- お役立ち記事
- Learn from the basics to ensure the reliability of procured parts – failure mechanisms and short-term and accurate reliability evaluation techniques
月間77,185名の
製造業ご担当者様が閲覧しています*
*2025年2月28日現在のGoogle Analyticsのデータより
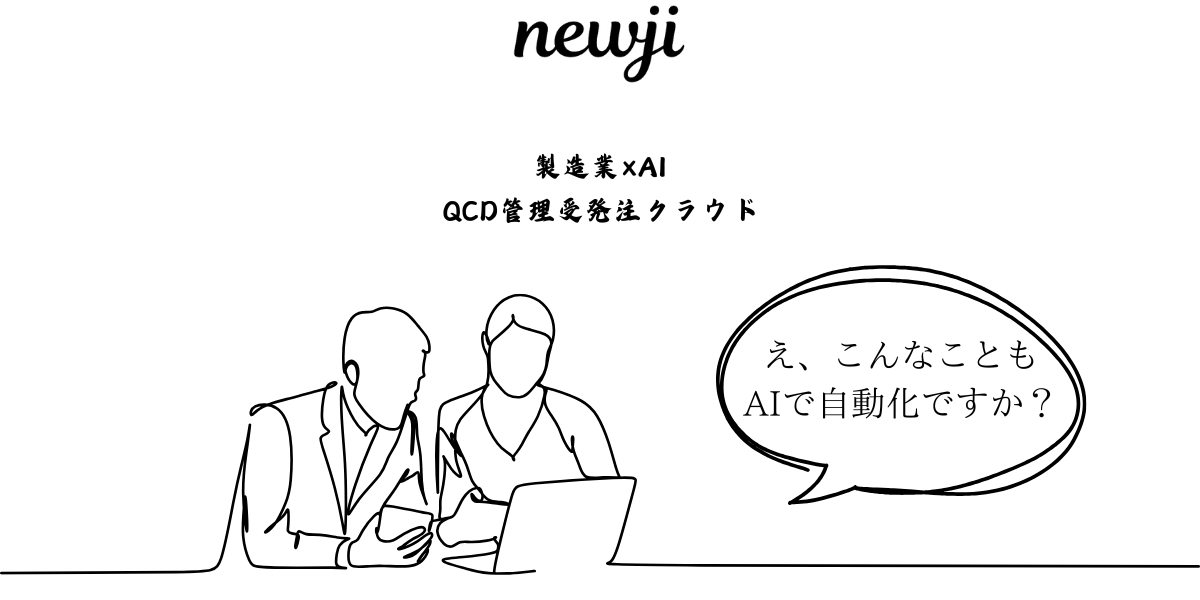
Learn from the basics to ensure the reliability of procured parts – failure mechanisms and short-term and accurate reliability evaluation techniques
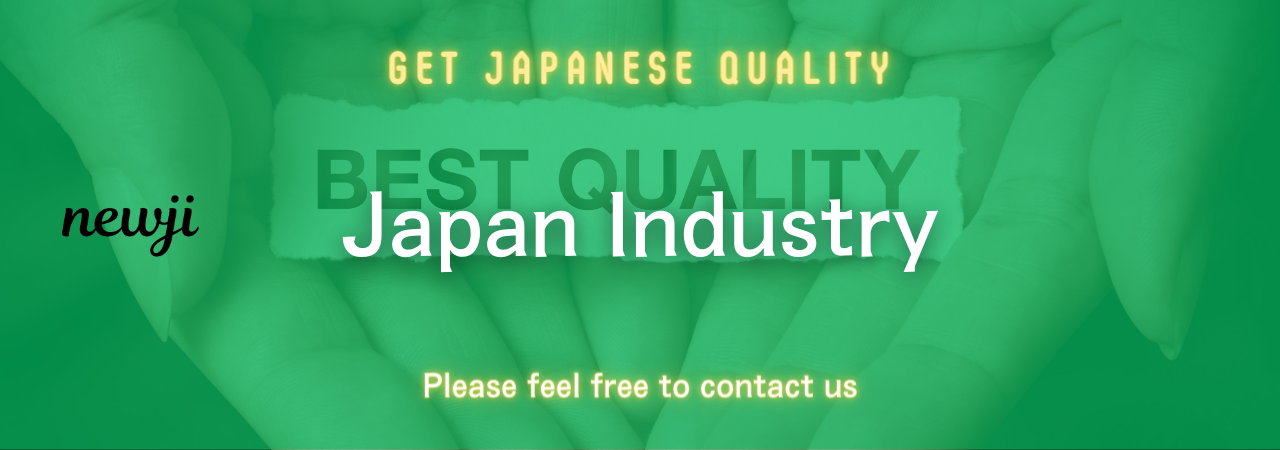
目次
Understanding the Importance of Reliability in Procured Parts
In today’s competitive market, ensuring the reliability of procured parts is more important than ever.
Products across industries rely on the durability and performance of their components to meet customer expectations and regulatory standards.
When procuring parts, failure mechanisms and reliability are crucial factors to consider.
Reliability in this context refers to the ability of a part to perform its intended function under specified conditions for a specific period of time.
To ensure this reliability, companies must understand the basic concepts and evaluation techniques involved.
Identifying Common Failure Mechanisms
Understanding failure mechanisms is the first step toward enhancing the reliability of procured parts.
Failure mechanisms can be broadly categorized into several types, including mechanical, thermal, electrical, and chemical failures.
Mechanical failures are often due to stress, which can result from improper design or excessive load.
Fatigue, fracture, and wear are common examples.
Thermal failures occur when components are exposed to temperatures beyond their tolerance, leading to deformation or breakdown.
Electrical failures might happen when parts experience voltage surges or when there’s a breakdown in insulation.
Chemical failures arise due to corrosion, oxidation, or other chemical reactions that degrade materials over time.
By identifying and mitigating these failure mechanisms, companies can increase the lifespan and performance of their products.
Short-Term Reliability Testing Techniques
To ensure procured parts meet desired reliability standards, industries employ various short-term reliability testing techniques.
These techniques are designed to simulate real-world conditions and identify potential issues before products reach consumers.
One common technique is accelerated life testing, which exposes parts to higher stress levels to quickly induce failures.
This provides insight into how the components will behave under normal usage.
Environmental testing subjects parts to conditions such as high humidity, extreme temperatures, and corrosive environments to test their resilience.
Another crucial method is non-destructive testing, which includes techniques like ultrasonic testing, X-ray, and magnetic particle inspection that assess the integrity of parts without causing damage.
These techniques are valuable because they allow companies to identify potential weaknesses early on, reducing the risk of product failure in the field.
Accurate Reliability Evaluation Techniques
Evaluating the reliability of procured parts accurately involves both statistical analysis and practical testing.
Statistical methods help predict failure probabilities and understanding trends, while practical testing provides real-world evidence of reliability.
Failure Mode and Effects Analysis (FMEA) is widely used for evaluating potential reliability issues.
It involves identifying possible failure modes, their causes, and effects on the system, allowing companies to prioritize which areas require the most attention.
Another effective technique is reliability prediction analysis.
By using models such as the Weibull distribution, companies can forecast the life expectancy of parts and make informed procurement decisions.
Companies also utilize stress testing and life cycle testing, which apply real-world stress to parts over extended periods, determining how long they will last and identifying any unforeseen issues.
The Role of Data in Reliability Evaluation
In recent years, data has become a powerful tool in reliability evaluation.
Collecting and analyzing data from various stages of a component’s lifecycle allows companies to identify patterns and predict future failures more accurately.
Big data and machine learning technologies are increasingly used to process large datasets, extracting valuable insights that support decision-making.
This data-driven approach enhances the accuracy of reliability evaluations and helps companies optimize their procurement processes.
Harnessing data analytics not only improves the reliability of procured parts but also contributes to cost savings by minimizing recalls and warranty claims.
Best Practices for Ensuring Reliable Procurement
To achieve reliable procurement, companies must implement a comprehensive strategy that encompasses supplier selection, quality control, and ongoing evaluation.
Selecting reputable suppliers with a proven track record of delivering quality components is critical.
Establishing clear communication channels with suppliers helps to ensure quality standards are met and any issues are quickly addressed.
Regular audits and inspections are essential for maintaining high standards in procured parts.
This involves consistent quality checks during manufacturing and delivery, as well as inspecting incoming parts for defects.
Finally, ongoing evaluation and feedback loops are important in adapting to evolving reliability requirements.
Continuously assessing reliability metrics and making necessary adjustments to procurement strategies ensures that high standards are maintained.
Conclusion
Ensuring the reliability of procured parts is a crucial aspect of manufacturing that affects the entire lifecycle of a product.
Understanding failure mechanisms, employing short-term reliability testing, and conducting accurate reliability evaluations play pivotal roles in maintaining component integrity.
By leveraging data and adhering to best procurement practices, companies can reduce the risk of failures, enhance product quality, and satisfy customer needs.
In the ever-evolving market, ensuring reliability is not just a technical requirement—it is a competitive advantage.
資料ダウンロード
QCD管理受発注クラウド「newji」は、受発注部門で必要なQCD管理全てを備えた、現場特化型兼クラウド型の今世紀最高の受発注管理システムとなります。
ユーザー登録
受発注業務の効率化だけでなく、システムを導入することで、コスト削減や製品・資材のステータス可視化のほか、属人化していた受発注情報の共有化による内部不正防止や統制にも役立ちます。
NEWJI DX
製造業に特化したデジタルトランスフォーメーション(DX)の実現を目指す請負開発型のコンサルティングサービスです。AI、iPaaS、および先端の技術を駆使して、製造プロセスの効率化、業務効率化、チームワーク強化、コスト削減、品質向上を実現します。このサービスは、製造業の課題を深く理解し、それに対する最適なデジタルソリューションを提供することで、企業が持続的な成長とイノベーションを達成できるようサポートします。
製造業ニュース解説
製造業、主に購買・調達部門にお勤めの方々に向けた情報を配信しております。
新任の方やベテランの方、管理職を対象とした幅広いコンテンツをご用意しております。
お問い合わせ
コストダウンが利益に直結する術だと理解していても、なかなか前に進めることができない状況。そんな時は、newjiのコストダウン自動化機能で大きく利益貢献しよう!
(β版非公開)