- お役立ち記事
- Lead time shortening methods and improvement measures to prevent delivery delays
月間77,185名の
製造業ご担当者様が閲覧しています*
*2025年2月28日現在のGoogle Analyticsのデータより
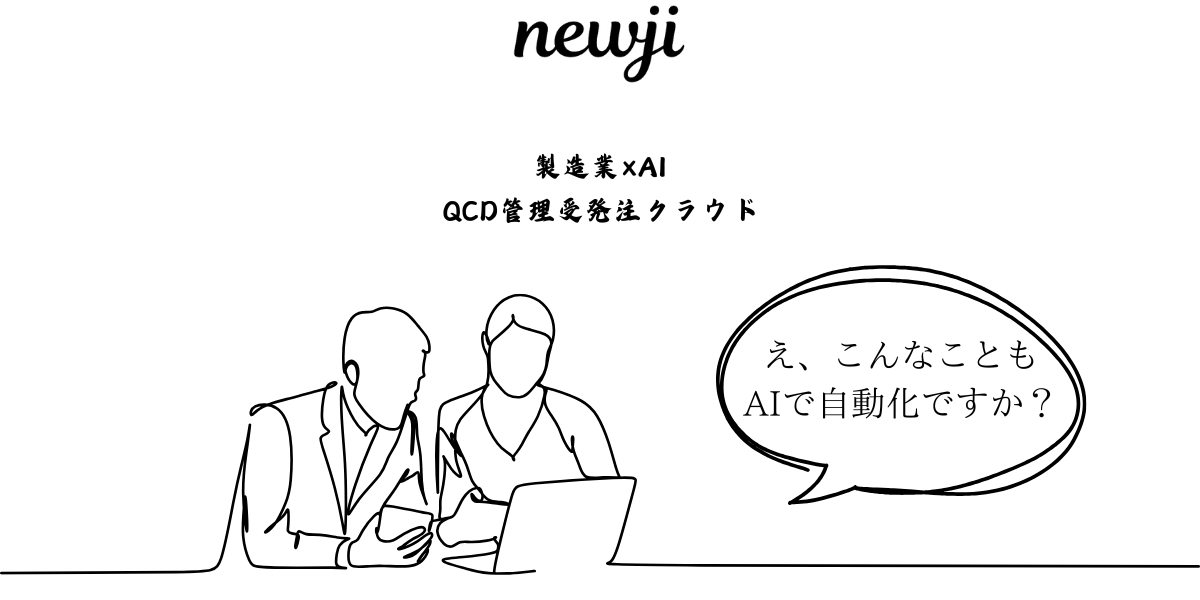
Lead time shortening methods and improvement measures to prevent delivery delays
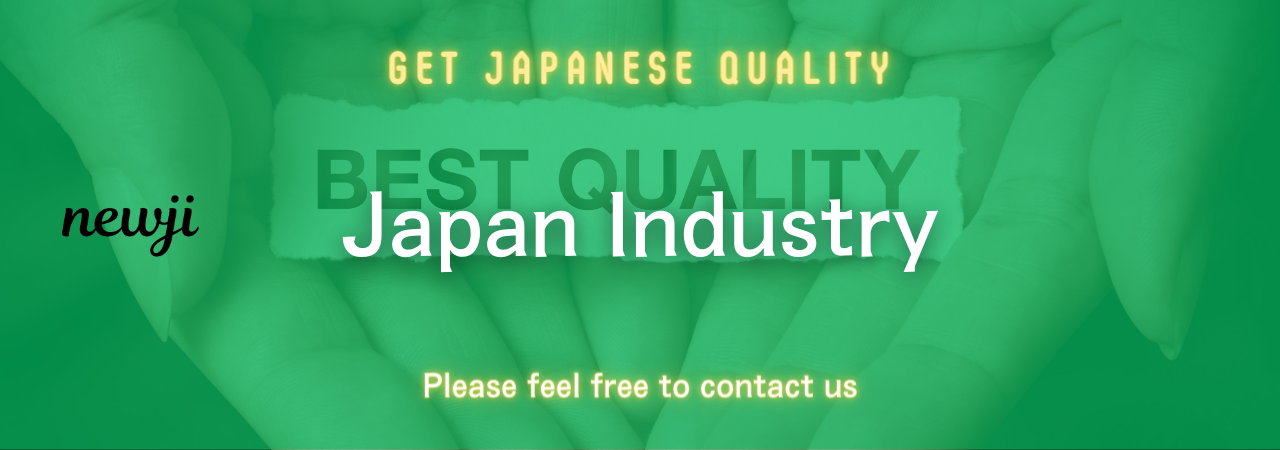
目次
Introduction to Lead Time and Delivery Delays
Lead time refers to the total time from when an order is placed until the product or service is delivered to the customer.
It’s a crucial metric impacting overall customer satisfaction and business efficiency.
Delivery delays can cause customer dissatisfaction, lead to canceled orders, and tarnish a company’s reputation.
To prevent such issues, businesses are constantly seeking ways to shorten lead times and improve their processes.
Understanding the Causes of Delivery Delays
Before implementing measures to reduce lead time, it’s important to understand the common causes of delivery delays.
These can include inadequate inventory management, supplier issues, inefficient production processes, and unpredictable demand.
External factors such as weather, transportation strikes, or customs clearance complications can also play a role.
By identifying specific bottlenecks and challenges within these areas, businesses can develop strategic solutions to address them.
Methods for Shortening Lead Time
1. Streamline Supply Chain Management
Optimizing the supply chain is one of the most effective methods for reducing lead time.
This involves improving coordination among suppliers, manufacturers, and distribution centers.
Using technology such as supply chain management software can enhance visibility and traceability, helping to anticipate and mitigate delays.
2. Implement Just-In-Time Inventory
Just-in-time (JIT) inventory management is about producing or purchasing goods only as they are needed in the production process.
This method significantly reduces the time goods are stored in warehouses, limiting excess inventory and freeing up capital.
However, it requires precise planning and reliable supplier relationships to ensure timely delivery.
3. Optimize Production Processes
Reviewing and improving production processes can also contribute to shorter lead times.
Analyzing each step of production to eliminate inefficiencies, such as unnecessary movements or waiting times, can lead to significant improvements.
Automation and technology can increase production speed and reduce errors, contributing to a more efficient process.
4. Enhance Communication and Collaboration
Effective communication across all levels of the supply chain is essential.
Regular meetings and updates with suppliers and partners can help to foresee potential delays and synchronize efforts.
Encouraging collaboration fosters a proactive rather than reactive approach to problem-solving.
Implementing Improvement Measures
1. Invest in Technology
Adopting advanced technology solutions like enterprise resource planning (ERP) systems can greatly improve lead time by integrating all business processes.
These systems provide real-time data and analytics to support better decision-making and anticipate future demand.
2. Establish Reliable Relationships with Suppliers
Building strong relationships with reliable suppliers is paramount.
Establishing clear terms for lead times, quality expectations, and repercussions for delays ensures accountability.
Consider diversifying suppliers to avoid dependency on a single source, which can mitigate risks associated with supplier-related delays.
3. Train and Empower Employees
Employees play a critical role in lead time management.
Comprehensive training programs ensure that staff are knowledgeable about the processes and understand the importance of meeting deadlines.
Empowering them to make quick decisions and adapt to changes can also lead to more efficient operations.
4. Monitor and Evaluate Performance
Regularly monitoring and evaluating lead time performance allows businesses to identify areas for improvement.
Key performance indicators (KPIs) specific to lead time should be established and tracked regularly.
Using data-driven insights to make informed decisions can enhance overall efficiency.
Conclusion
In today’s competitive market, reducing lead time and preventing delivery delays are essential for maintaining customer satisfaction and a strong market position.
By understanding the underlying causes of delays and implementing effective strategies to address them, businesses can significantly improve their operations.
Streamlining the supply chain, optimizing production processes, investing in technology, and fostering strong supplier relationships are key steps to achieving this goal.
Through continuous improvement and adaptation to changing circumstances, businesses can ensure timely delivery and enhance their overall competitiveness.
資料ダウンロード
QCD管理受発注クラウド「newji」は、受発注部門で必要なQCD管理全てを備えた、現場特化型兼クラウド型の今世紀最高の受発注管理システムとなります。
ユーザー登録
受発注業務の効率化だけでなく、システムを導入することで、コスト削減や製品・資材のステータス可視化のほか、属人化していた受発注情報の共有化による内部不正防止や統制にも役立ちます。
NEWJI DX
製造業に特化したデジタルトランスフォーメーション(DX)の実現を目指す請負開発型のコンサルティングサービスです。AI、iPaaS、および先端の技術を駆使して、製造プロセスの効率化、業務効率化、チームワーク強化、コスト削減、品質向上を実現します。このサービスは、製造業の課題を深く理解し、それに対する最適なデジタルソリューションを提供することで、企業が持続的な成長とイノベーションを達成できるようサポートします。
製造業ニュース解説
製造業、主に購買・調達部門にお勤めの方々に向けた情報を配信しております。
新任の方やベテランの方、管理職を対象とした幅広いコンテンツをご用意しております。
お問い合わせ
コストダウンが利益に直結する術だと理解していても、なかなか前に進めることができない状況。そんな時は、newjiのコストダウン自動化機能で大きく利益貢献しよう!
(β版非公開)