- お役立ち記事
- LEAN production method that managers of production operations departments should work on and its implementation effects
月間76,176名の
製造業ご担当者様が閲覧しています*
*2025年3月31日現在のGoogle Analyticsのデータより
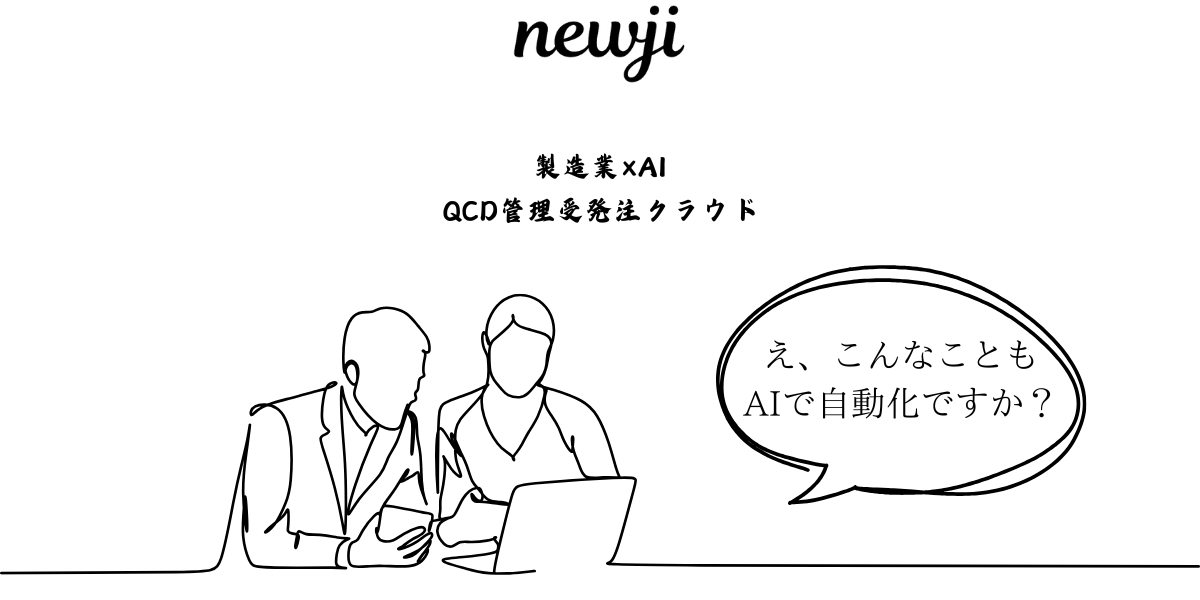
LEAN production method that managers of production operations departments should work on and its implementation effects
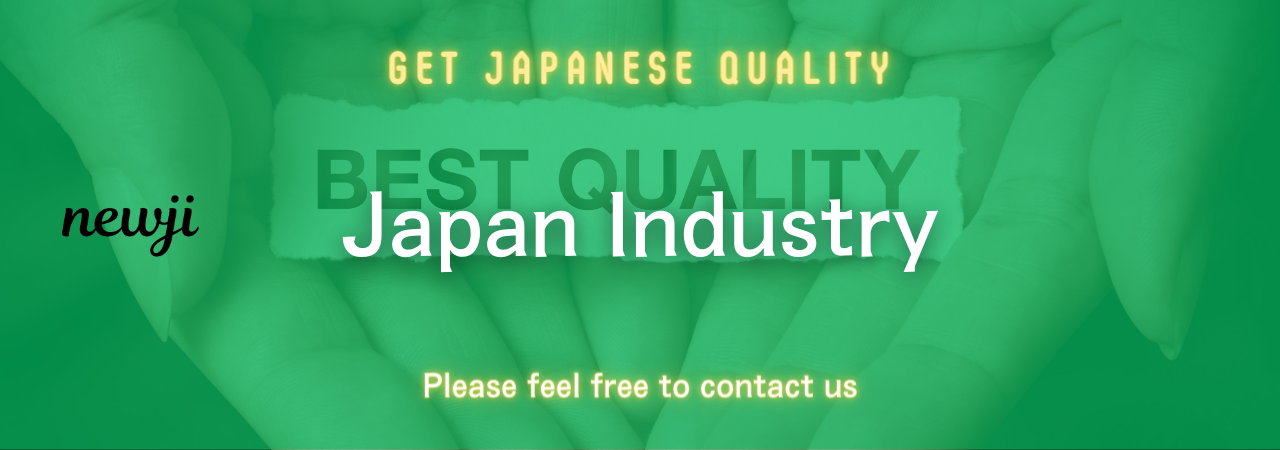
目次
Understanding the LEAN Production Method
The LEAN production method is a systematic approach used to streamline processes and eliminate waste, aiming to enhance productivity and quality in manufacturing and other sectors.
It’s a philosophy that originated in the manufacturing systems of Japan, particularly within the Toyota Production System, and it has since spread across various industries worldwide.
The core idea of LEAN production is to maximize value for the customer while minimizing resources, thereby creating a more efficient operation.
By focusing on reducing costs, improving quality, and speeding up delivery times, companies can gain a competitive edge.
The Five Principles of LEAN Production
Understanding the five guiding principles of LEAN production will help managers in production operations to effectively implement this method.
1. **Value**: Identify what customers actually value and are willing to pay for within a product or service.
This requires a deep understanding of customer needs and preferences.
2. **Value Stream**: Map out all the steps and processes involved in taking a product from raw materials to delivery to the customer.
The goal is to identify and eliminate any steps that do not add value.
3. **Flow**: Ensure that the production process flows smoothly without interruptions, bottlenecks, or delays.
This involves reorganizing production activities and resources in a way that maximizes efficiency.
4. **Pull**: Instead of forecasting and pushing production, adopt a pull system where production is based on actual demand.
This leads to lower inventory levels and reduces waste.
5. **Perfection**: A culture of continuous improvement should permeate the organization, with a focus on striving for perfection in all processes.
This involves constantly seeking ways to improve and innovate.
Key Benefits of Implementing LEAN Production
The implementation of LEAN production in an organization can result in several significant benefits:
1. **Reduced Waste**: By eliminating non-value-adding activities, companies can significantly reduce waste in their operations.
This not only applies to physical waste like excess materials but also time and labor.
2. **Improved Quality**: With a focus on continuous improvement and error reduction, the quality of products typically improves.
Faults and defects are minimized, leading to higher customer satisfaction.
3. **Increased Efficiency**: Streamlined processes mean faster production times and improved operational efficiency.
This can result in shorter lead times and quicker responses to market demands.
4. **Enhanced Customer Satisfaction**: LEAN practices focus on delivering what the customer wants most efficiently.
Improved quality, on-time delivery, and customization options directly enhance customer satisfaction and loyalty.
5. **Cost Savings**: By reducing waste and improving efficiency, companies can cut down on production costs.
These savings can be reinvested in other areas of the business to further drive growth and innovation.
Steps for Implementing LEAN Production
To successfully implement LEAN production, organizations should follow a structured approach:
1. **Define the Value from the Customer’s Perspective**: Gather insights directly from the customer to understand what they value most.
This will guide the optimization of processes and resources.
2. **Map the Value Stream**: Conduct a thorough examination of the entire production process to identify which steps add value and which do not.
This will highlight areas for improvement.
3. **Create Continuous Flow**: Work on reorganizing the workflow to eliminate interruptions and bottlenecks.
This involves aligning resources and processes to facilitate smooth transitions between production phases.
4. **Establish a Pull System**: Transition from pushing products through the system to pulling them based on customer demand.
Implement inventory controls and scheduling systems that align production with real-time customer needs.
5. **Pursue Perfection**: Encourage a culture of continuous improvement by setting clear goals and providing training.
Involve employees at all levels in problem-solving and innovation initiatives.
Challenges and Considerations
While the benefits of LEAN production are substantial, organizations may face several challenges in implementation:
1. **Resistance to Change**: Employees and management may resist changes due to uncertainty or comfort with current processes.
Clear communication, training, and involvement in the change process can help overcome this resistance.
2. **Resource Investment**: Initial implementation may require investment in terms of time, training, and resources.
However, these upfront costs are often offset by long-term gains.
3. **Maintaining Consistency**: Ensuring continuous improvement and maintaining LEAN principles over time can be challenging.
Regular reviews and updates to processes and strategies are essential.
4. **Complexity of Implementation**: Depending on the size and scope of the organization, implementing LEAN can be complex and time-consuming.
Breaking down the process into manageable steps and securing executive support can aid in navigating these complexities.
Conclusion
For managers in production operations, adopting the LEAN production method offers a robust framework for reducing waste, improving efficiency, and enhancing customer satisfaction.
By understanding the principles and benefits of LEAN, organizations can drive significant improvements in their operations.
Although challenges exist, with careful planning and commitment, the LEAN production method can lead to transformative results, ultimately contributing to the success and competitiveness of the business.
資料ダウンロード
QCD管理受発注クラウド「newji」は、受発注部門で必要なQCD管理全てを備えた、現場特化型兼クラウド型の今世紀最高の受発注管理システムとなります。
ユーザー登録
受発注業務の効率化だけでなく、システムを導入することで、コスト削減や製品・資材のステータス可視化のほか、属人化していた受発注情報の共有化による内部不正防止や統制にも役立ちます。
NEWJI DX
製造業に特化したデジタルトランスフォーメーション(DX)の実現を目指す請負開発型のコンサルティングサービスです。AI、iPaaS、および先端の技術を駆使して、製造プロセスの効率化、業務効率化、チームワーク強化、コスト削減、品質向上を実現します。このサービスは、製造業の課題を深く理解し、それに対する最適なデジタルソリューションを提供することで、企業が持続的な成長とイノベーションを達成できるようサポートします。
製造業ニュース解説
製造業、主に購買・調達部門にお勤めの方々に向けた情報を配信しております。
新任の方やベテランの方、管理職を対象とした幅広いコンテンツをご用意しております。
お問い合わせ
コストダウンが利益に直結する術だと理解していても、なかなか前に進めることができない状況。そんな時は、newjiのコストダウン自動化機能で大きく利益貢献しよう!
(β版非公開)