- お役立ち記事
- Learn injection molding technology from the basics and points to prevent molding defects
月間77,185名の
製造業ご担当者様が閲覧しています*
*2025年2月28日現在のGoogle Analyticsのデータより
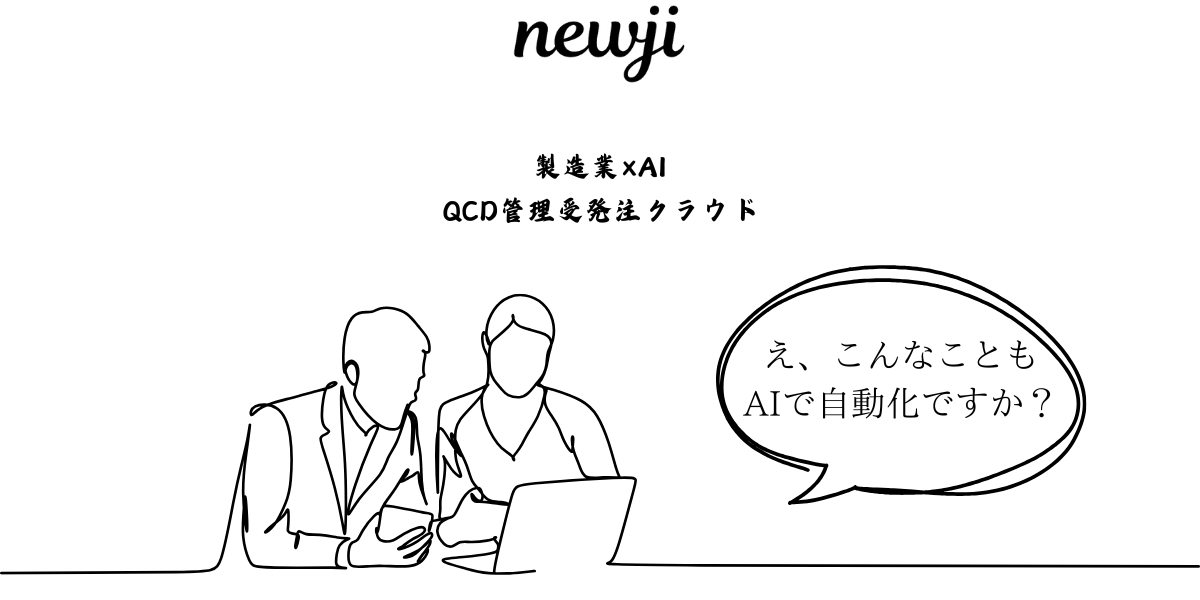
Learn injection molding technology from the basics and points to prevent molding defects
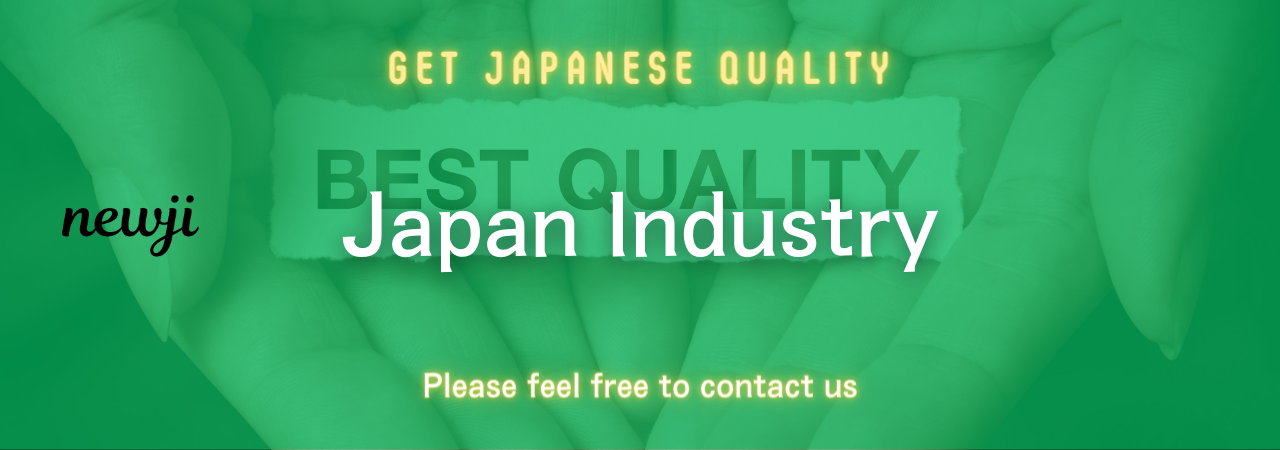
目次
What is Injection Molding?
Injection molding is a manufacturing process used to produce parts by injecting molten material into a mold.
This method is widely used for creating a multitude of everyday products, ranging from small components to large automotive parts.
The materials commonly used in injection molding include thermoplastics, thermosetting plastics, and metals.
The Basic Principles of Injection Molding
Injection molding involves several key steps.
First, the raw material is fed into a heated barrel, mixed, and then injected into a mold cavity.
Inside the mold, the material cools and solidifies into the shape of the cavity.
Once solidified, the part is ejected from the mold, and the cycle repeats.
The process requires a detailed understanding of how materials flow and solidify.
The mold must be carefully designed to ensure that the material flows evenly and meets the specifications for the final product.
Components of an Injection Molding Machine
An injection molding machine can be primarily broken down into three units: the injection unit, the clamping unit, and the mold.
– **Injection Unit:** Responsible for melting and injecting the material into the mold.
– **Clamping Unit:** Holds the mold together during injection and cooling.
– **Mold:** Contains cavities where the molded part is formed.
Materials Used in Injection Molding
Materials used in injection molding vary widely, but they are chosen based on the characteristics required for the final product.
Thermoplastic polymers are the most common and offer flexibility, durability, and ease of production.
Examples include Polyethylene (PE), Polypropylene (PP), and Polystyrene (PS).
For specific applications, other materials like thermosets and metals can also be used.
Each material has its melting point, flow characteristics, and cooling rate, which play crucial roles in the process.
Preventing Molding Defects in Injection Molding
Injection molding is highly efficient, but various defects can occur if not carefully managed.
Understanding and preventing these defects is crucial to produce high-quality parts consistently.
Common Molding Defects
1. **Short Shot:** Occurs when the mold cavity is not completely filled, leading to incomplete parts.
2. **Flash:** Excess material that extrudes from the mold, creating thin layers at the parting lines or around holes.
3. **Sink Marks:** Indentations on the surface of the molded part, typically due to improper cooling.
Strategies to Prevent Defects
Ensuring high-quality molding parts involves a combination of proper machine settings, material handling, and mold design.
– **Optimizing Machine Settings:** Adjusting temperature, pressure, and cycle times can help mitigate many common defects.
– **Material Handling:** Proper drying and treatment of the material before injection can prevent issues such as bubbling and discoloration.
– **Mold Design:** Ensuring that the mold is designed with the appropriate vents, gates, and cooling channels is crucial to minimizing defects.
Quality Control in Injection Molding
Maintaining consistent quality in injection molding requires rigorous quality control measures.
Inspection and Testing
Regular inspection and testing of molded parts are crucial.
Using tools such as calipers and coordinate measuring machines (CMMs) helps ensure parts meet specifications.
Visual inspections can also help identify defects early in the process.
Process Monitoring
Utilizing technology for process monitoring can track variables such as temperature and pressure throughout production, providing data that helps fine-tune the process and prevent defects.
Future Trends in Injection Molding
The future of injection molding looks promising with advancements in technology driving efficiency and precision.
Sustainable Materials and Processes
As environmental concerns rise, there is a growing focus on using biodegradable and recycled materials.
Innovations aim to lessen the environmental footprint without compromising material quality.
Automation and Smart Manufacturing
Automation and smart technology integration are enhancing productivity in the injection molding industry.
Robots and automated systems help increase production speed while reducing labor costs and defects.
The rise of the industrial Internet of Things (IoT) allows for better real-time data collection and analysis, leading to improved process control and product quality.
Understanding the basics of injection molding and staying informed about strategies to prevent defects ensures that manufacturers can continue to produce high-quality products efficiently, meeting both current demands and anticipating future trends.
資料ダウンロード
QCD管理受発注クラウド「newji」は、受発注部門で必要なQCD管理全てを備えた、現場特化型兼クラウド型の今世紀最高の受発注管理システムとなります。
ユーザー登録
受発注業務の効率化だけでなく、システムを導入することで、コスト削減や製品・資材のステータス可視化のほか、属人化していた受発注情報の共有化による内部不正防止や統制にも役立ちます。
NEWJI DX
製造業に特化したデジタルトランスフォーメーション(DX)の実現を目指す請負開発型のコンサルティングサービスです。AI、iPaaS、および先端の技術を駆使して、製造プロセスの効率化、業務効率化、チームワーク強化、コスト削減、品質向上を実現します。このサービスは、製造業の課題を深く理解し、それに対する最適なデジタルソリューションを提供することで、企業が持続的な成長とイノベーションを達成できるようサポートします。
製造業ニュース解説
製造業、主に購買・調達部門にお勤めの方々に向けた情報を配信しております。
新任の方やベテランの方、管理職を対象とした幅広いコンテンツをご用意しております。
お問い合わせ
コストダウンが利益に直結する術だと理解していても、なかなか前に進めることができない状況。そんな時は、newjiのコストダウン自動化機能で大きく利益貢献しよう!
(β版非公開)