- お役立ち記事
- Main types and causes of injection molding troubles
月間76,176名の
製造業ご担当者様が閲覧しています*
*2025年3月31日現在のGoogle Analyticsのデータより
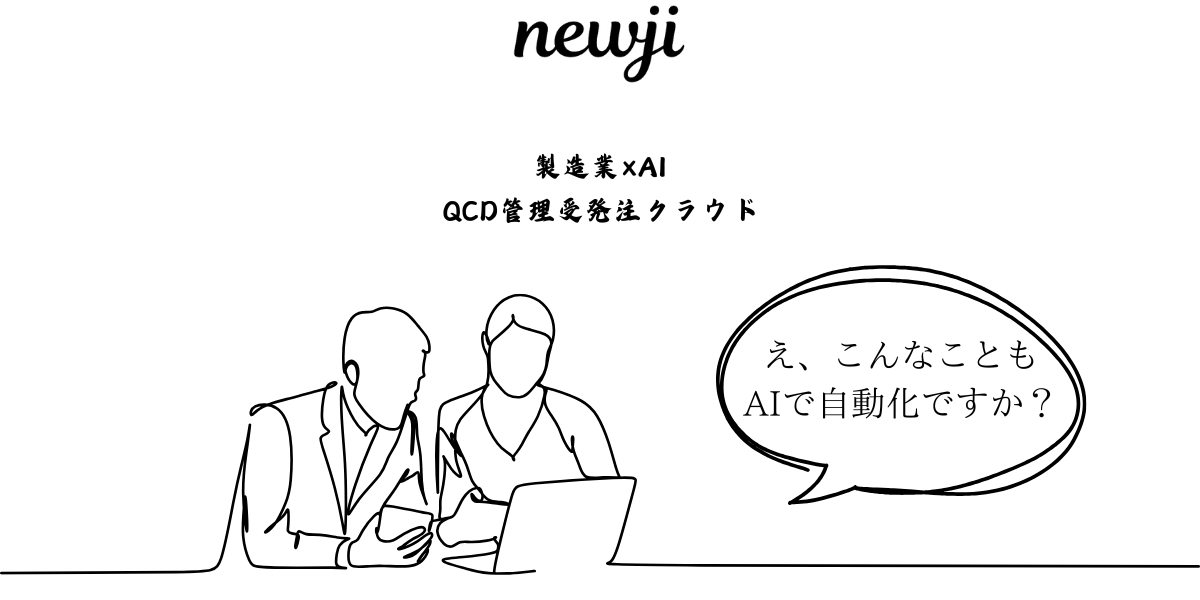
Main types and causes of injection molding troubles
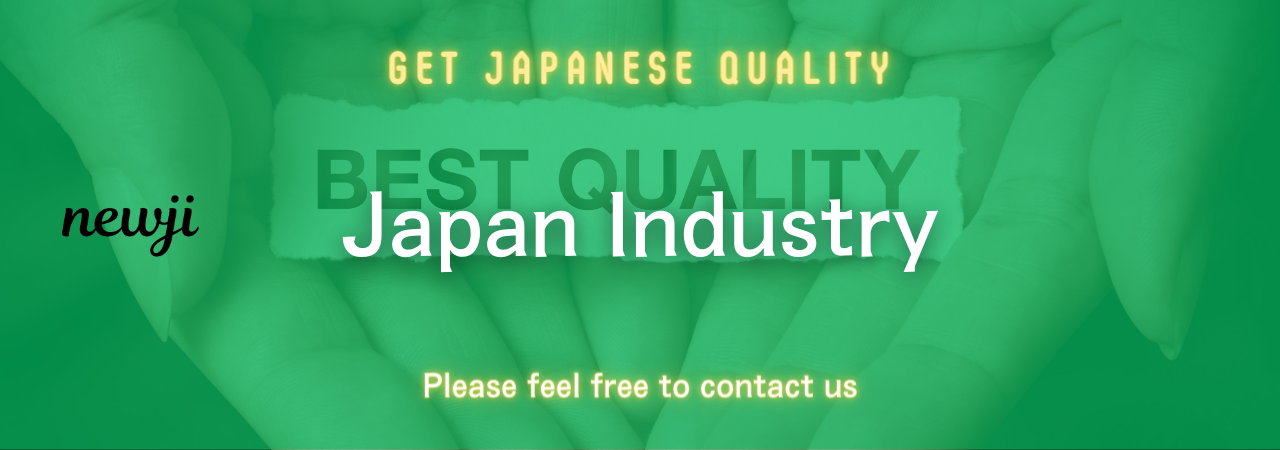
目次
Understanding Injection Molding
Injection molding is a manufacturing process that allows the mass production of plastic parts.
By injecting molten material into a mold, manufacturers can create precise and consistent shapes.
This process is widely used in many industries because it is efficient and cost-effective.
Despite its advantages, injection molding is not without its troubles.
Understanding these issues is crucial for maintaining high-quality production standards.
Types of Injection Molding Troubles
There are several types of troubles one might encounter in injection molding.
These can affect the quality of the final product, leading to defects or inefficiencies in the manufacturing process.
Let’s explore some of the most common issues.
Warping
Warping occurs when the plastic part cools unevenly, causing it to bend or twist.
This can lead to parts that don’t fit together properly, affecting the assembly of the final product.
Uneven cooling can be caused by various factors, such as variations in wall thickness or inconsistent mold temperatures.
Short Shot
A short shot happens when the plastic material does not fill the mold completely.
This can lead to incomplete products that are unusable.
Causes of short shots include insufficient material in the mold or blockages in the mold that prevent the material from flowing correctly.
Flash
Flash refers to excess plastic that seeps out of the mold cavity and solidifies.
This can create sharp, unwanted edges on the final product.
Flash often results from too much injection pressure or worn-out mold parts that no longer fit together tightly.
Sink Marks
Sink marks are depressions on the surface of a molded part.
They occur when the inner layers of plastic cool faster than the outer layers, causing the outer surface to sink inward.
This is usually caused by thick sections of the part or low holding pressure during the molding process.
Burn Marks
Burn marks are discolored areas on the surface of a plastic part.
They are often dark and can appear as streaks.
These marks are typically caused by trapped air that overheats during the injection process.
Excessive injection speed or inadequate venting can contribute to this issue.
Causes of Injection Molding Troubles
Identifying the causes of injection molding troubles is essential to preventing these issues and maintaining a smooth production process.
Here are some common causes:
Material Issues
The quality of the plastic material used in injection molding plays a significant role in the performance of the final product.
Impurities or inconsistencies in the material can lead to defects such as short shots or warping.
Ensuring that the material is appropriately dried and handled can help mitigate these issues.
Mold Design
Proper mold design is crucial for successful injection molding.
A poorly designed mold can lead to defects like flash or burn marks.
Factors such as gate location, wall thickness, and venting need to be carefully considered in the design phase to prevent common troubles.
Machine Malfunction
Injection molding machines must be regularly maintained to function correctly.
Worn-out components, improper calibration, or mechanical failures can result in defects.
Regular maintenance checks and calibration of injection parameters can help minimize the risk of machine-related issues.
Operator Error
Human error can also contribute to injection molding troubles.
Operators need to be adequately trained to handle the machinery and understand the process.
Incorrect settings or a lack of monitoring can lead to problems like inconsistent part quality or machine downtime.
Preventing Injection Molding Troubles
Prevention is always better than cure, especially in manufacturing processes like injection molding.
Implementing strategies to reduce the occurrence of defects is key to ensuring product quality and reducing waste.
Quality Control
Implementing robust quality control measures can help identify potential issues early in the production process.
Having a system in place for regular inspection of both the machinery and the final products can ensure problems are caught and corrected before they escalate.
Proper Maintenance
Regular maintenance of injection molding equipment is critical.
This includes checking for wear and tear on molds, performing routine machine calibration, and replacing old components to maintain performance.
Training
Ensuring that all operators are thoroughly trained can prevent many injection molding troubles.
Training should cover proper handling of materials, machine operation, and understanding troubleshooting methods to address issues as they arise.
Optimizing Design
Working with experienced mold designers can help in creating efficient mold designs that minimize defects.
This includes assessing potential weak points in the design and making necessary adjustments to reduce risks associated with mold-related issues.
In conclusion, while injection molding is a highly efficient manufacturing process, it is not without its challenges.
By understanding the types and causes of common troubles in injection molding, manufacturers can take proactive steps to prevent these issues and maintain high production standards.
資料ダウンロード
QCD管理受発注クラウド「newji」は、受発注部門で必要なQCD管理全てを備えた、現場特化型兼クラウド型の今世紀最高の受発注管理システムとなります。
ユーザー登録
受発注業務の効率化だけでなく、システムを導入することで、コスト削減や製品・資材のステータス可視化のほか、属人化していた受発注情報の共有化による内部不正防止や統制にも役立ちます。
NEWJI DX
製造業に特化したデジタルトランスフォーメーション(DX)の実現を目指す請負開発型のコンサルティングサービスです。AI、iPaaS、および先端の技術を駆使して、製造プロセスの効率化、業務効率化、チームワーク強化、コスト削減、品質向上を実現します。このサービスは、製造業の課題を深く理解し、それに対する最適なデジタルソリューションを提供することで、企業が持続的な成長とイノベーションを達成できるようサポートします。
製造業ニュース解説
製造業、主に購買・調達部門にお勤めの方々に向けた情報を配信しております。
新任の方やベテランの方、管理職を対象とした幅広いコンテンツをご用意しております。
お問い合わせ
コストダウンが利益に直結する術だと理解していても、なかなか前に進めることができない状況。そんな時は、newjiのコストダウン自動化機能で大きく利益貢献しよう!
(β版非公開)