- お役立ち記事
- LEAN production method and its success stories that production technology leaders should know
LEAN production method and its success stories that production technology leaders should know
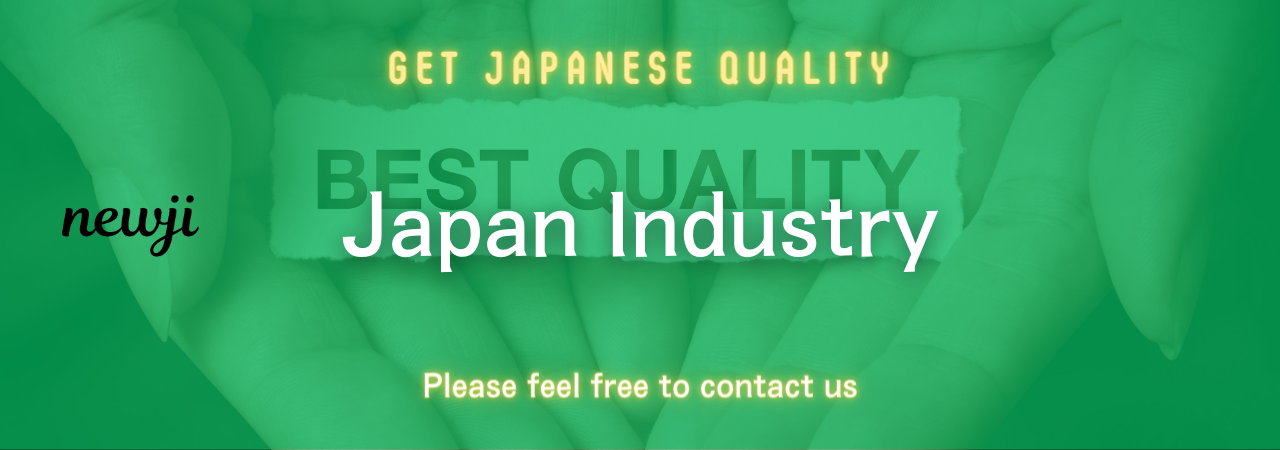
目次
Understanding LEAN Production
The LEAN production method is a systematic approach to minimizing waste within a manufacturing system without sacrificing productivity.
This model focuses on various types of waste, including overproduction, waiting times, unnecessary movement, over-processing, excess inventory, defects, and underutilized talent.
The goal of LEAN production is to create more value for customers with fewer resources.
LEAN production originated from the Toyota Production System, which became widely recognized in the 20th century.
Toyota had set the benchmark for efficient production processes, emphasizing waste reduction and continuous improvement.
The methodology has gained widespread adoption globally, across various industries, and is credited with enhancing productivity and profitability.
Key Principles of LEAN Production
1. Value
Value refers to anything that a customer is willing to pay for.
Identifying what constitutes value from the customer’s perspective is the first step in the LEAN process.
This enables organizations to focus their efforts on activities that genuinely add value.
2. Value Stream
The value stream is a series of steps that an organization takes to bring a product or service from conception to delivery.
By mapping the value stream, businesses can identify waste and areas for improvement.
The goal is to ensure each step adds value to the final product.
3. Flow
Once the non-value-added waste is removed from the value stream, products should move smoothly through the remaining processes.
Creating flow ensures no bottlenecks or interruptions, which can slow down production and increase costs.
4. Pull
The pull principle operates on demand-driven production, meaning products are made only when required by the customer.
This avoids overproduction and reduces inventory costs.
The pull approach requires flexibility and responsiveness to customer demands.
5. Perfection
LEAN production is built on a culture of continuous improvement, often termed “kaizen” in Japanese.
The pursuit of perfection is a journey that involves regularly seeking and eliminating root causes of issues, refining processes, and enhancing skills.
Success Stories of LEAN Production
Toyota – A LEAN Pioneer
Toyota remains a hallmark of LEAN production excellence.
By embedding the LEAN philosophy into their corporate culture, Toyota has created a robust manufacturing process that is flexible and efficient.
One of their most famous implementations is the Just-In-Time (JIT) system, which minimizes inventory levels and increases efficiency.
Toyota’s relentless pursuit of perfection has enabled the company to reduce costs, improve product quality, and increase customer satisfaction.
Their commitment to LEAN principles has led to better profitability and a strong competitive position in the automotive industry.
Ford – Revitalizing with LEAN
Ford Motor Company is another success story of LEAN production methods.
In the early 2000s, Ford experienced significant financial struggles and turned to LEAN practices to revitalize their manufacturing processes.
By embracing LEAN principles, Ford was able to streamline operations, cut costs, and improve its production systems.
The company’s “Ford Production System” emphasized value stream mapping, continuous flow, and employee empowerment, which resulted in reduced assembly time and improved product quality.
Boeing – Taking Flight with LEAN
The aerospace giant Boeing has also benefited from implementing LEAN methodologies.
Faced with the challenge of complex manufacturing processes and high production costs, Boeing adopted LEAN principles to enhance efficiency.
By executing LEAN strategies, Boeing reduced lead times and costs significantly.
They implemented coordinated workflows, minimized waste, and cultivated a culture of continuous improvement.
The adoption of LEAN production enabled Boeing to deliver aircraft more efficiently and maintain high-quality standards.
LEGO – Building Success with LEAN
The LEGO Group, renowned for their plastic toy bricks, also applied LEAN principles to transform their production operations.
In the early 2000s, LEGO faced financial difficulties due to inefficient production and supply chain processes.
To address these challenges, LEGO embarked on a LEAN journey.
The company focused on improving flow across their entire supply chain, reducing overheads, and eliminating inefficient steps.
This not only led to improved profitability but also enhanced LEGO’s ability to meet customer demand effectively.
Challenges and Considerations
While the benefits of LEAN production methods are significant, organizations must also be prepared for challenges.
Adopting a LEAN mindset requires a shift in organizational culture and employee attitudes.
It involves continuous training, communication, and alignment of goals.
Additionally, businesses must customize LEAN principles to suit their specific context.
Blindly applying LEAN strategies without proper analysis can lead to unintended consequences, such as reduced employee engagement or declining product quality.
A thoughtful approach ensures the LEAN methodology complements and enhances existing business processes.
Conclusion
The LEAN production method highlights a transformative approach for organizations seeking to improve efficiency, reduce costs, and enhance product quality.
With its focus on continuous improvement and waste reduction, LEAN has proven successful across various sectors.
Success stories from industry giants, such as Toyota, Ford, Boeing, and LEGO, demonstrate how LEAN principles can revolutionize production systems.
Production technology leaders can draw inspiration from these cases, adapting practices that align with their organization’s unique challenges and opportunities.
Implementing LEAN production methods requires commitment, collaboration, and adaptability.
As organizations embrace these principles, they create pathways for sustainable growth and a stronger competitive edge in today’s dynamic market landscape.
資料ダウンロード
QCD調達購買管理クラウド「newji」は、調達購買部門で必要なQCD管理全てを備えた、現場特化型兼クラウド型の今世紀最高の購買管理システムとなります。
ユーザー登録
調達購買業務の効率化だけでなく、システムを導入することで、コスト削減や製品・資材のステータス可視化のほか、属人化していた購買情報の共有化による内部不正防止や統制にも役立ちます。
NEWJI DX
製造業に特化したデジタルトランスフォーメーション(DX)の実現を目指す請負開発型のコンサルティングサービスです。AI、iPaaS、および先端の技術を駆使して、製造プロセスの効率化、業務効率化、チームワーク強化、コスト削減、品質向上を実現します。このサービスは、製造業の課題を深く理解し、それに対する最適なデジタルソリューションを提供することで、企業が持続的な成長とイノベーションを達成できるようサポートします。
オンライン講座
製造業、主に購買・調達部門にお勤めの方々に向けた情報を配信しております。
新任の方やベテランの方、管理職を対象とした幅広いコンテンツをご用意しております。
お問い合わせ
コストダウンが利益に直結する術だと理解していても、なかなか前に進めることができない状況。そんな時は、newjiのコストダウン自動化機能で大きく利益貢献しよう!
(Β版非公開)