- お役立ち記事
- Logistics challenges faced by purchasing departments and methods to improve efficiency
月間76,176名の
製造業ご担当者様が閲覧しています*
*2025年3月31日現在のGoogle Analyticsのデータより
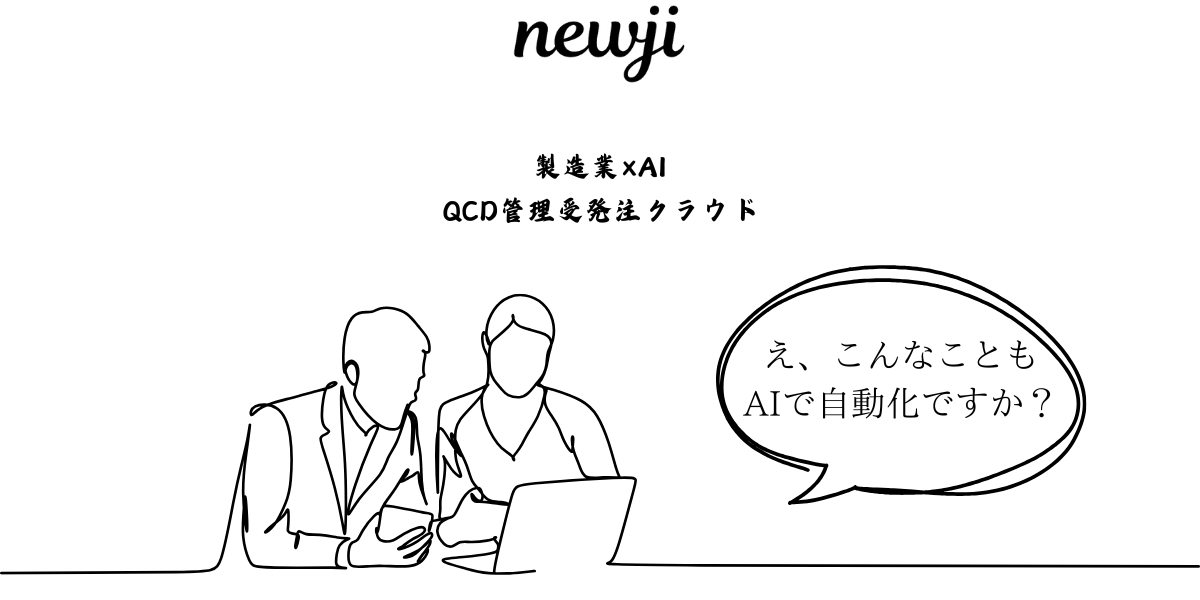
Logistics challenges faced by purchasing departments and methods to improve efficiency
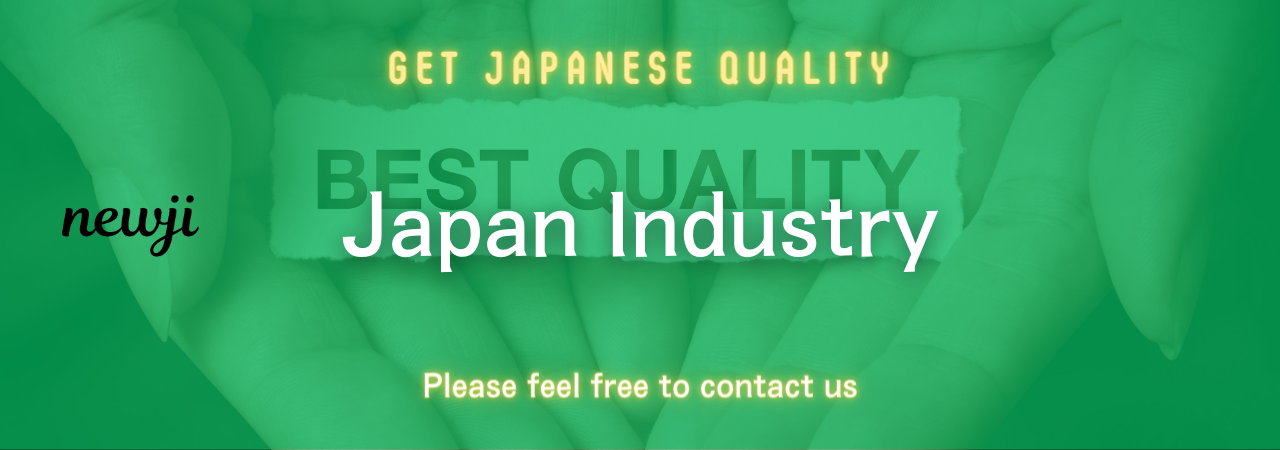
Understanding Logistics Challenges in Purchasing Departments
Purchasing departments play a critical role in the supply chain of any organization.
Their effectiveness directly influences a company’s ability to meet customer demands, manage costs, and maintain a competitive edge.
However, they face a variety of logistics challenges that can impact their performance.
These challenges include supply chain disruptions, fluctuating demand, and logistical inefficiencies that hamper the procurement process.
By understanding these obstacles, purchasing departments can develop strategies to improve efficiency and adaptability.
This article explores common logistics challenges faced by purchasing departments and offers methods to enhance their efficiency.
Supply Chain Disruptions
In today’s globalized economy, supply chains often span multiple countries and continents.
This complexity makes them vulnerable to disruptions caused by various factors, such as natural disasters, geopolitical issues, and pandemics.
When such disruptions occur, purchasing departments may struggle to obtain the necessary products or materials on time.
A delay in acquiring essential goods can lead to production halts, increased costs due to expedited shipping, or lost sales.
To mitigate these impacts, purchasing departments need to adopt proactive risk management strategies.
One approach is to diversify suppliers to ensure that reliance on a single provider does not jeopardize supply continuity.
Additionally, keeping safety stock, or buffer inventory, can help cushion the impact of unexpected disruptions.
Regularly reviewing and updating risk management plans ensures preparedness against potential supply chain crises.
Fluctuating Demand
Purchasing departments often encounter fluctuating demand, making it difficult to forecast requirements accurately.
This unpredictability can lead to overstocking or understocking, both of which have financial ramifications.
Overstocking results in excess inventory that ties up capital and incurs additional storage costs, while understocking affects the ability to meet customer demand, resulting in missed opportunities and dissatisfied customers.
To overcome this challenge, purchasing departments can implement demand forecasting techniques that help predict future purchasing needs more accurately.
Leveraging historical data, market trends, and advanced analytics can provide valuable insights that inform purchasing decisions.
Collaborating closely with sales and marketing departments also helps align purchasing strategies with anticipated changes in demand.
Implementing just-in-time (JIT) inventory practices adjusts purchasing schedules to actual sales patterns, minimizing the risk of excess inventory and optimizing resource allocation.
Logistical Inefficiencies
Logistical inefficiencies, such as delays in transportation or warehousing, affect purchasing departments significantly.
Inefficient logistics can result in longer lead times, higher transportation costs, and an inability to maintain optimal stock levels.
These issues can be compounded by challenges such as inadequate tracking systems, poor route planning, or reliance on outdated technologies.
Improving logistical efficiency requires an investment in technology and infrastructure.
Purchasing departments can leverage supply chain management software to enhance visibility into inventory levels, track shipments in real time, and optimize routing.
Implementing automation in order processing and inventory management can reduce human errors and speed up transactions.
Collaborating with logistics partners to streamline processes and share real-time data also helps improve coordination and communication across the supply chain.
Methods to Improve Purchasing Department Efficiency
To address the aforementioned logistics challenges, purchasing departments can adopt several methods to improve efficiency.
Embrace Technology and Data Analytics
Investing in new technologies and data analytics can significantly enhance the efficiency of purchasing departments.
Digital tools such as enterprise resource planning (ERP) systems integrate purchasing data with other business functions, facilitating smoother operations.
Advanced analytics provide insights that help anticipate demand fluctuations, identify supply chain bottlenecks, and inform strategic purchasing decisions.
Cloud-based solutions allow for real-time information sharing and collaboration between suppliers, purchasing agents, and other stakeholders.
Enhance Supplier Relationships
Strong relationships with suppliers are crucial for ensuring a reliable supply of goods.
Frequent communication and collaboration with suppliers can lead to mutually beneficial arrangements and improved reliability.
Establishing clear performance metrics and regularly reviewing supplier performance helps maintain high standards of quality and service.
Exploring strategic partnerships, such as vendor-managed inventory (VMI) or joint development initiatives, further strengthens supplier relationships and enhances supply chain resilience.
Focus on Sustainability and Ethical Sourcing
Consumers and stakeholders are increasingly demanding that companies prioritize sustainability and ethical sourcing.
Purchasing departments can improve efficiency while meeting these expectations by sourcing materials from environmentally and socially responsible vendors.
Implementing sustainable procurement practices reduces waste and improves resource efficiency.
This approach can also foster innovation and attract socially conscious customers, adding value to the organization.
Implement Continuous Improvement Practices
Continuous improvement methodologies, such as Lean and Six Sigma, can help purchasing departments identify inefficiencies and optimize processes.
By fostering a culture of continuous improvement, organizations encourage employees to identify and address inefficiencies at all levels.
Regular process reviews, streamlined workflows, and employee training are key components of a successful continuous improvement strategy.
By incorporating employee feedback and encouraging innovation, purchasing departments can adapt to evolving challenges and enhance operational efficiency.
Through a combination of technology adoption, relationship management, and process optimization, purchasing departments can rise above logistical challenges and achieve greater efficiency.
By focusing on these methods, organizations can improve their supply chain performance, reduce costs, and better serve their customers.
資料ダウンロード
QCD管理受発注クラウド「newji」は、受発注部門で必要なQCD管理全てを備えた、現場特化型兼クラウド型の今世紀最高の受発注管理システムとなります。
ユーザー登録
受発注業務の効率化だけでなく、システムを導入することで、コスト削減や製品・資材のステータス可視化のほか、属人化していた受発注情報の共有化による内部不正防止や統制にも役立ちます。
NEWJI DX
製造業に特化したデジタルトランスフォーメーション(DX)の実現を目指す請負開発型のコンサルティングサービスです。AI、iPaaS、および先端の技術を駆使して、製造プロセスの効率化、業務効率化、チームワーク強化、コスト削減、品質向上を実現します。このサービスは、製造業の課題を深く理解し、それに対する最適なデジタルソリューションを提供することで、企業が持続的な成長とイノベーションを達成できるようサポートします。
製造業ニュース解説
製造業、主に購買・調達部門にお勤めの方々に向けた情報を配信しております。
新任の方やベテランの方、管理職を対象とした幅広いコンテンツをご用意しております。
お問い合わせ
コストダウンが利益に直結する術だと理解していても、なかなか前に進めることができない状況。そんな時は、newjiのコストダウン自動化機能で大きく利益貢献しよう!
(β版非公開)