- お役立ち記事
- Machining of prototype parts and accuracy improvement technology
月間76,176名の
製造業ご担当者様が閲覧しています*
*2025年3月31日現在のGoogle Analyticsのデータより
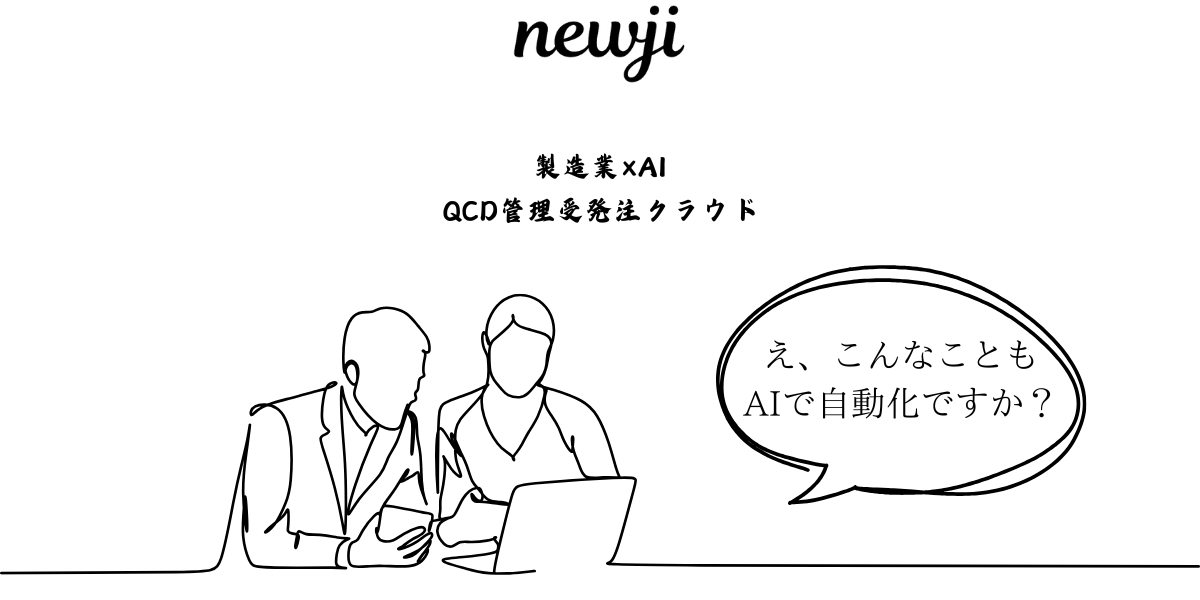
Machining of prototype parts and accuracy improvement technology
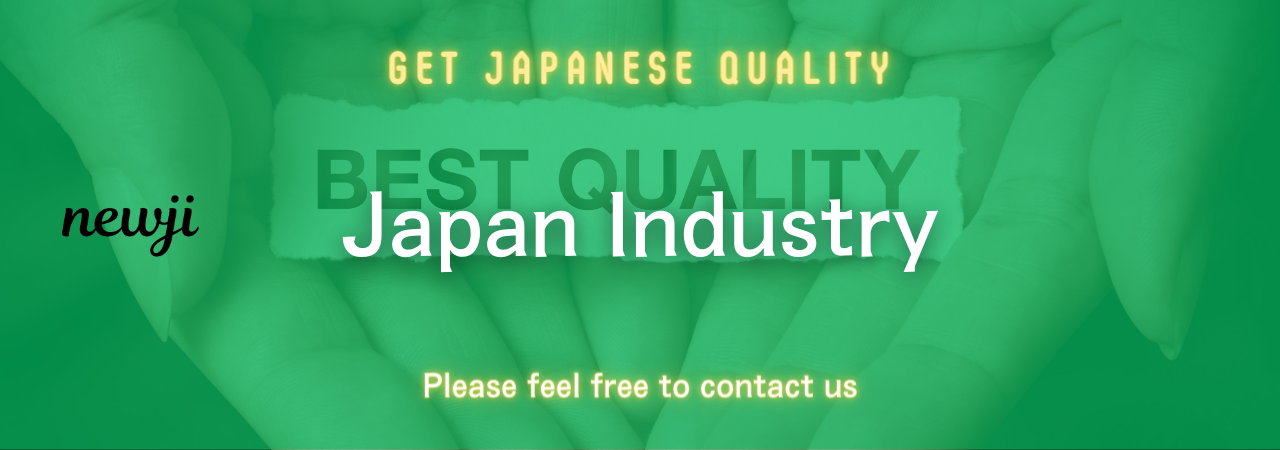
目次
Introduction to Machining of Prototype Parts
Machining of prototype parts is a crucial step in the development of any new product.
It involves the precise cutting, shaping, and finishing of materials to create parts that meet specific design requirements.
This process is essential for testing new designs, improving product features, and ensuring that parts will function correctly in their intended application.
The machining of prototype parts utilizes various techniques and technologies to achieve the desired level of precision and accuracy.
These techniques include computer numerical control (CNC) machining, 3D printing, laser cutting, and other advanced methods.
Each technique has its strengths and weaknesses, and choosing the right one depends on the material being used, the complexity of the design, and the required tolerances.
In this article, we will explore the machining of prototype parts and the technologies used to enhance accuracy.
Understanding these aspects is crucial for manufacturers, engineers, and designers who seek to deliver top-quality products.
CNC Machining: A Popular Choice
CNC machining is one of the most widely used techniques for the fabrication of prototype parts.
It involves the use of computer-controlled machines to remove material from a workpiece, shaping it into the desired part.
CNC machines can work with a wide range of materials, including metals, plastics, and composites.
One of the main advantages of CNC machining is its precision.
The machines operate with extremely tight tolerances, often within micrometers, ensuring that each part is produced to exact specifications.
This level of accuracy is essential for prototype parts, which must fit together perfectly with other components.
CNC machining is also highly versatile.
It can produce complex shapes and intricate designs, making it ideal for parts with detailed features.
Moreover, CNC machines can operate continuously, allowing for the production of multiple parts in a relatively short time.
Another benefit of CNC machining is its repeatability.
Once a program is created for a specific part, it can be reused to produce identical parts without any loss in accuracy.
This feature is particularly beneficial when multiple units of the prototype need to be tested.
3D Printing: A Growing Trend
3D printing, also known as additive manufacturing, is another technique gaining popularity for prototyping.
Unlike CNC machining, which is a subtractive process, 3D printing builds parts layer by layer.
This method allows for the creation of complex geometries and lightweight structures that would be difficult or impossible to achieve with traditional machining.
One of the key advantages of 3D printing is its speed.
Prototypes can be produced quickly, often within a few hours, depending on the complexity of the design and the material used.
This rapid turnaround allows designers to test and iterate their ideas much faster than with other methods.
3D printing is also cost-effective for small quantities.
There is no need for expensive tooling or molds, which makes it an attractive option for early-stage prototyping.
Furthermore, 3D printers can use a variety of materials, including plastics, metals, and even composites, providing flexibility in the choice of materials.
However, 3D printing does have limitations in terms of accuracy and surface finish.
While advancements are being made in this area, CNC machining remains the preferred choice for parts requiring tight tolerances and a smooth surface finish.
Laser Cutting: Precision and Speed
Laser cutting is another technology used in the machining of prototype parts.
It utilizes a high-powered laser beam to cut or engrave materials with precision.
This method is particularly effective for sheet materials such as metals, plastics, and wood.
Laser cutting offers excellent precision, allowing for intricate designs and detailed patterns to be produced with ease.
The laser beam is incredibly fine, enabling the cutting of narrow kerfs and minimizing material waste.
Another significant advantage of laser cutting is its speed.
It can produce parts quickly, making it suitable for rapid prototyping.
Additionally, laser cutting does not require direct contact with the material, reducing the risk of damaging delicate parts.
While laser cutting is highly effective for flat parts and engravings, it may not be suitable for all designs.
It is less effective for producing three-dimensional shapes, which is where 3D printing and CNC machining excel.
Improving Accuracy in Prototype Machining
Accuracy is a critical factor in the machining of prototype parts.
Achieving high accuracy ensures that parts will fit and function as intended, reducing the risk of errors during later stages of production.
Several strategies can be employed to improve accuracy in prototype machining.
First, selecting the right machining technique for the material and design is crucial.
Different techniques offer varying levels of precision, and choosing the most appropriate one can significantly impact the accuracy of the final part.
Secondly, using high-quality materials is essential.
Inferior materials can warp or deform during machining, leading to inaccuracies in the finished part.
Therefore, it is important to select materials that can withstand the machining process without degradation.
Another strategy is to establish and maintain proper machine calibration.
Regular maintenance and calibration of CNC machines, 3D printers, and laser cutters ensure they perform at their optimal levels.
Accurate calibration prevents deviations from the programmed dimensions and enhances the overall precision of the parts produced.
Additionally, leveraging advanced software solutions can improve accuracy.
Modern CAD/CAM software allows for precise modeling and simulation of the machining process, minimizing errors before physical production begins.
Quality control measures, such as dimensional inspection and testing, should also be implemented to verify the accuracy of each prototype part.
These measures help identify any discrepancies early in the process and allow for adjustments to be made before full-scale production.
Conclusion
Machining of prototype parts is an essential part of the product development process.
Technologies such as CNC machining, 3D printing, and laser cutting offer versatile solutions for creating accurate and functional prototypes.
Each technique comes with its distinct advantages, making it important to choose the right method based on the specific requirements of the design and material.
By employing strategies to improve accuracy, manufacturers and designers can ensure that each prototype part meets the highest standards.
In doing so, they pave the way for successful product development and manufacturing, ultimately leading to high-quality end products.
資料ダウンロード
QCD管理受発注クラウド「newji」は、受発注部門で必要なQCD管理全てを備えた、現場特化型兼クラウド型の今世紀最高の受発注管理システムとなります。
ユーザー登録
受発注業務の効率化だけでなく、システムを導入することで、コスト削減や製品・資材のステータス可視化のほか、属人化していた受発注情報の共有化による内部不正防止や統制にも役立ちます。
NEWJI DX
製造業に特化したデジタルトランスフォーメーション(DX)の実現を目指す請負開発型のコンサルティングサービスです。AI、iPaaS、および先端の技術を駆使して、製造プロセスの効率化、業務効率化、チームワーク強化、コスト削減、品質向上を実現します。このサービスは、製造業の課題を深く理解し、それに対する最適なデジタルソリューションを提供することで、企業が持続的な成長とイノベーションを達成できるようサポートします。
製造業ニュース解説
製造業、主に購買・調達部門にお勤めの方々に向けた情報を配信しております。
新任の方やベテランの方、管理職を対象とした幅広いコンテンツをご用意しております。
お問い合わせ
コストダウンが利益に直結する術だと理解していても、なかなか前に進めることができない状況。そんな時は、newjiのコストダウン自動化機能で大きく利益貢献しよう!
(β版非公開)