- お役立ち記事
- Leaning into Efficiency: How Japanese Manufacturing Masters the Art of Just-In-Time Production
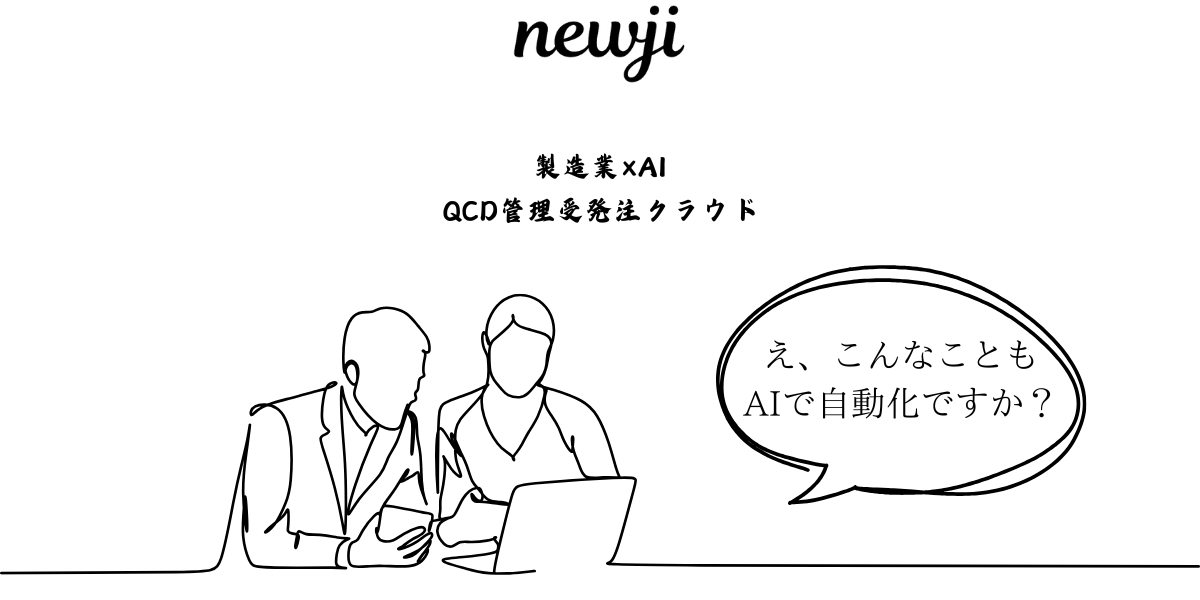
Leaning into Efficiency: How Japanese Manufacturing Masters the Art of Just-In-Time Production
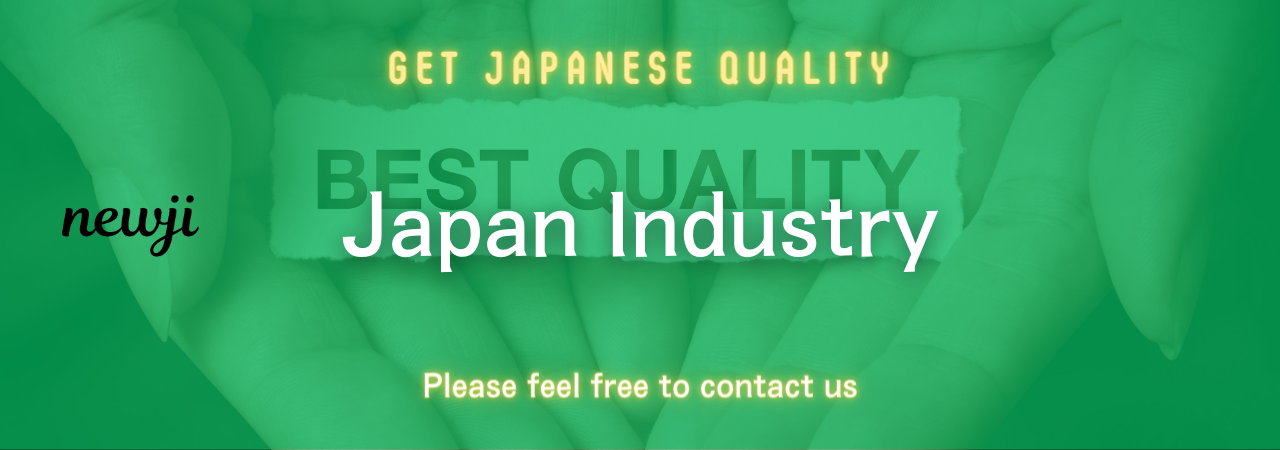
目次
Introduction
Just-In-Time (JIT) production is a cornerstone of modern manufacturing efficiency.
Originating in Japanese manufacturing, JIT has transformed how companies manage their production processes.
This article explores the mastery of JIT by Japanese manufacturers and how its principles can be applied globally.
Understanding JIT is essential for businesses aiming to enhance their procurement and purchasing strategies.
By delving into the advantages, challenges, and best practices, this article provides a comprehensive guide to mastering JIT.
The Evolution of Just-In-Time Production
Origins in Japanese Manufacturing
JIT production was pioneered by Japanese manufacturers, notably Toyota, in the post-World War II era.
Facing resource constraints, Toyota developed JIT to optimize production processes and eliminate waste.
The philosophy was deeply rooted in the principles of efficiency and continuous improvement.
JIT allowed Japanese companies to produce high-quality products with minimal inventory.
Adoption and Adaptation Globally
The success of JIT in Japan led to its global adoption across various industries.
Manufacturers worldwide recognized the benefits of reduced inventory costs and increased responsiveness.
However, the implementation of JIT required significant changes in supply chain management and organizational culture.
Global adaptation of JIT has been shaped by regional market conditions and technological advancements.
Key Principles of JIT
Elimination of Waste
At the core of JIT is the elimination of waste in all forms, including excess inventory, overproduction, and defects.
By identifying and removing non-value-added activities, companies streamline their operations.
This focus on waste reduction leads to cost savings and increased efficiency.
JIT encourages a culture of continuous assessment to maintain minimal waste levels.
Continuous Improvement (Kaizen)
Kaizen, or continuous improvement, is a fundamental principle in JIT.
It involves the ongoing effort to enhance processes, products, and services.
Employees at all levels are encouraged to suggest improvements, fostering a collaborative environment.
This relentless pursuit of excellence ensures that production processes remain optimized and responsive to change.
Respect for People
JIT emphasizes the importance of respecting employees, suppliers, and customers.
Empowering workers to take ownership of their tasks leads to higher motivation and better performance.
Strong, cooperative relationships with suppliers ensure timely delivery of quality materials.
Customer feedback is integral to refining products and services, aligning production with market demands.
Benefits of Just-In-Time Production
Increased Efficiency
JIT enhances efficiency by synchronizing production schedules with demand.
This alignment reduces idle time and maximizes resource utilization.
Efficient processes lead to faster production cycles and shorter lead times.
Overall, JIT contributes to a more agile and responsive manufacturing system.
Cost Reduction
By minimizing inventory levels, JIT reduces storage and holding costs.
Lower inventory also decreases the risk of obsolescence and waste.
Streamlined processes lead to lower operational costs and improved profitability.
Cost savings can be redirected towards innovation and quality improvement.
Enhanced Quality
JIT promotes high-quality standards by integrating quality control into every stage of production.
Defects are identified and addressed immediately, preventing the accumulation of faulty products.
Continuous improvement initiatives ensure that quality remains a priority.
Higher quality products enhance customer satisfaction and brand reputation.
Improved Supply Chain Management
JIT necessitates robust supply chain coordination and transparency.
Close collaboration with suppliers ensures timely delivery of materials and components.
Effective communication channels reduce delays and enhance supply chain resilience.
A well-managed supply chain supports the seamless flow of production and meets customer expectations.
Challenges and Limitations
Supply Chain Disruptions
JIT relies on the stable and timely delivery of materials.
Any disruption in the supply chain, such as natural disasters or geopolitical issues, can halt production.
Mitigating these risks requires contingency planning and diversified supplier networks.
Companies must remain vigilant and adaptable to unforeseen challenges.
High Dependence on Suppliers
JIT places significant trust in suppliers to deliver quality materials on time.
This dependence necessitates strong relationships and clear communication with suppliers.
Managing supplier performance is critical to maintaining the integrity of JIT systems.
Failures by suppliers can have cascading effects on the entire production process.
Implementation Costs
Transitioning to a JIT system involves upfront costs, including training, technology investments, and process reengineering.
Small and medium-sized enterprises may find these investments challenging.
However, the long-term benefits of JIT often outweigh the initial expenditures.
Careful planning and phased implementation can help manage these costs effectively.
JIT and International Procurement
Supplier Relationships
Successful JIT implementation requires building strong, collaborative relationships with international suppliers.
Trust and mutual respect are essential for effective collaboration.
Regular communication and shared goals ensure that suppliers understand and commit to JIT principles.
Long-term partnerships foster reliability and consistency in supply.
Negotiation Techniques
Negotiating with international suppliers for JIT involves balancing cost, quality, and reliability.
Clear articulation of expectations and requirements is essential.
Employing win-win negotiation strategies helps in building sustainable supplier relationships.
Flexibility and cultural sensitivity enhance negotiation outcomes and foster cooperation.
Market Conditions
Understanding global market dynamics is crucial for JIT procurement strategies.
Economic fluctuations, trade policies, and currency exchange rates impact supplier performance and costs.
Staying informed about market trends enables proactive adjustments to procurement plans.
Adaptive strategies ensure resilience and competitiveness in fluctuating markets.
Best Practices in Implementing JIT
Collaborative Planning
Effective JIT implementation relies on collaborative planning across the supply chain.
Joint forecasting and shared production schedules align supplier capabilities with production needs.
Collaborative planning reduces uncertainty and improves demand forecasting accuracy.
Integrated planning processes enhance the overall effectiveness of JIT systems.
Training and Development
Investing in training and development equips employees with the skills needed for JIT.
Continuous education fosters a culture of improvement and adaptability.
Empowered employees can identify and solve issues proactively, maintaining JIT standards.
Ongoing training ensures that the workforce remains competent and motivated.
Technology Integration
Advanced technologies support the seamless operation of JIT systems.
Inventory management software, real-time data analytics, and automated production systems enhance efficiency.
Technology facilitates better communication and coordination with suppliers.
Integrating technology into JIT processes leads to more informed decision-making and increased productivity.
Case Studies
Toyota
Toyota is renowned for its mastery of JIT, which has been fundamental to its success.
The Toyota Production System (TPS) embodies JIT principles, emphasizing waste reduction and continuous improvement.
Toyota’s commitment to quality and efficiency has made it a global leader in the automotive industry.
The company’s JIT practices serve as a benchmark for manufacturers worldwide.
Other Japanese Manufacturers
Beyond Toyota, many Japanese manufacturers have successfully implemented JIT.
Companies like Honda, Nissan, and Sony have adopted JIT to enhance their production processes.
These manufacturers have customized JIT principles to fit their specific industry needs and market conditions.
Their success stories demonstrate the versatility and effectiveness of JIT across different sectors.
Conclusion
Just-In-Time production is a powerful methodology that drives efficiency, reduces costs, and enhances quality.
Japanese manufacturers have perfected JIT, setting standards that others strive to emulate.
Despite its challenges, the benefits of JIT make it a valuable strategy for modern manufacturing.
By understanding its principles, overcoming its limitations, and adopting best practices, companies can harness the full potential of JIT.
Embracing JIT not only improves operational performance but also fosters a culture of continuous improvement and excellence.
資料ダウンロード
QCD調達購買管理クラウド「newji」は、調達購買部門で必要なQCD管理全てを備えた、現場特化型兼クラウド型の今世紀最高の購買管理システムとなります。
ユーザー登録
調達購買業務の効率化だけでなく、システムを導入することで、コスト削減や製品・資材のステータス可視化のほか、属人化していた購買情報の共有化による内部不正防止や統制にも役立ちます。
NEWJI DX
製造業に特化したデジタルトランスフォーメーション(DX)の実現を目指す請負開発型のコンサルティングサービスです。AI、iPaaS、および先端の技術を駆使して、製造プロセスの効率化、業務効率化、チームワーク強化、コスト削減、品質向上を実現します。このサービスは、製造業の課題を深く理解し、それに対する最適なデジタルソリューションを提供することで、企業が持続的な成長とイノベーションを達成できるようサポートします。
オンライン講座
製造業、主に購買・調達部門にお勤めの方々に向けた情報を配信しております。
新任の方やベテランの方、管理職を対象とした幅広いコンテンツをご用意しております。
お問い合わせ
コストダウンが利益に直結する術だと理解していても、なかなか前に進めることができない状況。そんな時は、newjiのコストダウン自動化機能で大きく利益貢献しよう!
(Β版非公開)