- お役立ち記事
- Machine vibration mechanism and vibration trouble countermeasures based on ISO18436
月間76,176名の
製造業ご担当者様が閲覧しています*
*2025年3月31日現在のGoogle Analyticsのデータより
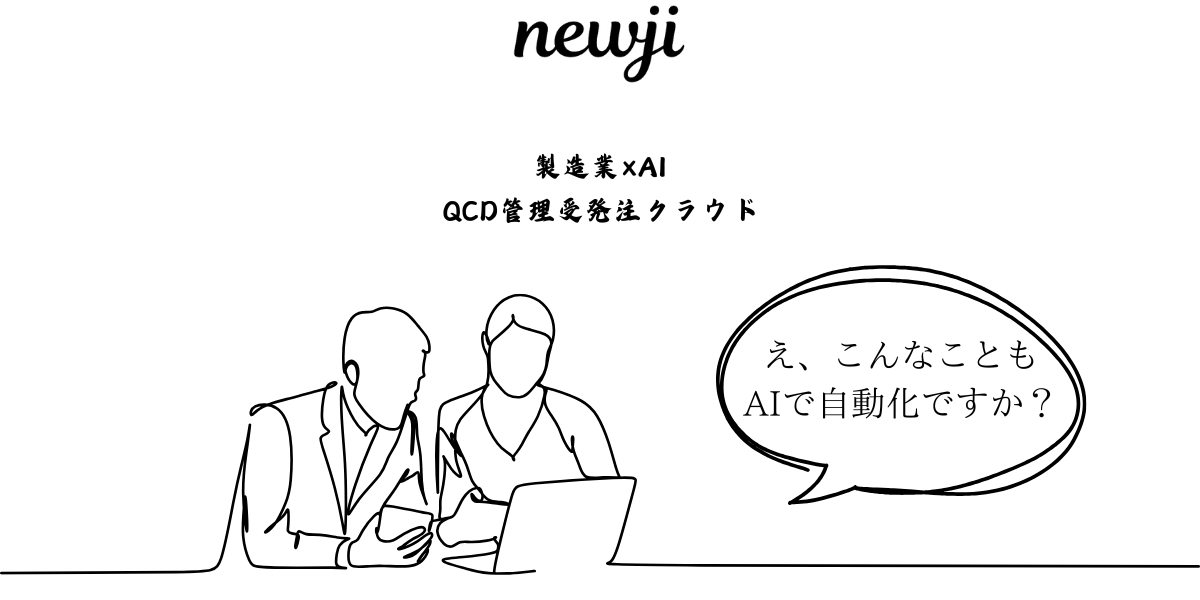
Machine vibration mechanism and vibration trouble countermeasures based on ISO18436
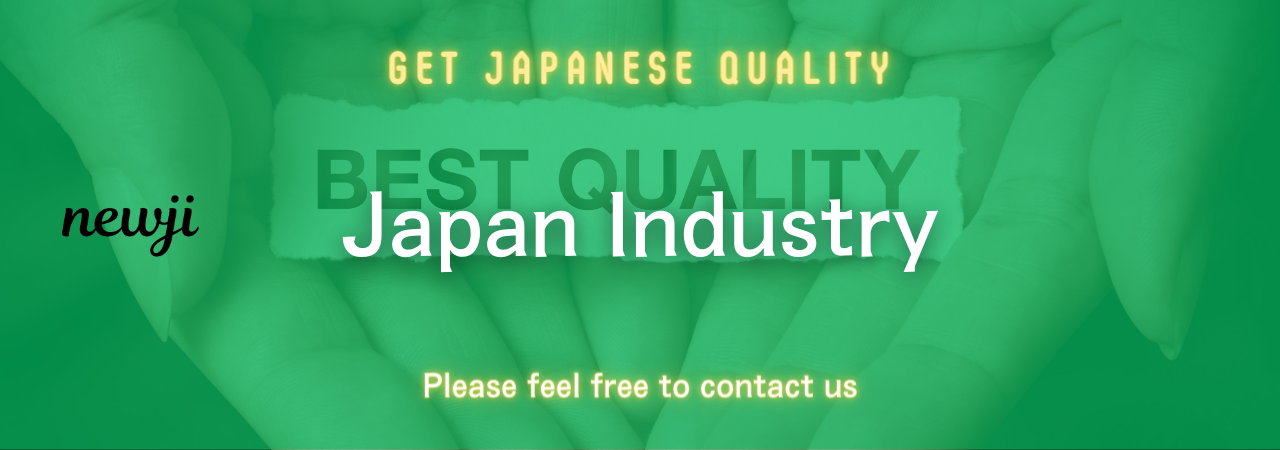
目次
Understanding Machine Vibration
Machine vibration is an essential concept in engineering and maintenance, impacting everything from the lifespan of equipment to its efficiency and safety.
In general terms, vibration in machines refers to the oscillation that occurs as a result of the machine’s components moving.
These oscillations can be felt, heard, and seen, depending on their frequency and intensity.
Vibration is categorized into two main types: free vibration and forced vibration.
Free vibration occurs naturally when a machine encounters an external force but then continues to oscillate at its natural frequency.
Forced vibration, on the other hand, occurs when a machine is continuously driven by an external force, which can lead to resonance if the frequency matches the machine’s natural frequency.
Understanding these types of vibrations is crucial for identifying and mitigating issues that can arise in industrial settings.
Common Causes of Machine Vibration
The sources of machine vibration can vary, and understanding them is vital for effective diagnosis.
Imbalance is one of the most common causes, often resulting from uneven mass distribution around the machine’s axis of rotation.
Misalignment, whether parallel or angular, can also contribute to increased vibration levels, especially in rotating equipment.
Wear and tear of components can lead to looseness, which is another frequent cause of vibration.
Looseness can result in parts moving in unintended ways, thereby generating abnormal vibrations.
Other contributors to machine vibration include inadequate lubrication, improper assembly, and component failure due to fatigue or stress.
Understanding these sources helps engineers and technicians develop proactive maintenance strategies, preventing costly breakdowns and ensuring smoother operation of machinery.
Impact of Machine Vibration
The impact of machine vibration can be wide-ranging, affecting both the machines themselves and the surrounding environment.
Excessive vibration can lead to premature failure of machine components, reducing their operational life and increasing maintenance costs.
It can also lead to safety hazards, with loosened parts potentially causing accidents.
Moreover, vibration can cause noise pollution, which is not only an inconvenience but can also lead to regulatory compliance issues and worker dissatisfaction.
In certain industries, vibration can also affect the quality of production, especially in precision manufacturing where accurate measurements are critical.
Understanding these impacts is crucial for prioritizing vibration monitoring as a key part of a comprehensive maintenance strategy.
ISO18436: The Standard for Vibration Analysis
ISO18436 provides a framework for the industrial application of vibration analysis and condition monitoring.
This international standard outlines the requirements for the training and certification of personnel involved in these activities, ensuring a consistent approach to diagnosing machine vibrations.
The standard addresses the necessary skills and knowledge bases that practitioners require, which include understanding vibration data collection, analysis, and reporting.
By adhering to ISO18436, organizations can ensure they have qualified personnel, thereby improving maintenance practices and reducing machine downtime.
ISO18436 emphasizes the importance of using systematic methods for assessing machine condition, providing guidelines that help in detecting potential failures early on.
This standard is pivotal in establishing best practices that lead to more reliable and safer industrial operations.
Vibration Trouble Countermeasures
Addressing vibration issues effectively requires a combination of monitoring, analysis, and corrective actions.
Regular vibration monitoring allows for early detection of issues, with techniques ranging from simple handheld devices to advanced online monitoring systems.
By capturing vibration signatures, technicians can identify deviations from normal operating conditions.
Once a vibration problem is identified, analysis should follow.
Techniques such as Fast Fourier Transform (FFT) analysis enable the identification of frequencies that might be causing the problem.
This data-driven approach helps in pinpointing the root cause of vibration, whether it’s imbalance, misalignment, or another issue.
To mitigate vibration troubles, corrective measures are necessary.
These might include balancing rotating parts, ensuring proper alignment, tightening loose components, and performing regular maintenance to replace worn or defective parts.
Engineering solutions can also be applied, such as installing vibration dampers or isolators to minimize transmission of vibrations to other parts of the machinery.
Implementing Effective Vibration Management
Effective vibration management is a sustained effort that requires ongoing training, investment in technology, and a culture of proactive maintenance.
Organizations should ensure their staff are well-trained and certified as per ISO18436 guidelines.
Access to the right technology is also crucial; selecting appropriate vibration monitoring equipment that aligns with the complexity and criticality of machine operations can make a significant difference.
A proactive maintenance culture fosters ongoing observation of machinery and emphasizes the importance of addressing small issues before they escalate into major problems.
This includes regular inspections, timely data analysis, and a commitment to using findings to make informed maintenance decisions.
The Benefits of Vibration Management
Investing in robust vibration management strategies yields numerous benefits.
It can extend the service life of machinery and reduce unexpected downtime, leading to improved operational efficiency.
By preventing potential failures before they occur, organizations can also lower maintenance costs and improve safety.
Furthermore, maintaining equipment at optimal vibration levels can lead to better product quality and greater consistency in output.
Overall, these benefits translate to a competitive advantage, as high reliability and efficiency are crucial to maximizing production capabilities.
Conclusion
Understanding the mechanisms behind machine vibration and adhering to standards like ISO18436 is critical for modern industrial operations.
By implementing effective vibration monitoring and trouble countermeasures, organizations can significantly enhance the reliability, safety, and efficiency of their machinery.
Staying informed and applying best practices in vibration management not only protects assets but also contributes to a sustainable industrial environment where resources are optimally used, and risks are minimized.
資料ダウンロード
QCD管理受発注クラウド「newji」は、受発注部門で必要なQCD管理全てを備えた、現場特化型兼クラウド型の今世紀最高の受発注管理システムとなります。
ユーザー登録
受発注業務の効率化だけでなく、システムを導入することで、コスト削減や製品・資材のステータス可視化のほか、属人化していた受発注情報の共有化による内部不正防止や統制にも役立ちます。
NEWJI DX
製造業に特化したデジタルトランスフォーメーション(DX)の実現を目指す請負開発型のコンサルティングサービスです。AI、iPaaS、および先端の技術を駆使して、製造プロセスの効率化、業務効率化、チームワーク強化、コスト削減、品質向上を実現します。このサービスは、製造業の課題を深く理解し、それに対する最適なデジタルソリューションを提供することで、企業が持続的な成長とイノベーションを達成できるようサポートします。
製造業ニュース解説
製造業、主に購買・調達部門にお勤めの方々に向けた情報を配信しております。
新任の方やベテランの方、管理職を対象とした幅広いコンテンツをご用意しております。
お問い合わせ
コストダウンが利益に直結する術だと理解していても、なかなか前に進めることができない状況。そんな時は、newjiのコストダウン自動化機能で大きく利益貢献しよう!
(β版非公開)