- お役立ち記事
- Leveraging the Digital Supply Chain Twin to Enhance Competitiveness in Manufacturing
Leveraging the Digital Supply Chain Twin to Enhance Competitiveness in Manufacturing
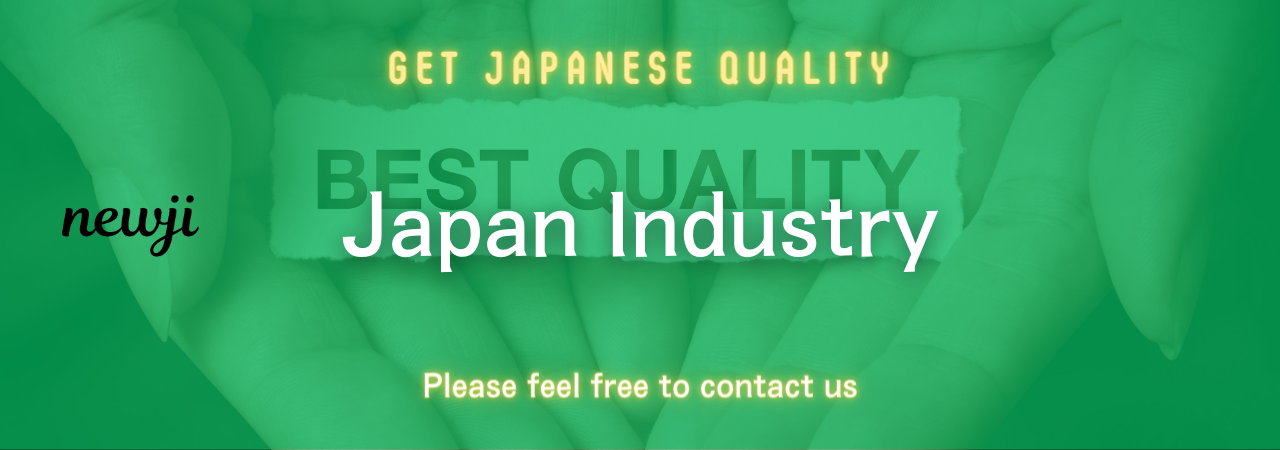
In today’s rapidly evolving manufacturing landscape, the digital supply chain twin has emerged as a crucial component for enterprises striving to maintain and enhance their competitiveness. This revolutionary concept involves creating a digital replica of the physical supply chain, integrating data from various sources to provide a comprehensive and real-time view of operations. By leveraging the digital supply chain twin, manufacturers can achieve greater visibility, agility, and efficiency, significantly boosting their competitiveness in the market.
The digital supply chain twin uses advanced technologies, such as the Internet of Things (IoT), artificial intelligence (AI), and machine learning, to collect and analyze data from every stage of the supply chain. This enables manufacturers to make informed decisions, optimize processes, and predict potential disruptions before they occur. Here’s how leveraging the digital supply chain twin can enhance competitiveness in manufacturing:
Enhanced Visibility and Transparency
One of the key benefits of the digital supply chain twin is the enhanced visibility it provides. By integrating data from various supply chain nodes, manufacturers can obtain a holistic view of their operations. This real-time insight allows them to identify bottlenecks, monitor inventory levels, track shipments, and manage supplier performance more effectively. This level of transparency helps manufacturers to respond swiftly to changes, reducing lead times and improving overall efficiency.
Improved Decision-Making
With the digital supply chain twin, manufacturers have access to a wealth of data that can inform decision-making at every level. By analyzing this data, manufacturers can identify patterns, trends, and anomalies that may impact their operations. For example, they can predict demand fluctuations, optimize production schedules, and manage inventory more efficiently. The ability to make data-driven decisions not only improves operational efficiency but also enhances the agility and responsiveness of the supply chain.
Proactive Risk Management
Risk management is a critical component of supply chain management. Disruptions, whether due to natural disasters, geopolitical events, or supplier issues, can have severe consequences for manufacturers. The digital supply chain twin allows manufacturers to proactively manage risks by identifying potential threats and implementing mitigation strategies. By simulating various scenarios, manufacturers can assess the impact of disruptions and develop contingency plans to minimize their effects on operations.
Optimized Processes and Cost Reduction
The digital supply chain twin enables manufacturers to optimize their processes by identifying inefficiencies and areas for improvement. By analyzing data on production, transportation, and inventory management, manufacturers can streamline operations and reduce costs. For example, they can optimize routing and scheduling to minimize transportation costs, reduce excess inventory levels, and improve asset utilization. These optimizations not only lower operational costs but also enhance the overall performance and competitiveness of the supply chain.
Enhanced Collaboration and Communication
The digital supply chain twin facilitates enhanced collaboration and communication among supply chain stakeholders. By providing a centralized platform for data sharing, manufacturers, suppliers, and customers can collaborate more effectively. This improved communication helps to align objectives, streamline workflows, and resolve issues more quickly. Enhanced collaboration not only improves operational efficiency but also fosters stronger relationships with suppliers and customers, contributing to the competitiveness of the manufacturing enterprise.
Predictive Maintenance
Predictive maintenance is another area where the digital supply chain twin can significantly enhance competitiveness. By continuously monitoring the condition of equipment and machinery, manufacturers can predict when maintenance is required and schedule it accordingly. This proactive approach to maintenance helps to prevent equipment failures, reduce downtime, and extend the lifespan of assets. As a result, manufacturers can maintain high levels of productivity and reduce maintenance costs, further enhancing their competitiveness.
Sustainable and Resilient Supply Chain
Sustainability and resilience are becoming increasingly important considerations for manufacturers. The digital supply chain twin can help manufacturers to create more sustainable and resilient supply chains by optimizing resource utilization, reducing waste, and minimizing the environmental impact of operations. For example, manufacturers can use data to identify opportunities for energy savings, reduce carbon emissions, and implement sustainable sourcing practices. Additionally, the ability to simulate various scenarios enables manufacturers to build more resilient supply chains that can withstand disruptions and adapt to changing conditions.
Real-Time Performance Monitoring
Real-time performance monitoring is a critical advantage offered by the digital supply chain twin. Manufacturers can track key performance indicators (KPIs) such as production efficiency, order fulfillment rates, and delivery times in real-time. This continuous monitoring allows manufacturers to identify deviations from targets and take corrective actions promptly. By maintaining high levels of performance, manufacturers can ensure customer satisfaction, build a strong reputation, and enhance their competitiveness in the market.
Conclusion
The digital supply chain twin is a game-changer for manufacturers aiming to enhance their competitiveness in a rapidly evolving industry. By leveraging advanced technologies to create a digital replica of the physical supply chain, manufacturers can gain unprecedented visibility, make informed decisions, manage risks proactively, optimize processes, and foster collaboration. The ability to monitor performance in real-time, implement predictive maintenance, and build sustainable and resilient supply chains further contributes to the competitiveness of manufacturing enterprises.
As the manufacturing landscape continues to evolve, the adoption of the digital supply chain twin will become increasingly essential for staying ahead of the competition. By embracing this innovative approach, manufacturers can unlock new opportunities for growth, efficiency, and sustainability, positioning themselves as leaders in the industry.
資料ダウンロード
QCD調達購買管理クラウド「newji」は、調達購買部門で必要なQCD管理全てを備えた、現場特化型兼クラウド型の今世紀最高の購買管理システムとなります。
ユーザー登録
調達購買業務の効率化だけでなく、システムを導入することで、コスト削減や製品・資材のステータス可視化のほか、属人化していた購買情報の共有化による内部不正防止や統制にも役立ちます。
NEWJI DX
製造業に特化したデジタルトランスフォーメーション(DX)の実現を目指す請負開発型のコンサルティングサービスです。AI、iPaaS、および先端の技術を駆使して、製造プロセスの効率化、業務効率化、チームワーク強化、コスト削減、品質向上を実現します。このサービスは、製造業の課題を深く理解し、それに対する最適なデジタルソリューションを提供することで、企業が持続的な成長とイノベーションを達成できるようサポートします。
オンライン講座
製造業、主に購買・調達部門にお勤めの方々に向けた情報を配信しております。
新任の方やベテランの方、管理職を対象とした幅広いコンテンツをご用意しております。
お問い合わせ
コストダウンが利益に直結する術だと理解していても、なかなか前に進めることができない状況。そんな時は、newjiのコストダウン自動化機能で大きく利益貢献しよう!
(Β版非公開)