- お役立ち記事
- Learn hot forging processing technology from the basics and its key points
月間77,185名の
製造業ご担当者様が閲覧しています*
*2025年2月28日現在のGoogle Analyticsのデータより
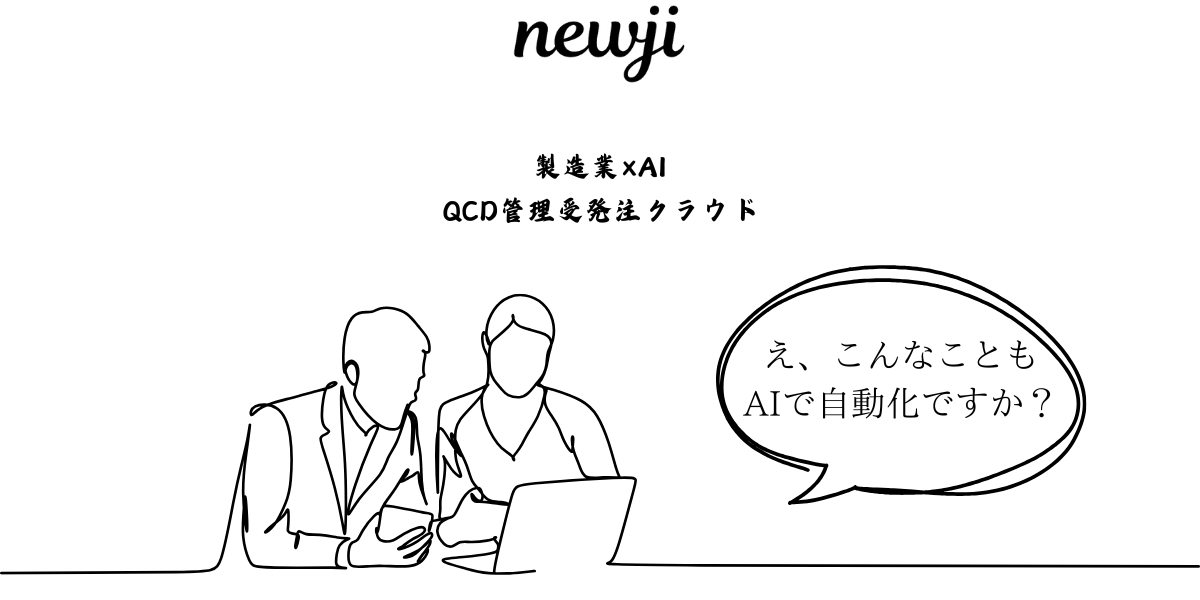
Learn hot forging processing technology from the basics and its key points
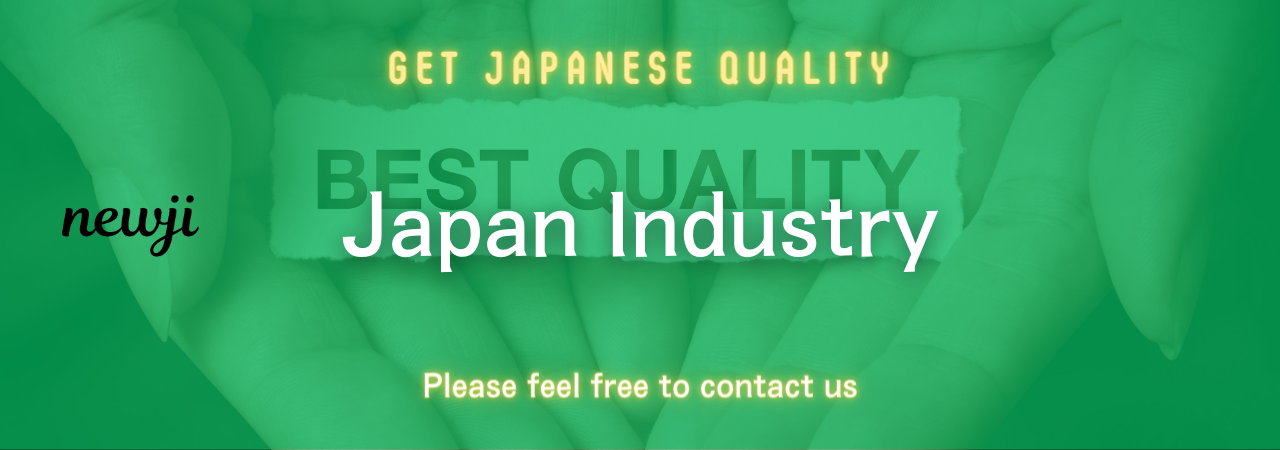
目次
Understanding Hot Forging
Hot forging is a metal forming technique that involves heating a metal material beyond its recrystallization temperature and then shaping it using various tools and machinery.
Unlike cold forging, this process ensures that the metal maintains a high degree of malleability, making it easier to manipulate into desired shapes.
The basic principle of hot forging is to transform a piece of metal into a component with optimal strength, durability, and precision.
By applying both heat and pressure, the metal’s grain structure is refined, enhancing its mechanical properties.
The significance of hot forging lies in its ability to produce strong and intricate metal parts for various industries such as automotive, aerospace, and construction.
The Process of Hot Forging
Step 1: Heating the Metal
The first step in hot forging involves heating the metal to a temperature beyond its recrystallization point.
This typically ranges from 700°C to 1250°C, depending on the specific material being used.
The purpose of this heating is to make the metal malleable and malleable enough for shaping.
Step 2: Forging and Shaping
Once heated, the metal is transferred to a forging press or hammer where the actual shaping takes place.
The metal is compressed between two dies, which are large metal blocks that have been shaped in advance to have the desired final profile.
The force exerted by the press causes the metal to flow and fill the die cavity, forming the required shape.
Step 3: Cooling and Finishing
After the forging process, the metal is allowed to cool down gradually.
This helps in stabilizing the component’s structure and reducing any internal stresses.
Once cooled, additional finishing processes like machining or grinding may be required to meet precise specifications or tolerances.
The Advantages of Hot Forging
Improved Strength
One of the main benefits of hot forging is the improvement in mechanical strength.
The process refines the internal grain structure of the metal, resulting in a component that is more durable and resistant to wear and tear.
Greater Ductility
Because the metal is worked at high temperatures, it becomes more ductile, meaning it can be stretched and shaped without breaking.
This property is crucial for creating intricate and complex shapes that require significant deformation.
Cost Efficiency
Despite the upfront costs of machinery and energy, hot forging is cost-effective in the long run due to its ability to mass-produce components with minimal material waste.
The process achieves near-net shapes, reducing the need for excessive machining post-production.
Versatility and Variety
Hot forging can be applied to a wide array of metals, including steel, aluminum, copper, and titanium.
This makes it a versatile option across multiple industries, catering to diverse needs and specifications.
Key Points to Consider
Material Selection
Choosing the right metal is essential for ensuring the success of the hot forging process.
Different metals behave differently under heat and pressure, so understanding their properties is crucial.
Some materials might require additional treatments or alloying to achieve the desired results.
Temperature Control
Maintaining the appropriate temperature throughout the process is vital for achieving the desired mechanical properties.
Both overheating and underheating can lead to defects such as surface cracking or incomplete die filling.
Die Design
The die design is a critical factor that directly impacts the quality of the final product.
Dies should be designed to account for metal flow and to ensure uniformity in the finished component.
Regular die maintenance is also necessary to prevent wear and extend tool life.
Quality Control
Implementing rigorous quality control measures is essential to identify and rectify defects early in the manufacturing process.
Non-destructive testing methods such as ultrasonic testing or magnetic particle inspection can help ensure the integrity of the forgings.
Conclusion
Hot forging is a powerful metal forming technique that has stood the test of time due to its numerous advantages.
By understanding the underlying principles and critical factors, manufacturers can produce high-quality, durable, and cost-effective components.
Whether it’s for automotive parts, aircraft components, or construction equipment, mastering hot forging can be a game-changer in the world of manufacturing.
資料ダウンロード
QCD管理受発注クラウド「newji」は、受発注部門で必要なQCD管理全てを備えた、現場特化型兼クラウド型の今世紀最高の受発注管理システムとなります。
ユーザー登録
受発注業務の効率化だけでなく、システムを導入することで、コスト削減や製品・資材のステータス可視化のほか、属人化していた受発注情報の共有化による内部不正防止や統制にも役立ちます。
NEWJI DX
製造業に特化したデジタルトランスフォーメーション(DX)の実現を目指す請負開発型のコンサルティングサービスです。AI、iPaaS、および先端の技術を駆使して、製造プロセスの効率化、業務効率化、チームワーク強化、コスト削減、品質向上を実現します。このサービスは、製造業の課題を深く理解し、それに対する最適なデジタルソリューションを提供することで、企業が持続的な成長とイノベーションを達成できるようサポートします。
製造業ニュース解説
製造業、主に購買・調達部門にお勤めの方々に向けた情報を配信しております。
新任の方やベテランの方、管理職を対象とした幅広いコンテンツをご用意しております。
お問い合わせ
コストダウンが利益に直結する術だと理解していても、なかなか前に進めることができない状況。そんな時は、newjiのコストダウン自動化機能で大きく利益貢献しよう!
(β版非公開)