- お役立ち記事
- Learning the Concepts and Approaches to Business Process Improvement
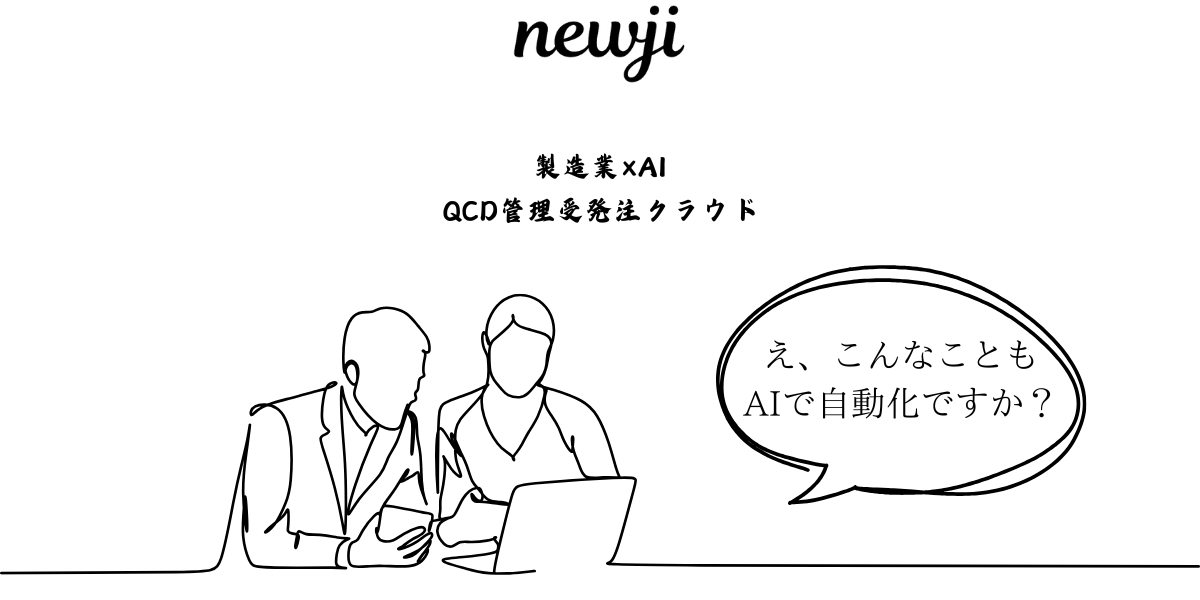
Learning the Concepts and Approaches to Business Process Improvement
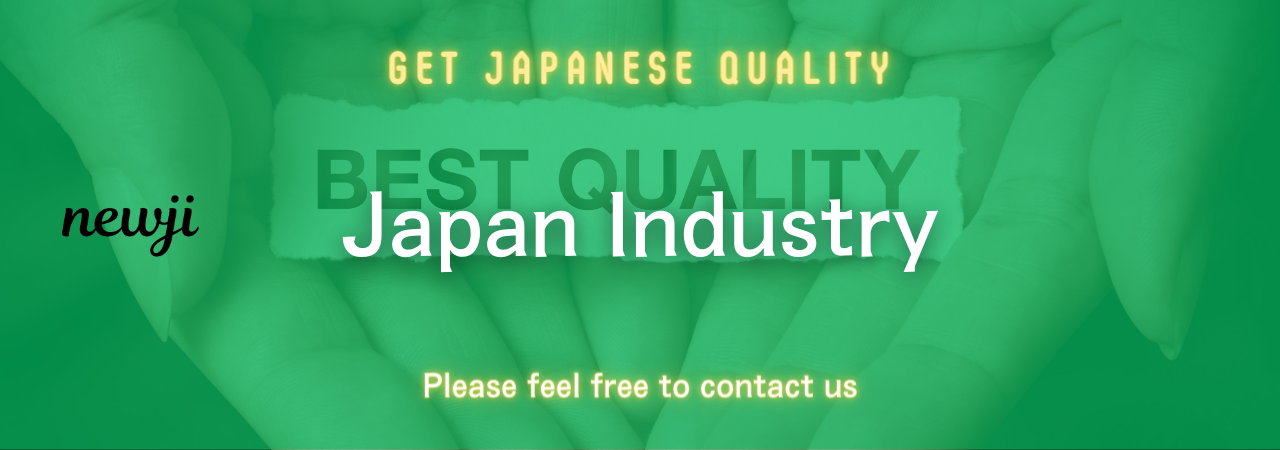
目次
Understanding Business Process Improvement
Business process improvement (BPI) is a systematic approach to help an organization optimize its underlying processes to achieve more efficient results.
At its core, BPI aims to reduce waste and improve productivity through various methodologies and techniques.
If this concept sounds complex, don’t worry.
In simple terms, it’s all about making your business processes better, faster, and cheaper.
Why is Business Process Improvement Important?
Business process improvement is crucial for several reasons.
First, it enables organizations to stay competitive in a fast-paced market.
If your processes are efficient, you can deliver better products and services to your customers, and do it quicker than your competitors.
Second, it helps in reducing costs by eliminating waste, redundancies, and inefficiencies.
Finally, BPI can improve employee satisfaction by making their tasks easier and less time-consuming, which in turn boosts overall productivity.
Basic Concepts of Business Process Improvement
To understand BPI, it’s essential to know its basic concepts.
Here are some key terms you’ll come across:
Process Mapping
This involves identifying and documenting the specific steps in a business process.
Think of it as creating a flowchart that visually represents the steps, who is responsible for each step, and how they interconnect.
Benchmarking
Benchmarking is the practice of comparing your processes with best practices from other organizations or standard measurements.
It provides a frame of reference to gauge performance and identify areas for improvement.
Root Cause Analysis
This is used to identify the primary cause of a problem within a process.
Once the root cause is identified, it’s easier to develop solutions that will prevent the problem from recurring.
Key Performance Indicators (KPIs)
KPIs are metrics that help you measure the effectiveness of your processes.
Examples include turnaround time, error rates, and customer satisfaction.
Monitoring KPIs allows you to see how well your processes are performing and where improvements are needed.
Approaches to Business Process Improvement
Various methodologies can help in the implementation of business process improvement.
Here are a few that are widely used:
Lean
Derived from Toyota’s production system, Lean focuses on eliminating waste and ensuring that every aspect of the process adds value.
Lean methods aim to streamline processes, improve product quality, and enhance customer satisfaction.
Tools such as 5S (Sort, Set in order, Shine, Standardize, Sustain) and Kaizen (continuous improvement) are commonly used in Lean.
Six Sigma
Six Sigma aims to improve the quality of process outputs by identifying and removing the causes of defects, minimizing variability, and reducing waste.
It employs a set of quality management tools, including statistical methods.
Six Sigma is often represented by the DMAIC framework (Define, Measure, Analyze, Improve, Control).
Total Quality Management (TQM)
TQM is a comprehensive approach that focuses on long-term success through customer satisfaction.
It involves all members of an organization in improving processes, products, services, and culture.
TQM stresses continuous improvement, involving everyone from top management to frontline employees.
Agile
Although commonly associated with software development, Agile principles are also highly applicable to business process improvement.
Agile methodologies focus on flexibility, collaboration, and customer feedback, allowing for rapid adjustments and refinements.
Approaches like Scrum and Kanban are part of Agile methodologies.
Steps to Implement Business Process Improvement
Implementing business process improvement involves several steps:
Identify the Processes to Improve
First, you need to identify which processes are causing inefficiencies or customer dissatisfaction.
This can be done through employee feedback, customer complaints, or by monitoring KPIs.
Analyze the Current Process
Next, analyze the existing process to understand its strengths and weaknesses.
This is where process mapping and root cause analysis come into play.
Design the Improved Process
Once you understand the current process, design an improved version.
This might involve changing the sequence of steps, integrating new technologies, or reassigning responsibilities.
Implement the Improvement
Execute the new process design.
This might require retraining employees, altering workflows, or investing in new tools or software.
Monitor and Control
Finally, after implementing the improved process, monitor its performance to ensure it delivers the expected results.
Use KPIs to measure success and make adjustments as necessary to iron out any issues.
Challenges in Business Process Improvement
While the benefits of BPI are clear, implementing it is often challenging.
Resistance to Change
Employees may be resistant to changing existing processes.
It’s essential to communicate the benefits clearly and involve them in the improvement efforts to gain their buy-in.
Lack of Resources
Implementing BPI can be resource-intensive, requiring time, budget, and expertise.
Careful planning and securing executive support can help mitigate this challenge.
Complexity
Some processes are inherently complex, making them challenging to map, analyze, and improve.
Using specialized software and seeking external expertise can simplify the process.
Conclusion
Business process improvement is a valuable approach for enhancing efficiency, reducing costs, and boosting overall productivity.
By understanding its core concepts and utilizing methodologies like Lean, Six Sigma, TQM, and Agile, organizations can achieve significant improvements.
Although there are challenges, the benefits far outweigh the difficulties, making BPI an indispensable tool for any business aiming to stay competitive and grow in today’s dynamic market.
資料ダウンロード
QCD調達購買管理クラウド「newji」は、調達購買部門で必要なQCD管理全てを備えた、現場特化型兼クラウド型の今世紀最高の購買管理システムとなります。
ユーザー登録
調達購買業務の効率化だけでなく、システムを導入することで、コスト削減や製品・資材のステータス可視化のほか、属人化していた購買情報の共有化による内部不正防止や統制にも役立ちます。
NEWJI DX
製造業に特化したデジタルトランスフォーメーション(DX)の実現を目指す請負開発型のコンサルティングサービスです。AI、iPaaS、および先端の技術を駆使して、製造プロセスの効率化、業務効率化、チームワーク強化、コスト削減、品質向上を実現します。このサービスは、製造業の課題を深く理解し、それに対する最適なデジタルソリューションを提供することで、企業が持続的な成長とイノベーションを達成できるようサポートします。
オンライン講座
製造業、主に購買・調達部門にお勤めの方々に向けた情報を配信しております。
新任の方やベテランの方、管理職を対象とした幅広いコンテンツをご用意しております。
お問い合わせ
コストダウンが利益に直結する術だと理解していても、なかなか前に進めることができない状況。そんな時は、newjiのコストダウン自動化機能で大きく利益貢献しよう!
(Β版非公開)