- お役立ち記事
- Low-cost, high-quality parts production realized through trial production requests! Thorough explanation of successful cases of initial sample verification and improvement process
月間77,185名の
製造業ご担当者様が閲覧しています*
*2025年2月28日現在のGoogle Analyticsのデータより
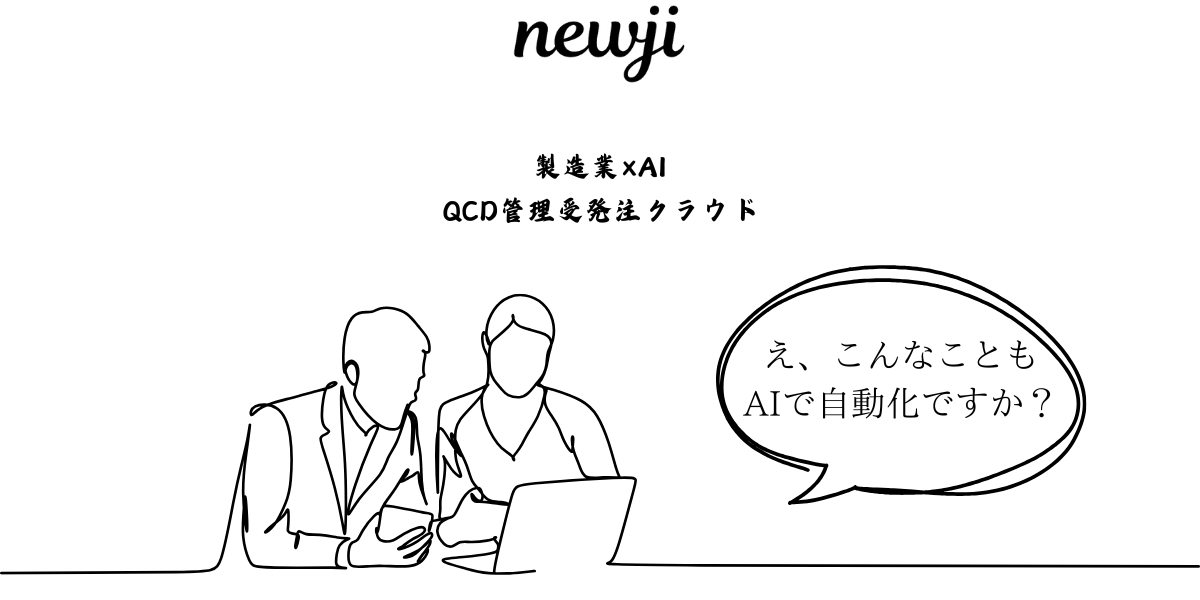
Low-cost, high-quality parts production realized through trial production requests! Thorough explanation of successful cases of initial sample verification and improvement process
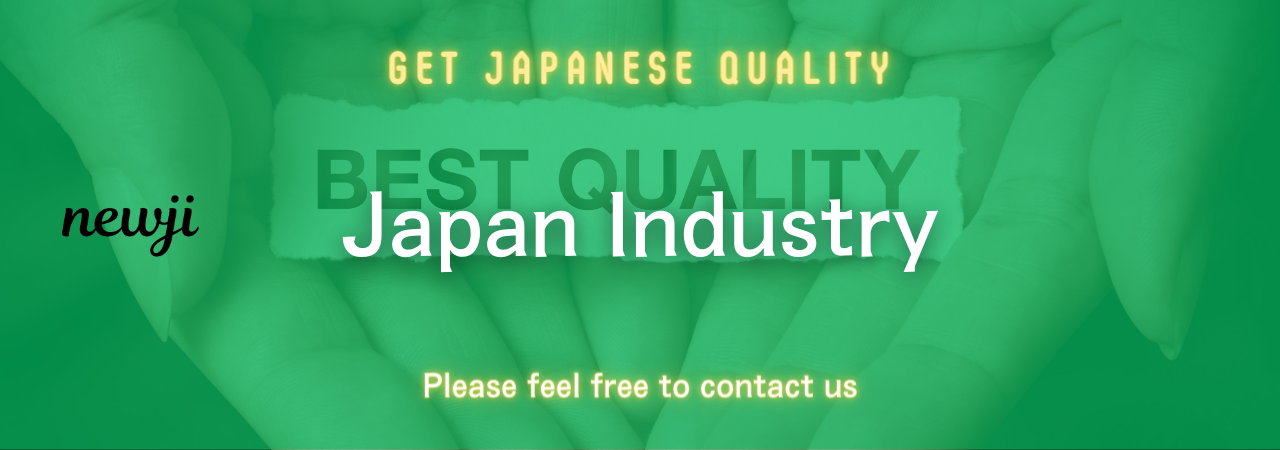
目次
Introduction to Low-Cost, High-Quality Parts Production
The manufacturing industry is constantly evolving, with companies seeking ways to improve efficiency while cutting costs.
One effective method to achieve this is through trial production requests.
This approach allows businesses to produce high-quality parts at a low cost, ensuring that their products meet market standards while reducing expenditures.
In this article, we will explore how trial production requests can lead to successful parts production, with a focus on initial sample verification and the improvement process.
Understanding Trial Production Requests
Trial production requests are a vital step in the manufacturing process.
They involve creating a small batch of parts, often prototypes, to test their design, functionality, and manufacturability before moving to full-scale production.
This step is crucial for identifying potential issues and making necessary adjustments early in the production process.
By investing time and resources into trial production, companies can avoid costly mistakes that may arise from launching full-scale production without adequate testing.
This method not only helps in maintaining quality standards but also reduces waste and overall production costs.
The Benefits of Trial Production
1. **Cost Effectiveness:** Trial production often requires fewer resources than full-scale production, allowing companies to conserve materials and labor.
2. **Quality Assurance:** By identifying and resolving issues during trial production, companies can ensure that their final products meet or exceed industry standards.
3. **Time Efficiency:** Addressing potential problems early in the process can prevent delays and ensure timely product delivery.
4. **Customization:** Trial production allows for easy adjustments and customization, ensuring that the final product aligns with customer specifications.
Initial Sample Verification
Once a trial production batch is complete, the next critical step is initial sample verification.
This involves rigorous testing and evaluation of the produced parts to ensure they meet the desired criteria.
Initial sample verification typically includes the following steps:
1. **Visual Inspection:** A thorough examination of the parts for any obvious defects or irregularities.
2. **Dimensional Analysis:** Measurements are taken to ensure the parts conform to the specified dimensions and tolerances.
3. **Material Testing:** Assessing the materials used to confirm they meet the necessary specifications for strength, durability, and other properties.
4. **Functional Testing:** Evaluating the performance of the parts under expected conditions to ensure they function correctly and efficiently.
By conducting these tests, manufacturers can identify any discrepancies and address them before mass production begins.
Case Study: A Success Story in Parts Production
Let’s take a look at a real-life example of how a company successfully used trial production and initial sample verification to improve their manufacturing process.
Company XYZ, a manufacturer of automotive components, faced challenges with delivering high-quality parts at a competitive price.
They decided to implement trial production requests as part of their development strategy.
By producing initial samples and conducting thorough tests, they identified several areas for improvement.
During the visual inspection, minor defects that could have impacted the part’s performance were found.
Dimensional analysis revealed slight deviations in measurements that could affect assembly.
Through material testing, it was discovered that an alternative, more cost-effective material could be used without compromising quality.
After addressing these issues, Company XYZ proceeded with a final trial production run, resulting in a set of high-quality parts ready for mass production.
This process not only ensured product quality but also reduced production costs, leading to increased customer satisfaction and market competitiveness.
Improvement Process
The improvement process is a crucial phase following initial sample verification.
It involves using the data and insights gathered during verification to refine and enhance the manufacturing process.
Key steps in this process include:
1. **Root Cause Analysis:** Identifying the underlying causes of any defects or issues observed during sample verification.
2. **Process Optimization:** Implementing changes to the manufacturing process to eliminate identified issues and improve efficiency.
3. **Design Modifications:** Making necessary adjustments to the product design to enhance performance and manufacturability.
4. **Continuous Monitoring:** Establishing ongoing monitoring practices to ensure consistent quality and identify potential areas for further improvement.
Conclusion: Achieving Success with Trial Production
By embracing trial production requests, manufacturers can produce high-quality parts at a lower cost, ensuring success in a competitive market.
Initial sample verification and a robust improvement process are critical components of this strategy, providing a foundation for producing superior products.
As demonstrated in the case study, companies that effectively utilize these methods can achieve significant benefits, from cost savings to enhanced product quality.
In conclusion, trial production is not merely a step in the manufacturing process; it is a strategic approach that empowers companies to meet their production goals while maintaining high standards.
By focusing on trial production, sample verification, and continuous improvement, businesses can thrive in an ever-evolving industry landscape.
資料ダウンロード
QCD管理受発注クラウド「newji」は、受発注部門で必要なQCD管理全てを備えた、現場特化型兼クラウド型の今世紀最高の受発注管理システムとなります。
ユーザー登録
受発注業務の効率化だけでなく、システムを導入することで、コスト削減や製品・資材のステータス可視化のほか、属人化していた受発注情報の共有化による内部不正防止や統制にも役立ちます。
NEWJI DX
製造業に特化したデジタルトランスフォーメーション(DX)の実現を目指す請負開発型のコンサルティングサービスです。AI、iPaaS、および先端の技術を駆使して、製造プロセスの効率化、業務効率化、チームワーク強化、コスト削減、品質向上を実現します。このサービスは、製造業の課題を深く理解し、それに対する最適なデジタルソリューションを提供することで、企業が持続的な成長とイノベーションを達成できるようサポートします。
製造業ニュース解説
製造業、主に購買・調達部門にお勤めの方々に向けた情報を配信しております。
新任の方やベテランの方、管理職を対象とした幅広いコンテンツをご用意しております。
お問い合わせ
コストダウンが利益に直結する術だと理解していても、なかなか前に進めることができない状況。そんな時は、newjiのコストダウン自動化機能で大きく利益貢献しよう!
(β版非公開)