- お役立ち記事
- Managers in the quality assurance department cannot be overlooked! Basics of TQM and sustainable quality improvement strategies
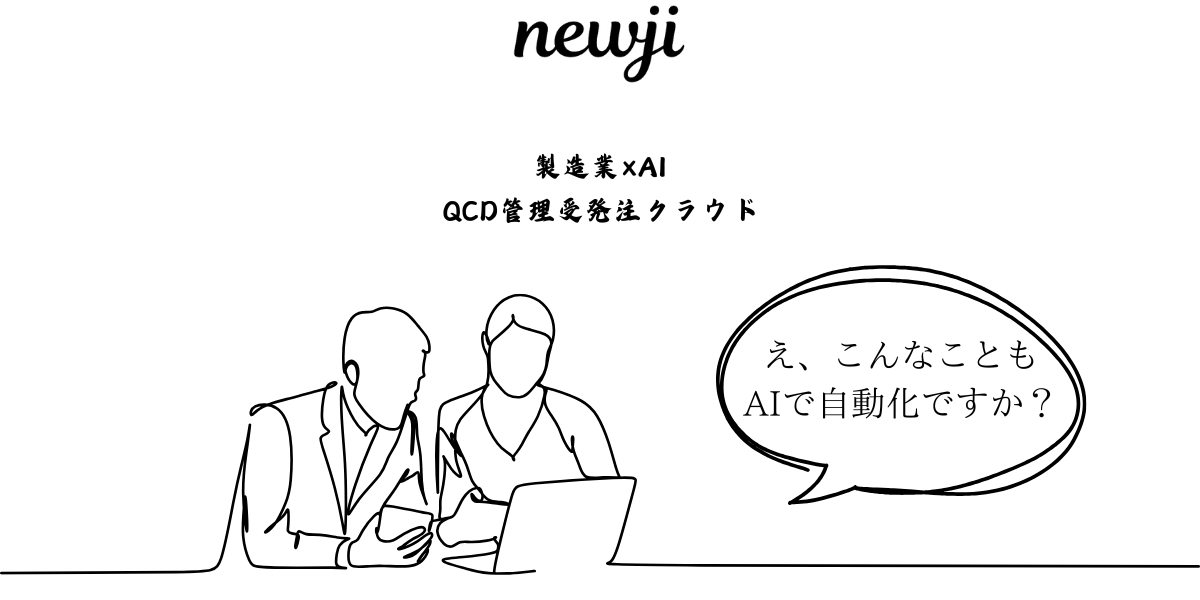
Managers in the quality assurance department cannot be overlooked! Basics of TQM and sustainable quality improvement strategies
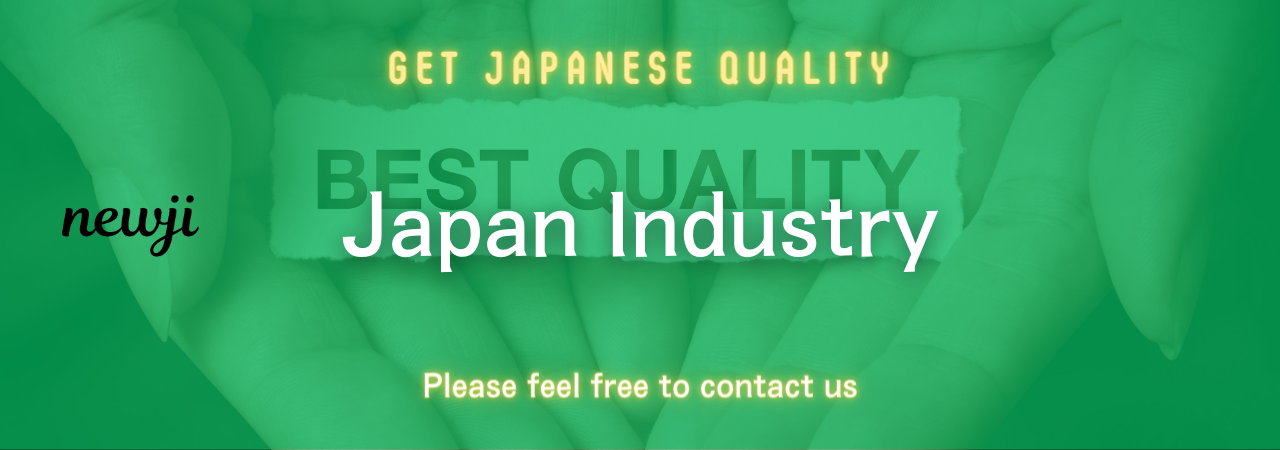
目次
Understanding Total Quality Management (TQM)
Total Quality Management, commonly referred to as TQM, is an organizational approach that seeks to improve quality and performance which will meet or exceed customer expectations.
TQM involves the participation of all members of an organization in improving processes, products, services, and the culture in which they work.
This comprehensive system ensures that everyone at every level—the management, workforce, suppliers, and even customers—is involved in the quality control and improvement processes.
The ultimate goal of TQM is to foster a culture of continuous improvement where quality becomes everyone’s responsibility.
Key Principles of TQM
To truly grasp the basics of TQM, it’s essential to understand its key principles.
These foundations drive the strategies that ensure sustainable quality improvement.
1. **Customer Focus**: A business depends on its customers, so it is crucial to understand current and future customer needs and strive to meet or exceed those needs.
2. **Continuous Improvement**: TQM involves an ongoing commitment to enhancing processes, products, and services.
3. **Employee Participation**: Engaging all employees, from top management to front-line staff, is critical as they are the ones interacting with the process daily.
4. **Process-Centric**: Understanding and managing processes are vital to ensuring that the desired outcome is achieved efficiently.
5. **Integrated System**: Quality focused processes are integrated with company strategy and operations, known as Quality frameworks.
6. **Strategic Approach**: Establishing a strategic plan that involves setting goals, defining KPIs and metrics, and tracking improvements.
7. **Decision-Making based on Data**: Analyzing data to measure performance, understand issues, and identify areas of improvement is crucial.
8. **Effective Communication**: Promoting consistent and clear communication throughout the organization ensures that everyone is on the same page and can drive improvements effectively.
Roles of Managers in the Quality Assurance Department
In any organization, the quality assurance (QA) department plays a pivotal role in maintaining the standards of products and services.
Managers within this department are crucial for the implementation and success of TQM initiatives.
Their responsibilities include:
1. Setting Clear Quality Goals
Managers are responsible for aligning the quality objectives with the overall strategic goals of the organization.
This involves setting achievable and measurable targets that guide the quality improvement efforts across the organization.
2. Leading by Example
Managers must embody the principles of TQM by demonstrating commitment to quality through their actions.
This includes adopting an open attitude, promoting a culture of continuous improvement, and facilitating effective communication.
3. Facilitating Employee Involvement
Employees are at the heart of TQM.
Managers need to create an environment where employees feel engaged and encouraged to participate in improvement initiatives.
This involves recognizing their contributions, providing the necessary training, and empowering them to take ownership of their tasks.
4. Data Analysis and Decision Making
Managers must utilize data to make informed decisions.
This involves using metrics to track performance, identify areas of improvement, and implement strategies that lead to enhanced quality.
5. Supplier Collaboration
The quality of the end product is influenced by the quality of materials and services provided by suppliers.
Managers should work closely with suppliers to ensure that they meet the quality standards.
This collaboration involves assessing their quality systems and fostering a mutually beneficial partnership.
6. Implementing Continuous Improvement Practices
Continuous improvement is a key component of TQM, and managers play a significant role in implementing this in their department.
This may involve introducing quality improvement methods such as Six Sigma or Lean manufacturing to streamline processes, reduce waste and enhance product quality.
Strategies for Sustainable Quality Improvement
A sustainable quality strategy is critical to the long-term success of an organization.
Managers can employ various strategies to achieve sustainable quality improvements.
1. Cultivating a Quality Culture
Instilling a culture that values quality at its core is crucial.
This involves promoting awareness, responsibility, and accountability for quality among all employees.
Creating a positive working environment where employees understand the importance of quality leads to commitment and consistently high standards.
2. Investing in Training and Development
Continuous education and skill development keep the workforce equipped with the latest quality improvement techniques.
Training programs, workshops, and certifications enhance employees’ knowledge and abilities, enabling them to make meaningful contributions to quality improvements.
3. Adopting Advanced Technology
Investing in cutting-edge technology can greatly enhance quality processes.
From automation and data analytics to AI in quality inspections, the right technology can lead to improved accuracy, efficiency, and decision-making.
4. Regular Auditing and Feedback Systems
Regular inspections and audits help identify any deviations from quality standards promptly.
Feedback systems enable continuous monitoring and provide valuable insights into potential areas for improvement, ensuring that corrective actions are taken without delay.
Conclusion
Managers in the quality assurance department serve as the cornerstone of implementing and advancing Total Quality Management within an organization.
Their leadership and commitment to quality are instrumental in achieving a culture of continuous improvement and sustainable quality strategies.
By aligning the essential principles of TQM with daily practices, engaging the workforce, and leveraging technology, managers can ensure that quality remains a priority and that the organization continues to meet customer expectations successfully.
資料ダウンロード
QCD調達購買管理クラウド「newji」は、調達購買部門で必要なQCD管理全てを備えた、現場特化型兼クラウド型の今世紀最高の購買管理システムとなります。
ユーザー登録
調達購買業務の効率化だけでなく、システムを導入することで、コスト削減や製品・資材のステータス可視化のほか、属人化していた購買情報の共有化による内部不正防止や統制にも役立ちます。
NEWJI DX
製造業に特化したデジタルトランスフォーメーション(DX)の実現を目指す請負開発型のコンサルティングサービスです。AI、iPaaS、および先端の技術を駆使して、製造プロセスの効率化、業務効率化、チームワーク強化、コスト削減、品質向上を実現します。このサービスは、製造業の課題を深く理解し、それに対する最適なデジタルソリューションを提供することで、企業が持続的な成長とイノベーションを達成できるようサポートします。
オンライン講座
製造業、主に購買・調達部門にお勤めの方々に向けた情報を配信しております。
新任の方やベテランの方、管理職を対象とした幅広いコンテンツをご用意しております。
お問い合わせ
コストダウンが利益に直結する術だと理解していても、なかなか前に進めることができない状況。そんな時は、newjiのコストダウン自動化機能で大きく利益貢献しよう!
(Β版非公開)