- お役立ち記事
- LMS for Supply Chain Visibility in Manufacturing
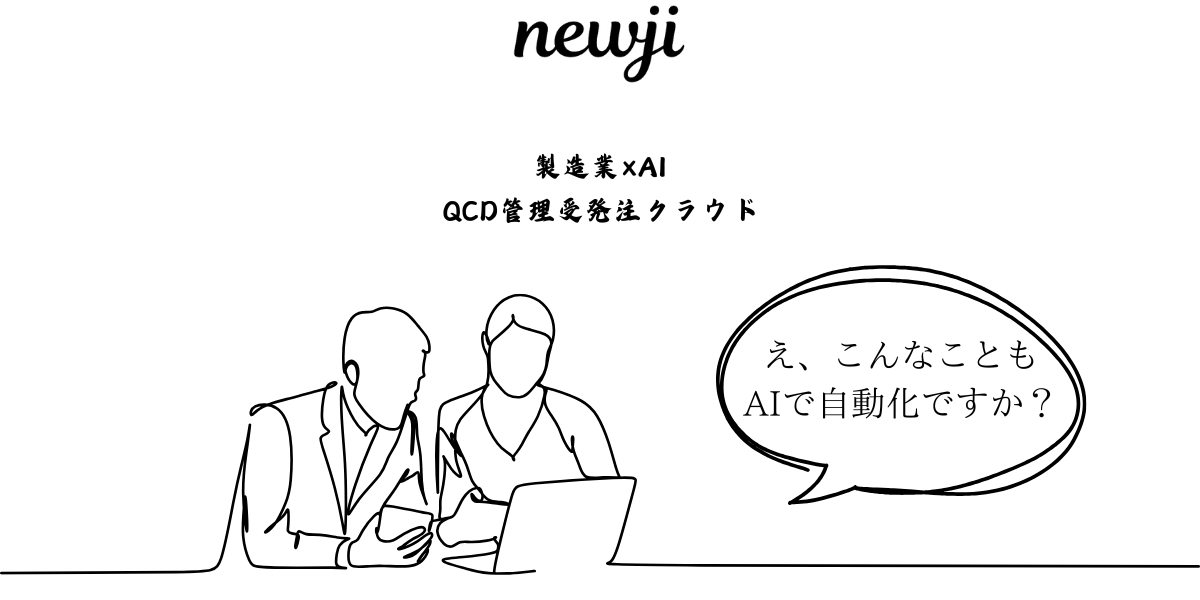
LMS for Supply Chain Visibility in Manufacturing
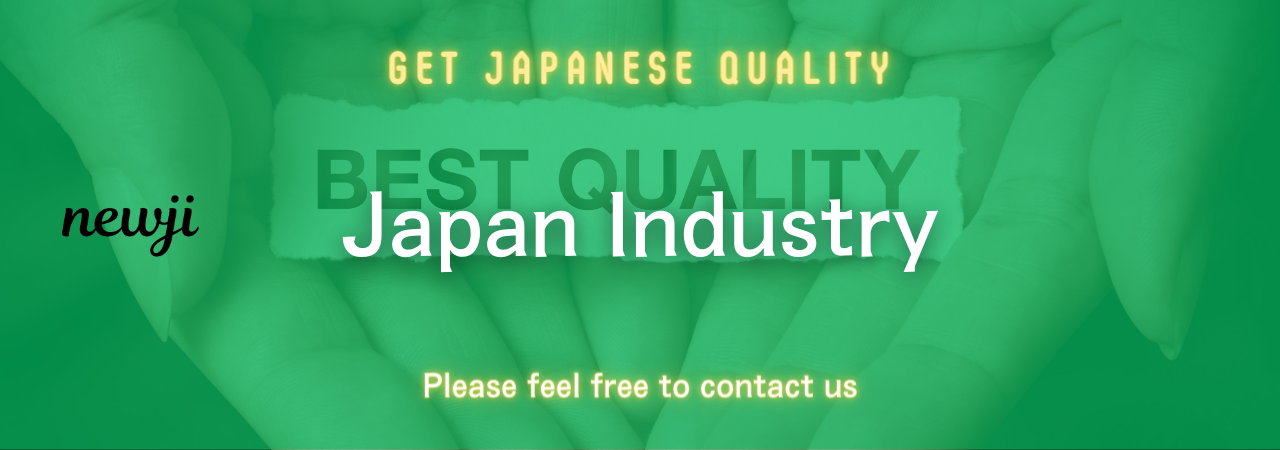
目次
What is Supply Chain Visibility?
Supply chain visibility refers to the ability of a business to track and monitor various processes within its supply chain, from raw material sourcing to product delivery.
It is essential for manufacturers to have a clear view of their supply chains to ensure smooth operations, minimize delays, and reduce costs.
In today’s highly competitive market, the absence of supply chain visibility can lead to inefficiencies, customer dissatisfaction, and increased risks.
With enhanced visibility, manufacturers can efficiently manage their inventories, forecast demand more accurately, and streamline their operations.
The Role of LMS in Supply Chain Visibility
A Learning Management System (LMS) in the manufacturing industry can play a pivotal role in enhancing supply chain visibility.
While traditionally used for managing employee training, LMS technology extends its benefits to ensuring that staff are knowledgeable about the supply chain and equipped to handle supply chain disruptions effectively.
By providing access to training content, real-time data, and predictive analytics, LMS can offer critical insights into various aspects of the supply chain.
How LMS Enhances Communication
One of the most significant ways LMS aids supply chain visibility is by improving communication across the manufacturing process.
Through a centralized platform, employees from different departments can communicate and share essential updates.
For instance, real-time notifications can alert staff to changes in inventory levels or potential delays in shipping.
This instant communication reduces lag times and allows quick adjustments, thereby maintaining continuity of operations.
Training and Development through LMS
LMS also supports supply chain visibility by offering robust training modules tailored for supply chain management.
Training programs can educate employees about the importance of maintaining accurate records, the impact of shortages, and how to use technological tools that support supply chain activities.
Interactive courses and simulations can prepare workers for potential disruptions and enhance their problem-solving skills.
Benefits of LMS in Manufacturing Supply Chains
Manufacturers using LMS technology for supply chain management experience numerous benefits.
It has revolutionized traditional supply chain management methods by providing tools for comprehensive oversight.
Real-Time Monitoring and Data Analysis
An LMS allows manufacturers to monitor supply chain activities in real-time.
This contributes to faster decision-making and reduces the time taken to identify and rectify supply chain issues.
With data analytics tools embedded within the LMS, companies can process information quickly and gain insights into patterns and trends that affect supply chain efficiency.
Predictive analytics can forecast demand or potential issues, allowing managers to proactively address them.
Enhanced Collaboration
LMS enables greater collaboration among teams involved in the supply chain.
When everyone from procurement to distribution has access to the same data, it fosters transparency and a unified approach to solving problems.
Collaborative tools within an LMS can also aid in supplier management by ensuring that suppliers are informed and agile in response to changing needs.
Implementing LMS for Improved Supply Chain Visibility
Successfully integrating an LMS into the supply chain starts with understanding the specific needs of your manufacturing operations.
Setting Clear Objectives
Before implementing an LMS, it is crucial to define clear objectives.
Determine what you want to achieve, whether it’s improved inventory management, faster production times, or enhanced supplier relationships.
Setting these goals will guide the selection of appropriate LMS features and functionalities.
Integration with Existing Systems
An LMS should seamlessly integrate with existing enterprise systems such as ERP (Enterprise Resource Planning) or SCM (Supply Chain Management) software.
This integration ensures that all data is consolidated, providing a holistic view of operations and facilitating more strategic decision-making.
Training and Support
Emphasize comprehensive training for all employees on how to use the new LMS effectively.
Continuous support should also be provided to address any challenges that arise post-implementation.
Trainings not only aid in maximizing the utility of the LMS but also in aligning staff with the overall objectives of enhancing supply chain visibility.
Conclusion
Incorporating a Learning Management System into manufacturing processes can significantly enhance supply chain visibility.
By improving communication, offering tailored training programs, and utilizing real-time data and analytics, an LMS can streamline operations and foster proactive decision-making.
For manufacturers aiming to maintain a competitive edge and meet consumer demands efficiently, investing in LMS technology proves to be a strategic move that can lead to significant operational improvements and cost savings.
資料ダウンロード
QCD調達購買管理クラウド「newji」は、調達購買部門で必要なQCD管理全てを備えた、現場特化型兼クラウド型の今世紀最高の購買管理システムとなります。
ユーザー登録
調達購買業務の効率化だけでなく、システムを導入することで、コスト削減や製品・資材のステータス可視化のほか、属人化していた購買情報の共有化による内部不正防止や統制にも役立ちます。
NEWJI DX
製造業に特化したデジタルトランスフォーメーション(DX)の実現を目指す請負開発型のコンサルティングサービスです。AI、iPaaS、および先端の技術を駆使して、製造プロセスの効率化、業務効率化、チームワーク強化、コスト削減、品質向上を実現します。このサービスは、製造業の課題を深く理解し、それに対する最適なデジタルソリューションを提供することで、企業が持続的な成長とイノベーションを達成できるようサポートします。
オンライン講座
製造業、主に購買・調達部門にお勤めの方々に向けた情報を配信しております。
新任の方やベテランの方、管理職を対象とした幅広いコンテンツをご用意しております。
お問い合わせ
コストダウンが利益に直結する術だと理解していても、なかなか前に進めることができない状況。そんな時は、newjiのコストダウン自動化機能で大きく利益貢献しよう!
(Β版非公開)