- お役立ち記事
- Maintenance Techniques to Ensure Machining Precision in Production Equipment
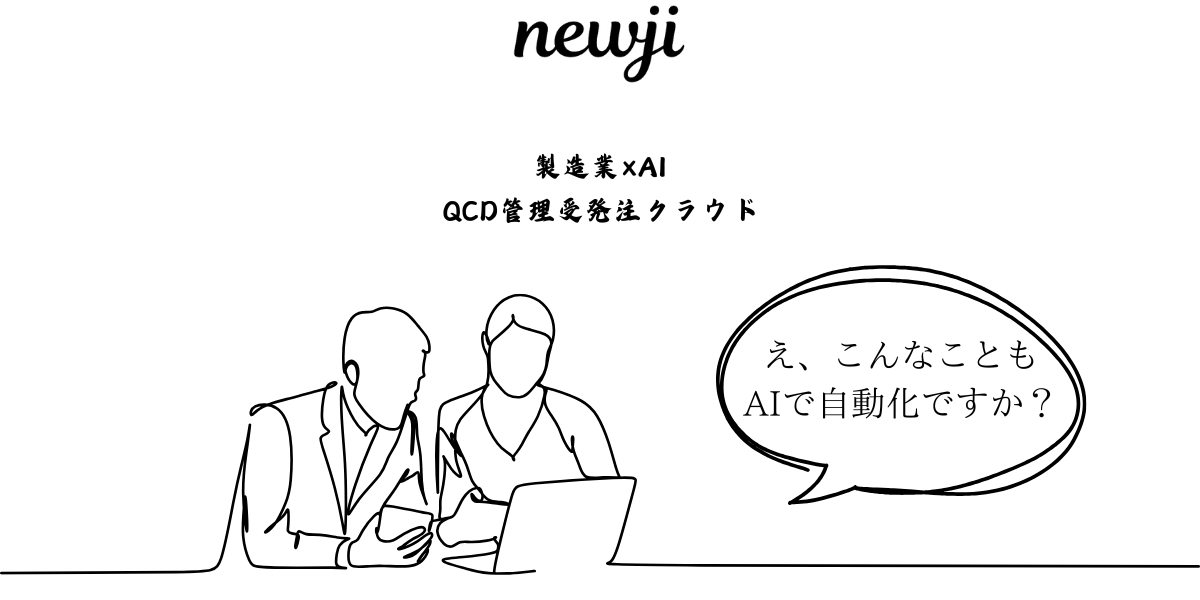
Maintenance Techniques to Ensure Machining Precision in Production Equipment
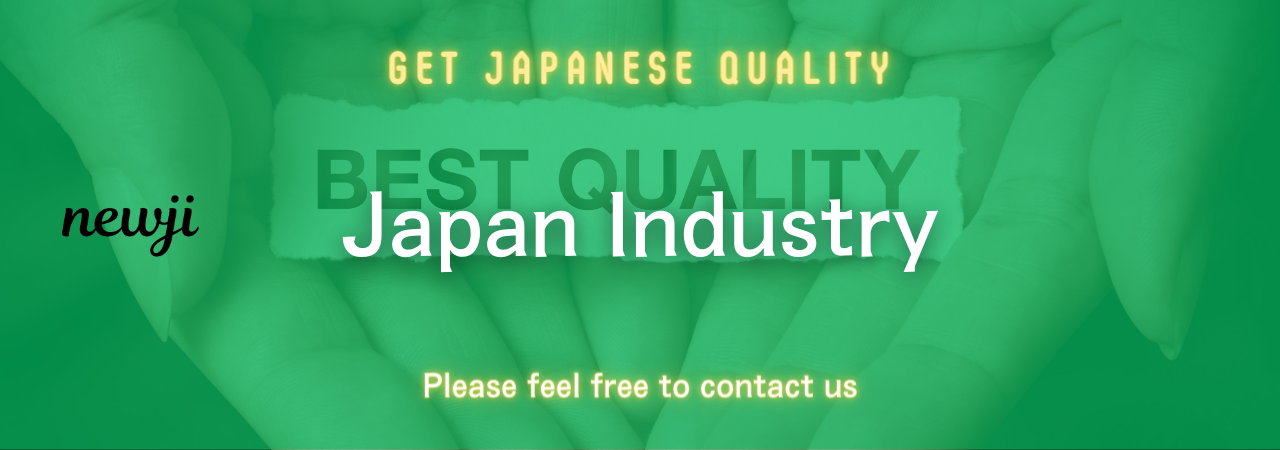
目次
Understanding the Importance of Machining Precision
In the manufacturing world, precision is paramount.
Without precise machining, the quality and functionality of products can be compromised.
Machining precision refers to the accurate execution of manufacturing tasks, ensuring that each component meets specified dimensions and tolerances.
For companies looking to maintain competitive advantage and ensure consumer satisfaction, maintaining machining precision within production equipment is crucial.
Factors Affecting Machining Precision
Several factors can affect machining precision.
Understanding these can help manufacturers pinpoint areas that require attention or improvement.
Firstly, the wear and tear on tools can significantly impact precision.
Tools must be kept sharp and regularly inspected to prevent defects that could affect part accuracy.
Secondly, machine alignment plays a critical role.
Misaligned machines can produce inconsistent results, which can lead to subpar production quality.
Regular inspections and calibrations help keep alignment intact.
Environmental factors, such as temperature and humidity, also play a role.
These elements can cause slight expansions or contractions in materials or machinery, leading to inaccuracies if not properly accounted for in the process.
Ensuring that the workshop environment is controlled can mitigate these influences.
Maintenance Techniques for Optimal Performance
To maintain machining precision, consistent and proactive maintenance practices are essential.
Regular Machine Calibration
Calibration is a critical aspect of machine maintenance.
Over time, machines can drift from their original specifications, leading to inaccuracies.
Regularly scheduled calibration sessions ensure that machines operate at optimal precision, adhering to original parameters.
This helps in maintaining quality and reducing scrap rates.
Tool Management and Care
Proper tool management is vital for maintaining machining precision.
Tools must be regularly examined for signs of wear and replaced as necessary.
Dull or worn-out tools can lead to inaccurate cuts and poor finishes.
Employing a tool management system can help track tool usage and schedule timely replacements or regrinding.
Lubrication and Cleaning
Lubrication is crucial in reducing friction and wear, promoting smoother machine operations.
Effective lubrication not only extends the lifespan of machinery but also ensures precision in movement and force.
Coupled with lubrication, regular cleaning of machines helps prevent the buildup of debris that could impair operation and precision.
Tracking and Analyzing Performance Data
Data-driven decision-making supports the maintenance of machining precision.
By tracking machine performance data over time, manufacturers can identify trends or irregularities.
This enables prompt corrective actions before minor issues escalate into major disruptions.
Advanced monitoring systems can alert operators to deviations from normal operating conditions, allowing for quick intervention.
Implementing Preventive Maintenance Strategies
Preventive maintenance is a strategic approach that reduces the likelihood of unexpected equipment failures.
By addressing potential issues before they become problematic, manufacturers can maintain machining precision and equipment reliability.
Scheduling Regular Inspections
Scheduled inspections are the cornerstone of preventive maintenance strategies.
These inspections help in identifying worn-out parts, alignment issues, or other potential problems.
Regular assessment ensures continuous operational efficiency and supports the long-term maintenance of precision standards.
Establishing Quality Assurance Protocols
Implementing quality assurance protocols is essential for preventing machining errors.
A robust quality assurance program includes checks and balances that monitor every stage of production.
Inspection of random samples against design specifications helps ensure that precision is maintained consistently throughout production runs.
The Role of Technology in Precision Maintenance
Modern technology offers tools that support and enhance maintenance strategies aimed at achieving machining precision.
Adopting Automation Solutions
Automation solutions can relieve manual burdens while enhancing precision.
Automated handlers and robotic arms can perform tasks with high accuracy, reducing human error.
Furthermore, automation allows for continuous operation, adhering closely to programmed specifications to maintain high precision.
Utilizing Predictive Maintenance Tools
Predictive maintenance utilizes data analytics and machine learning to anticipate machine failures before they happen.
By analyzing performance data, predictive tools can forecast when a machine component might fail, allowing for early intervention.
This proactive approach helps maintain machine performance levels and precision standards, avoiding unexpected downtime.
Training and Educating Personnel
Human resources play a significant role in maintaining machining precision.
Well-trained personnel can effectively operate and maintain machinery, applying the correct techniques and guidelines to sustain high precision.
Continuous Skill Development
Regular training programs help keep operators updated on the latest machining technologies and maintenance techniques.
A skilled workforce is critical in detecting and addressing potential precision problems, ensuring adherence to best practices at all times.
Promoting a Culture of Precision
In closing, instilling a culture of precision within the organization is essential.
When employees recognize the importance of precision, they are more likely to adhere to maintenance protocols and quality standards.
Engaging personnel at all levels fosters a shared commitment to maintaining excellence in machining practices.
By integrating these maintenance techniques, manufacturers can safeguard machining precision, ensuring top-quality production and strengthening their competitive edge in the market.
資料ダウンロード
QCD調達購買管理クラウド「newji」は、調達購買部門で必要なQCD管理全てを備えた、現場特化型兼クラウド型の今世紀最高の購買管理システムとなります。
ユーザー登録
調達購買業務の効率化だけでなく、システムを導入することで、コスト削減や製品・資材のステータス可視化のほか、属人化していた購買情報の共有化による内部不正防止や統制にも役立ちます。
NEWJI DX
製造業に特化したデジタルトランスフォーメーション(DX)の実現を目指す請負開発型のコンサルティングサービスです。AI、iPaaS、および先端の技術を駆使して、製造プロセスの効率化、業務効率化、チームワーク強化、コスト削減、品質向上を実現します。このサービスは、製造業の課題を深く理解し、それに対する最適なデジタルソリューションを提供することで、企業が持続的な成長とイノベーションを達成できるようサポートします。
オンライン講座
製造業、主に購買・調達部門にお勤めの方々に向けた情報を配信しております。
新任の方やベテランの方、管理職を対象とした幅広いコンテンツをご用意しております。
お問い合わせ
コストダウンが利益に直結する術だと理解していても、なかなか前に進めることができない状況。そんな時は、newjiのコストダウン自動化機能で大きく利益貢献しよう!
(Β版非公開)