- お役立ち記事
- Learning from Japanese Suppliers: Efficient Production Line Management
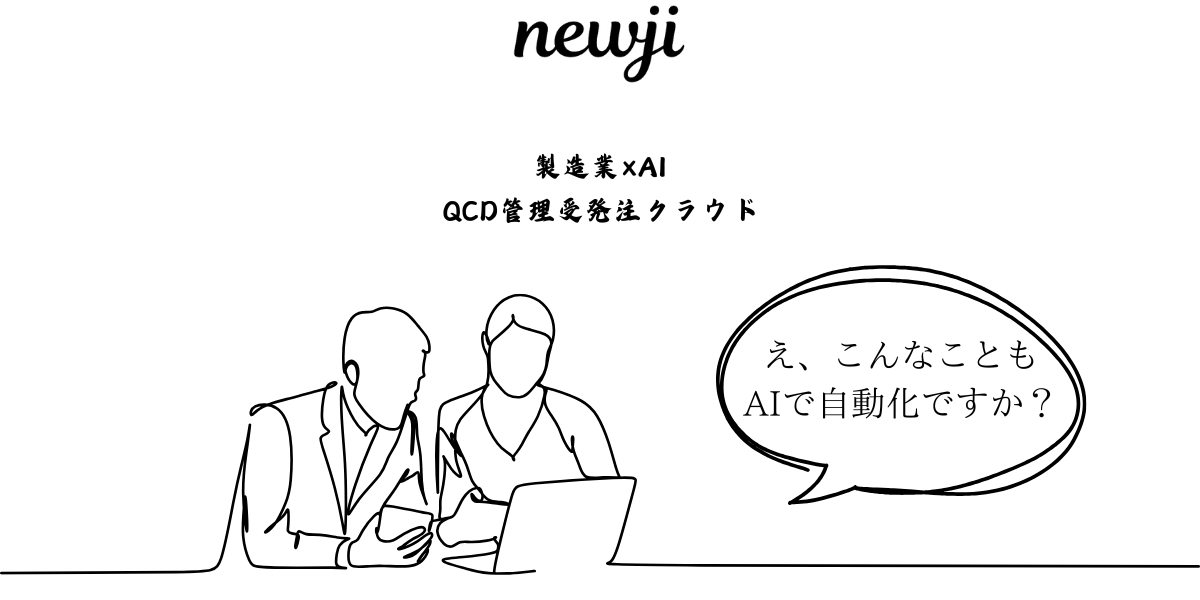
Learning from Japanese Suppliers: Efficient Production Line Management
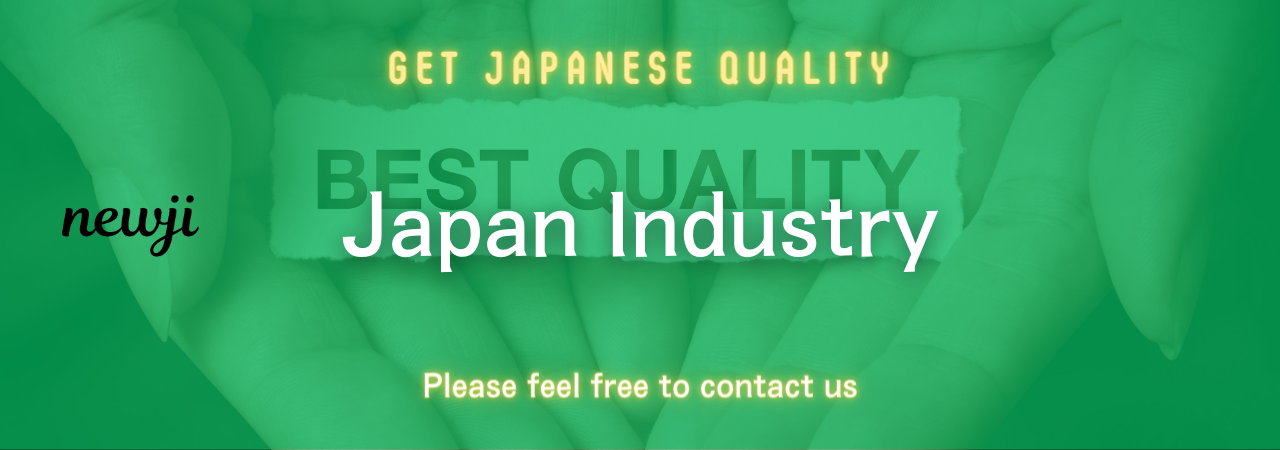
Efficient production line management is vital for any manufacturing operation.
In this article, we’ll explore how Japanese suppliers excel in this area and what lessons can be learned from their practices.
目次
Understanding Production Line Management
Production line management involves overseeing the manufacturing process to ensure efficiency, quality, and timely delivery of products.
In simple terms, it’s about making sure that everything works smoothly from start to finish.
The Basics of Production Line Management
The core elements of production line management include:
1. **Planning and Scheduling:** Ensuring that all necessary resources are available and that production runs according to a set timetable.
2. **Quality Control:** Monitoring the products to ensure they meet specific standards.
3. **Inventory Management:** Keeping track of raw materials and finished goods to avoid shortages or surpluses.
4. **Continuous Improvement:** Regularly looking for ways to make the process more efficient.
Japanese suppliers have mastered these elements, and their methods have become a global benchmark.
Lean Manufacturing: The Japanese Approach
Lean manufacturing, pioneered by Japanese companies like Toyota, focuses on reducing waste and increasing efficiency.
This approach has gained worldwide recognition and is often used by companies seeking to improve their production line management.
What is Lean Manufacturing?
Lean manufacturing is a methodology aimed at minimizing waste without compromising quality.
The main principles include:
1. **Value:** Identifying what adds value to the customer and eliminating everything else.
2. **Value Stream:** Mapping out the entire production process to identify areas of waste.
3. **Flow:** Ensuring that the production process flows smoothly without interruptions.
4. **Pull:** Producing only what is needed when it is needed.
5. **Perfection:** Continuously seeking ways to improve the process.
These principles can be applied to any manufacturing operation to enhance efficiency and quality.
Key Techniques in Lean Manufacturing
Japanese suppliers use several specific techniques to implement lean manufacturing effectively.
Let’s explore some of these key techniques.
Kaizen (Continuous Improvement)
Kaizen is a philosophy that focuses on continuous, incremental improvements in the production process.
It involves everyone in the organization, from top management to frontline workers.
By encouraging small, daily changes, Kaizen fosters a culture of continuous improvement.
This approach ensures that production lines remain efficient and adaptable to changes.
Just-in-Time (JIT) Production
JIT production aims to produce only what is needed, when it is needed.
This technique minimizes inventory costs and reduces waste.
By aligning production with demand, companies can respond quickly to changes in the market.
Japanese suppliers excel in JIT production, ensuring that their production lines are always efficient and responsive.
5S Methodology
The 5S methodology is a workplace organization technique that helps maintain an efficient and clean production line.
The five S’s stand for:
1. **Sort (Seiri):** Removing unnecessary items from the workplace.
2. **Set in Order (Seiton):** Organizing tools and materials for easy access.
3. **Shine (Seiso):** Keeping the workplace clean and tidy.
4. **Standardize (Seiketsu):** Establishing standards for organization and cleanliness.
5. **Sustain (Shitsuke):** Maintaining and improving these standards over time.
The 5S methodology creates a more efficient and pleasant working environment, leading to better productivity.
Benefits of Adopting Japanese Production Practices
By adopting Japanese production practices, companies can achieve significant improvements in their production line management.
Increased Efficiency
Lean manufacturing techniques eliminate waste and streamline the production process.
This leads to faster production times and reduced costs.
Improved Quality
Emphasizing continuous improvement and quality control ensures that products meet high standards.
This results in fewer defects and higher customer satisfaction.
Greater Flexibility
Techniques like JIT production allow companies to respond quickly to changing market demands.
This flexibility is crucial in today’s fast-paced business environment.
Enhanced Employee Engagement
Involving employees in continuous improvement processes fosters a sense of ownership and engagement.
This leads to a more motivated and productive workforce.
Implementing Japanese Production Practices
Adopting Japanese production practices requires commitment and a willingness to change.
Here are some steps to get started.
Analyze Your Current Process
Start by mapping out your current production process.
Identify areas where waste occurs and where improvements can be made.
Educate and Train Employees
Involve your employees in the transition process.
Provide training on lean manufacturing principles and techniques like Kaizen, JIT, and 5S.
Create a Continuous Improvement Culture
Foster a culture that values continuous improvement.
Encourage employees to suggest and implement small changes that can enhance efficiency.
Monitor and Adjust
Regularly monitor the results of the changes you’ve implemented.
Be prepared to make adjustments as needed to ensure continued improvement.
Conclusion
Learning from Japanese suppliers can provide valuable insights into efficient production line management.
By adopting lean manufacturing techniques, companies can enhance efficiency, improve quality, and become more responsive to market demands.
Implementing these practices requires commitment and a willingness to change, but the benefits are well worth the effort.
Whether you’re a small manufacturer or a large corporation, the lessons from Japanese suppliers can help you achieve a more efficient and productive operation.
資料ダウンロード
QCD調達購買管理クラウド「newji」は、調達購買部門で必要なQCD管理全てを備えた、現場特化型兼クラウド型の今世紀最高の購買管理システムとなります。
ユーザー登録
調達購買業務の効率化だけでなく、システムを導入することで、コスト削減や製品・資材のステータス可視化のほか、属人化していた購買情報の共有化による内部不正防止や統制にも役立ちます。
NEWJI DX
製造業に特化したデジタルトランスフォーメーション(DX)の実現を目指す請負開発型のコンサルティングサービスです。AI、iPaaS、および先端の技術を駆使して、製造プロセスの効率化、業務効率化、チームワーク強化、コスト削減、品質向上を実現します。このサービスは、製造業の課題を深く理解し、それに対する最適なデジタルソリューションを提供することで、企業が持続的な成長とイノベーションを達成できるようサポートします。
オンライン講座
製造業、主に購買・調達部門にお勤めの方々に向けた情報を配信しております。
新任の方やベテランの方、管理職を対象とした幅広いコンテンツをご用意しております。
お問い合わせ
コストダウンが利益に直結する術だと理解していても、なかなか前に進めることができない状況。そんな時は、newjiのコストダウン自動化機能で大きく利益貢献しよう!
(Β版非公開)