- お役立ち記事
- Machine vibration mechanism and vibration trouble countermeasures based on ISO18436
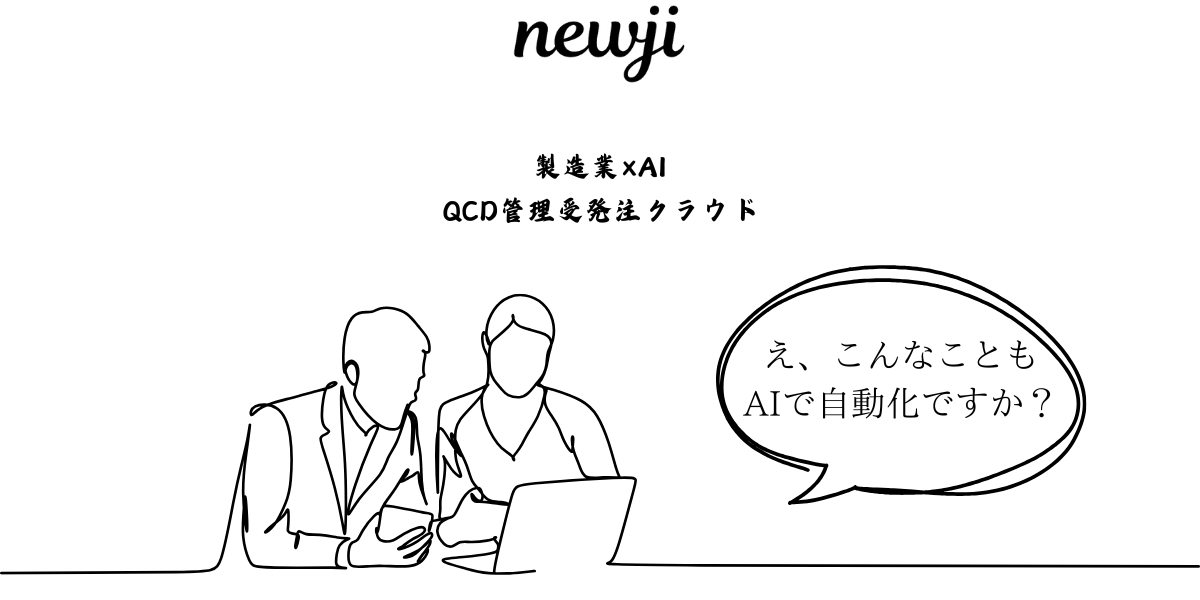
Machine vibration mechanism and vibration trouble countermeasures based on ISO18436
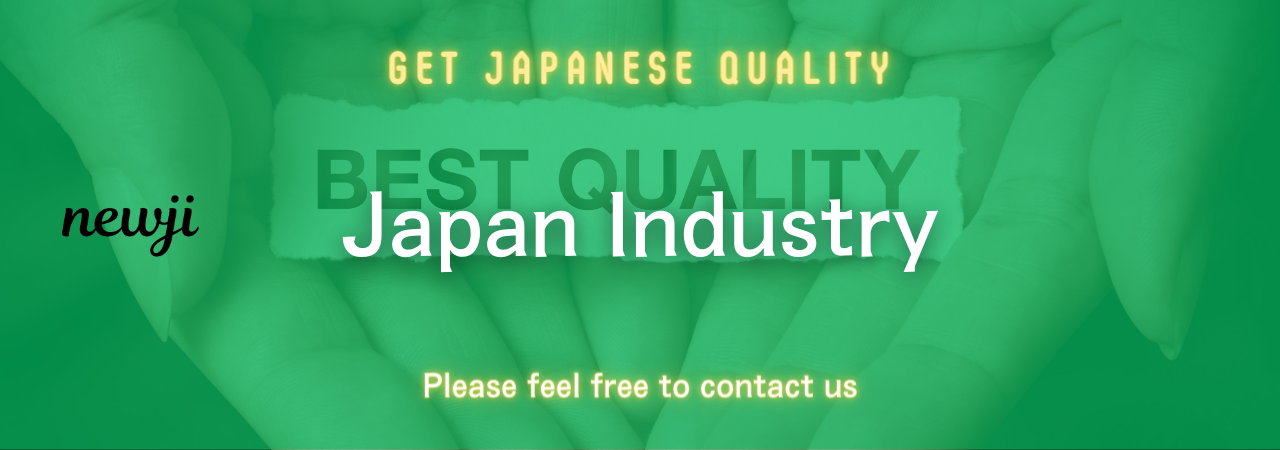
目次
Understanding Machine Vibration
Machine vibration is a common phenomenon seen in various industrial and mechanical systems.
This vibration can be caused by numerous factors, including mechanical imbalances, worn-out parts, or external forces.
It’s essential to understand the mechanism behind machine vibrations to maintain the optimal functioning of equipment and ensure their longevity.
Machine vibration can manifest in different ways, such as noise, oscillations, or outright shaking of the machine components.
The vibrations are typically analyzed in terms of amplitude, frequency, and phase difference.
Proper analysis can help identify the source of the vibration and aid in strategizing effective solutions to mitigate potential damage or operational inefficiencies.
Common Causes of Machine Vibration
There are several common causes of machine vibration, which are primarily rooted in machine inefficiencies or flaws in design.
Imbalance
Imbalance in a rotating body is a significant cause of vibrations.
When a machine’s rotating parts have uneven weight distribution, it results in centrifugal force during operation.
This can lead to vibrations throughout the machine.
Misalignment
Misalignment occurs when the machine components such as couplings, gears, or belts are not aligned correctly.
This misalignment can cause undue strain on the machine parts, leading to excessive vibration as they strive to operate under suboptimal conditions.
Mechanical Looseness
Over time, parts of the machine may become loose due to wear or improper assembly.
When these parts are not securely fastened, they tend to vibrate freely during operation, leading to potential machine damage or failure.
Resonance
Every machine has a natural frequency at which it vibrates most readily.
If operating conditions inadvertently meet this frequency, resonance occurs, which can amplify the machine’s vibrations significantly.
Prolonged resonance can cause severe damage, sometimes abruptly.
ISO 18436: An Overview
ISO 18436 is an international standard developed for the training and certification of condition monitoring and diagnosis of machines.
This standard is crucial for qualifying personnel in the techniques of condition monitoring, including vibration analysis, which is pivotal in maintaining and improving machinery performance.
The ISO 18436 standard outlines the requisite skills and knowledge for practitioners at different levels, ensuring that professionals are equipped to perform appropriate diagnostics and anticipate potential machine failures.
The standard aims to ensure consistency and accuracy in the analysis of machine conditions across various industries.
Importance in Vibration Analysis
By adhering to ISO 18436, organizations can ensure that their personnel are competent in understanding and analyzing machine conditions based on current technological advances.
This includes proficiency in identifying early signs of potential failures, thereby preventing costly downtimes and prolonging machine life.
Vibration analysis, under ISO 18436, provides a methodological approach to monitoring changes in machine conditions, ultimately contributing to improved productivity and reliability in systems.
Vibration Trouble Countermeasures
Addressing machine vibration issues promptly is vital to avert possible breakdowns and maintain operational efficiency.
Below are several countermeasures that can be implemented based on the principles of ISO 18436.
Regular Maintenance and Inspection
Routine checks and maintenance are fundamental to detect early signs of vibration problems.
Carrying out periodic inspections and maintenance according to standard protocols can help in identifying misalignments or loose components before they exacerbate into more serious issues.
Balancing Rotating Components
Proper balancing of rotating components is a critical measure to minimize vibrations.
This involves redistributing weight evenly across all parts to maintain equilibrium during operation, which aligns with best practices of machine maintenance and prevents uneven wear.
Addressing Misalignments
Correcting misalignment reduces unnecessary stress on machine components.
Realignment practices should comply with standardized methodologies to ensure enduring solutions that adhere to ISO 18436 guidelines for condition monitoring.
Use of Vibration Dampeners
Installing vibration dampeners can absorb excess energy generated during machine operation.
This limits the transmission of vibrations between components, thereby reducing overall machine noise and wear.
Conclusion
Understanding machine vibration mechanisms and implementing countermeasures based on ISO 18436 principles is crucial in mitigating potential operational failures.
Regular maintenance, informed diagnostics, and adherence to international standards for condition monitoring are indispensable for ensuring machinery’s efficient, safe, and prolonged functionality.
Possessing a comprehensive knowledge of these elements not only safeguards equipment but also enhances productivity, equipping organizations with the assurance of continual operational readiness.
資料ダウンロード
QCD調達購買管理クラウド「newji」は、調達購買部門で必要なQCD管理全てを備えた、現場特化型兼クラウド型の今世紀最高の購買管理システムとなります。
ユーザー登録
調達購買業務の効率化だけでなく、システムを導入することで、コスト削減や製品・資材のステータス可視化のほか、属人化していた購買情報の共有化による内部不正防止や統制にも役立ちます。
NEWJI DX
製造業に特化したデジタルトランスフォーメーション(DX)の実現を目指す請負開発型のコンサルティングサービスです。AI、iPaaS、および先端の技術を駆使して、製造プロセスの効率化、業務効率化、チームワーク強化、コスト削減、品質向上を実現します。このサービスは、製造業の課題を深く理解し、それに対する最適なデジタルソリューションを提供することで、企業が持続的な成長とイノベーションを達成できるようサポートします。
オンライン講座
製造業、主に購買・調達部門にお勤めの方々に向けた情報を配信しております。
新任の方やベテランの方、管理職を対象とした幅広いコンテンツをご用意しております。
お問い合わせ
コストダウンが利益に直結する術だと理解していても、なかなか前に進めることができない状況。そんな時は、newjiのコストダウン自動化機能で大きく利益貢献しよう!
(Β版非公開)