention.
4. **Regular Audits:** Conducting frequent inventory audits can help identify discrepancies and adjust stock levels accordingly.
Benefits of Inventory Minimization
Effective inventory minimization yields several advantages:
– **Reduced Storage Costs:** Less inventory means lower costs for warehousing and storage.
– **Better Cash Flow:** Less money is tied up in inventory, freeing up capital for other investments.
– **Enhanced Flexibility:** With leaner inventory, businesses can adapt more quickly to changes in demand and market conditions.
Combining Both Strategies
While lead time reduction and inventory minimization are beneficial individually, combining these strategies can multiply their efficacy.
Streamlined Operations
Integrating lead time reduction with inventory minimization streamlines operations, ensuring that products are produced and delivered swiftly without overstocking.
Technology Integration
Using technology to synchronize these strategies can lead to significant improvements.
For instance, adopting an advanced inventory management system can provide real-time data on stock levels and lead times, helping in decision-making.
Continuous Improvement
Continuous monitoring and improvement of these processes ensure that the strategies adapt to any changes in the business environment.
Regularly revisiting and refining these strategies helps to maintain their relevance and effectiveness.
Case Study: Successful Implementation
To illustrate the effectiveness of these strategies, consider a company that successfully implemented lead time reduction and inventory minimization.
By automating their production line and partnering with reliable suppliers, they reduced lead time by 30%.
Additionally, adopting a JIT inventory system helped them cut down on excess stock by 20%.
As a result, they experienced a 15% increase in customer satisfaction and a 10% reduction in operational costs.
Conclusion
Lead time reduction and inventory minimization are crucial strategies for any business aiming to enhance efficiency and profitability.
By understanding the causes of long lead times and excessive inventory, and implementing the right strategies, companies can achieve a faster operational pace and lower costs.
Combining both strategies and leveraging technology for continuous improvement ensures long-term success.
Achieving these goals doesn’t just benefit the business but also leads to improved customer satisfaction and better market competitiveness.
資料ダウンロード
QCD調達購買管理クラウド「newji」は、調達購買部門で必要なQCD管理全てを備えた、現場特化型兼クラウド型の今世紀最高の購買管理システムとなります。
ユーザー登録
調達購買業務の効率化だけでなく、システムを導入することで、コスト削減や製品・資材のステータス可視化のほか、属人化していた購買情報の共有化による内部不正防止や統制にも役立ちます。
NEWJI DX
製造業に特化したデジタルトランスフォーメーション(DX)の実現を目指す請負開発型のコンサルティングサービスです。AI、iPaaS、および先端の技術を駆使して、製造プロセスの効率化、業務効率化、チームワーク強化、コスト削減、品質向上を実現します。このサービスは、製造業の課題を深く理解し、それに対する最適なデジタルソリューションを提供することで、企業が持続的な成長とイノベーションを達成できるようサポートします。
オンライン講座
製造業、主に購買・調達部門にお勤めの方々に向けた情報を配信しております。
新任の方やベテランの方、管理職を対象とした幅広いコンテンツをご用意しております。
お問い合わせ
コストダウンが利益に直結する術だと理解していても、なかなか前に進めることができない状況。そんな時は、newjiのコストダウン自動化機能で大きく利益貢献しよう!
(Β版非公開)