- お役立ち記事
- Logistics management and purchasing department cooperation methods to reduce transportation risks
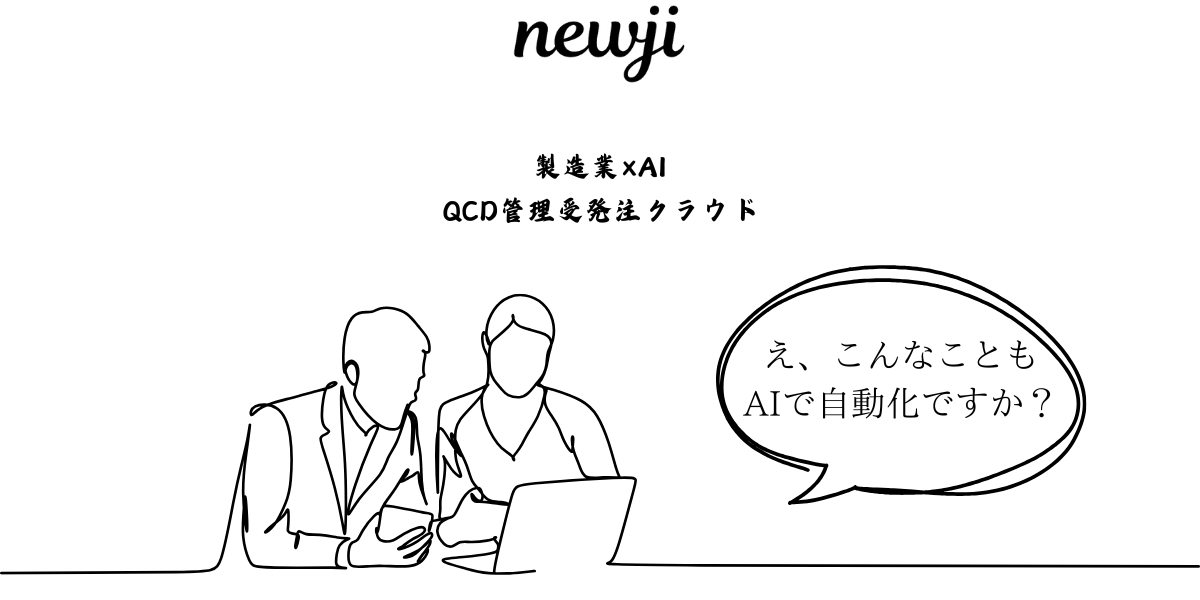
Logistics management and purchasing department cooperation methods to reduce transportation risks
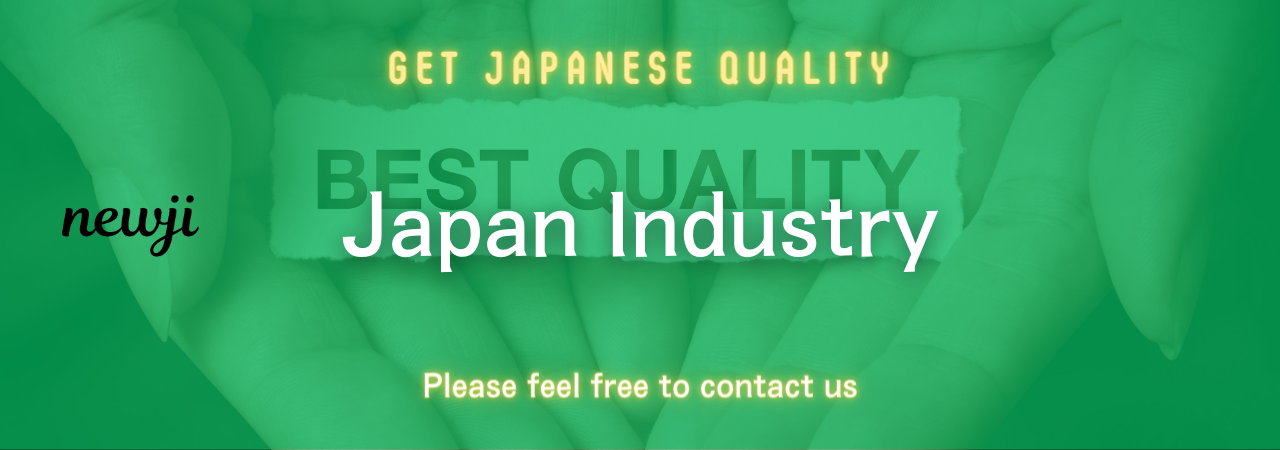
目次
Understanding the Role of Logistics Management
Logistics management is the backbone of any supply chain operation, ensuring that goods flow efficiently from the point of origin to the final destination.
It involves carefully coordinating different functions, including transportation, warehousing, inventory management, and order processing, to meet customer demands effectively.
A key element of logistics management is minimizing risks associated with transportation, which can impact delivery times, costs, and customer satisfaction.
Understanding the intricacies involved in this process is crucial for developing strategies that foster successful cooperation with purchasing departments.
Identifying Transportation Risks
To effectively mitigate transportation risks, it is crucial to first identify the potential challenges that may arise.
Transportation risks can vary based on the type of goods being moved, the geographical areas involved, and the modes of transport used.
Common challenges include delays due to weather or traffic conditions, accidents, equipment failures, and regulatory compliance issues.
Financial risks such as fluctuating fuel prices or changes in tariffs can also impact the cost of transportation significantly.
By identifying these risks early, both the logistics management and the purchasing department can develop strategies to address them collaboratively.
The Role of the Purchasing Department
The purchasing department plays a critical role in the supply chain by ensuring that the organization obtains the necessary resources to meet production and customer needs.
By coordinating closely with logistics management, the purchasing department can help mitigate transportation risks.
This partnership involves aligning purchase orders with transportation schedules, choosing reliable suppliers, and negotiating terms that include risk-sharing provisions.
By working together, these departments can anticipate potential disruptions and plan accordingly to ensure a smooth flow of goods.
Developing Effective Collaboration
For successful cooperation between logistics management and the purchasing department, clear communication and shared objectives are essential.
Regular meetings and updates can keep all parties informed about supply chain activities, potential risks, and changes in the market that may affect operations.
Joint risk assessments should be conducted to identify vulnerabilities and develop mitigation strategies.
By creating a comprehensive risk management plan, both departments can proactively address issues that may arise during transportation.
Implementing Technology Solutions
In today’s fast-paced world, technology plays a vital role in enhancing supply chain operations.
Logistics management and purchasing departments can harness various technological solutions to improve transparency, increase efficiency, and reduce transportation risks.
Real-time tracking systems allow stakeholders to monitor shipments, addressing potential delays and rerouting as necessary.
Inventory management software can help both departments keep track of stock levels and coordinate reorders strategically.
Additionally, predictive analytics can identify trends and suggest preventive measures to mitigate identified risks.
Integrating these technologies can streamline processes and improve the overall effectiveness of the collaboration.
Optimizing Supplier Performance
Effective supplier management is another critical component in reducing transportation risks.
The purchasing department should work closely with logistics management to evaluate supplier performance regularly.
This involves assessing delivery reliability, quality of goods, and adherence to agreed terms.
Establishing key performance indicators (KPIs) helps benchmark supplier performance and identify areas needing improvement.
In cases where suppliers do not meet expectations, it may be necessary to explore alternative sources or negotiate new terms that incentivize compliance.
This ongoing evaluation ensures that suppliers play a positive role in minimizing transportation risks.
Adapting to Market Changes
The supply chain landscape is constantly evolving, influenced by technological advancements, market demands, and regulatory shifts.
To keep pace, logistics management and the purchasing department must adopt a flexible approach to address transportation risks.
Continuous monitoring of market trends allows these departments to anticipate changes, such as new trade policies or environmental regulations, that could impact operations.
Being prepared for such changes helps both entities adapt their strategies effectively, ensuring continued efficiency and cost control.
Flexibility is key to navigating this dynamic environment and maintaining a smooth flow of goods within the supply chain.
Fostering a Culture of Continuous Improvement
A commitment to continuous improvement is essential for reducing transportation risks over the long term.
Both logistics management and the purchasing department should foster a culture that encourages innovation and embraces best practices.
Regular training and development opportunities enable team members to stay informed about industry developments and emerging technologies.
Feedback loops and process reviews can identify areas for improvement, driving ongoing enhancements to existing procedures.
By prioritizing continuous improvement, organizations can ensure that they remain agile and competitive, reducing transportation risks effectively.
Conclusion
Reducing transportation risks requires a well-coordinated effort between logistics management and the purchasing department.
By identifying transportation challenges, collaborating effectively, implementing technology, optimizing supplier performance, and adapting to market changes, these departments can succeed in mitigating risks.
A proactive approach, supported by continuous improvement, will equip organizations to navigate the complexities of the supply chain efficiently and deliver seamless service to their customers.
資料ダウンロード
QCD調達購買管理クラウド「newji」は、調達購買部門で必要なQCD管理全てを備えた、現場特化型兼クラウド型の今世紀最高の購買管理システムとなります。
ユーザー登録
調達購買業務の効率化だけでなく、システムを導入することで、コスト削減や製品・資材のステータス可視化のほか、属人化していた購買情報の共有化による内部不正防止や統制にも役立ちます。
NEWJI DX
製造業に特化したデジタルトランスフォーメーション(DX)の実現を目指す請負開発型のコンサルティングサービスです。AI、iPaaS、および先端の技術を駆使して、製造プロセスの効率化、業務効率化、チームワーク強化、コスト削減、品質向上を実現します。このサービスは、製造業の課題を深く理解し、それに対する最適なデジタルソリューションを提供することで、企業が持続的な成長とイノベーションを達成できるようサポートします。
オンライン講座
製造業、主に購買・調達部門にお勤めの方々に向けた情報を配信しております。
新任の方やベテランの方、管理職を対象とした幅広いコンテンツをご用意しております。
お問い合わせ
コストダウンが利益に直結する術だと理解していても、なかなか前に進めることができない状況。そんな時は、newjiのコストダウン自動化機能で大きく利益貢献しよう!
(Β版非公開)