- お役立ち記事
- Lot Size Optimization for Cost Reduction: Planning Methods for Purchasing Managers
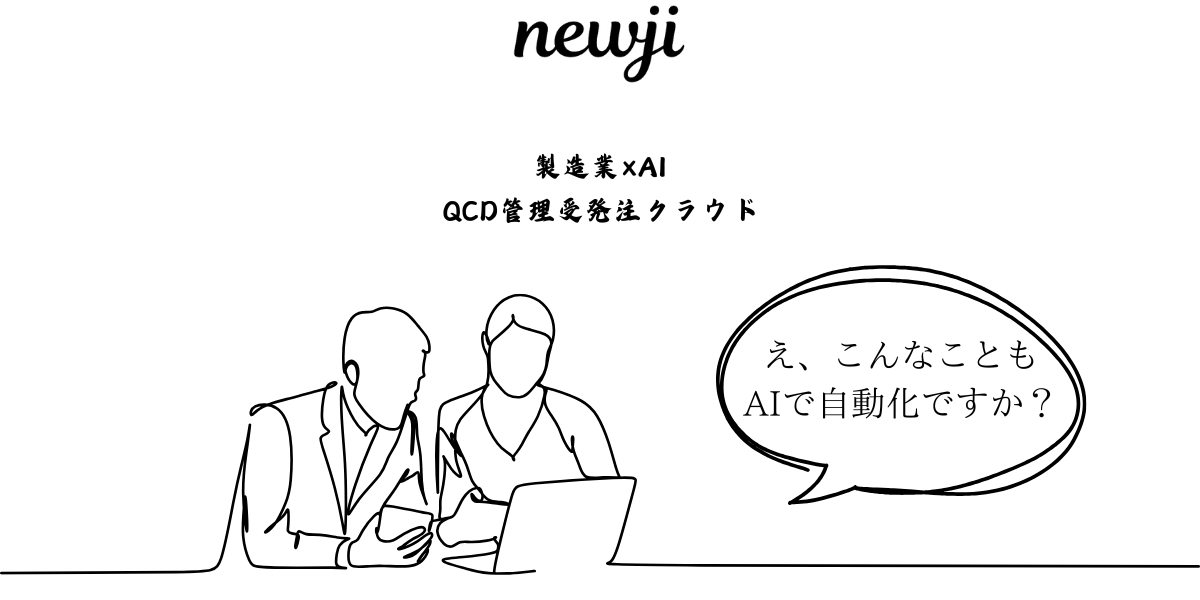
Lot Size Optimization for Cost Reduction: Planning Methods for Purchasing Managers
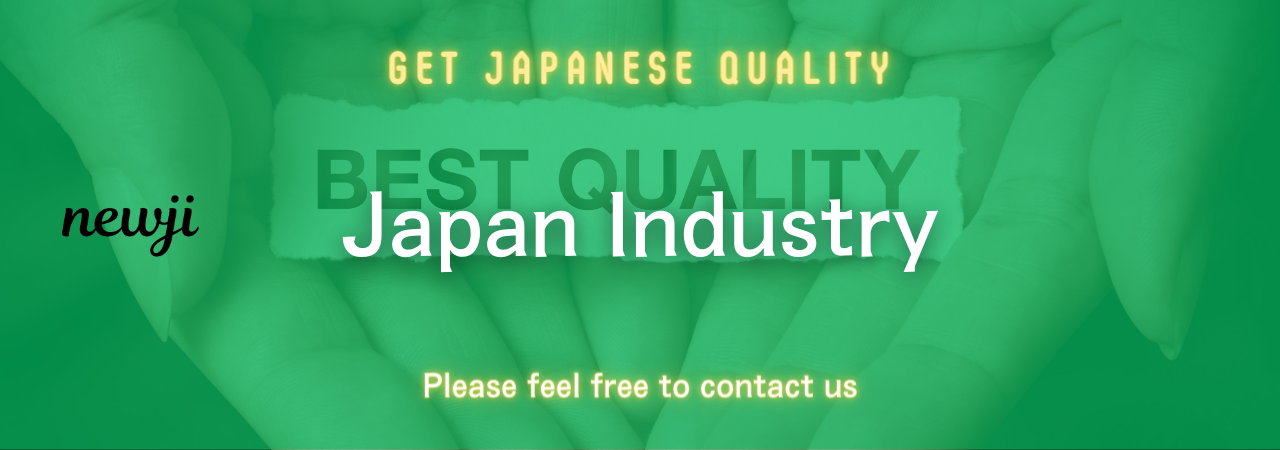
目次
Understanding Lot Size Optimization
Purchasing managers play a crucial role in ensuring the smooth operation of a company’s supply chain.
One of the key strategies they can employ to enhance efficiency and reduce costs is lot size optimization.
This involves determining the optimal order quantity that minimizes total costs, including holding and ordering expenses.
Understanding the basics of lot size optimization can significantly impact a company’s bottom line.
The Importance of Lot Size Optimization
Lot size optimization is essential because it directly impacts a company’s inventory costs.
Ordering too much can lead to high holding costs, while ordering too little can result in frequent purchasing and increased ordering costs.
Achieving an optimal balance helps companies maintain adequate stock levels while minimizing expenses.
Factors Influencing Lot Size
Several factors need to be considered when optimizing lot size.
These include demand variability, lead times, storage costs, and ordering expenses.
Purchasing managers must analyze these factors to determine the best lot size that aligns with company goals and market conditions.
Methods for Lot Size Optimization
There are several methods purchasing managers can use to optimize lot sizes.
Each method has its advantages and is suitable for different types of businesses.
Here are some common strategies:
Economic Order Quantity (EOQ)
The Economic Order Quantity (EOQ) model is one of the most widely used lot size optimization techniques.
It calculates the ideal order quantity that minimizes total inventory costs by balancing ordering and holding expenses.
EOQ takes into account factors such as demand rate, ordering cost, and holding cost.
The formula for EOQ is:
EOQ = √((2DS)/H)
Where:
– D = Demand rate (units per year)
– S = Ordering cost per order
– H = Holding cost per unit per year
This formula helps determine the most cost-effective order size, ensuring companies do not overstock or understock.
Just-In-Time (JIT) System
The Just-In-Time (JIT) system is another popular approach to lot size optimization.
JIT focuses on ordering inventory only as needed, reducing holding costs by minimizing excess stock.
In a JIT system, purchasing managers maintain close communication with suppliers to ensure timely delivery of materials and products.
This method is particularly effective in industries where demand can be predicted accurately, and lead times are short.
ABC Analysis
ABC analysis is a technique used to categorize inventory items into three categories: A, B, and C.
‘A’ items are high-value products with a low frequency of sales, ‘B’ items have medium sales frequency and value, and ‘C’ items are low-value products with high sales frequency.
Purchasing managers can use this analysis to prioritize resources and efforts.
By focusing on optimizing lot sizes for ‘A’ items, companies can significantly reduce costs, as these items often account for the most substantial portion of inventory expenses.
Technology and Lot Size Optimization
Advancements in technology have revolutionized lot size optimization.
Software solutions and algorithms can now analyze large data sets to provide insights into optimal order quantities.
These tools allow purchasing managers to make data-driven decisions, enhancing accuracy and efficiency.
Machine learning algorithms can predict demand patterns more precisely, allowing for better lot size optimization.
Additionally, inventory management systems integrate seamlessly with enterprise resource planning (ERP) systems, providing real-time data and automating lot size calculations.
Implementing Lot Size Optimization
Purchasing managers looking to implement lot size optimization should start by analyzing current inventory practices.
Identifying areas where costs can be reduced, or processes can be streamlined is crucial.
Engaging with internal stakeholders, such as finance and operations teams, can provide valuable insights and foster a collaborative approach to optimization.
Training staff on the latest tools and technologies can also support successful implementation.
Monitoring and Adjusting the Strategy
Once a lot size optimization strategy is in place, it is important to continuously monitor its effectiveness.
Market conditions and consumer demand can change, so purchasing managers must be prepared to adjust their strategies accordingly.
Regularly reviewing inventory performance data can highlight trends and areas for improvement.
Purchasing managers should be open to experimenting with different methods to find the most effective approach for their organization.
Benefits of Lot Size Optimization
Effective lot size optimization offers several benefits.
It leads to cost savings by reducing unnecessary holding and ordering expenses.
It also enhances supplier relationships, as companies can better manage their demands and lead times.
Additionally, lot size optimization improves inventory accuracy, reducing the risk of stockouts or overstocking.
Ultimately, purchasing managers can contribute to the company’s profitability and competitive advantage.
Conclusion
Lot size optimization is a powerful tool for purchasing managers seeking to reduce costs and improve efficiency.
By understanding the different methods available and leveraging technology, managers can implement effective strategies tailored to their company’s needs.
Ongoing monitoring and adjustments ensure that these strategies continue to deliver value in a dynamic market environment.
資料ダウンロード
QCD調達購買管理クラウド「newji」は、調達購買部門で必要なQCD管理全てを備えた、現場特化型兼クラウド型の今世紀最高の購買管理システムとなります。
ユーザー登録
調達購買業務の効率化だけでなく、システムを導入することで、コスト削減や製品・資材のステータス可視化のほか、属人化していた購買情報の共有化による内部不正防止や統制にも役立ちます。
NEWJI DX
製造業に特化したデジタルトランスフォーメーション(DX)の実現を目指す請負開発型のコンサルティングサービスです。AI、iPaaS、および先端の技術を駆使して、製造プロセスの効率化、業務効率化、チームワーク強化、コスト削減、品質向上を実現します。このサービスは、製造業の課題を深く理解し、それに対する最適なデジタルソリューションを提供することで、企業が持続的な成長とイノベーションを達成できるようサポートします。
オンライン講座
製造業、主に購買・調達部門にお勤めの方々に向けた情報を配信しております。
新任の方やベテランの方、管理職を対象とした幅広いコンテンツをご用意しております。
お問い合わせ
コストダウンが利益に直結する術だと理解していても、なかなか前に進めることができない状況。そんな時は、newjiのコストダウン自動化機能で大きく利益貢献しよう!
(Β版非公開)