- お役立ち記事
- Logistics strategy proposed by the purchasing department that enables lead time reduction
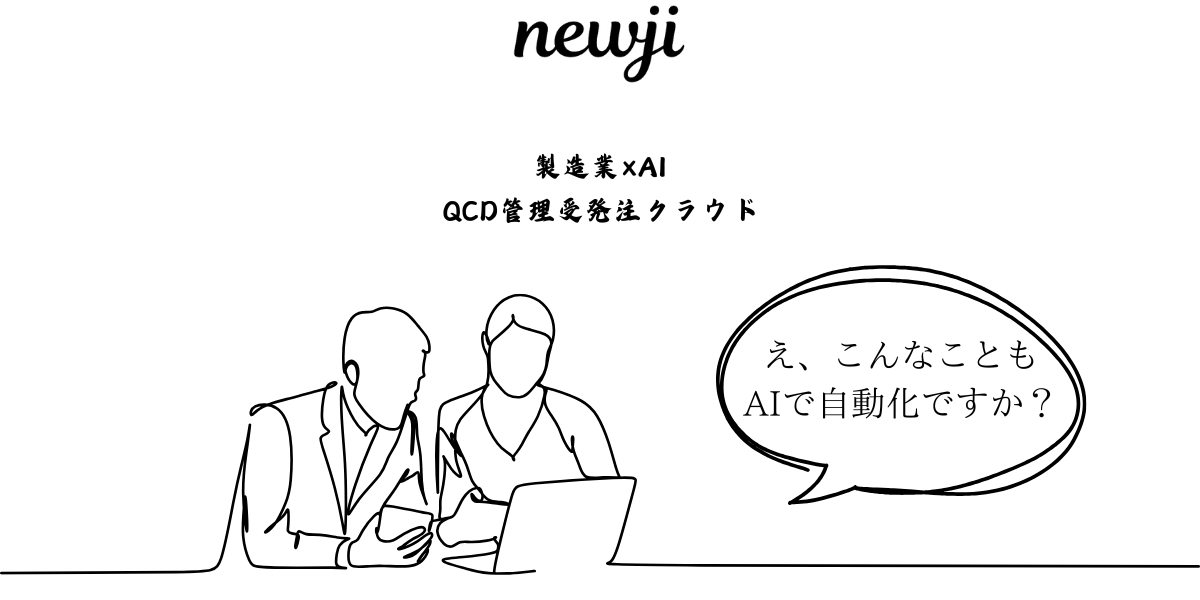
Logistics strategy proposed by the purchasing department that enables lead time reduction
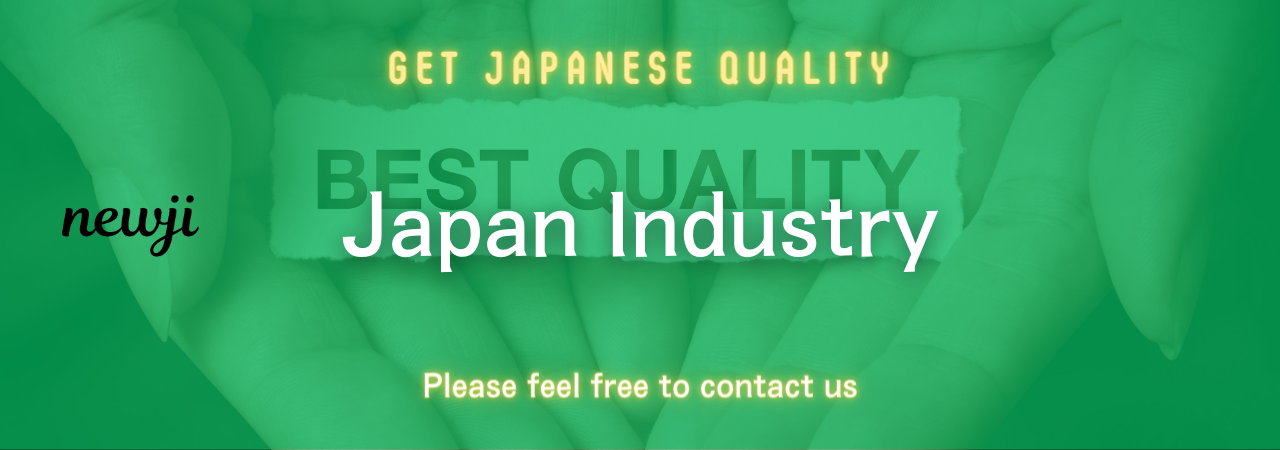
目次
Understanding Lead Time Reduction
The concept of lead time reduction is a cornerstone of efficient logistics strategy.
In simpler terms, lead time is the period it takes from the initiation of an order to its final delivery.
For businesses, especially those in procurement and logistics, reducing this time can be crucial.
It not only enhances customer satisfaction but also improves overall productivity and cuts costs.
The purchasing department plays a pivotal role in shaping strategies that focus on minimizing lead time.
By optimizing various processes, they ensure that goods move faster through the supply chain.
However, achieving this requires a well-thought-out logistics plan.
The Role of the Purchasing Department
The purchasing department often acts as the backbone of an organization’s supply chain operations.
Their primary role includes sourcing goods and services, negotiating with suppliers, and ensuring timely deliveries.
By developing robust logistics strategies, the purchasing department significantly contributes to lead time reduction.
Building Strong Relationships with Suppliers
One effective strategy for reducing lead times is forging strong relationships with suppliers.
When the purchasing department maintains good rapport with vendors, they are more likely to respond promptly to orders.
This level of partnership can lead to better negotiation terms, such as early deliveries or prioritization of your orders.
Additionally, collaborative relationships often result in quicker conflict resolution if any issues arise.
Streamlining Order Processes
Another strategy is the streamlining of order processes.
This involves evaluating current systems and identifying bottlenecks that may cause delays.
Once identified, the purchasing department can implement solutions to streamline these processes.
For example, automating purchase orders can significantly reduce administrative time, leading to quicker order placements.
Implementing Forecasting Methods
Accurate forecasting is essential for effective lead time management.
The purchasing department should employ advanced forecasting methods to predict demand accurately.
This allows for better preparation and timely ordering of stock.
When demand is anticipated correctly, rush orders—which often come with longer lead times—can be minimized.
Technology as a Catalyst for Change
Technology plays a critical role in reducing lead times.
The purchasing department can leverage technology to optimize logistics and procurement processes.
Integrating Supply Chain Management Software
Adopting comprehensive supply chain management software can immensely aid in reducing lead times.
These platforms enable real-time tracking of orders, inventory management, and supplier coordination.
By having a centralized system, the purchasing department can oversee the entire supply chain in real-time, making it easier to identify and address any delays quickly.
Utilizing Data Analytics
Data analytics is invaluable for understanding trends and improving lead times.
The purchasing department can analyze past data to identify patterns that lead to delays.
By understanding these patterns, more informed strategies can be formulated to address and avoid potential bottlenecks.
Effective Communication and Collaboration
Another crucial aspect of reducing lead times is ensuring effective communication across all departments.
The purchasing department must work closely with other teams, such as operations and sales, to align goals.
Cross-Departmental Collaboration
Cross-departmental collaboration ensures that everyone is on the same page regarding order priorities and logistics processes.
Regular meetings and updates help maintain transparency and allow for joint problem-solving, which can speed up processes significantly.
Setting Clear Expectations
Setting clear expectations with suppliers and internal teams is vital.
This includes delivery timelines, product specifications, and potential challenges.
Clear communication helps prevent misunderstandings that could cause delays.
Continuous Improvement and Training
To maintain reduced lead times, the purchasing department should focus on continuous improvement and employee training.
Regular Process Reviews
Regularly reviewing and analyzing logistics processes help identify new areas for improvement.
By staying flexible and open to change, the purchasing department can continuously streamline operations for better efficiency.
Employee Training and Development
Investing in employee training ensures that staff members are equipped with the latest knowledge and skills.
This enables them to execute logistics strategies effectively and contribute to reducing lead times.
Benefits of Reducing Lead Times
Implementing an effective logistics strategy that focuses on reducing lead times offers several benefits to an organization.
Increased Customer Satisfaction
When orders are delivered promptly, customer satisfaction naturally increases.
Happy customers are more likely to become repeat buyers and recommend your business to others, directly impacting sales and revenue.
Cost Savings
Reducing lead times can also lead to significant cost savings.
Despite the initial investment in technology and process improvements, the long-term cost benefits such as reduced inventory holding costs and fewer rush shipments outweigh these expenses.
Competitive Advantage
Organizations that efficiently manage lead times position themselves ahead of competitors.
Faster delivery times can be a unique selling point, attracting more customers to your business over others.
In conclusion, by following these strategies, the purchasing department can play a crucial role in reducing lead times.
Whether through strong supplier relationships, technological integration, or fostering collaboration, the benefits of improved logistics efficiency are manifold.
Ultimately, this not only meets but exceeds customer expectations, setting a strong foundation for sustained business success.
資料ダウンロード
QCD調達購買管理クラウド「newji」は、調達購買部門で必要なQCD管理全てを備えた、現場特化型兼クラウド型の今世紀最高の購買管理システムとなります。
ユーザー登録
調達購買業務の効率化だけでなく、システムを導入することで、コスト削減や製品・資材のステータス可視化のほか、属人化していた購買情報の共有化による内部不正防止や統制にも役立ちます。
NEWJI DX
製造業に特化したデジタルトランスフォーメーション(DX)の実現を目指す請負開発型のコンサルティングサービスです。AI、iPaaS、および先端の技術を駆使して、製造プロセスの効率化、業務効率化、チームワーク強化、コスト削減、品質向上を実現します。このサービスは、製造業の課題を深く理解し、それに対する最適なデジタルソリューションを提供することで、企業が持続的な成長とイノベーションを達成できるようサポートします。
オンライン講座
製造業、主に購買・調達部門にお勤めの方々に向けた情報を配信しております。
新任の方やベテランの方、管理職を対象とした幅広いコンテンツをご用意しております。
お問い合わせ
コストダウンが利益に直結する術だと理解していても、なかなか前に進めることができない状況。そんな時は、newjiのコストダウン自動化機能で大きく利益貢献しよう!
(Β版非公開)