- お役立ち記事
- Leveraging Big Data for Innovation: How Japanese Manufacturing is Leading the Way
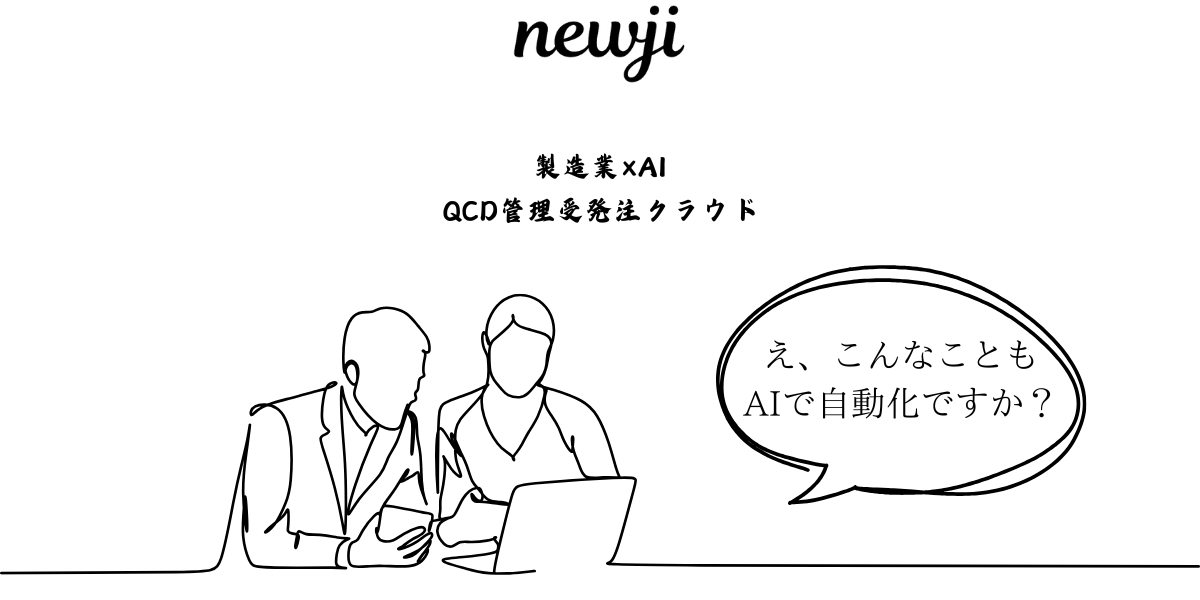
Leveraging Big Data for Innovation: How Japanese Manufacturing is Leading the Way
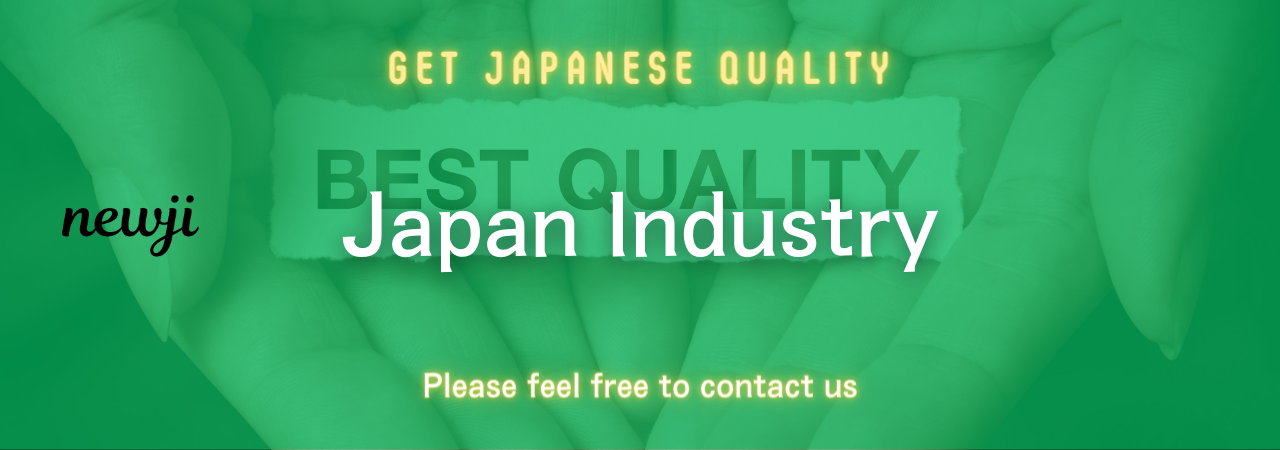
目次
The Rise of Big Data in Manufacturing
Big Data has transformed numerous industries, and manufacturing is no exception.
Japanese manufacturing companies, known for their precision, efficiency, and attention to detail, have been quick to adopt Big Data technologies to stay ahead of their global competitors.
This proactive approach has enabled them to innovate continuously and maintain their status as industry leaders.
The Impact of Big Data on Manufacturing Processes
Before diving into how Japanese manufacturers are leveraging Big Data, it’s essential to understand its impact on manufacturing processes.
Big Data refers to the vast volumes of data generated from various sources, such as machines, sensors, and enterprise systems.
When analyzed, this data provides invaluable insights that can enhance production efficiency, reduce downtime, and improve overall product quality.
Japanese manufacturers have implemented Big Data analytics across various stages of the production lifecycle.
From raw material procurement to end-product delivery, each phase can benefit from real-time data analysis.
For instance, predictive maintenance uses data from machine sensors to forecast equipment failures before they happen, thus minimizing downtime and maintenance costs.
Likewise, quality control processes are enhanced by analyzing data from production lines to identify patterns and anomalies that could signify defects.
Advantages of Big Data in Japanese Manufacturing
Enhanced Quality Control
Japanese manufacturers hold a reputation for high quality, and Big Data has only strengthened this position.
With tools like machine learning and artificial intelligence, companies can analyze enormous datasets to identify defects and variations in real-time.
This immediate response capability ensures that corrective actions are taken promptly, reducing the likelihood of defective products reaching the consumer.
Optimized Production Processes
Through data analysis, manufacturers can fine-tune their production processes for optimal efficiency.
For example, by analyzing historical data, Japanese companies can identify bottlenecks and inefficiencies in production lines.
This information allows for adjustments that result in smoother operations and faster production times.
Moreover, data analytics can help manage inventory more effectively, ensuring that stock levels are maintained without excess holding costs.
Cost Reduction
Cost control is a critical aspect of manufacturing, and Big Data offers numerous ways to cut expenses.
Predictive maintenance reduces the costly downtime associated with machine failures.
Energy usage can be optimized by monitoring consumption patterns and identifying areas where savings can be made.
Furthermore, supply chain logistics benefit from data analytics by ensuring efficient routing and reducing transportation costs.
Challenges and Disadvantages
Despite the numerous advantages, the adoption of Big Data in manufacturing is not without challenges.
Data Security
One significant concern is data security.
As manufacturing processes become increasingly digital, the risk of cyberattacks escalates.
Japanese manufacturers must invest heavily in cybersecurity measures to protect sensitive data from breaches.
This investment can be costly and requires continuous updates to stay ahead of potential threats.
Integration Issues
Another challenge is integrating Big Data systems with existing manufacturing infrastructure.
Many Japanese companies have long histories and use legacy equipment that may not be compatible with modern data analytics tools.
Bridging this gap often requires substantial investment in new technologies and extensive retraining for existing staff.
Skilled Workforce Shortage
There’s also the issue of a skilled workforce.
Data analytics require specialized knowledge, and there’s currently a shortage of data scientists and engineers who can leverage Big Data effectively.
Japanese companies need to invest in training programs and collaborate with educational institutions to cultivate the next generation of skilled professionals.
Best Practices for Leveraging Big Data
The successful implementation of Big Data in manufacturing requires a strategic approach.
Comprehensive Data Collection
To fully leverage Big Data, manufacturers must collect comprehensive data from all available sources.
This includes machine sensors, production line cameras, and enterprise management systems.
The broader the data pool, the more accurate and actionable the insights will be.
Invest in Advanced Analytics Tools
Utilizing advanced analytics tools is essential for processing and analyzing data efficiently.
Japanese manufacturers should invest in machine learning, AI, and other cutting-edge technologies that can turn raw data into valuable insights.
These tools can identify patterns and trends that would be impossible to detect manually.
Collaborate with Technology Partners
Collaborating with technology partners can provide access to the latest advancements in Big Data analytics.
Japanese companies often form alliances with tech firms to integrate new technologies seamlessly.
These partnerships also offer additional support and expertise, ensuring a smoother transition to data-driven manufacturing processes.
Continuous Training and Development
To address the skilled workforce shortage, continuous training programs are essential.
Companies must regularly update their employees on the latest data analytics techniques and tools.
Collaborating with educational institutions to create specialized courses can also help cultivate new talent in the field.
Adopt a Holistic Approach
A holistic approach to Big Data implementation ensures that all aspects of the manufacturing process are covered.
Japanese manufacturers must integrate data analytics into procurement, production, quality control, and logistics.
This comprehensive strategy guarantees that data-driven insights are utilized to their fullest potential across the entire production lifecycle.
Supplier Negotiation Techniques with Big Data
Big Data can also play a crucial role in supplier negotiations, a vital aspect of procurement and purchasing.
Data-Driven Decision Making
When negotiating with suppliers, having access to detailed data can provide a significant advantage.
Japanese manufacturers can use data analytics to assess supplier performance, delivery times, and cost structures.
This information enables more informed decision-making and helps in selecting the most reliable and cost-effective suppliers.
Predicting Market Trends
Big Data analytics can forecast market trends, enabling manufacturers to anticipate changes in raw material prices and supply chain disruptions.
These predictions allow companies to negotiate better contracts and locking favorable terms before market conditions change.
Furthermore, understanding market trends helps in diversifying the supplier base to mitigate risks associated with reliance on a single source.
Improved Collaboration
Sharing data with suppliers can lead to improved collaboration and transparency.
Japanese manufacturers can use Big Data to provide suppliers with insights on production schedules, demand forecasts, and quality requirements.
This transparency fosters stronger relationships and ensures that suppliers can meet the company’s needs more effectively.
Market Conditions and Japanese Leadership
The global market for Big Data in manufacturing is growing rapidly, and Japan is at the forefront of this trend.
Government Support
The Japanese government plays a significant role in supporting Big Data initiatives.
Through policies and funding programs, the government encourages the adoption of advanced technologies in the manufacturing sector.
This support is vital for smaller companies that may not have the resources to invest heavily in Big Data infrastructure.
Strong R&D Investment
Japanese manufacturers are known for their strong commitment to research and development (R&D).
By investing heavily in R&D, companies can develop new Big Data applications tailored to their specific needs.
This continuous innovation cycle ensures that Japanese manufacturers remain leaders in utilizing Big Data for manufacturing excellence.
Focus on Quality and Precision
The emphasis on quality and precision in Japanese manufacturing aligns perfectly with the capabilities of Big Data analytics.
By leveraging data to enhance quality control processes, Japanese companies can maintain their high standards and continue to deliver superior products to the market.
Conclusion
Japanese manufacturing is leading the way in leveraging Big Data for innovation.
By adopting advanced analytics tools, investing in R&D, and fostering strong government and supplier collaborations, Japanese companies can harness the power of Big Data to enhance their production processes, reduce costs, and maintain their reputation for high quality.
As the global market for Big Data in manufacturing continues to grow, the lessons learned from Japan’s approach can serve as a benchmark for other manufacturers seeking to capitalize on this transformative technology.
資料ダウンロード
QCD調達購買管理クラウド「newji」は、調達購買部門で必要なQCD管理全てを備えた、現場特化型兼クラウド型の今世紀最高の購買管理システムとなります。
ユーザー登録
調達購買業務の効率化だけでなく、システムを導入することで、コスト削減や製品・資材のステータス可視化のほか、属人化していた購買情報の共有化による内部不正防止や統制にも役立ちます。
NEWJI DX
製造業に特化したデジタルトランスフォーメーション(DX)の実現を目指す請負開発型のコンサルティングサービスです。AI、iPaaS、および先端の技術を駆使して、製造プロセスの効率化、業務効率化、チームワーク強化、コスト削減、品質向上を実現します。このサービスは、製造業の課題を深く理解し、それに対する最適なデジタルソリューションを提供することで、企業が持続的な成長とイノベーションを達成できるようサポートします。
オンライン講座
製造業、主に購買・調達部門にお勤めの方々に向けた情報を配信しております。
新任の方やベテランの方、管理職を対象とした幅広いコンテンツをご用意しております。
お問い合わせ
コストダウンが利益に直結する術だと理解していても、なかなか前に進めることができない状況。そんな時は、newjiのコストダウン自動化機能で大きく利益貢献しよう!
(Β版非公開)