- お役立ち記事
- Learn about the troubles you want to avoid in global parts procurement and their solutions
月間76,176名の
製造業ご担当者様が閲覧しています*
*2025年3月31日現在のGoogle Analyticsのデータより
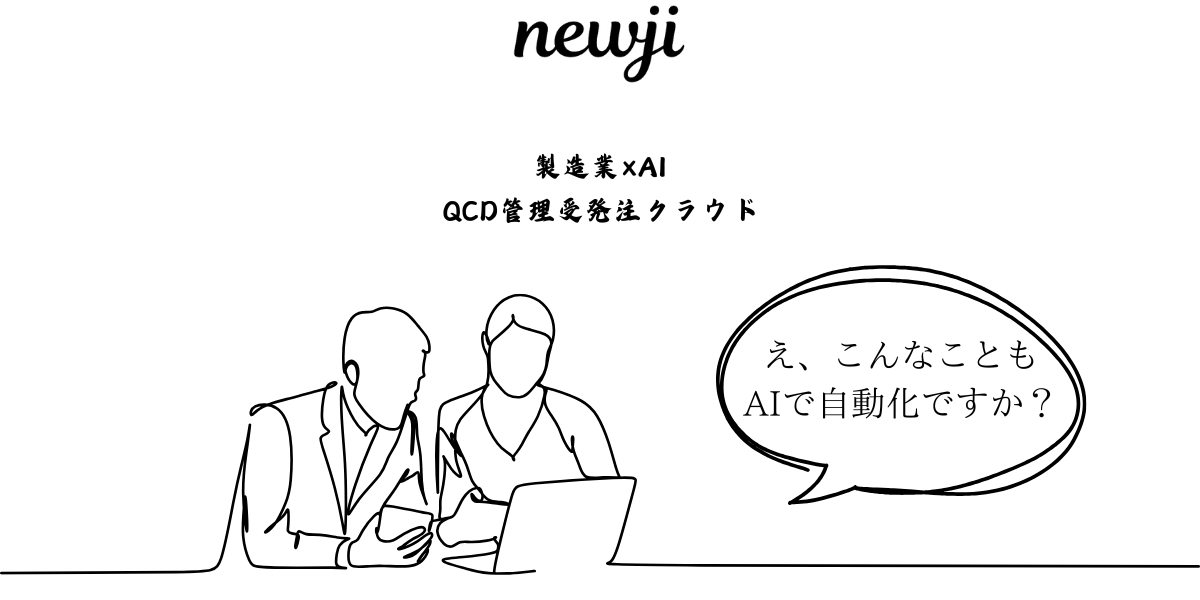
Learn about the troubles you want to avoid in global parts procurement and their solutions
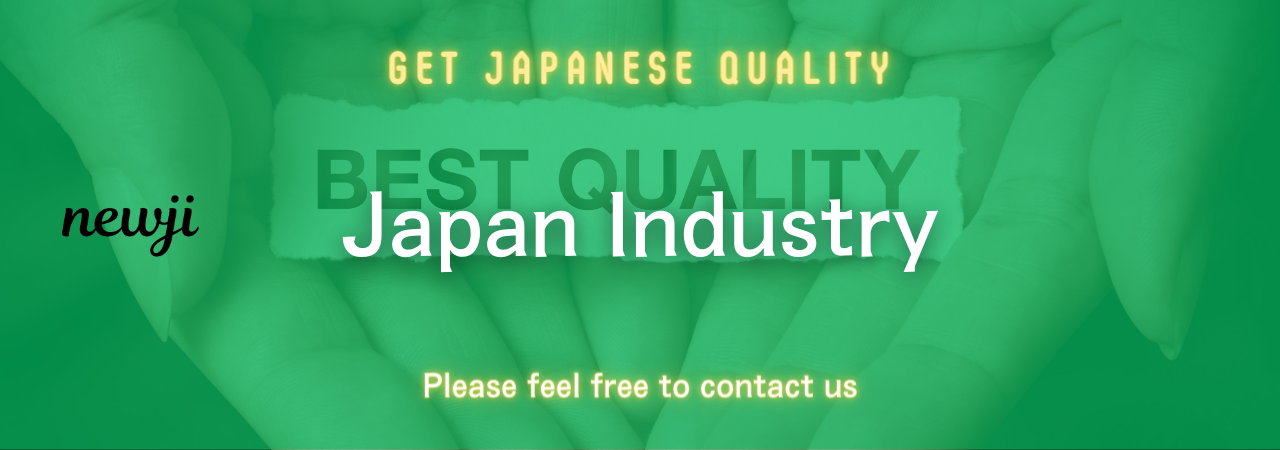
目次
Understanding Global Parts Procurement
Global parts procurement involves sourcing components or materials from manufacturers or suppliers around the world.
It has become an integral part of many businesses, especially in industries like automotive and electronics.
The main advantage of global procurement is the potential for cost savings due to lower production costs in certain countries.
Additionally, it allows companies to access specialized components that may not be available locally.
However, global procurement is not without its challenges.
Common Challenges in Global Parts Procurement
Despite its benefits, global procurement can pose several challenges that businesses need to navigate carefully.
Language and Cultural Barriers
Working with suppliers across different regions means dealing with language and cultural differences.
Misunderstandings can occur, leading to miscommunications about product specifications, delivery schedules, and contractual terms.
It’s essential to have clear communication strategies in place, which could include hiring translators or using translation software.
Supply Chain Disruptions
The COVID-19 pandemic has highlighted how vulnerable global supply chains can be.
Natural disasters, political unrest, or changes in trade policies can disrupt the flow of parts, causing delays and increasing costs.
Companies need to develop robust risk management strategies to mitigate these disruptions.
Quality Assurance
Ensuring consistent quality is crucial when sourcing parts globally.
Different countries may have varying quality standards, which can affect the final product’s quality.
Establishing stringent quality control measures and regular audits can help maintain product standards.
Logistics and Transportation Issues
Transporting goods across international borders involves complex logistics management.
Delays in customs clearance, lack of reliable transportation infrastructure, or inefficiencies in shipping can impact the timely delivery of parts.
Engaging experienced logistics partners is key to overcoming these challenges.
Currency Fluctuations
Global procurement deals with multiple currencies, which can fluctuate greatly.
This volatility can affect the cost of parts and complicate budgeting.
Companies should employ financial strategies like hedging to manage the risks associated with currency fluctuations.
Solutions to Global Procurement Challenges
To manage the challenges of global parts procurement effectively, businesses can employ the following strategies:
Effective Communication Channels
Develop clear communication channels that accommodate language differences.
This might include using collaborative platforms that allow real-time translation or hiring bilingual staff to liaise with suppliers.
Implementing Robust Risk Management
Create a comprehensive risk management strategy that includes contingency plans for supply chain disruptions.
Diversifying suppliers can reduce dependency on a single source and mitigate risks associated with geopolitical issues.
Quality Control Standards
Establish strong, consistent quality control measures.
Working closely with suppliers to understand and implement desired quality standards can prevent discrepancies and ensure reliable product quality.
Regular audits and inspections are critical components of this strategy.
Efficient Logistics Collaboration
Partner with experienced logistics providers who understand international transport complexities and can ensure efficient movement of goods.
Advanced tracking systems can provide real-time updates and help manage delays proactively.
Financial Strategy for Currency Management
Implement financial tools and strategies to manage currency risks.
This could include forward contracts, options, or other hedging instruments that lock in favorable exchange rates and protect against unfavorable fluctuations.
Conclusion
Global parts procurement offers many benefits but comes with its own set of challenges.
By understanding these challenges and applying effective solutions, businesses can harness the full potential of global sourcing.
Implementing strategic planning, robust risk management, and effective communication can help navigate the complexities of global procurement successfully.
With these measures in place, companies can achieve cost efficiencies and maintain a competitive edge in the global marketplace.
資料ダウンロード
QCD管理受発注クラウド「newji」は、受発注部門で必要なQCD管理全てを備えた、現場特化型兼クラウド型の今世紀最高の受発注管理システムとなります。
ユーザー登録
受発注業務の効率化だけでなく、システムを導入することで、コスト削減や製品・資材のステータス可視化のほか、属人化していた受発注情報の共有化による内部不正防止や統制にも役立ちます。
NEWJI DX
製造業に特化したデジタルトランスフォーメーション(DX)の実現を目指す請負開発型のコンサルティングサービスです。AI、iPaaS、および先端の技術を駆使して、製造プロセスの効率化、業務効率化、チームワーク強化、コスト削減、品質向上を実現します。このサービスは、製造業の課題を深く理解し、それに対する最適なデジタルソリューションを提供することで、企業が持続的な成長とイノベーションを達成できるようサポートします。
製造業ニュース解説
製造業、主に購買・調達部門にお勤めの方々に向けた情報を配信しております。
新任の方やベテランの方、管理職を対象とした幅広いコンテンツをご用意しております。
お問い合わせ
コストダウンが利益に直結する術だと理解していても、なかなか前に進めることができない状況。そんな時は、newjiのコストダウン自動化機能で大きく利益貢献しよう!
(β版非公開)