- お役立ち記事
- Maintaining Cleanliness in Manufacturing Lines with CIP (Cleaning In Place) Implementation
月間76,176名の
製造業ご担当者様が閲覧しています*
*2025年3月31日現在のGoogle Analyticsのデータより
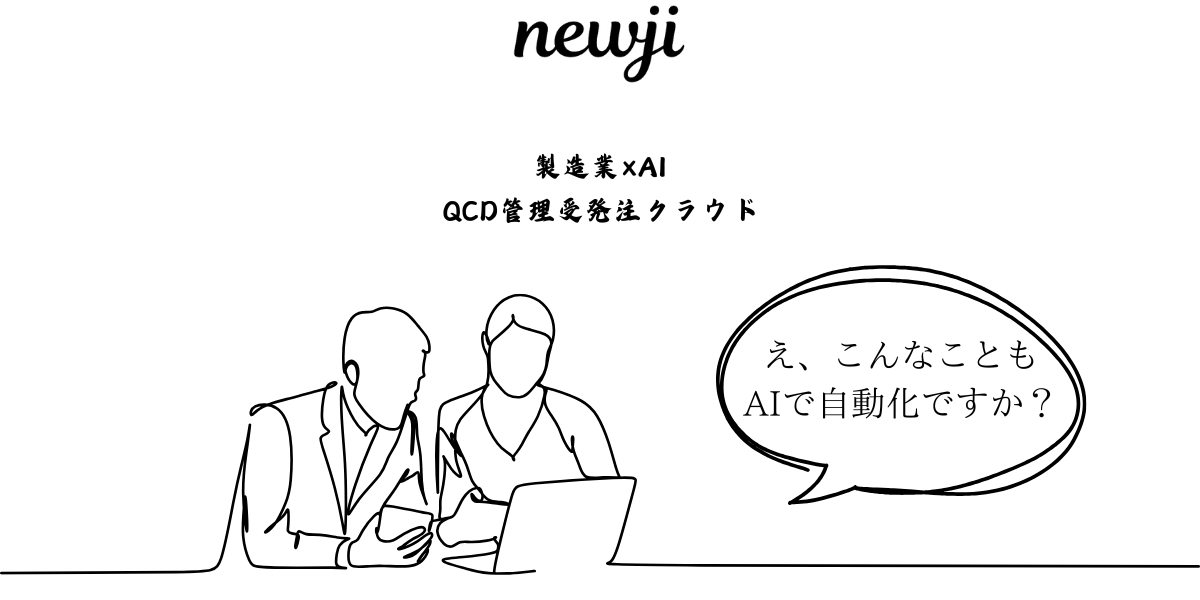
Maintaining Cleanliness in Manufacturing Lines with CIP (Cleaning In Place) Implementation
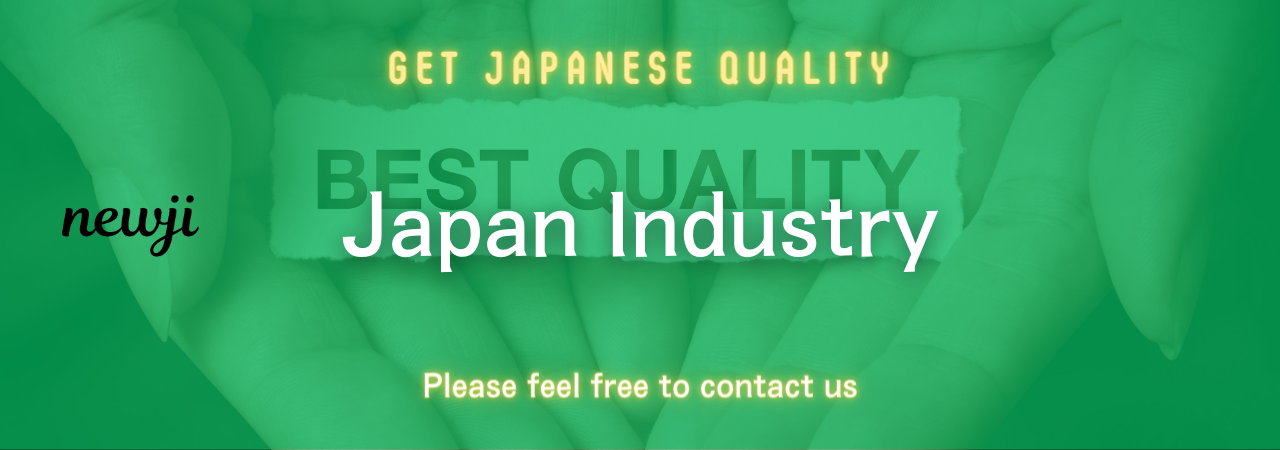
In the world of manufacturing, keeping the production line clean is crucial.
Cleanliness ensures that products meet quality standards and that the equipment functions efficiently.
One effective method for maintaining cleanliness in manufacturing lines is CIP, or Cleaning In Place.
This technique is especially popular in industries such as food and beverage, pharmaceuticals, and cosmetics, where hygiene is paramount.
目次
What is CIP?
CIP, or Cleaning In Place, is a method of cleaning the interior surfaces of pipes, vessels, process equipment, filters, and other fittings without disassembling them.
This system allows for efficient and effective cleaning, ensuring that contaminants are removed without the need to take apart the machinery.
The process typically involves circulating cleaning agents, rinsing waters, and sanitizing solutions through the equipment.
This helps to remove any residual product, microorganisms, or allergens that could compromise the quality of the next production batch.
The Importance of Cleanliness in Manufacturing
Clean manufacturing environments are vital for several reasons.
Firstly, they help to ensure product safety and quality, which are essential for consumer trust and regulatory compliance.
Contaminants in the production line can lead to batch recalls, financial losses, and damage to the company’s reputation.
Secondly, cleanliness reduces equipment wear and tear, leading to longer machine life and fewer maintenance requirements.
This results in operational cost savings and minimized downtime.
Regulatory Compliance
Many industries are subject to strict regulations regarding cleanliness and hygiene.
For example, the food and beverage industry must comply with standards set by organizations like the FDA and HACCP.
Similarly, the pharmaceutical industry is regulated by agencies such as the FDA and EMA.
Implementing CIP ensures that manufacturing processes meet these stringent standards consistently, thus avoiding fines and sanctions.
Consumer Trust and Brand Reputation
In today’s market, consumers are more informed and value product safety and quality.
A single instance of contamination can lead to a loss of consumer trust and damage the brand’s reputation.
By maintaining a clean manufacturing line through CIP, companies can uphold high standards, thus ensuring customer satisfaction and loyalty.
Operational Efficiency
Dirty equipment often operates less efficiently, consuming more energy and potentially causing production delays.
Regular cleaning using CIP systems keeps machines running smoothly and efficiently.
This translates to higher production rates, less energy consumption, and reduced downtime, all of which contribute to improved operational efficiency and profitability.
Benefits of CIP in Manufacturing Lines
Implementing CIP systems in manufacturing lines offers numerous benefits:
Time Savings
One of the primary advantages of CIP is the significant time savings achieved.
Traditional cleaning methods require disassembling and manually cleaning equipment, which is time-consuming.
CIP automates the cleaning process, allowing for simultaneous cleaning and production preparations, thus minimizing downtime.
Consistency and Reliability
CIP provides consistent and reliable cleaning results every time.
With manually cleaning, the outcome can vary based on the worker’s diligence and technique.
Automated CIP systems ensure that every nook and cranny of the equipment is cleaned thoroughly and uniformly, reducing the risk of contamination.
Worker Safety
Cleaning machinery manually can pose risks to workers, including exposure to hazardous cleaning chemicals and potential injuries from equipment.
CIP reduces these risks by automating the cleaning process, thereby protecting workers and creating a safer work environment.
Resource Efficiency
CIP systems are designed to use cleaning agents, water, and energy efficiently.
This not only reduces the environmental footprint but also lowers the operating costs associated with cleaning.
Recycling of cleaning solutions and water further enhances the sustainability of the cleaning process.
Key Components of a CIP System
A typical CIP system comprises several key components that work together to ensure efficient cleaning:
CIP Tanks
These tanks store the cleaning agents and solutions used in the CIP process.
They are usually made of stainless steel to prevent corrosion and contamination.
Pumps
Pumps are essential for circulating cleaning solutions through the system.
High-pressure pumps ensure that the cleaning agents reach all parts of the equipment.
Heat Exchangers
Heat exchangers are used to heat the cleaning solutions to the required temperature.
This helps in breaking down residues and enhancing the cleaning efficiency.
Control Units
Control units are the brains of the CIP system.
They automate the cleaning process, ensuring that the correct cleaning sequence, temperature, and duration are maintained.
This ensures consistent and effective cleaning.
Implementing CIP in Your Manufacturing Line
Integrating a CIP system into your manufacturing process can be a game-changer, but it requires careful planning and execution:
Assess Your Needs
The first step is to assess the specific cleaning needs of your manufacturing line.
Factors to consider include the types of residues commonly encountered, the equipment configuration, and the regulatory requirements.
Design the System
Based on the assessment, design a CIP system that addresses your unique needs.
Consulting with CIP system providers and experts can help in creating a design that maximizes efficiency and effectiveness.
Installation and Testing
Once the design is complete, the next step is installation.
Ensure that the installation process is meticulously handled to avoid any issues.
After installation, thorough testing is essential to verify that the system works as intended and meets all cleaning criteria.
Training and Maintenance
Training workers on the operation of the CIP system is crucial for smooth implementation.
Regular maintenance is also necessary to keep the system in optimal condition and to address any issues promptly.
Periodic audits and reviews can help in identifying areas for improvement and ensuring continuous compliance.
Conclusion
Incorporating CIP systems in manufacturing lines is a strategic move that brings numerous benefits.
From regulatory compliance and resource efficiency to improved operational efficiency and worker safety, CIP makes maintaining cleanliness easier and more effective.
By adopting CIP, manufacturers can ensure high-quality product output, maintain consumer trust, and enhance their overall productivity.
資料ダウンロード
QCD管理受発注クラウド「newji」は、受発注部門で必要なQCD管理全てを備えた、現場特化型兼クラウド型の今世紀最高の受発注管理システムとなります。
ユーザー登録
受発注業務の効率化だけでなく、システムを導入することで、コスト削減や製品・資材のステータス可視化のほか、属人化していた受発注情報の共有化による内部不正防止や統制にも役立ちます。
NEWJI DX
製造業に特化したデジタルトランスフォーメーション(DX)の実現を目指す請負開発型のコンサルティングサービスです。AI、iPaaS、および先端の技術を駆使して、製造プロセスの効率化、業務効率化、チームワーク強化、コスト削減、品質向上を実現します。このサービスは、製造業の課題を深く理解し、それに対する最適なデジタルソリューションを提供することで、企業が持続的な成長とイノベーションを達成できるようサポートします。
製造業ニュース解説
製造業、主に購買・調達部門にお勤めの方々に向けた情報を配信しております。
新任の方やベテランの方、管理職を対象とした幅広いコンテンツをご用意しております。
お問い合わせ
コストダウンが利益に直結する術だと理解していても、なかなか前に進めることができない状況。そんな時は、newjiのコストダウン自動化機能で大きく利益貢献しよう!
(β版非公開)