- お役立ち記事
- Management of Solidification Speed in Copper Alloy Casting
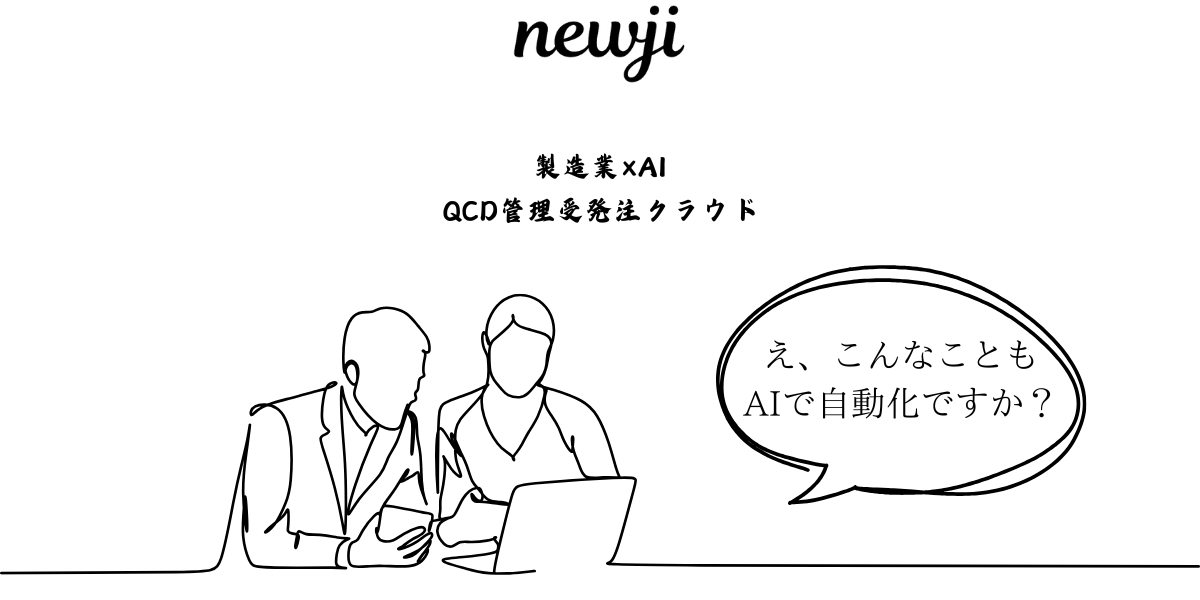
Management of Solidification Speed in Copper Alloy Casting
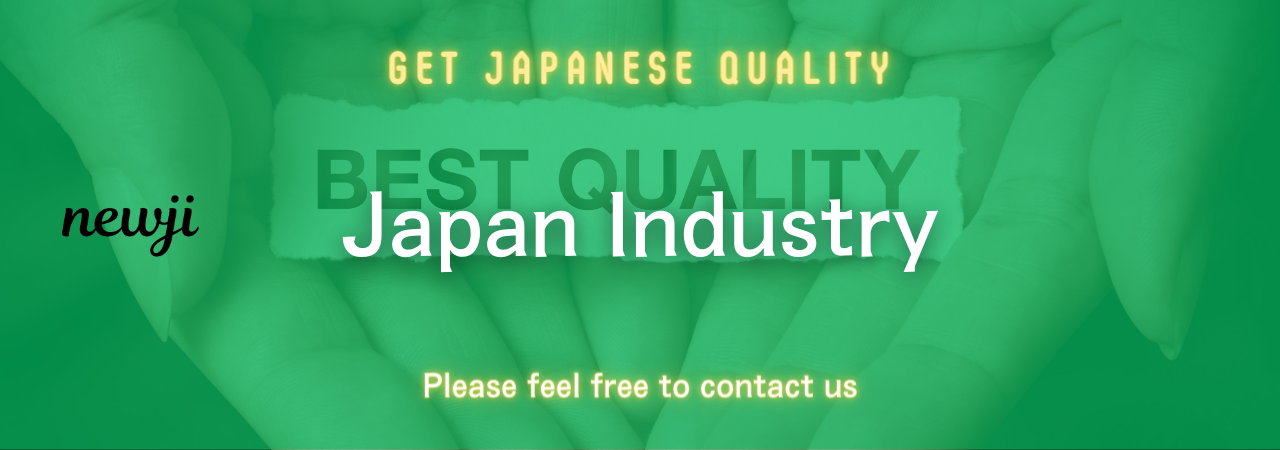
目次
Introduction to Copper Alloy Casting
Copper alloy casting is a vital process in the manufacturing industry, used to create a wide variety of products and components.
By mixing copper with other metals, such as zinc, tin, or nickel, manufacturers produce alloys like bronze and brass, which exhibit unique properties suitable for different applications.
One critical aspect of this process is managing the solidification speed during casting.
This directly affects the mechanical properties, surface finish, and dimensional accuracy of the final product.
Why Solidification Speed Matters
Solidification speed in copper alloy casting determines several key characteristics of the cast product.
A controlled solidification process helps in reducing defects such as shrinkage porosity, cracking, and segregation.
These defects can compromise the structural integrity and overall quality of the alloy.
The speed at which a copper alloy solidifies can influence its grain size and microstructure.
A slower solidification rate usually results in a coarse grain structure, which might enhance certain mechanical properties, while a faster rate can produce a finer grain structure, often providing better surface finishes and greater strength in specific applications.
Effects on Mechanical Properties
The mechanical properties of cast copper alloys, including tensile strength, ductility, and hardness, are significantly impacted by how quickly the alloy solidifies.
For instance, a slower cooling rate might lead to a soft and ductile material, whereas a quicker speed will often increase hardness.
This means that producers must carefully control the solidification conditions to meet the specific requirements of the finished product.
Understanding the relationship between cooling rate and mechanical properties allows manufacturers to tailor alloys to specific applications, enhancing performance and lifespan in their intended use.
Controlling Solidification Speed
Managing the solidification speed involves careful control over several factors during the casting process, including temperature, mold material, and cooling methods.
Let’s delve into how each of these elements can be optimized.
Temperature Management
One primary factor in solidification control is the temperature at which the process is conducted.
Proper management of the pouring temperature can significantly influence the cooling rate.
Pouring the copper alloy at an optimal temperature ensures that it solidifies evenly and minimises defects such as gas porosity and shrinkage.
Lowering the pouring temperature generally increases the cooling rate, leading to finer grain structures, while higher temperatures may result in slower cooling and coarser grains.
Maintaining the correct temperature is crucial to achieving a balance between quality and efficiency.
Mold Material and Design
The choice of mold material is another critical factor that directly affects how fast an alloy solidifies.
Mold materials with high thermal conductivity, such as graphite or metal, can facilitate quicker cooling rates.
In contrast, sand or ceramic molds usually lead to slower solidification due to their lower thermal conductivity.
Moreover, the design of the mold can impact solidification speed.
Incorporating features like cooling fins or channels can regulate how heat is dissipated from the molten alloy, allowing manufacturers to fine-tune the solidification rate.
Cooling Methods
Active cooling methods, such as air or water cooling, can be employed to control the rate at which the copper alloy solidifies.
These methods can be combined with casting molds that enhance heat extraction, allowing for precise management of the solidification process.
In some cases, using controlled atmospheres, like a vacuum or inert gas environments, can also affect cooling rates by altering the heat transfer dynamics.
Such methods might be used to achieve specific microstructures and mechanical properties in challenging casting situations.
Challenges in Solidification Speed Management
While controlling solidification speed is crucial, it also presents several challenges.
Predicting the exact cooling path and resultant structure of the alloy can be complex.
Factors like mold geometry, alloy composition, and environmental conditions can interact in unpredictable ways.
Moreover, achieving a uniform grain structure can be difficult, especially in larger castings where different sections cool at varying rates.
Uneven cooling can lead to residual stress and warping, compromising the final product’s quality.
Technological Innovations
Advances in technology are helping to overcome these challenges.
Simulation software allows foundry engineers to model the solidification process virtually, predicting outcomes and tweaking process parameters for optimal results.
This proactive approach reduces the trial-and-error aspect of casting, saving time and resources.
Additionally, automation in casting lines enables precise control over parameters such as temperature and cooling rates, enhancing consistency and quality in mass production.
Conclusion
The management of solidification speed in copper alloy casting is pivotal for producing components with desired properties and minimal defects.
By carefully controlling variables such as temperature, mold material, and cooling methods, manufacturers can optimize the casting process to meet their specific needs.
Despite the challenges, ongoing technological advancements present promising solutions that make the management of solidification speed more precise and efficient.
Understanding and implementing these practices effectively will ensure high-quality, durable copper alloy products for various applications.
資料ダウンロード
QCD調達購買管理クラウド「newji」は、調達購買部門で必要なQCD管理全てを備えた、現場特化型兼クラウド型の今世紀最高の購買管理システムとなります。
ユーザー登録
調達購買業務の効率化だけでなく、システムを導入することで、コスト削減や製品・資材のステータス可視化のほか、属人化していた購買情報の共有化による内部不正防止や統制にも役立ちます。
NEWJI DX
製造業に特化したデジタルトランスフォーメーション(DX)の実現を目指す請負開発型のコンサルティングサービスです。AI、iPaaS、および先端の技術を駆使して、製造プロセスの効率化、業務効率化、チームワーク強化、コスト削減、品質向上を実現します。このサービスは、製造業の課題を深く理解し、それに対する最適なデジタルソリューションを提供することで、企業が持続的な成長とイノベーションを達成できるようサポートします。
オンライン講座
製造業、主に購買・調達部門にお勤めの方々に向けた情報を配信しております。
新任の方やベテランの方、管理職を対象とした幅広いコンテンツをご用意しております。
お問い合わせ
コストダウンが利益に直結する術だと理解していても、なかなか前に進めることができない状況。そんな時は、newjiのコストダウン自動化機能で大きく利益貢献しよう!
(Β版非公開)